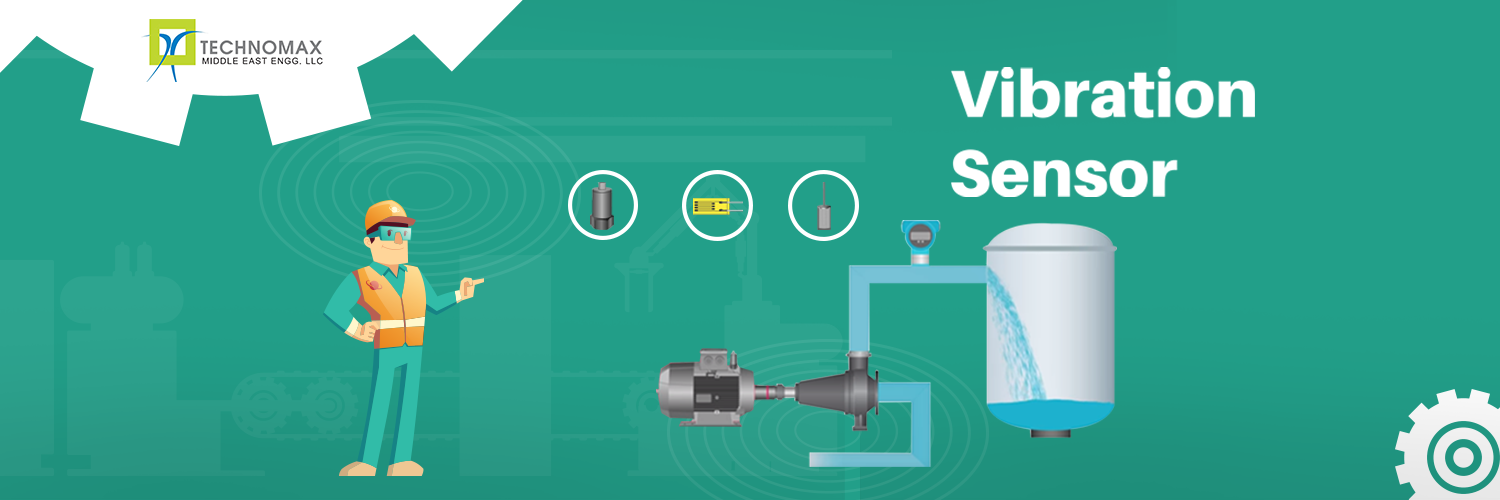
Vibration Sensors: An Overview – Types of Vibration Sensors
What is a Vibration Sensor?
Vibration Sensors are devices used to measure vibration, changes in acceleration, pressure, force, temperature, and strain. By leveraging the piezoelectric effect, vibration sensors can measure fluctuating accelerations and sense vibrations. To ensure the ideal functioning of a machine, it is necessary to do regular checkups on speed, vibration, temperature, and pressure.
Aptly monitoring these parameters will eliminate downtime and machine malfunction, thus saving money. Vibration is the best parameter to understand the dynamics of the machine, and Vibration sensors are exclusively designed to precisely measure vibration.
The tool is used for predictive maintenance of machinery, reducing overhead charges, and optimising performance. Piezoelectric accelerometers are generally used for aerial navigation, process control systems, and underwater applications.
Temperatures between -50 degrees Celsius and 85 degrees Celcius and a frequency range from 0.2 Hz to 2500Hz are the optimal conditions for the vibration sensor to work.
You may also like to read:
- Pipeline Leak Detection Services UAE - Leak Detection UAE
- The Influence of Lubrication, Vibration Infrared Analysis Results
- Maximising Plant Productivity Through Machinery Diagnosis
Types of Vibration Sensors
Vibrations are mechanical oscillations of a machine component.
There are two types of vibrations: axial and radial vibrations.
There are different types of vibration sensors to measure these vibrations. Let’s take a look at the types of vibration sensors.
1. Velocity Sensors
a. Electromagnetic Linear Velocity Transducers
Used to measure oscillatory velocity, electromagnetic linear velocity transducers have a permanent magnet that oscillates within a coil winding inducing an electromagnetic field. The generated emf is proportional to the velocity of the magnet.
b. Electromagnetic Tachometer Generators
Electromagnetic Tachometer generators are used to measure the angular velocity of vibrating objects. The instrument produces a voltage or frequency that is proportional to the angular velocity.
2. Acceleration Sensors
a. Piezoelectric Accelerometers
Piezoelectric vibration sensors or piezo sensors leverage the mechanical strain caused by equipment’s high-frequency motion to measure vibration. Materials like quartz possess piezoelectric properties and thus will generate a positive or negative voltage when mechanical pressure is applied to them.
In the piezoelectric accelerometer, a piezoelectric material is placed between an unconstrained proof mass and a sensor frame. The sensor is fixed to the device, which is to be tested so the vibration will move the sensor housing.
The inertia of the proof mass then causes it to apply stress to the piezoelectric material, which will, in turn, generate a voltage.
b. Capacitive Accelerometers
Capacitive accelerometers are used in equipment that has a diaphragm-supported seismic mass as a moving electrode along with one or two fixed electrodes. The change in capacitance will produce a signal which will be post-processed using an LC circuit.
c. Potentiometric Accelerometers
Potentiometric accelerometers are economical and are used where slowly varying acceleration is to be measured accurately.
The displacement of the spring-mass system is linked to a viper arm mechanically, and it moves along a potentiometric resistive substance.
Applications of Vibration Sensors
Regular monitoring of vibration in industrial maintenance systems has always proven fruitful in cost reduction and data collection for decision-making.
Let’s look at some of the real-life applications of vibration sensors.
1. Automotive Industry
Vibration sensors play a major role in condition monitoring. They collect data that can be later used for data-driven decision-making or to calculate the remaining life the instrument has. Through precise and effective predictive maintenance, the condition of the machine can be determined along with the maintenance requirement.
Automotive production facilities can engage vibration sensors to automate the monitoring process and minimise overhead charges by saving the maintenance team a lot of time which can be redirected to other tasks.
2. Oil and Gas Industry
Regular vibration monitoring for oil and gas equipment and machines to detect anomalies or potential damages beforehand. Machines like blowers, turbines, and cooling towers could use vibration sensors to ensure proper functioning.
Explosion-proof vibrations sensors are available to withstand and perform precisely even under unfriendly environments.
3. HVAC Systems
Fans and compressors are critical for the proper functioning of HVAC systems. While engaging vibration sensors to monitor the performance, it will detect the regular airflow, which keeps the machine cool and will alert the team if there is even a possibility of a defect.
This early detection or preventive maintenance will definitely save the company a lot of money and human efforts.
4. Water Distribution & Wastewater Treatment
The downtime in water distribution and wastewater treatment can negatively affect the water quality and customer access.
Installing vibration sensors will give an ever-roving eye to the running machine, which will prevent unexpected failures and undefined downtimes.
5. Food & Beverage
The rollers, gearboxes, and chillers are very critical in the food and beverage production units. The proper functioning of these machines is mandatory. By installing an apt vibration sensor, one can monitor the condition of the running equipment and detect the anomalies, if any, beforehand.
Through precise predictive maintenance, industries can eliminate unexpected downtimes and undesired economic losses.
You may also like to read:
- Vibration Motion Magnification by Technomax
- Bearing Fault Condition Monitoring Techniques
- Dynamic Balancing Of Gas Turbine Rotor
Conclusion
Extending the life of your equipment by making data-driven decisions is how predictive maintenance works. Vibration sensors assist industries in monitoring their machines constantly and collect data that can be later used while making decisions.
For example, vibration sensors will detect how long will the machine work and how well is the machine performing or a possible threat in the future. The sensor predicts the future of the machines, which will allow you to plan accordingly.
Predictive maintenance will increase your equipment reliability and thus will make your lives easier. The human dependency is reduced by considerably reducing the overhead charges. By precisely analysing the ‘purr’ of your machines, Vibration sensors will give you an almost exact prediction on the lifespan, upcoming maintenance, and relevant data on all these.
The data-driven decisions will save you time and money, and the chances of mistakes are diminished along with maintenance costs. Include vibration sensors in your industrial process and save yourself some time, money, and resources.
Learn More About Our Services
Recent Blogs
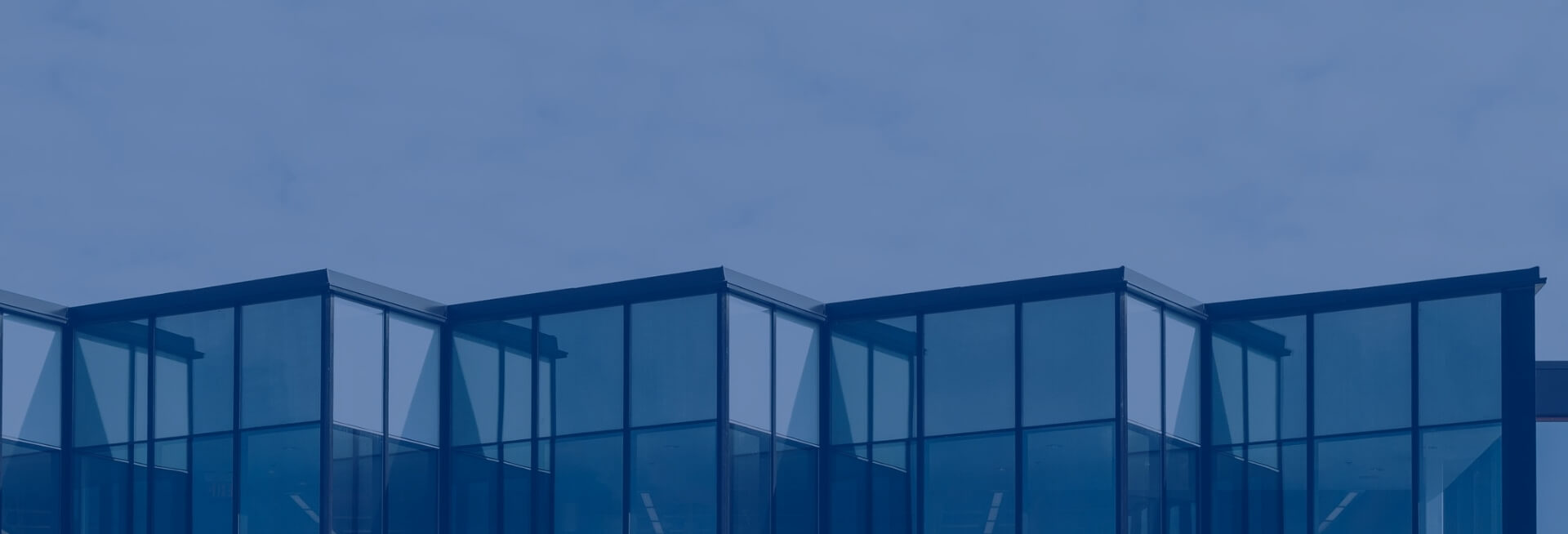
Get Started Now!
It takes less than a minute of your time. Or you may simply call +971 2 555 1 783