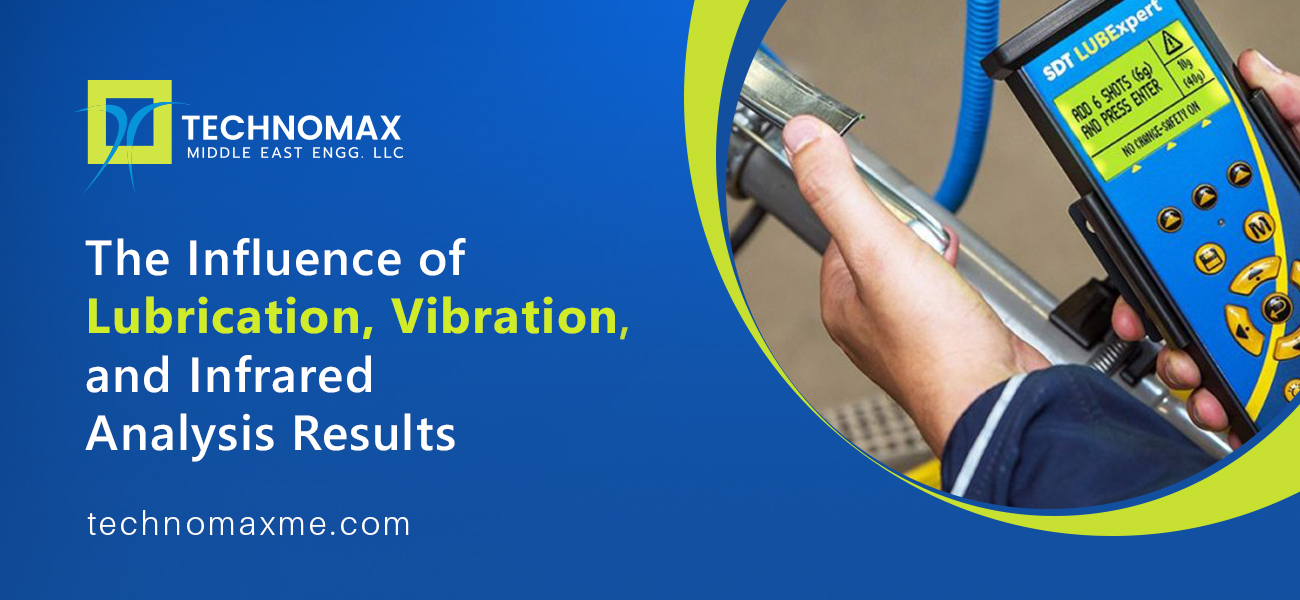
Machinery Lubrication: The Influence of Vibration and Infrared Analysis
Machinery lubrication is a crucial aspect of equipment maintenance that involves the application of lubricants to reduce friction, wear, and heat generation within mechanical systems. The primary purpose of machinery lubrication is to ensure the smooth operation and longevity of moving parts in various industrial and mechanical applications.
Although individual predictive maintenance (PdM) systems can operate properly on their own, coordination is necessary for them to work to their full potential. Most of the time, it's easier to find and fix problems with equipment's dependability if you know a lot about the maintenance plan, the technologies used, and how they all work together. Read more about The Influence of Machinery Lubrication & Vibration Infrared Analysis Results.
Predictive Maintenance in Machinery Lubrication
By evaluating the equipment's state, predictive maintenance attempts to determine when maintenance should be carried out. Throughout history, technologies like vibration, lubrication, infrared thermography, and others have been utilized to track failure. Then, work is scheduled to be completed prior to a significant component breakdown.
Predictive maintenance techniques provide a number of advantages. The inventory of replacement parts may be diminished because issues with components are sometimes identified weeks or even months before the breakdown is anticipated to occur. This realization enables maintenance planning to reduce stored overhead and cap the number of components.
Another benefit is the quicker repair time. Early failure detection means fewer catastrophic failures, which reduces the number of parts that need to be serviced and the time it takes to maintain equipment.
While there are many advantages to this method, it is also important to note certain disadvantages. First, implementation may be expensive due to the up-front costs of the technology-specific tools and early training. Additionally, learning any particular technology by staff takes time.
Read more about:
- Identifying Mechanical Faults with Motor Current Signature Analysis
- The Significance of Electrical Preventive Maintenance
- How to Consider Machine Alignment to Avoid Equipment Failures
- Laser Shaft Alignment- An Overview
The Influence of Predictive Technologies
Several technologies can be applied to the field of predictive maintenance. Here, we'll focus on machinery lubrication, vibration, and infrared thermography as the three main technologies. Depending on the component and application, other technologies like ultrasonography, motor current measurement, and motion amplification can also be very useful.
Vibration Analysis
Monitoring anomalies and rates of change in a system's signature is the technique of vibration analysis. The three categories of equipment vibration symptoms are sub-synchronous, synchronous, and non-synchronous. The sub-synchronous section's symptoms manifest more frequently than the turning speed. Belt vibration and oil swirl are two examples. Synchronous symptoms happen at or after the turning speed. The bulk of vibration-related problems are usually found in this area. Inconsistencies in synchronization include imbalance, misalignment, and looseness.
It's also crucial to know when to gather vibration data. Typically, baseline vibration data is gathered when the device is installed. Once the baseline has been created, you should choose a frequency for gathering general vibration data, and you should compare the readings to the baseline.
After problems have been found, you can do more vibration tests like high-resolution data, resonance testing, and cross-channel phase to learn more about them.
Lube Oil analysis
One of the first technologies still in use today is oil analysis. Controlling friction, wear, corrosion, temperature, impurities, and power transmission are all functions of lubricants. Maintaining a clean, cool, and dry atmosphere should be the goal.
This is accomplished by keeping the lubricant, the machinery lubrication system, and the machine in good working order. Grease and oil are the two main types of lubricants that are looked at. The main things to look for are fluid characteristics, contamination, and wear debris.
Depending on the aforementioned circumstances, several tests are done in each group. Some of the most common tests are the viscosity analysis, the amount of moisture, and the particle count.
Infrared Thermography
The detection of radiation energy that is emitted, transmitted, and reflected, as well as its conversion into a temperature display from a non-contact instrument, is known as infrared thermography analysis. The main goals of this technology are to identify changes in the way radiation varies, find thermal problems, and encourage replacement before they cause major maintenance work or equipment downtime.
Understanding where infrared energy is located on the electromagnetic spectrum enables consumers to comprehend how infrared and visible light are related.
To establish a reference point, infrared surveys are normally carried out after the equipment installation is complete or right before it is put back into use. Following this, surveys are often done at a regular interval, depending on the equipment's criticality and state of operation.
On equipment, abnormal, alert, and alarm ranges are frequently established as indicators of when to take action. Infrared thermography can be used as a cross-reference tool and to help find problems with components, just like any other technology.
You may also like to read:
- Importance of vibration analysis in maintenance
- Common causes of Piping Vibration and their effects on piping systems
- How Can IoT Condition Monitoring Methods Enhance Machinery Health
MaChinery Lubrication from Technomax
In conclusion, even while a single technology can work effectively on its own, it is frequently beneficial to use a variety of technologies to identify problems. By learning about the predictive maintenance approach, the technologies that can be used, and how they work together to get results, you can make a big difference in finding and fixing equipment dependability problems.
With over 15 years of industry expertise, Technomax is the clients' chosen source for material procurement and maintenance services. The dedicated, skilled, and highly experienced people who work for Technomax work directly with clients to make sure they get the best services possible.
Learn More About Our Services
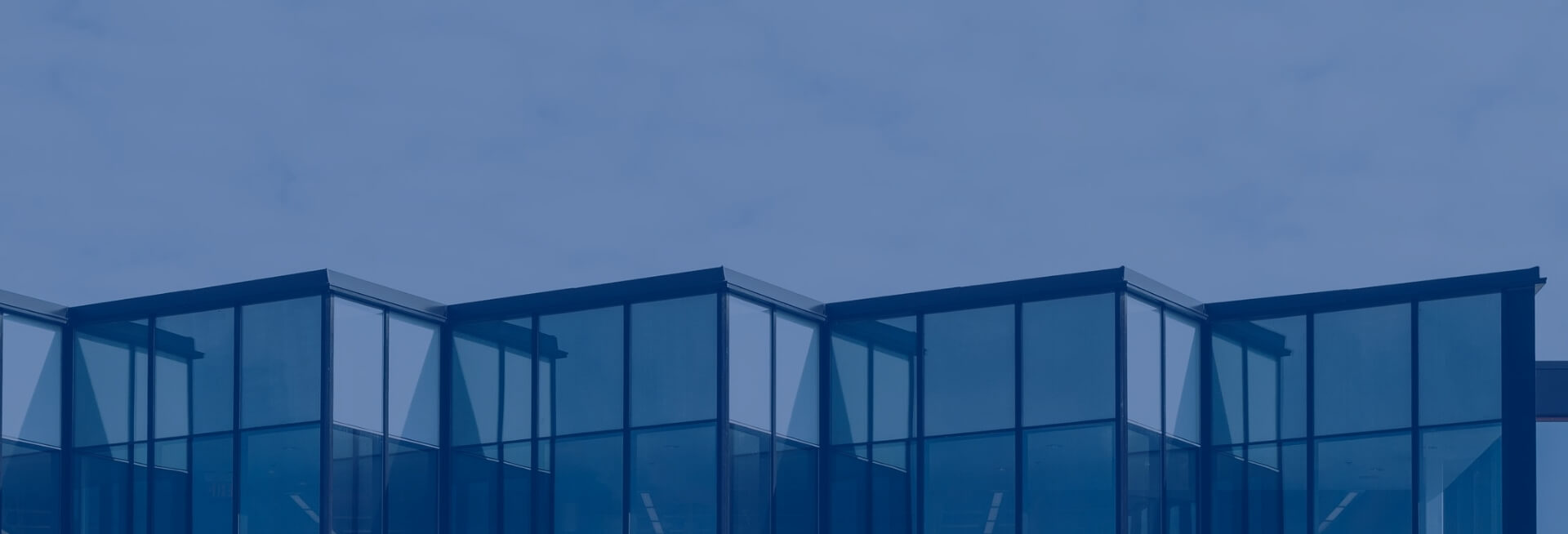
Get Started Now!
It takes less than a minute of your time. Or you may simply call +971 2 555 1 783