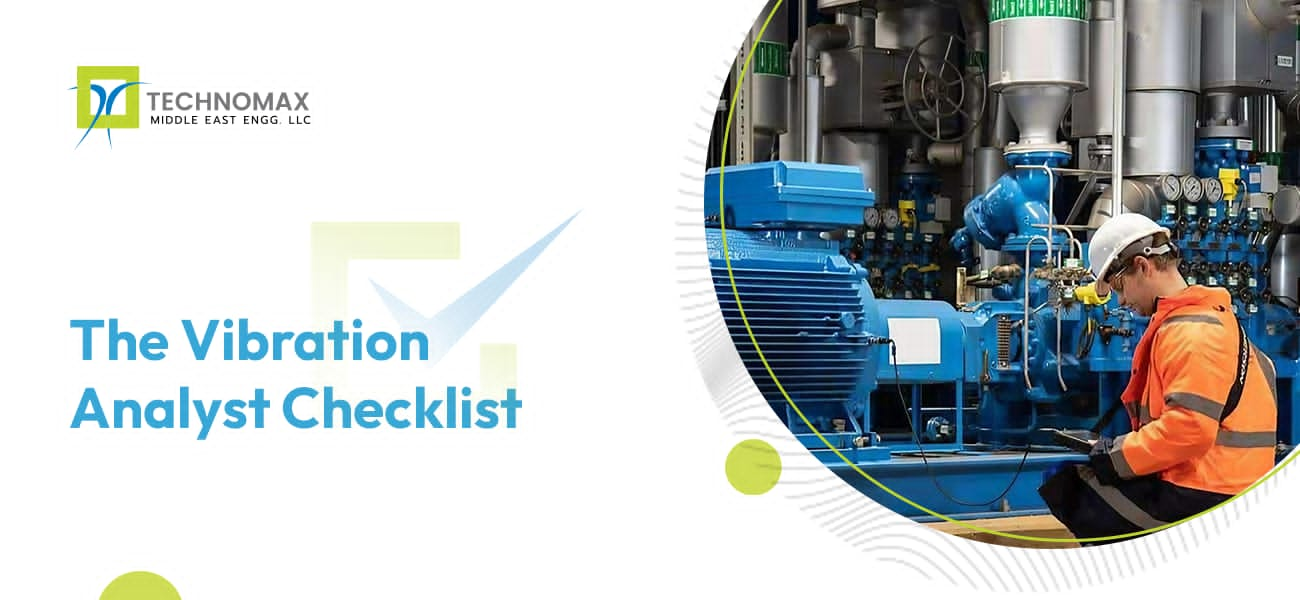
The Vibration Analyst Checklist
Vibration analysis gathers the vibrations equipment detects and measures them concerning the failure of the machine to identify the possible points of failure.
Vibration Analysis helps the maintenance experts to proactively act on performance issues before the damage or unexpected machine damage.
This blog gives you insights on the vibration analyst checklist with all the key prerequisites to ensure the reliability and durability of industrial equipment.
You may also like to read:
- Preventive Maintenance Using Vibration Analysis in Electric Induction Motors
- Vibration Motion Magnification by Technomax
- The Influence of Lubrication, Vibration Infrared Analysis Results
Why Does Vibration Analysis Matter?
The ability of vibration analysis to predict possible failures makes it a beneficial tool in planning maintenance, triggering the performance of assets and avoiding unscheduled downtime.
It also helps to perform condition monitoring which saves money ultimately through:
-minimizing the unplanned downtime and work scheduling that suits organizational plans;
-saving money through enhancing the product quality with equipment operating at the desired performance levels;
-elimination of wasted production expenses while making unplanned repairs;
-providing products on time through reliable equipment.
Checklist Every Vibration Analyst Must Have
Here’s a glance at the checklist you should keep a note of the vibration analysis measures to be taken for the industrial equipment:
- Has the data been collected from the right measurement axes?
- Are the Fmax and Lines of Resolution (LOR) set?
- Have the overlap percentage and number of averages been set correctly?
- Are the mounting techniques correct?
- Any additional technologies and special tests are used to confirm the diagnoses?
- Is the document successful and are the financial benefits well reported?
- Does the reliability improve with the performance of root cause analysis and acceptance testing?
Let’s deep dive into these points in the vibration analyst checklist in detail:
Has the data been collected from the right measurement axes?
Machines vibrate in vertical, horizontal, and axial directions. Based on the orientation of the equipment, the kind of bearings used, the orientation of the machine components, and the nature of the fault, the vibration trend that best reflects the fault situation could exist in all axes. You might miss the fault if you don’t measure in this axis.
It is often advantageous to compare the data from one axis to another that compares the levels or tests for the presence of sidebands or harmonics. If you make efforts to save time by measuring only one axis, this is the best option for you.
You can also go out, and conduct re-testing of the machine to gather data from the additional axes, however, you don't need to have historic data to be used as a standard for comparison.
Are the Fmax and Lines of Resolution (LOR) set?
You must leverage the right Fmax and Lines of resolution. If Fmax is not great enough, you could miss vital information so easily. With an insufficient LOR, you would miss the important detail.
As per the equation, Measurement time equals LOR/ Fmax. With the increase in Fmax, the measurement gets completed more speedily which is desirable.
However, with an increase in Fmax, the effective resolutions drop, which is not great. Increasing LOR from 800 lines to 1600 or 3200 lines can make time to collect data double or quadruple.
Fmax should be large enough to see all frequencies and related harmonics, but necessary to have the preferred resolution to correctly interpret these frequencies.
To increase the time record without impacting the frequency span, you need to increase the lines of resolution.
Have the overlap percentage and number of averages been set correctly?
Averaging lets you gain repeatability and makes sure you collect data while the equipment undergoes many rotations (cycles).
This has two key aspects to consider:
- Repeatability
- Data loss
Repeatability or noise reduction: The higher overlap percentage and the reduced number of averages can minimize the time required to finish the measurement.
Data loss: The process of Hanning windowing causes data suppression at the start and end of the time record. Therefore, we might lose the necessary data. Overlap averaging saves data from being lost.
The vibration readings should be repeatable and should capture the various instances of continuous mechanical events.
Are the mounting techniques correct?
You should mount the accelerometer appropriately along with the necessary practices to follow repeatability. There are two major issues here to consider: sensor mounting and repeatability.
Sensor mounting: Sensor mounting is the most frequent problem. It should create great solid contact with the housing of the bearings. The higher frequency vibration sources are generated once they should cross the air cavities.
If you make envelope measurements or any specific measurements that use high-frequency data, your measurements can get highly affected if you don't prepare the mounting surface correctly. Hence, while working in a dirty environment, you need a clear and flat surface with a clean cloth to wipe.
A powerful magnet is a minimum need, with stud-mounted sensors for the desirable results. Also, avoid surfaces that might resonate at the operating speeds like guards or motor end bell cowlings.
Mounting Repeatability: You should mount the sensor in the exact place all the time. The location changes can create changes in amplitude levels. If the same person performs data collection, it is least likely to cause a problem. Else, mark the right test location or add a mounting pad.
Any additional technologies and special tests are used to confirm the diagnoses?
Depending on spectra alone which you collect in a routine can’t give you a complete picture.
There are various other data types, tests, condition monitoring, and the required performance data that lets you improve accuracy and the promptness of diagnosis.
The time waveforms can let you rule in/out the specific fault conditions, and also while learning about gearboxes or low-speed machines.
Here, the rubs, impacts, and looseness are visible in the waveform.
Is the document successful and are the financial benefits well reported?
A Vibration analyst can interpret the analysis, highlight the recommendations to adopt, and determine the success of programs with benefits.
Everyone should be aware of the financial advantages of the program and you should determine how to report this data in the organization.
If you find that a bearing could fail and you rightly recommend that it should be replaced, you can save the company for every fault you detect, manage and take action.
Report the benefits of the program in a relevant, meaningful, and trustworthy manner while agreeing with the management.
Does the reliability improve with the performance of the root cause analysis and acceptance testing?
Several vibration analyst believe that their task is to identify and report the fault conditions, which isn’t true.
The vibration data and other condition monitoring information may cause the faults to occur in the first place.
If you can report that the bearing might fail, or when you can brief what causes the bearing to make fault or why the machine gets misaligned, it proves better.
You can report the fault, wait for it to build again, or do your best to make sure it doesn’t repeat. Precision balancing, adequate lubrication, alignment, and acceptance testing-related practices help to scale the reliability of the equipment.
Vibration analysis and various condition monitoring technologies are still necessary, however with improved maintenance, purchase, and repair process, you can help machine life approach design life.
Read more about:
- How Technomax Performs In-situ Balancing
- Rotodynamic Analysis Services from Technomax
- Why Do Steam Traps Fail: Causes, Factors & Preventive Methods
The Bottom Line
Being a non-destructive method of condition monitoring, vibration analysis helps to identify faults within the machinery that records the vibrations a system produces.
The vibration signatures generate an installation that could be recorded and observed to know about the health state of every system.
Appropriate vibration testing and diagnosis can help to explore the chronic and repairable concerns due to electrical, operational, and mechanical irregularities.
Technomax has state-of-the-art instruments that track the vibrations and sound at your industrial facilities.
Using the vibration analysis, we let you perform noise level cartography, and analyze and manage health, safety, and welfare hazards.
Contact our experts today to identify, build and scale the real-time control systems with capabilities to conduct vibration analysis for the machinery.
Learn More About Our Services
Recent Blogs
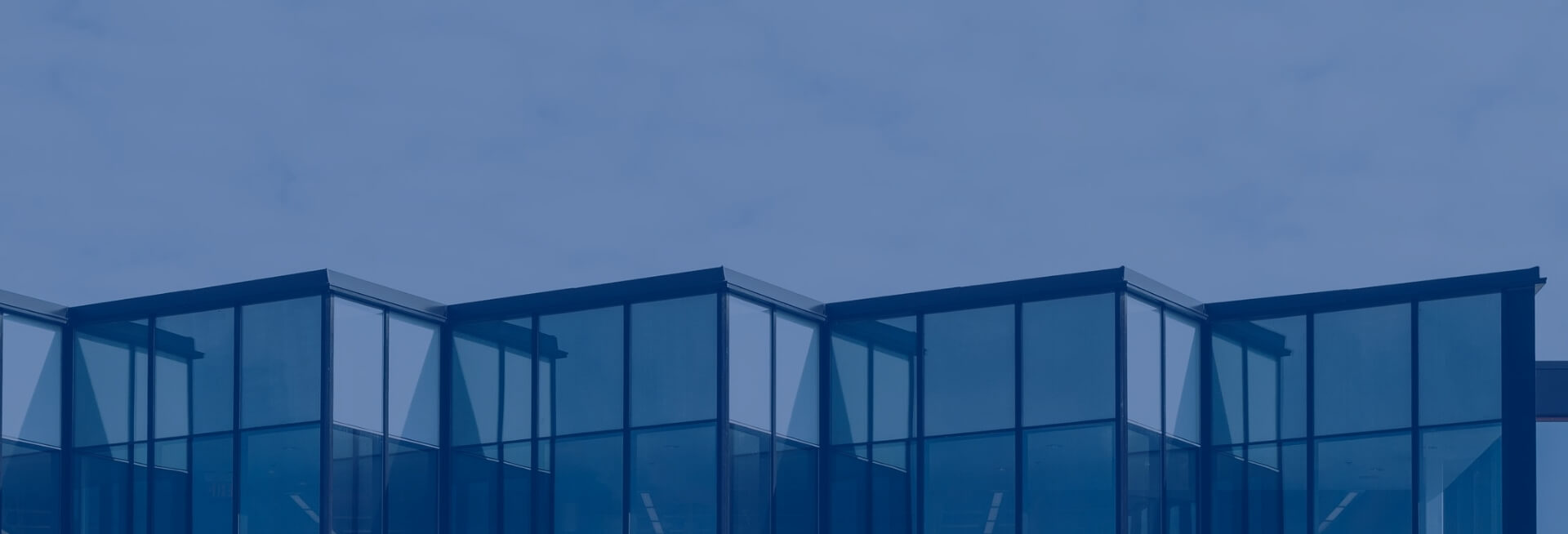
Get Started Now!
It takes less than a minute of your time. Or you may simply call +971 2 555 1 783