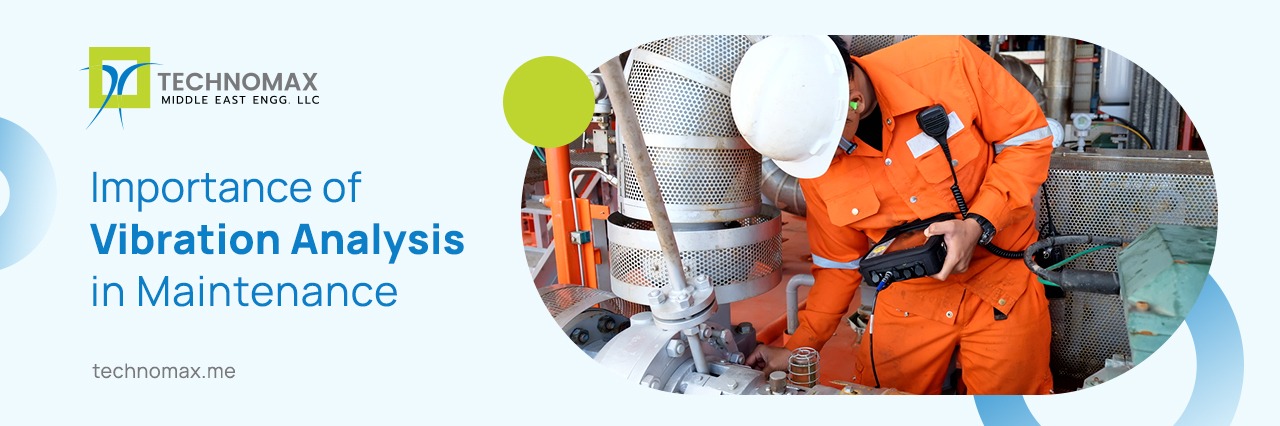
The Importance of Vibration Analysis in Maintenance
Vibration analysis collects and measures vibrations detected by equipment to determine failed vibrations and potential failure points.
This method can be applied to any piece of equipment with rotating parts and components, such as turbines, pumps, conveyor components, gears, fans, rotors, and so on. Vibration analysis allows you to detect abnormal operations in the above-mentioned components and eliminate problems before they occur. Read more about Vibration Analysis in Maintenance.
A Brief Summary of Vibration Analysis(VA) In 30 Seconds
- Vibration analysis provides calculations that can be used to detect signs of machine breakdown or deterioration.
- A trained vibration analyst can quickly grasp the fundamentals of vibration analysis and equipment failure modes.
- Predictive maintenance aids in the planning of all routine maintenance and unavoidable downtime.
- Reactive maintenance provides vibration data that aids in replacing or mending worn-out parts.
- Preventive maintenance is regular maintenance to keep the equipment running by preventing unplanned downtime and costs from machine failures that are not anticipated.
Related blogs:
- Common causes of Piping Vibration and their effects on piping systems
- How Can IoT Condition Monitoring Methods Enhance Machinery Health
- Radio Remote Control for EOT Crane
What Is the Use of Vibration Analysis?
We now understand the significance of vibration analysis. So, let us explore the applications of vibration analysis and learn more about it.
Some of the key aspects that vibration monitoring and analysis can detect problems with are as follows:
- Problems with impeller operation
- Gear flaws
- Deranged
- Bearing health
- Bent shafts
- Balances of components or machines
- Fasteners, mounts, loose bolts, etc.
- Problems related to electricity
- Problems with process flow
Vibration analysis assists in the detection of equipment health and the prevention of failures. How is this even possible? Modern vibration analyzers give a quick glimpse of what is going on inside the machine.
Modern vibration analysis units can simultaneously display the entire frequency spectrum and time of three axes. The person who calculates the data must be familiar with the fundamentals of vibration analysis as well as the breakdown of the equipment and how to apply them to the equipment under consideration.
What Are the Techniques Used for Vibration Analysis in Maintenance?
When you collect data, it is important to collect the entire dataset. You must obtain a complete vibration signature for the equipment's vertical, axial, and horizontal axes, as well as both ends of the motor. You have to make sure that you can address any failures.
It is critical to test all three axes because if you don't, you may miss the problem. The unplanned machinery failure will damage the viability of the vibration program and might lead to an unsolvable issue. And with a careful and timed waveform vibration analysis, you'll be able to detect the issues and be on your way.
Predictive maintenance will assist you in detecting issues and successfully completing the process.
What Are the Benefits of Vibration Analysis in Maintenance?
- Reduce the unplanned downtime
- VA has a long history of reliability
- The possibility of failure can be easily identified
- More control over the downtime and maintenance processes
- Aside from the most common bearing failure search, VA has a variety of other applications.
Types of Maintenance and Their Uses
Maintenance can be divided into three types. They are:
- Reactive maintenance
- Predictive maintenance
- Preventive maintenance
Let's get to know deeply reactive, predictive, and preventive maintenance.
Reactive Maintenance
Reactive machinery maintenance is also known as the "run until failure approach." This method addresses issues as they arise. This approach is used by a wide range of businesses as it is the most convenient choice.
The disadvantage of this strategy is that it only addresses the problem after it has occurred, which can result in significant secondary damage. Repairs will be costly due to the necessity for additional labor and new parts as a result of the extensive secondary damage.
Reactive maintenance has no initial cost and provides an easy solution to many maintenance issues. Frequent vibration analysis and monitoring are required for reactive maintenance to be effective. It will also assist you in identifying failures from the start as well as resolving them quickly, cheaply, and easily.
Our Vibration Analysis services:
Predictive Maintenance
Predictive maintenance is the polar opposite of reactive maintenance. Predictive maintenance monitors the equipment while it operates. The main goal of which is to predict which parts will fail and when they are going to fail.
The benefit of this method is that any parts that show any sign of destruction or deterioration can be replaced on the spot itself.
When comparing reactive maintenance to predictive maintenance, it frequently results in the minimum number of issues, thereby less downtime. Because of the higher cost of equipment and special training for staff, predictive maintenance is more costly than reactive maintenance.
Preventive Maintenance
Preventive maintenance is the regular maintenance that keeps machines running by forbidding unplanned downtime and unexpected equipment failures. Preventive maintenance is essential for avoiding unplanned equipment failures and reducing the need for repairs or replacement. Regular inspection and maintenance extend the life of the equipment.
Preventive maintenance is carried out when machines are down, but predictive maintenance is carried out when machines are in use. This is the basic difference between preventive and predictive maintenance.
Reactive maintenance can be an effective and cost-effective solution when using vibration analysis. As can be seen, some companies prefer predictive vibration sensor maintenance to reactive maintenance that does not include vibration analysis. Portable vibration monitoring is becoming less expensive than other methods.
Learn More About Our Services
Recent Blogs
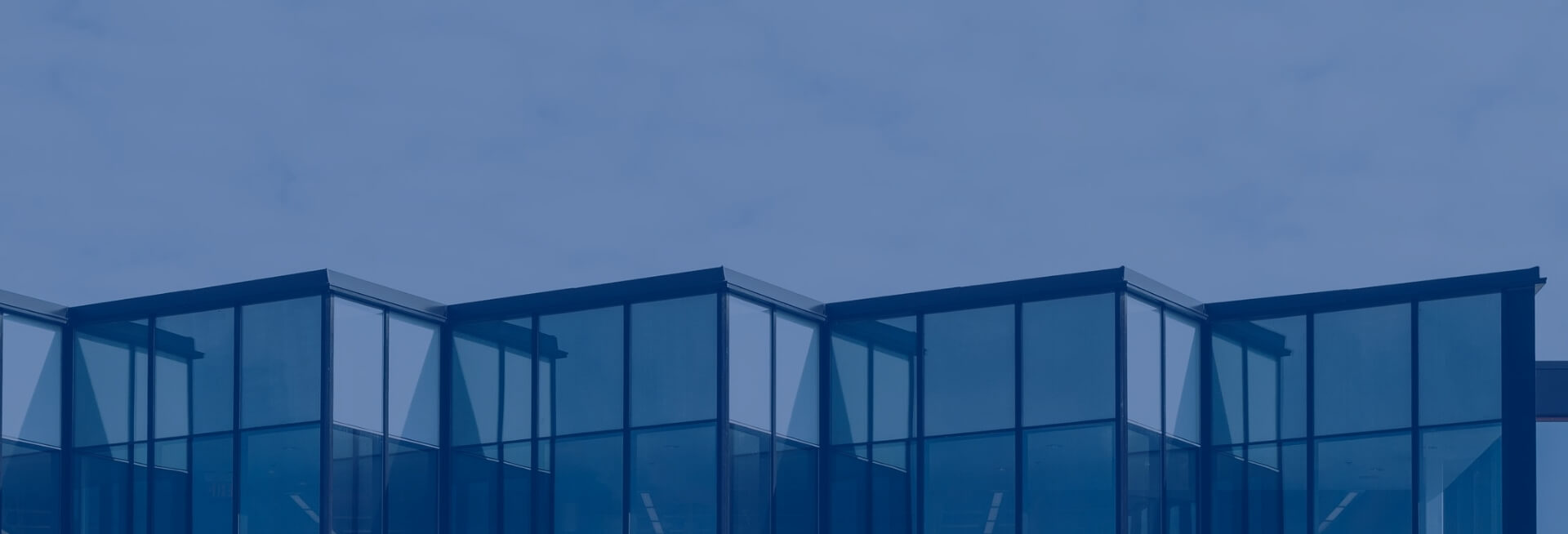
Get Started Now!
It takes less than a minute of your time. Or you may simply call +971 2 555 1 783