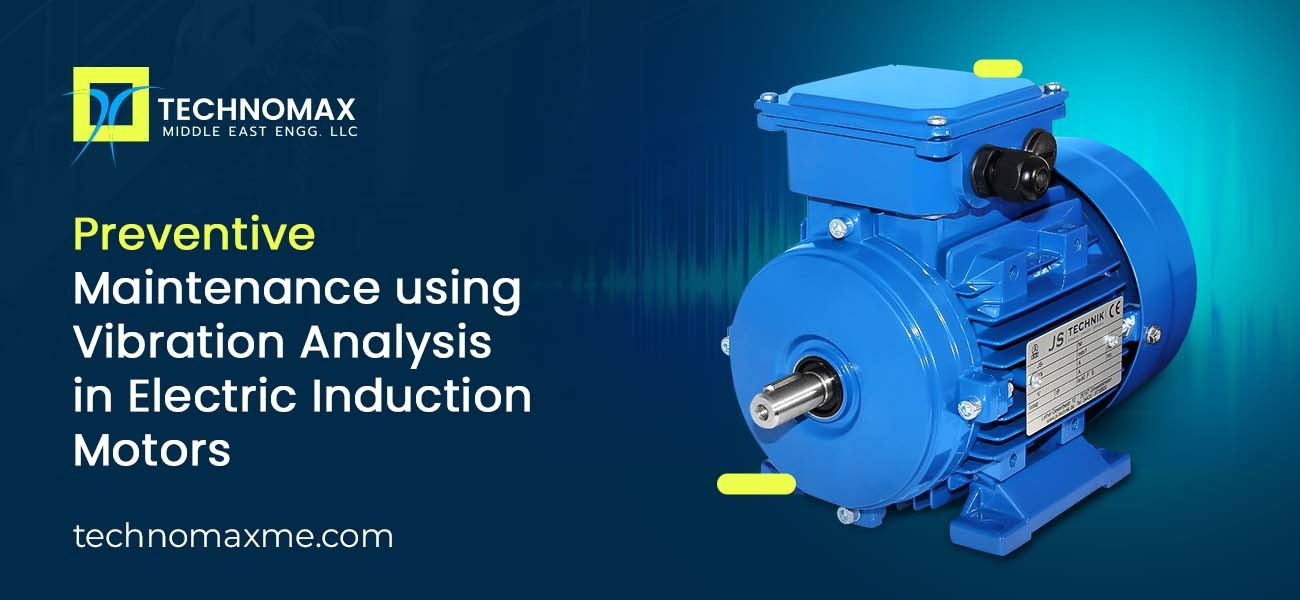
Preventive Maintenance Using Vibration Analysis in Electric Induction Motors
Induction motors(asynchronous motors) work based on the principle of electromagnetic induction. Manufacturing of induction motors is usually performed for various applications and factors such as power, efficiency, operating speed, etc.
Every moving mechanical piece of equipment produces a vibration profile that signifies its state of operation. This applies true regardless of the speed, or its execution along reaction, revolution or even a straight line.
The vibrations of electric induction motors can originate from shaft bowing, uneven rotors, shaft misalignment, conditions of pulleys, belts or any other pivoting components, deviations in the directions for the activity, etc.
There are two major sources of electromagnetic vibration within the induction motors, namely tangential, electromagnetic forces, and radial electromagnetic forces.
In either case due to the deficiencies of the inner engine or outer problems, for instance, the low quality of power supply and related burden, the electromagnetic vibration can impact the activity of the typical engine.
This blog takes you through the concepts of motor vibration analysis, its features, and its benefits in detail. Read more about Vibration Analysis in Electric Induction Motors.
Related Blogs:
- Rotodynamic Analysis Services from Technomax
- Turbo Machinery Analysis and Balancing
- Equipment Performance Monitoring – Our Approach
Why Vibration Analysis?
Vibration analysis plays a crucial role in electric induction motor maintenance. While some degree of vibration is expected in rotating machines, excessive vibration can lead to severe damage. By precisely identifying vibration frequencies and detecting established patterns, mechanical faults can be uncovered. This approach, known as condition-based maintenance, prioritizes the machine's condition over a fixed schedule, enabling the identification and scheduling of repair actions.
Why use Vibration before other technologies?
Because it is the best practice for when a mechanical fault needs action.
Thermography is good but is often too late ,temperature increases the later stages just before failure.
Ultrasound is good but it is often too early- bearings make a noise very early and often they just need to be lubricated.
Vibration is best for diagnosing mechanical faults and tracking the severity from slight to extreme over 12-18 months or longer.
What is the Solution?
The presence of vibration in industrial machinery can have detrimental effects on equipment performance, longevity, and safety. Premature component wear, reduced equipment lifespan, excessive noise generation, and potential safety hazards are some of the consequences associated with vibration. Specifically, imbalance or misalignment in rotating assets can lead to severe consequences such as the cracking or breakage of driveshafts and other critical components.
Vibration data analysis enhances maintenance and reliability programs by providing valuable insights. Merely examining vibration amplitude is insufficient for a comprehensive understanding. Analyzing the time waveform shape reveals underlying causes of vibration changes. Historical data trends enable the identification of deviations from the expected norm in a machine's vibration.
Vibration analysis is highly effective in identifying mechanical and electrical motor faults. Each fault type has a unique signature in the vibration spectrum, enabling accurate recognition through comprehensive analysis. Misalignment, looseness, unbalance, bearing faults, and some electrical faults follow the same principles and rules as other machinery components. Vibration analysis is a valuable tool for detecting these faults.
You should measure the motor with and without a power supply to find them. Some vibration signatures could disappear after power off – those with an electrical origin. You can also focus on the exact frequency of peaks in the spectrum. If you find a peak with your exact current supply frequency (for example 50Hz and more often on its harmonic frequencies) it is probably an electric issue because there is always some slip on a loaded electric motor and the motor isn't running on its exact rotation frequency.
Types of Vibration Analysis
Operating deflection shape or ODS is used for the structural vibration analysis which is also called ODS analysis. This method is ideal for the visualization of vibration, and patterns of equipment or structure based on its surrounding operating forces.
It is the angular vibration of an object, particularly a shaft across the axis of rotation. This is a concern mainly in the power transmission systems which use couplings or rotating shafts. This is used to find out the torsional, natural frequency and the methods to effectively dampen the system.
How is Vibration measured?
Vibration is measured in the frequency of the revolutions or oscillations around a reference point. For example, a shaft vibrates relative to the casing of a piece of machinery and a bearing vibrates relative to a bearing housing. Hertz (Hz) is the standard vibration measurement unit. The frequency of vibration is measured by accelerometers, MEMS sensors, and/or piezoelectric sensors, which convert vibration data into electrical signals for analysis.
Vibration testing personnel measure vibration with handheld analyzers, wireless vibration sensors, or through on-line vibration monitoring systems. Most vibration tools capture the time waveform of the vibration over time. This can then be translated into frequency domain readings through FFT conversion, which gives further insight into what components are responsible for which signals, and which faults are present.
Wireless sensors give you the power to monitor asset condition 24/7, sending measurements to your systems at specified intervals. These are ideal for setting up alarms when vibration readings exceed normal levels. Online vibration monitoring systems are sophisticated wired set ups that continuously collect data. Vibration experts implement on-line monitoring to work on critical machines that need in-depth vibration analysis.
What are the Causes of Vibration in Electric motors
- Imbalance & misalignment
Imbalance is caused in electric motors due to the wrong balancing procedures, deformation of rotors, where, or breakage of fans and couplings, breakage of improperly, mounted cooling, fan, no consideration of keyways etc.
Under such situations, you can adopt the following actions:
- Select the root cause analysis to verify the problems in operations, maintenance, new engine etc.
- Verify the processes and quality grade of balancing for every application
- Conductor runs out a check to analyze the deformations of the rotor.
- Analyze the calibration of the balancing machine.
- Identify factors like features and criticality of the motor. Implement precision balancing based on them and also check the cooling fan.
Misalignment is the impact of an inappropriate procedure of alignment. This could take birth from thermal expansion, standard or tolerance, alignment, and concerns. Inappropriate support, base, failures in the coupling, soft foot, excessive runout, etc.
In case of misalignment, in the electric motor, the following steps can help:
- Assess the staff procedures and training
- Apply relevant standards to do precision alignment
- Evaluate the condition of the base and coupling
- Analyze the thermal expansion influence on the alignment process.
- Bearing Issues
The bearing problems of electric motors arise due to unwanted preload or wear of the bearing housing, bad assembly, failure of the lubrication process, poor quality lubricant, contaminated lubricant, equipment failures in the grounding wiring, etc.
The following steps can help when bearing issues in the electric motor are detected:
- Analyze the characteristics causing damage— erosion, wear, corrosion
- Evaluate the assembly procedure for bearing
- Verify alignment and balancing
- Identify the right bearing selection
- Check the tolerances and dimensions of mounting in the rotor and housing
- Optimize the process of lubrication
- Test earthing wire
- Eccentricity
Eccentricity is caused in electric motors due to excessive wear of bearing housing, rotors and bearings, misalignment of the housings, rotor deformation, etc.
The following steps can help while detecting the concerns with eccentricity:
- Check for wear in the bearing housings
- Analyze alignment between motor end shields or bearing housings
- Analyze the runout in pulleys, coupling, rotor, etc.
- Structural Issues
The structural issues of electrical motors arise due to the weak or damaged base after corrosion, defects in the bolts, loose screws and anchor bolts, etc.
The steps you can follow while detecting structural issues are:
- Evaluate the machine and foundation conditions
- Analyze the condition of anchor bolts
- Adjust bolts according to the right torque
- Electrical Issues
The electrical issues in the motor originate due to the uneven air gap between the stator and rotor, broken rotor bars, poor electric power quality like harmonics, voltage imbalance, frequency inverter failures, a lot of motor start and stop, excess load and insulation concerns.
The following actions can help during the detection of electrical problems:
- Implement a power quality analysis
- Evaluate rotor/stator origin, and study the air gap
- Perform insulation quality test on the motor
- Analyze the number of successive start-ups
- Resonance
Resonance in electric motors arises usually due to structural stiffness changes, operations with proximity to the system’s natural frequency, variable speed motors, etc.
The following steps can help with vibration analysis when detecting resonance in the electric motor:
- Conduct a test to evaluate the critical speed
- Implement an impact test to check if any natural frequency is being implemented
- Analyze whether the stiffness of the system has changed
Vibration Analysis in Electric Induction Motors
Improved performance of motors
It makes it easy to carry out predictive maintenance successfully. While unexpected machinery failure can affect the regular vibrations of the machine, a careful vibration analysis can help in the frequent maintenance which nearby contributes to the improved motor performance.
Minimized downtime
Schedule maintenance can replace the individual components on the machines which reduces the downtime, with proper scheduling of repair and timely replacement of the equipment. While scheduling emergency repairs will cost you a lot, vibration analysis can eliminate the requirement of emergencies through predictive maintenance measures.
Longer lifespan of motors
It helps you detect the early signs of failure or the deterioration of the machine. It lets the experts and technicians repair the machinery or replace the parts of the machine before a major functional failure happens. This improves the overall lifespan of the motors and helps to keep them durable for a long time.
Cost savings
You can save on labour expenses and the costs of parts when a vibration analysis is conducted. It reveals a problem with any part of the machine. With timely replacement that prevents catastrophic failure, you can save on time and cost rather than replacing the entire machine in the future.
In a Nutshell
The vibration analysis technique is one of the most useful techniques used for the condition monitoring of rotating equipment, especially induction motors. This is a scalable, efficient and convenient tool that diagnoses mechanical problems which usually occur in induction motors and helps to expand the lifespan of equipment for a hassle-free operation. To know more about our motor vibration analysis services, contact us today.
Learn More About Our Services
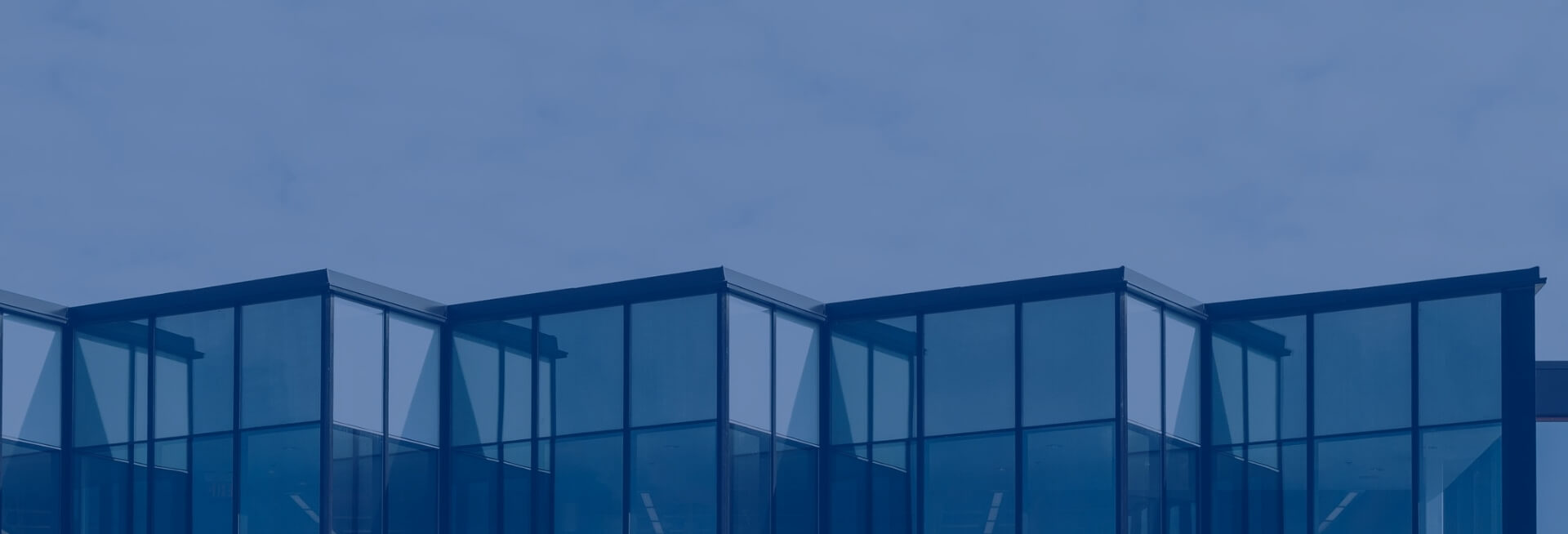
Get Started Now!
It takes less than a minute of your time. Or you may simply call +971 2 555 1 783