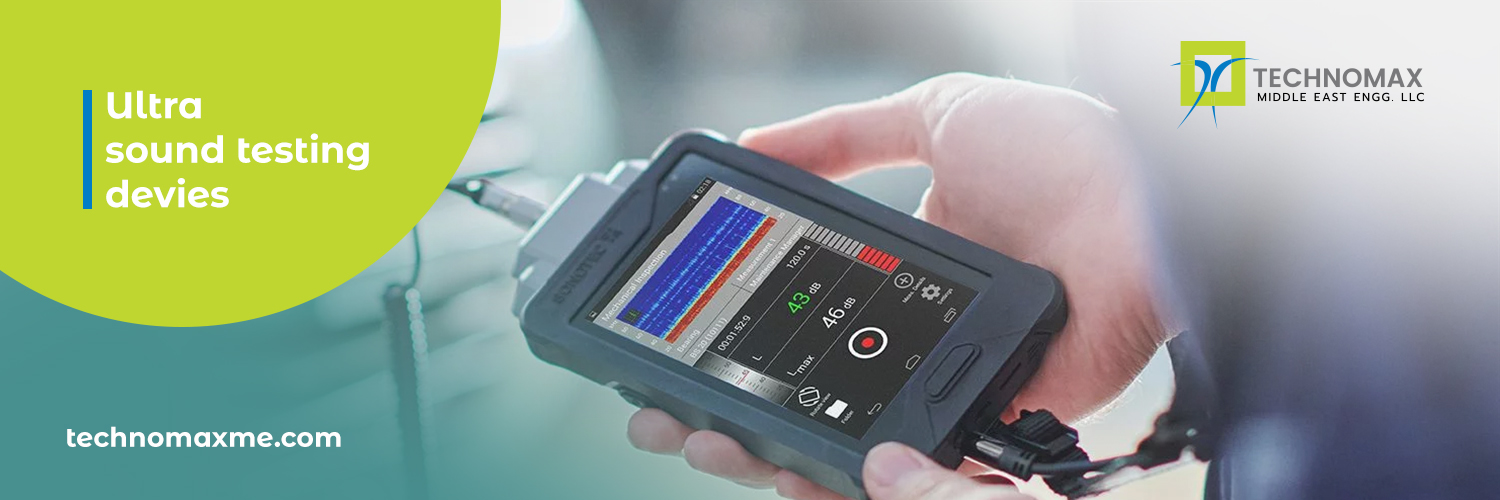
What is Ultrasonic Testing?
Ultrasonic testing is a procedure to measure & record ultrasonic waves (frequency >20KHz) that propagate through the medium (Solids and liquids) to determine irregularities related to friction in bearings and air/gas leakages. Steel, aluminium, power sector, oil & gas, manufacturing, aerospace, automotive, and many other industries use this testing mechanism to improve plant reliability.
Read more about Ultrasonic Testing Devices.
How is it performed?
In ultrasonic testing, an ultrasound transducer (a device that converts ultrasound energy to electrical energy) will be used to inspect with the help of diagnostic equipment.
There are two types of transducers based on the application,
- Air borne
- Structure Borne
Airborne ultrasonic inspection will be carried out to determine air/gas leakages in critical industries which will not only affect the efficiency of the plant but also pose a greater risk to personal safety in hazardous emissions. In this testing, the transducer will be used without having to contact and can be inspected with distances up to 15 meters using different kinds of sensors like parabolic.
You may also like to read:
- Why Do Steam Traps Fail: Causes, Factors & Preventive Methods
- Electrical Preventive Maintenance and Scalable Services
- Maximising Plant Productivity Through Machinery Diagnosis
Any kind of air/gas leakage will generate ultrasonic noise due to the turbulence at the leakage location and the sensor on proper aiming will generate proportional noise levels in the diagnostic instrument which in turn helps us to calculate cost loss per year with provided data by the manufacturer with the help of SONOTEC leak loss calculator.
Structure-borne ultrasonic inspection will be carried out to determine the irregularities related to bearing deterioration and steam trap malfunction in industries with critical rotating machinery which improves the machine component lifetime efficiency.
In this testing, the transducer will be used by placing it on the component surface. Any kind of irregularities inside the roller bearing will generate ultrasonic noise due to the friction between the components and the sensor will generate a spectrum proportional to the abnormalities.
Features of Ultrasonic Testing Devices
- Early fault detection in the bearing diagnosis and suitable for monitoring the condition of the machine.
- High sensitivity allows the detection of even the tiniest abnormalities.
- In assessing the depth of internal defects and the minor air/gas leakages, this method is more accurate than other nondestructive methods.
- Has the capability to predict the amount of leak by providing manufacturer data.
- Non-hazardous to other operations or surrounding employees and does not affect nearby equipment and materials.
- Portable and fully automated operation is possible.
- The results are immediate. Corrective measures can be implemented immediately after the inspection.
Major Industrial Application of Ultrasonic Testing Devices
Ultrasonic testing, a non-destructive testing procedure, is perfect for finding leaks and defects without causing damage to the object or material being examined.
Periodic ultrasonic examinations can also be used to check for bearing health conditions, lubrication management, steam trap inspection, and compressor air leaks.
1. Efficient Lubrication Management:
Ultrasonic can be used to lubricate machine bearings for implementing condition-based maintenance rather than time-based maintenance.
2. Bearing Health Monitoring and steam Trap Inspection:
Ultrasonic can be used to Monitor bearing & steam trap health conditions periodically and can be helpful to plan maintenance action well in advance and improve overall plant reliability.
3. Air/Gas Leak detection:
Ultrasonic can be used to inspect and record air/gas leaks at all compressed pipeline joints and will improve overall plant efficiency and provide cost-saving applications.
Read more about:
- Equipment Performance Monitoring – Our Approach
- Vibration Motion Magnification by Technomax
- Turbo Machinery Analysis and Balancing
Ultrasonic Testing Devices and Equipment for Preventive Maintenance Offered By Technomax
1. SONAPHONE® Pocket
Compact Ultrasonic Testing Device for Preventive Maintenance
Numerous preventive maintenance tasks can be handled quickly and efficiently with the SONAPHONEPocket.
Lower your energy costs and increase your operational safety with the most compact testing device of the SONAPHONE series. The device is perfectly suited for:
- Leak detection on compressed air systems
- Condition monitoring
- Detection of partial discharges
- Tightness testing
2. SONAPHONE®
Digital Ultrasonic Testing Device for Preventive Maintenance
In the age of Industry 4.0 optimizing processes, increasing operational safety, and improving energy efficiency are becoming more and more significant. Meet the challenges of Maintenance 4.0 with the new SONAPHONE from SONOTEC.
The digital ultrasonic testing device combines innovative sensors and software for preventive maintenance that can be operated intuitively and paves the way for new processes for new
- Intuitive Web and App Concept
- Optional modular PC software platform for Measurement point organization | Route planning Trend analysis | documentation
- Bundle important information about the measuring point
- Broadband ultrasonic analysis
- Test reports with just a few clicks
- 5-inch display with multi-touchscreen
- Realizing Maintenance 4.0
3. SONAPHONE® E
ATEX Certified for the Use in Areas With Risk of Explosion
Due to its intrinsically safe construction, the SONAPHONE E is suitable for use in the most hazardous areas and potentially explosive atmospheres.
In addition to the reliable location of compressed air and gas leaks, the ultrasonic testing device is also suitable for tightness testing of various systems, wear control on rotating machinery, and providing evidence of partial electrical discharges where there is insulation damage.
The checking of steam traps and valves is another application covered by the handheld device.
- For use in potentially explosive atmospheres
- Integrated data logger
- Multifunctional testing device
- Easy handling
Conclusion
The power generation, oil and gas, transportation, and manufacturing industries employ large, expensive equipment or machinery. Nondestructive testing is used in these industries to identify whether or not important machinery needs maintenance or repairs.
Technomax offers a wide range of ultrasonic nondestructive testing machines for use in these sectors. This increases machine life and reduces the need for capital expenditures to replace critical equipment. It also guards against system failures.
Nondestructive testing is available in a variety of forms, each with its own set of advantages and disadvantages.
Ultrasonic testing is a widely used, practical, and low-cost method. Ultrasonic testing equipment from Technomax can quickly, effectively, and economically provide an image of the material's internal structure.
Learn More About Our Services
Recent Blogs
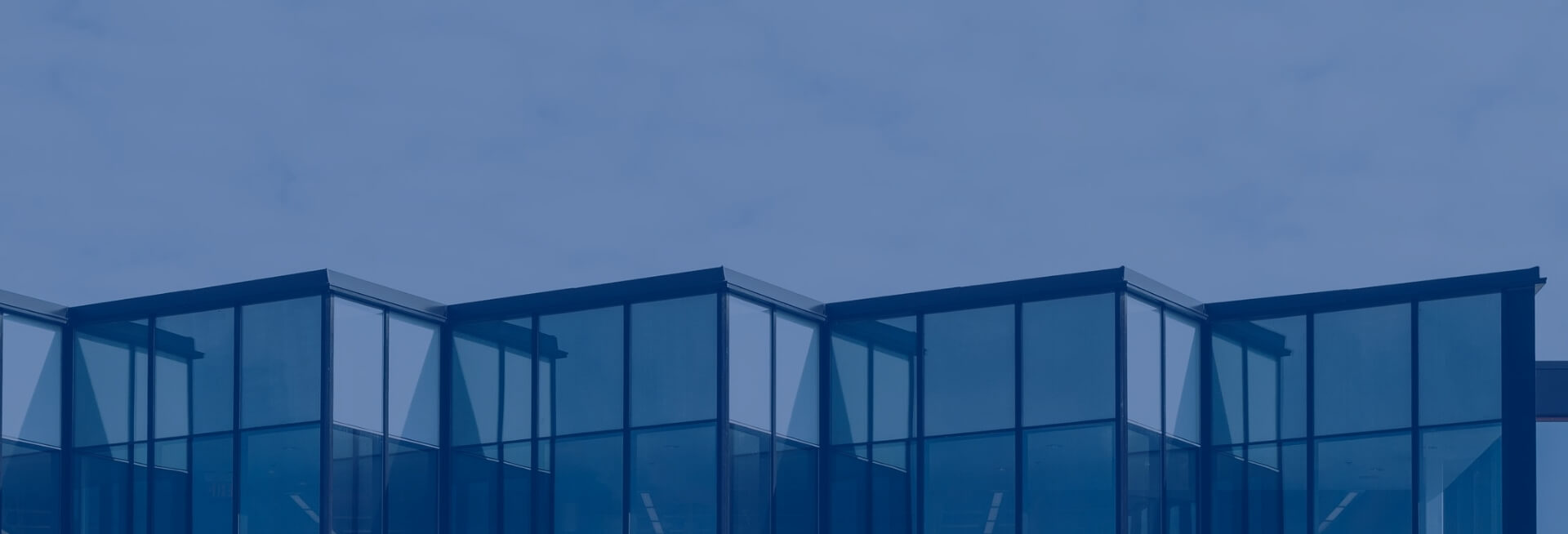
Get Started Now!
It takes less than a minute of your time. Or you may simply call +971 2 555 1 783