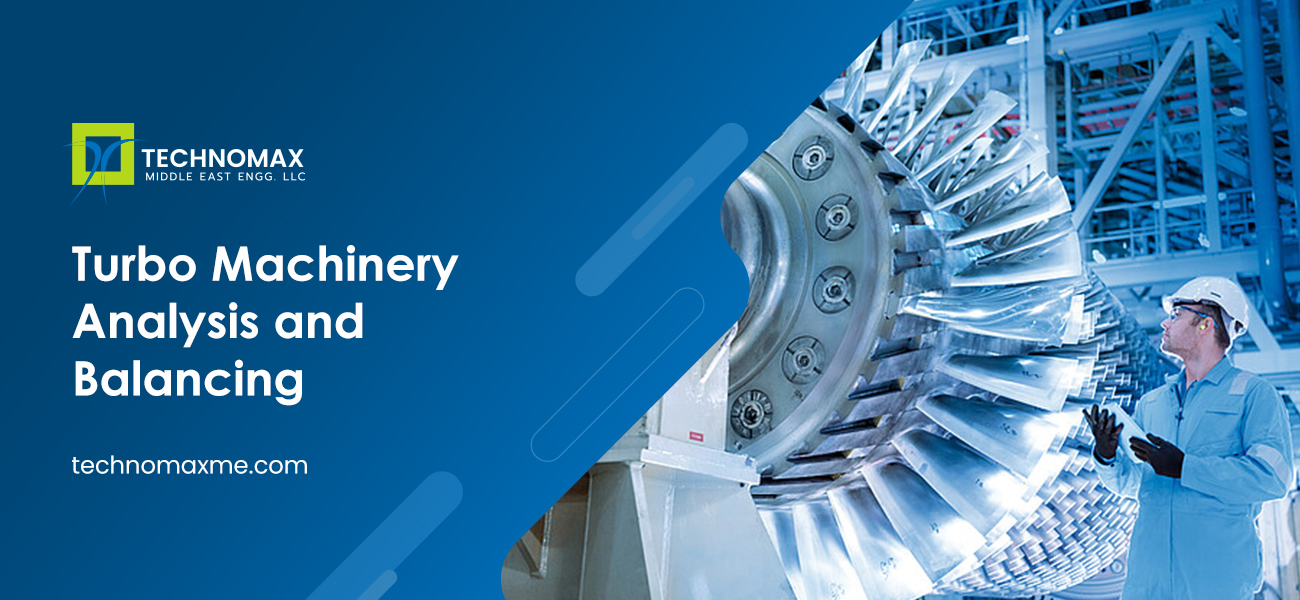
Introduction:
Generally, when a machinery experiences high vibration at 1X running speed, the first course of action that an analyst thinks is to improve balance of the rotor. The purpose of balancing a rotor is to help ensure that the machinery is safe and reliable, this is achieved when a rotor mass and rotational centerline are as close to equal as possible. Excessive unbalance causes vibrations that minimize the engine performance and deteriorate the whole system.
This blog gives insights into the causes, effects, and uses of turbomachinery analysis and balancing in detail.
Read more about:
- Rubber Tyre Gantry Cranes(RTG Crane): An Overview
- Vibration Motion Magnification by Technomax
- Equipment Performance Monitoring – Our Approach
Causes of Unbalance:
- Foreign particles/dust deposition on impeller.
- Asymmetric weight distribution on the rotor.
- Removal of components/previous weights on the impeller.
- The over speeding adopted in the turbo can cause components to wear down and leads to a shaft imbalance.
- Machine imbalance can be due to various reasons like rotor corrosion/erosion, bearing or seal issues, improperly balanced rotors, etc.
Vibration is the main characteristic that occurs if the system is unbalanced, which will cause severe damage to the equipment when it becomes the catastrophic failure and will cause below consequences.
- Production loss
- Unplanned breakdowns
- Manpower cost
- Equipment performance will reduce.
- Even causes damage to shafts, bearings, seals etc.
- Unbalanced turbos can also minimize engine performance, but this could go unnoticed initially. However, this would be the major reason behind the potential failure of the system.
How do Turbomachinery Analysis and Balancing work?
Balancing can be carried out either in-situ or on the test bed balancing machines. A pair of proximity probes were installed on the bearings along with a key phaser for speed reference. Absolute phase angles and vibration data collected initially before balancing.
There are 3 types of unbalanced conditions such as Static, Coupled and Dynamic Unbalance. By choosing the appropriate method the balancing is carried out as per the ISO standards 1940 (G6.3 & G2.5) for such class of equipment.
You may also like to read:
- Maximising Plant Productivity Through Machinery Diagnosis
- Keeping it on the rails: The Importance of Overhead Crane Runway/Rail Inspections
- Electrical Preventive Maintenance and Scalable Services
Final Note
Are you a company that manages impeller overhauling, or a production firm that requires balancing services for the turbo systems?
Only a team of specialists can assist you with promising solutions for precise balancing needs.
Technomax has been working continuously to deliver promising turbomachinery analysis and balancing services to augment the operations of turbo systems.
Our team of experienced engineers understand and analyse your turbo systems to analyse critical speeds, diagnose the machine faults, implement on-site balancing, monitor the machine periodically, and support the start-up tests after overhauling.
Learn More About Our Services
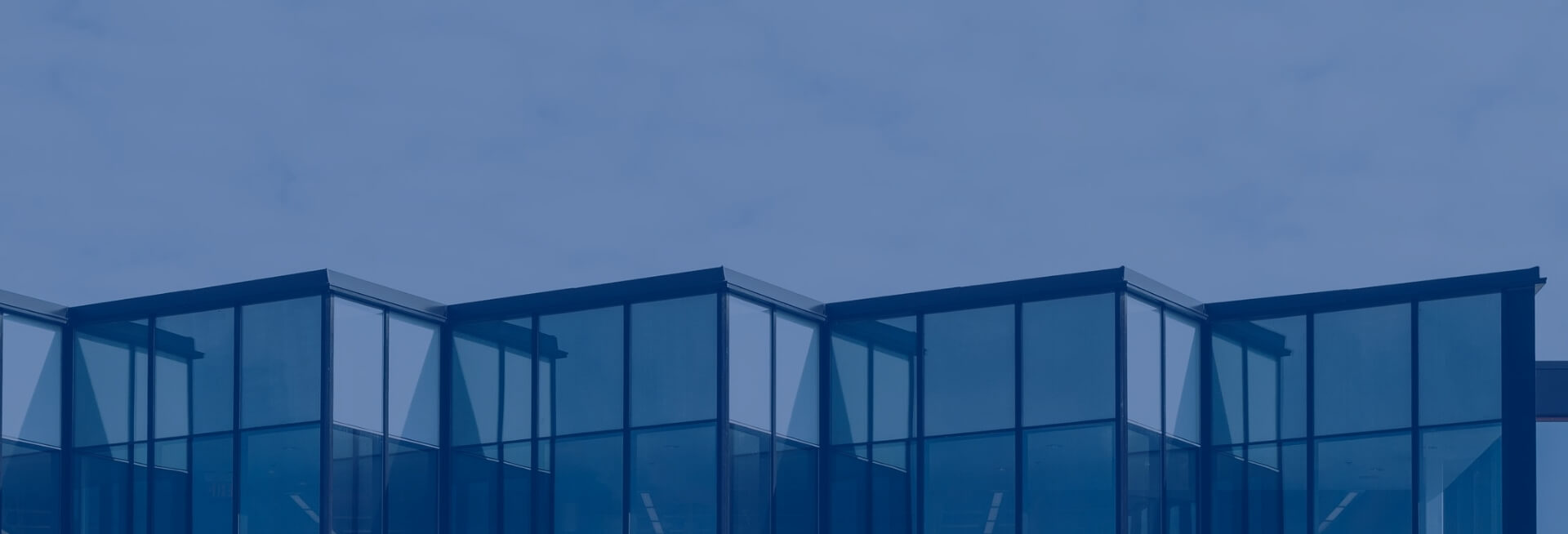
Get Started Now!
It takes less than a minute of your time. Or you may simply call +971 2 555 1 783