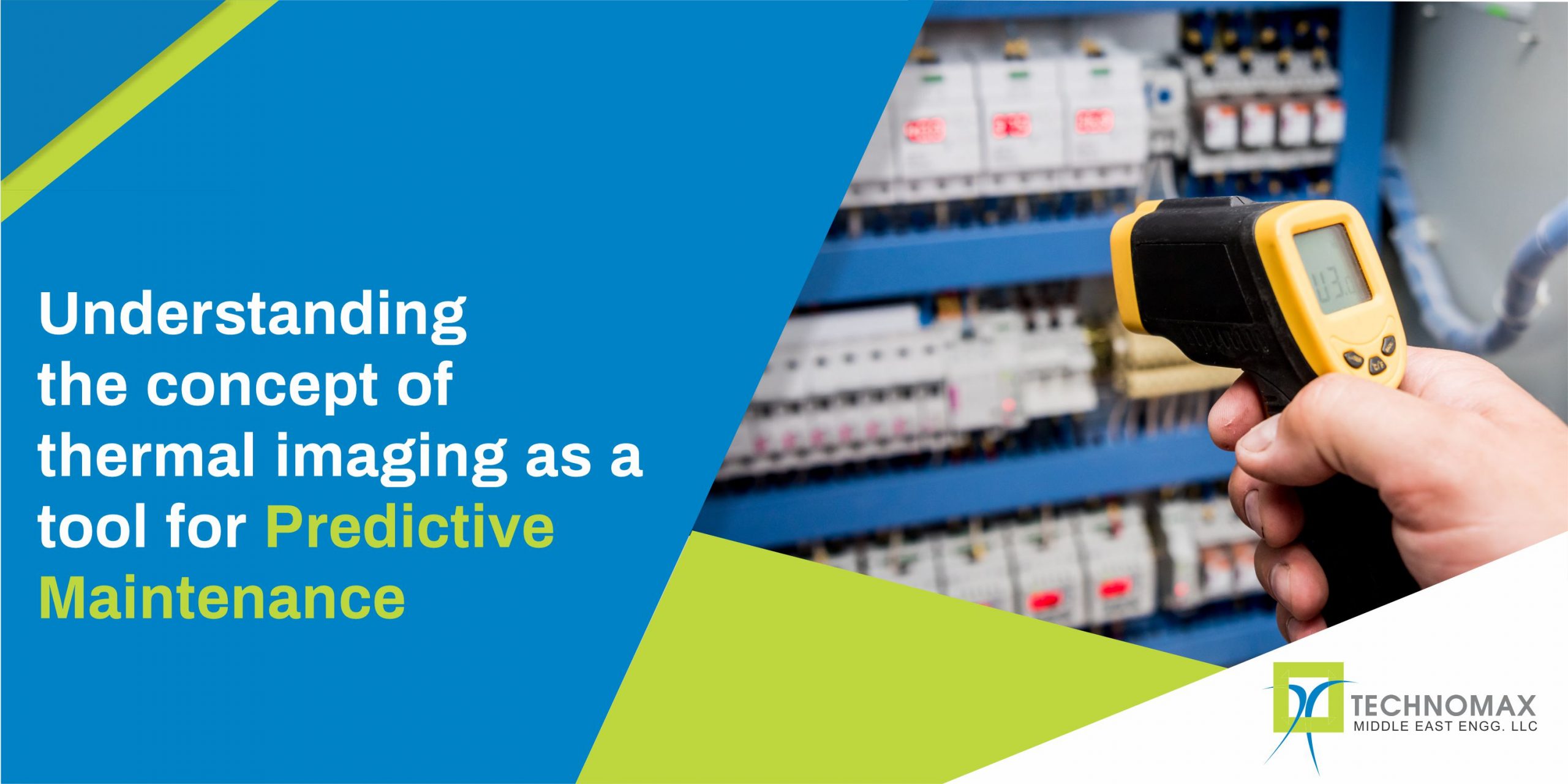
Understanding The Concept Of Thermal Imaging As A Tool For Predictive Maintenance
Introduction to Thermal Imaging
The simplest definition calls it a method of utilizing the heat given off by an object to produce an image. This means that highly efficient thermal imaging cameras convert heat into visible light. Machinery and electrical equipment may give out heat thus exposing them to thermal imaging devices even in pitch darkness.
Thermal Imaging technology is designed to work in the total absence of light as it does not need visible light for its functioning. Thermal imaging devices work even in hazy and foggy weather conditions and have widespread applications in industry.
Living beings and objects emit heat that comprises visible light and infrared radiation both of which form part of the electromagnetic spectrum. Visible light, in fact, is a very minute part of this spectrum. The infrared radiation that is emitted by the skin, in living creatures, and by objects with heat, is what thermal imaging devices capture for further analysis.
Read more:
- Understanding The Concept Of Wireless Condition Monitoring
- Understanding The Concept Of Thermal Imaging As A Tool For Predictive Maintenance
- Principles and Applications Of Infrared Thermography
How Does Thermal Imaging Work in Predictive Maintenance?
The devices, sensitive to even small differences in temperature, pick up radiation from the objects in the surrounding area, and segregate the data basis its “heat signature”. Heat signature denotes the level of thermal radiation emitted by objects and all such data sourced by thermal imaging devices are compiled and put onto a “heat map”. Thermal imaging is a very effective, efficient, and compact technology using simple cameras that monitor, heat sources, by focusing with the help of crosshairs.
Advanced devices can accommodate multiple crosshairs to enable comparison. Colour options can be as simple as monochrome to a full-fledged palette. By default, the conventional thermal images were 100% in grayscale wherein white would represent heat and black would denote cold regions. The shades in between would signify varying levels of temperature. Newer models have evolved with the times and offer a full-color palette to help users distinguish objects and temperatures more clearly.
The devices help safety professionals inspect earmarked areas at defined intervals to quickly map out risk areas and look for speedy resolutions. With data readily available, the role of the safety professionals is focused on resolving the problem rather than spending disproportionate time identifying the problem and its magnitude.
Powering the Devices
The thermal sensing and imaging devices run on either AC or DC power and can be easily placed or moved to required locations. The batteries give a solid backup of up to 2 days when used conservatively and almost 15 hours when used normally.
The devices can be positioned at different angles, preferably 15 to 20 feet from the equipment, to capture quality images. The sensors can be stuck on the allocated places using adhesives or agnets. These devices can also work on the principle of the thermostat by alerting when defined temperature thresholds are breached.
Thermal Imaging for Predictive Maintenance
There are different kinds of Predictive maintenance plans. For eg- Preventive maintenance has now evolved into predictive maintenance that helps save billions of dollars each year. The necessity to sense impending failure and the alacrity in responding with defined turnaround times (TATs) can prevent major failures that can cause loss of life besides money. Heat is the first red flag and almost always one of the earliest indicators of a fault while cold spots could mean failed fuses.
Electrical engineers use thermal imaging to locate parts that are at risk of fault. The faulty parts would start emitting more heat as compared to the healthier ones. They also help find loose wiring. In transformer commissioning, tests can be easily run to ensure that the transformer is correctly installed.
Riding on the Multiplier Effect
Simultaneously and continually capturing images from more than one component and equipment is one of the key upsides in recent generations of thermal sensors thus redefining the concept. Modern sensors are always ON and keep transmitting observation data in real-time to a central monitoring desk.
The monitoring desk can send technicians only when a failure is predicted rather than deploying staff at every location. They can also compare images across locations, determine priorities, and decide whether problems can be included in regular maintenance or need immediate attention. This adds to the money saved in addition to the amount already saved by preventing major failures well in advance.
An Ideal Thermal Imaging Device
There are a wide variety of options available in this segment and the right one depends on the extent of usage, the environment in which it would be used, and the choice of infographics to display output. However, thermal sensitivity and resolution will be two critical parameters to look for when selecting a device.
The quality of the display, as is the case with any display, depends on the resolution that is in turn based on the number of pixels. Every pixel would have some associated thermal data and therefore larger displays produce clearer imagery.
Top Advantages & Benefits of Thermal Imaging As A Tool For Predictive Maintenance
- Continuous monitoring and multi-device,multi-image capturing capability
- Convenience and ease of installation, positioning, and movement
- Auto flags basis pre-defined thresholds and centralized data capturing
- Flexi power source and solid battery backup
Remote Monitoring
The images captured by sensors are sent and stored in the cloud. As wireless sensors are used, there is no need for wiring cabling or, connection to any local networks. Apps for both PCs and smartphones are available for wireless transfer and real-time monitoring.
The apps also help in generating reports and infographics so that managers can make decisions quickly rather than spend time trying to understand the raw data.
Conclusion
Irrespective of industry or equipment, the necessity to predict equipment failure can no longer be undermined. The loss to the organization, life, and even public property at large is a real possibility if the situation goes out of control. Thermal imaging is now one of the widely accepted, adopted, and effective tools in condition monitoring.
The underlying logic is simple and obvious. Heat is a very clear and early signal of a fault whereas cold spots denote component failure. Patterns captured and projected on heat maps with effective use of colour imaging techniques can help in quicker identification and resolution.
Learn More About Our Services
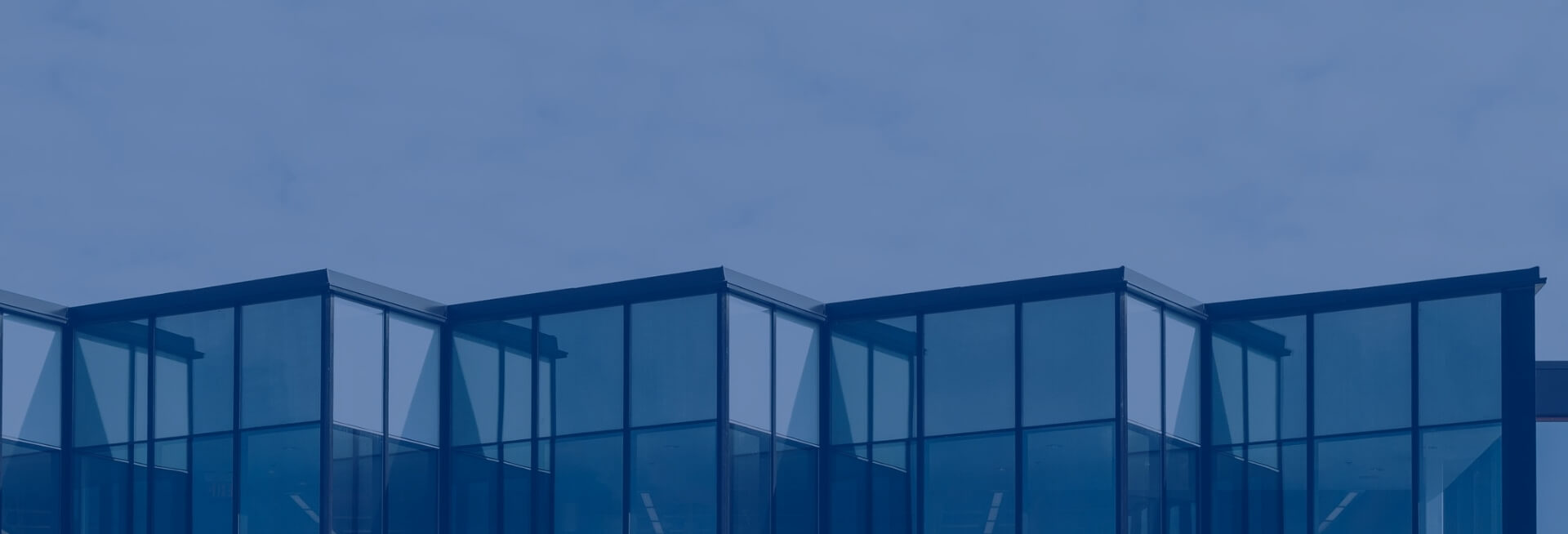
Get Started Now!
It takes less than a minute of your time. Or you may simply call +971 2 555 1 783