- Services
- Performance Analysis of Compressor
Performance Analysis of Compressor
Conducting a thorough examination of a compressor’s performance is critical in determining its effectiveness, dependability, and overall efficiency in meeting operational requirements. Compressors are widely used across a variety of industries, including manufacturing, oil and gas, and HVAC systems, to increase the pressure of gases or air for different applications. By conducting a comprehensive performance analysis, organizations can identify areas for improvement, optimize energy consumption, and ensure the optimal functioning of the compressor. Read more about Performance Analysis of Compressor.
The process of examining a compressor's performance typically involves the following steps:
- Collecting operational data: The initial step is to gather relevant operational data, including information about the compressor's specifications, design parameters, and operating conditions. This data can include compressor type, capacity, discharge pressure, suction pressure, temperature, power consumption, and flow rates. It is essential to ensure accurate and comprehensive data collection for a reliable performance analysis.
- Determining energy efficiency: Energy efficiency is a key performance metric for compressors. It represents the ratio of the output work (compressor discharge pressure) to the input energy (power consumed). By determining energy efficiency, organizations can assess how effectively the compressor converts the input energy into the desired output. Energy efficiency can be calculated using formulas and industry standards or by utilizing specialized software.
- Evaluating capacity and performance: The capacity of a compressor refers to its ability to deliver a specific volume of gas or air per unit of time. Performance analysis involves assessing whether the compressor is operating at its intended capacity or if there are deviations. It is important to compare the actual performance of the compressor with its design specifications and industry standards. Any discrepancies may indicate issues that require attention, such as wear and tear, leakage, or inadequate maintenance.
- Assessing pressure differentials: Pressure differentials across the compressor are crucial indicators of its performance. Analyzing pressure differences at different points within the compressor system can provide insights into the condition of the compressor. Deviations from expected pressure differentials may indicate problems such as obstructions, leaks, or inefficiencies in the compressor itself. Measuring and monitoring pressure differentials help identify potential issues and guide appropriate corrective actions.
- Monitoring vibration levels: Abnormal vibration in a compressor can indicate mechanical issues or unbalanced. Evaluating vibration levels can help pinpoint potential problems such as misalignment, deteriorated bearings, or impaired impellers. Vibration analysis involves utilizing specialized equipment to measure and evaluate the vibration levels, contrasting them against recommended industry norms or manufacturer specifications. Recognizing and addressing vibration problems promptly can prevent further impairment to the compressor and enhance its performance.
- Analyzing maintenance documents: Maintenance plays a vital role in the operation of a compressor. Scrutinizing maintenance records, including maintenance schedules, repair history, and downtime incidents, can offer insights into the dependability and availability of the compressor. By identifying recurring issues or maintenance practices that may affect performance, organizations can devise strategies to improve dependability, decrease unplanned downtime, and optimize maintenance schedules.
- Environmental factors: Performance analysis for compressors may also involve assessing ecological factors. Appraising discharges, noise levels, and energy efficiency can help organizations identify opportunities to reduce the ecological footprint of the compressor and comply with regulations. Optimizing energy consumption and adopting energy-efficient practices contribute to ecological sustainability and cost savings.
- Continuous enhancement: Performance analysis of a compressor is an ongoing process aimed at achieving continuous enhancement. Regular monitoring, data collection, and analysis enable organizations to track performance trends, set goals, and implement corrective actions when deviations are identified. Establishing a culture of continuous enhancement encourages feedback, data-driven decision-making, and knowledge sharing among team members.
Wrapping Up
In summary, performing a performance analysis of a compressor involves assessing factors such as energy efficiency, capacity, pressure differentials, vibration levels, maintenance records, and environmental factors. By conducting a comprehensive analysis, organizations can optimize the performance of the compressor, improve energy efficiency, reduce downtime, and ensure reliable operation. Continuous monitoring and analysis allow for proactive maintenance and the identification of opportunities for process optimization and cost savings.
Other Services & Products
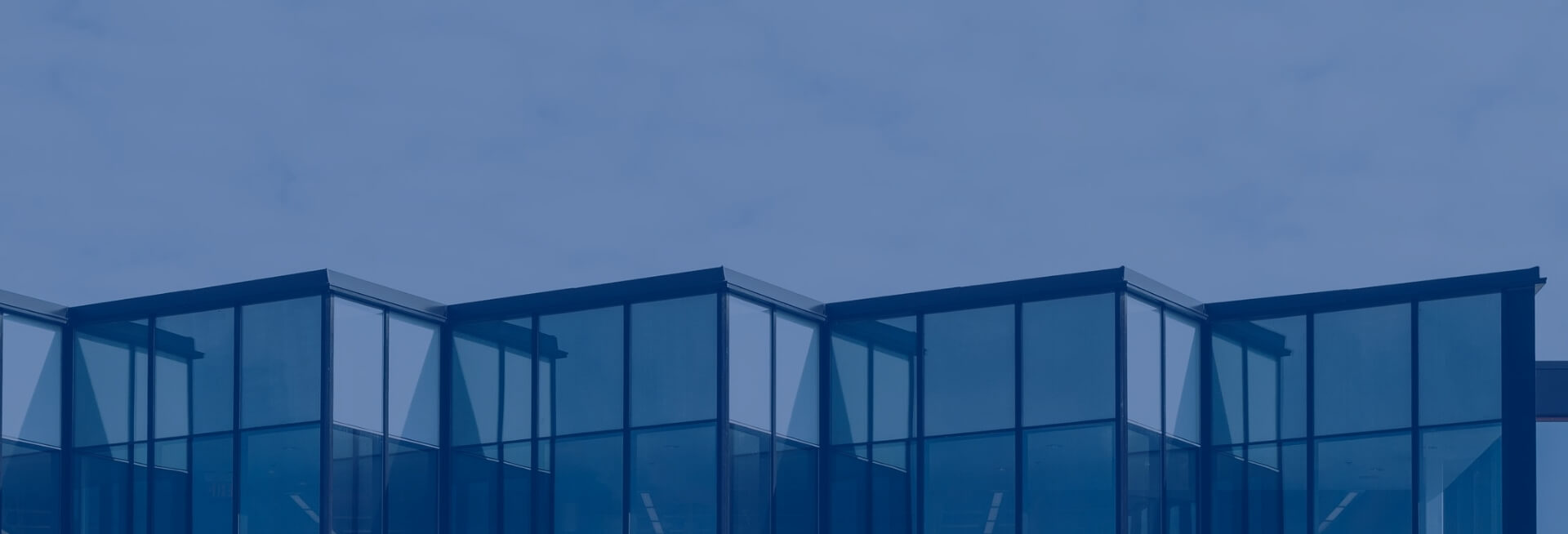
Get Started Now!
It takes less than a minute of your time. Or you may simply call +971 2 555 1 783