- Services
- Lube Oil Analysis
Lube Oil Analysis
Lube Oil testing may be defined as a systematic analysis of oil health, contamination, and wear at regular intervals. Technomax’s oil testing service validates that a lubricated machine is operating according to expectations and predetermined standards. It can be seen as a routine predictive maintenance activity to furnish meaningful and accurate information on lubricant and the overall condition monitoring of the machine.
Lube Oil analysis is one of the processes utilised by Technomax in its condition monitoring services in the UAE. The sample results obtained over the life of a machine can be used to discover trends, which can help save us from costly repairs. Lube Oil analysis can also be used to schedule maintenance before a critical failure occurs, such as crane operating problems, to save money.
Types of Lube Oil Analysis we provide
Fluid Properties
This type of lube oil testing focuses on identifying the oil’s current physical and chemical state and defining its remaining useful life. It is a type of inspection of the oil’s constituents based on their age and composition to prevent the machine from wearing out and losing its usable life.
Contamination
This is a process of testing the quality of oil so as to identify the extent of purity of the same and the contaminants(if any), which tend to reduce the useful life of the oil, leading to the erosion of the machine, by detecting the presence of destructive contaminants and narrowing down their probable sources, either external or internal.
Wear Debris
Wear debris is arguably the most popular form of oil testing. It is primarily concerned about determining the presence and identification of particles produced due to mechanical wear, corrosion or other machine surface degradation.
Benefits of Lube Oil Analysis
The benefits of lube oil Analysis are primarily of two types:
Maintenance Cost Savings
Oil mix up is one of the most common lubrication problems contributing to machine failure. Putting the right lubricating oil in a machine is a simple task that can improve machine reliability. Checking the viscosity, brand and grade of incoming oil and checking for contamination of alien fluids helps reduce the chances of oil mix up and keep the machines running at optimal efficiency. To keep the oil dry, clean and free of contaminants, seals and filtration systems need to work properly, and oils should be checked regularly. Sand and dirt in oil cause abrasion. Moisture in oil causes corrosion. Fuel or coolant in engine oil changes viscosity and causes abrasion again. It is necessary to keep the lubricating oil clean and dry at all times. This, in turn, keeps the machine healthy and avoids any failure of the same, which consequently is known to reduce maintenance cost and unwanted repair charges.
Increase Productivity
With a well-defined schedule for condition monitoring and preventive maintenance involving a thorough testing routine for oil contamination, one can ensure that the machine keeps working efficiently. This can reduce production losses due to any unwanted machine failure and save on the production time that could have gone waster.
Why Choose Technomax’s Lube Oil Analysis Service?
Predictive maintenance programs for Oil Condition Monitoring (OCM) or Used Oil Analysis (UOA) help customers avoid expensive machinery, engines, and powertrain failures by monitoring changes in machinery lubricant quality. Provide vital “early warning” of impending problems and support the smooth and reliable operation of machines. Operational issues on machines, engines, and other components are usually reflected in the condition of the used lubricating oil. Regular monitoring of oil conditions or used oil analysis can identify mechanical problems before they affect the efficient operation of the machinery, avoiding costly headaches in the future.
Often lubricants must function under demanding conditions, exposed to pressures, temperatures, and other damaging factors, including water contamination, corrosion, fuel, and airborne particles. High levels of wear particles provide early warning of possible machine malfunctions, enabling timely corrective action. When analytical results suggest that undue wear is not occurring, the operator can extend the interval between services or oil changes. Scheduled lubricant testing and expert advice can prevent and mitigate costly components or system failures and unscheduled maintenance.
Other Services & Products
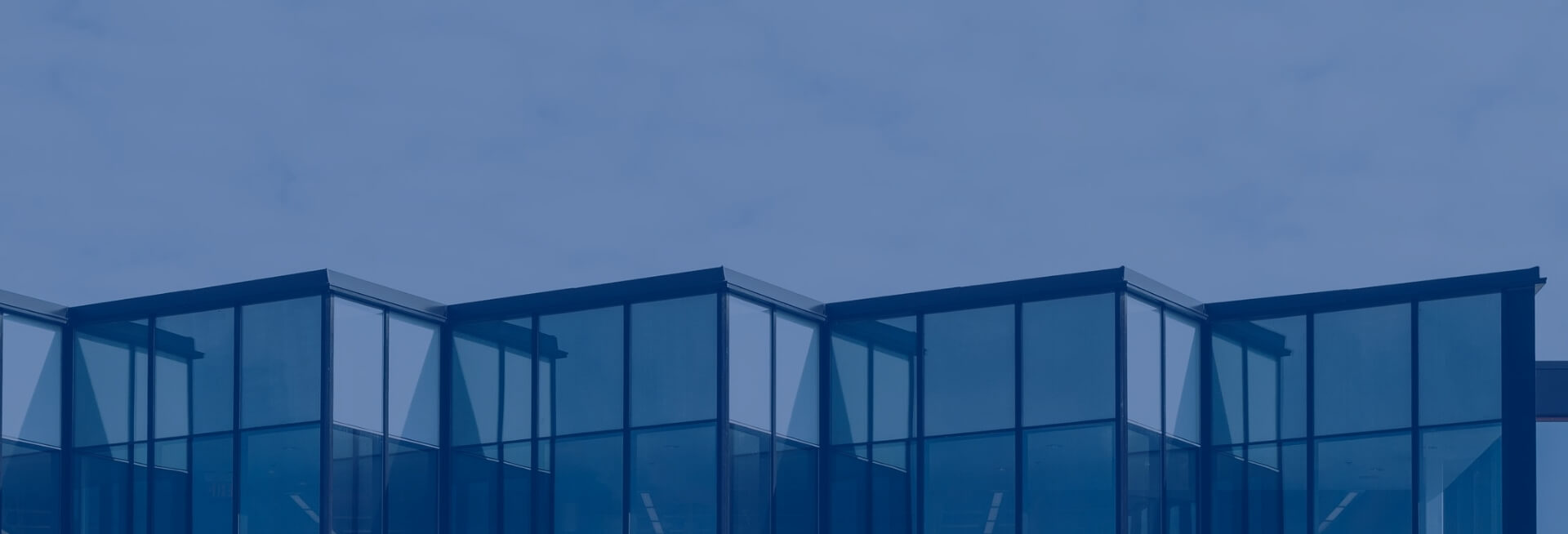
Get Started Now!
It takes less than a minute of your time. Or you may simply call +971 2 555 1 783