- Services
- Gearbox Vibration Analysis
Gearbox Vibration Analysis
A Gearbox plays a vital role in various industrial processes and because of its criticality, the condition should be monitored closely to prevent any catastrophic failure and prevent huge production losses. Vibration analysis is the most effective predictive maintenance method to detect faults in gearboxes at the early stage itself so that the necessary steps can be taken to prevent failures. Each gear component vibrates differently, creating a distinct pattern. This pattern undergoes a change when there is a fault.
The symptoms differ when the problem is due to damage, imbalance, misalignment etc. The vibration data are collected using a field vibration analyzer. Vibration analysts will be able to diagnose the cause and source of vibration after the detailed spectrum analysis. Conducting vibration analysis in the gearbox helps to predict the faults at the early stage itself thereby helping the maintenance department to schedule the maintenance in advance with a proper plan, resources and tools avoiding the chances of any potential safety concerns.
Intro
The Engineer measures the vibration of the machine gearbox using a real time portable vibration analyzer. Each gear component vibrates differently, creating a distinct sound pattern. This pattern undergoes change when there is a fault. As the symptoms are different when the problem is due to damage, imbalance, or misalignment, it helps the engineer to identify the problem. Causes of gear failure could be due to manufacturing or application errors, poor design or maintenance error. Gearbox vibration analysis will be done using vibration analysis methods like frequency or time domain, envelope, order, circular plot, or phase measurement analysis.
Benefits of Gearbox Vibration Analysis
- Gearbox vibration analysis conducted by Technomax helps in identifying and resolving gearbox faults.
- It allows the technicians to understand the underlying cause of the damage – misalignment, extreme wear or backlash, overload, high friction, broken teeth, or assembly/manufacturing defects.
- Early detection of potential problems allows management to plan and schedule maintenance and servicing of equipment, like conducting oil analysis, improving quality control measures, etc.
- This translates into significant time and cost savings, and uninterrupted flow of work.
- You can extend the life of the equipment by ensuring no damage to the gearbox.
How is Gearbox Vibration Analysis Done at Technomax?
- In predictive maintenance methods like gearbox vibration analysis, our engineers check the level and frequency of the vibration of the gears to identify and fix problems. Some vibrations are normal, even expected. A baseline of the vibration spectrum is established so that the abnormal vibrations can be pointed out easily.
- Next, the vibration signals are expressed in digital form, and then converted into frequency spectrum to analyze machinery defects.
- In gearbox vibration analysis, different kinds of complicated vibration signals are observed, with some of them being random noise, some inherent operating frequencies, and some are failure frequencies. There is increased amplitude in the sidebands; the differences in the amplitude tell the engineers what the exact problem is.
Other Services & Products
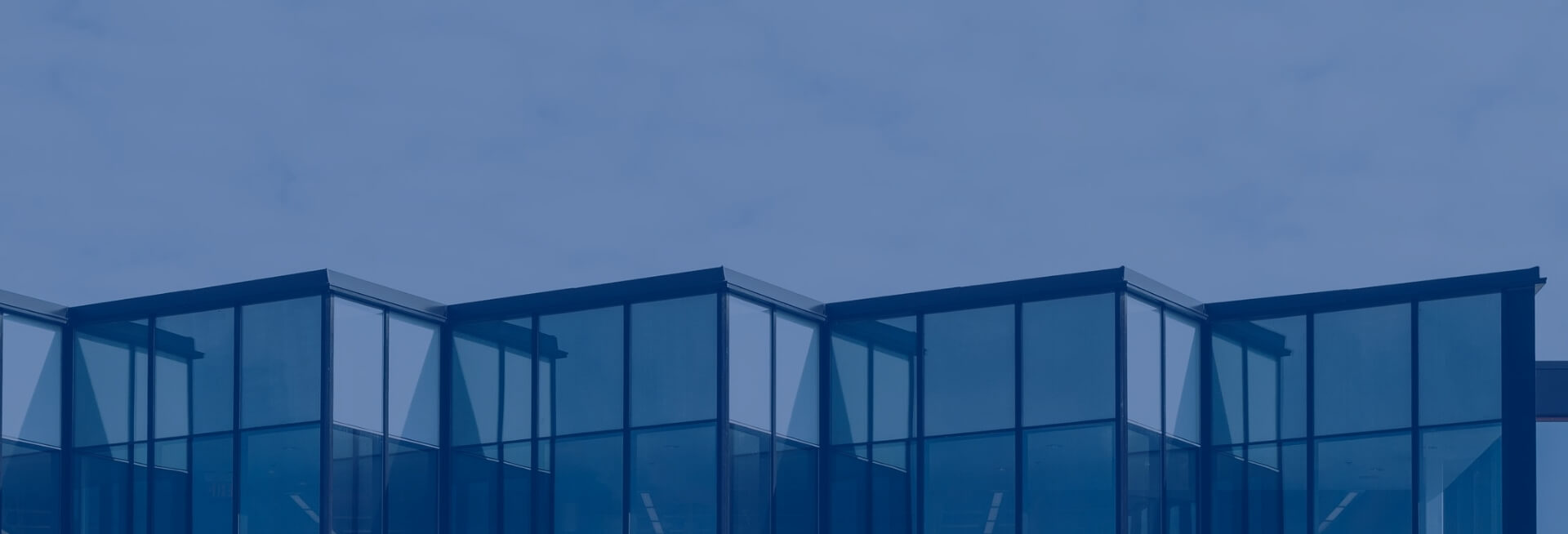
Get Started Now!
It takes less than a minute of your time. Or you may simply call +971 2 555 1 783