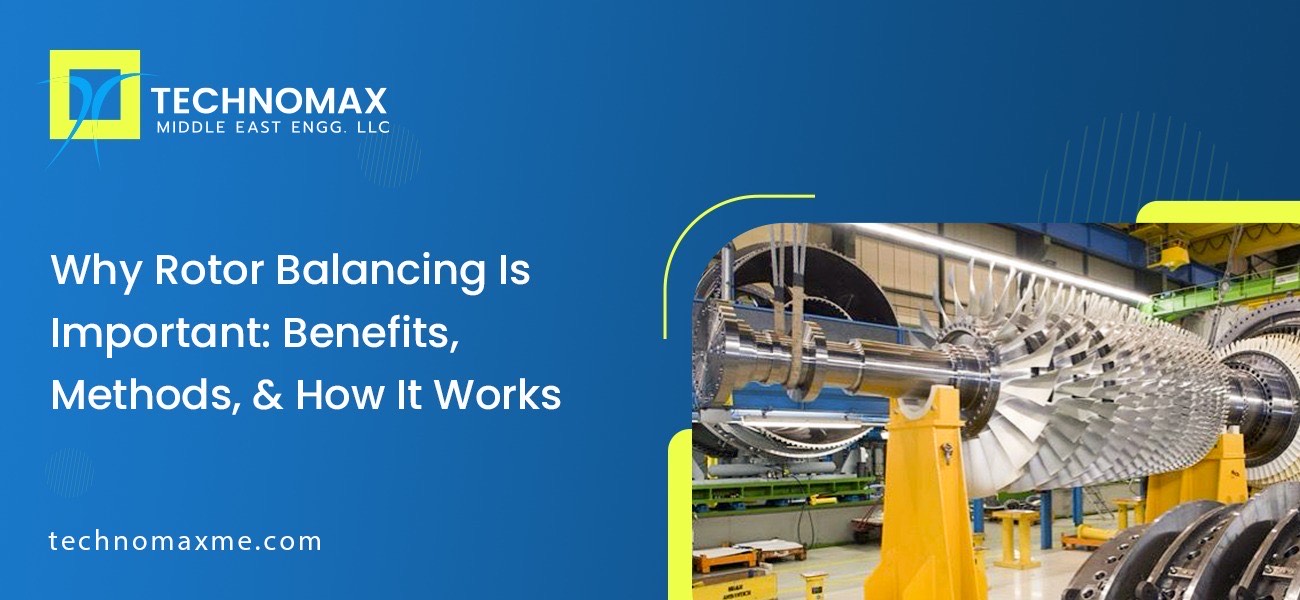
Rotor balancing is important in rotating machinery which plays an important role in countless industries, from power generation and transportation to manufacturing and healthcare. This machinery’s rotor, an essential part that spins at high speeds, is located at its centre. However, without proper balancing, these rotors can generate vibrations that can lead to a cascade of problems, impacting performance, longevity, and safety.
This blog discusses the significance of rotor balancing, its benefits, and the various methods used to achieve the best performance.
What Is Rotor Balancing?
Rotor dynamic balancing refers to the process of equally distributing the rotating mass of a rotor around its axis of rotation. This complex procedure is realised either by the addition or deduction of components from the rotor or by modifying the positioning of the existing material on the rotor. When a rotor is erroneously balanced, the ensuing vibration throughout rotations can lead to a plethora of issues, such as:
- Accelerated wear and tear on bearings and other major components.
- Increased noise and disruptive vibration.
- Noticeable decrease in efficiency and overall performance.
- Potential safety hazards.
Rotor balancing plays a pivotal role in ensuring the optimal operation of any rotating machinery. It helps prevent potential mechanical damage, enhances performance, and significantly extends the lifespan of the machinery.
The Importance of Rotor Balancing
There are numerous reasons why rotor balancing is crucial for the maintenance and proper functioning of mechanical components, such as:
- Preventing machinery damage: An unbalanced rotor can cause excessive wear and tear on seals, bearings, and other major components, leading to breakdowns and reduced lifespan.
- Improved performance: Balancing the rotor reduces vibrations caused by imbalance, resulting in improved efficiency and performance of the machinery.
- Extended lifespan: Properly balanced rotors are less prone to wear and tear than unbalanced ones, leading to a significantly longer service life.
- Noise and vibration reduction: Unbalanced rotors generate excessive noise and vibration, disrupting personnel and potentially damaging the machine over time. Balancing mitigates these issues.
- Safety considerations: Unbalanced rotors can shatter, collapse, or disintegrate at high speeds, posing serious safety risks to nearby personnel. Balancing ensures a safe and stable operation.
Types of Rotor Groups and Their Characteristics
Rotors can be categorised into different groups based on their flexibility and operating speeds:
- Rigid rotors: These are stiff and maintain shape even at high speeds. Examples include electric motor rotors and turbine shafts. They are relatively easy to balance gas turbine rotors and typically require static balancing at low speeds.
- Flexible rotors: These exhibit some degree of deflection when rotating. Examples include turbocharger shafts and fan blades. Due to their flexibility, they require dynamic balancing at operating speeds to account for deformation.
- Gyroscopic rotors: These exhibit significant gyroscopic effects due to their high rotational speeds and mass distribution. Examples include helicopter rotors and wind turbine blades. Balancing these rotors requires specialised techniques to account for the complex interactions between rotation and gyroscopic forces.
Different Types of Rotor Unbalance
Rotor unbalance occurs when the mass distribution is uneven around the axis of rotation. This unevenness can lead to various types of imbalances, each with distinct characteristics:
-
Static Unbalance:
This occurs when the principal axis of inertia is displaced parallel to the shaft’s rotational axis. Common in rotors with centrally concentrated mass distribution, including narrow discs, flywheels, car wheels, and fan wheels.
Detection and Correction: Readily detectable by observing a rotating rotor on rollers or knife edges. The heavy spot will naturally settle at the lowest point. Correction involves placing an equal mass at 180° opposite to the unbalanced mass and at the same radius.
2. Couple Unbalance:
This takes place when two equal masses are placed at opposite ends of a rotor, separated by 180°. The inertia axis intersects the rotational axis at the centre of gravity but is tilted at an angle.
Detection and Correction: Unlike static unbalance, a couple unbalance does not exhibit self-rotation on rollers or knife edges. Requires dynamic methods for detection, such as vibration readings or centrifugal force measurements. Correction involves adding balancing masses opposite to the couple to restore balance. This process typically involves two planes of correction, often on hard-bearing balance machines.
3. Dynamic Unbalance:
The most prevalent type encountered in rotating assemblies. It occurs when the inertia axis neither intersects nor runs parallel to the shaft’s rotational axis.
Detection and Correction: Similar to couple unbalance, dynamic unbalance necessitates dynamic detection methods, usually involving vibration or centrifugal force measurements while the rotor is running. Correction requires adding balancing masses in two planes perpendicular to the shaft centre, with adjustments guided by the measurement data.
Causes of Rotor Unbalance and How to Prevent Them
Several factors can contribute to rotor unbalance, including:
- Manufacturing imperfections: Variations in material density, machining errors, and casting flaws can lead to uneven mass distribution within the rotor itself. Implementing robust quality control measures during manufacturing can help abate these issues.
- Wear and tear: Over time, components like bearings and blades can wear unevenly, causing the rotor to become unbalanced. Regular maintenance and inspections are essential to identify and address wear before it leads to significant problems.
- Deformation: Operating at high temperatures or under excessive loads can cause rotors to deform, leading to unbalance. Ensuring proper operating conditions and avoiding overloading of equipment can help prevent deformation.
- Improper assembly: Incorrect installation of components or missing parts can create an uneven mass distribution. Following proper assembly procedures and using qualified personnel can minimise these errors.
Phase Indications of Rotor Unbalance and Their Significance
Vibration sensors are used to identify and analyse rotor unbalance. The phase angle of the vibration signal provides valuable information about the type and location of the unbalance. By analysing the phase angles at different points on the rotor, technicians can determine the amount and location of mass needed to correct the imbalance.
Benefits of Rotor Dynamic Balancing:
The importance of proper rotor balancing cannot be overstated. Beyond ensuring smooth and efficient operation, it offers several critical benefits of rotor balancing:
- Reduced vibration: Unbalanced rotors generate excessive vibration, leading to noise, discomfort, and potential damage to surrounding equipment. Proper balancing minimises vibration, improves operator comfort, and protects the equipment.
- Extended lifespan: Unbalance increases stress on bearings, seals, and other components, leading to premature wear and tear. Balancing reduces stress, extending the lifespan of components and lowering maintenance costs.
- Improved efficiency: Unbalanced rotors consume more energy to maintain rotational speed. Balancing reduces energy consumption, leading to cost savings and improved environmental performance.
- Enhanced safety: Excessive vibration can lead to fatigue and failure of components, posing a safety risk to operators and personnel near the equipment. Balancing minimises vibration, ensuring a safer operating environment.
Balancing Standards and Guidelines:
Industry standards play a crucial role in ensuring rotating machinery's safe and reliable operation. These standards define acceptable levels of rotor unbalance for different applications, guiding manufacturers and operators. By adhering to these standards, businesses can guarantee that their equipment meets safety and performance requirements.
Different Methods for Balancing Rotors
Several methods are available for balancing rotors, each with its advantages and limitations:
- Static balancing: This method involves measuring and correcting static unbalance at low speeds. It is suitable for rigid rotors and is relatively simple to implement.
- Dynamic balancing: This method involves measuring and correcting all types of imbalances at operating speeds. It is essential for flexible rotors and those operating at high speeds.
- In-situ balancing: This method involves balancing rotors while they are installed in their operating environment, eliminating the need for removal and disassembly. It is particularly useful for large rotors or those in difficult-to-access locations.
- Modal balancing: This method involves analysing the natural vibration modes of the rotor to identify and correct imbalances. It is particularly effective for flexible rotors with complex vibration patterns.
- Influence coefficient balancing: This method involves calculating the influence of adding or removing mass at specific locations on the rotor’s vibration. It is a powerful technique for optimising balance solutions and minimising the number of balancing runs required.
- Automated balancing: This method utilises computer-controlled systems to automatically measure, analyse, and correct rotor unbalance. It provides consistent results and reduces the need for manual intervention.
In-situ Dynamic Balancing Solutions from Technomax
Technomax offers In-situ dynamic balancing solutions that can be customised to meet the specific needs of various industries on site. These solutions offer several advantages:
- High accuracy: Utilising advanced sensor technology and algorithms, Technomax’s systems achieve precise balance correction.
- Reduced downtime: Balancing rotors while they are installed minimises downtime and production losses.
- Improved safety: Eliminating the need for rotor removal and transportation reduces safety risks for personnel.
- Cost-effective: Technomax’s solutions are designed to provide long-term value and reduce maintenance costs.
By choosing the appropriate dynamic balancing services and partnering with skilled Engineering company in UAE Technomax, businesses can ensure their rotating machinery operates smoothly, efficiently, and safely, maximising productivity and minimising downtime. For more information about rotor balancing and how it can benefit your operations, contact Technomax today!
Learn More About Our Services
Recent Blogs
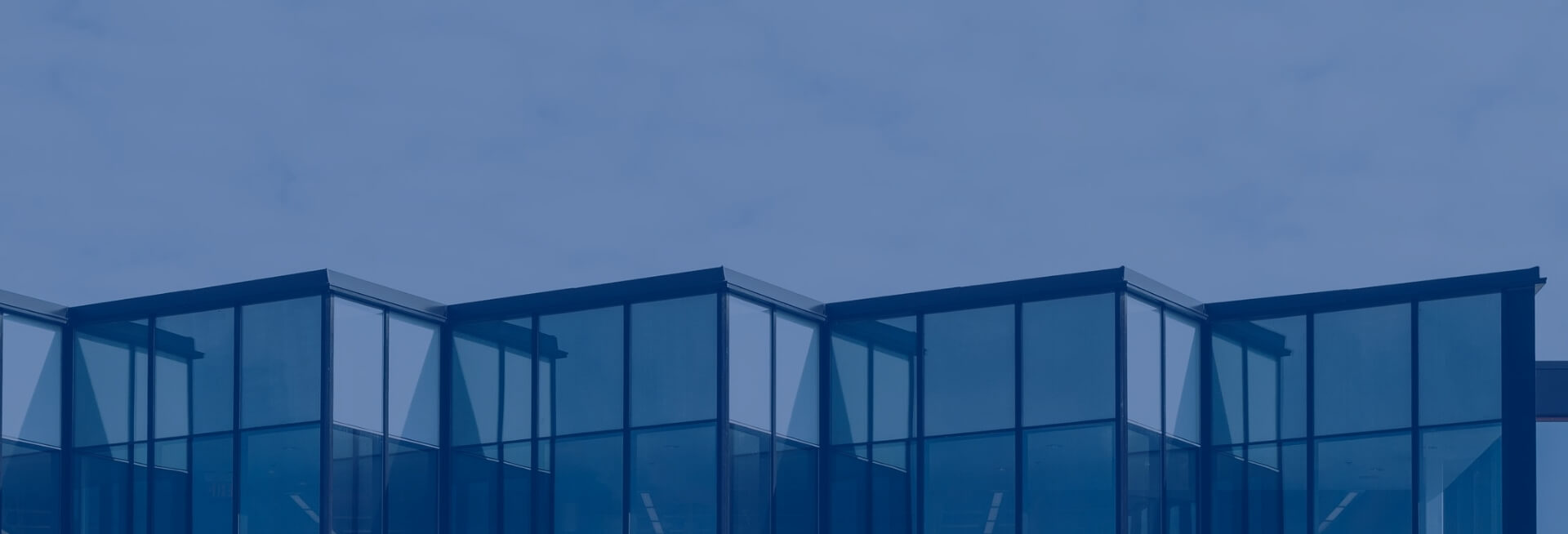
Get Started Now!
It takes less than a minute of your time. Or you may simply call +971 2 555 1 783