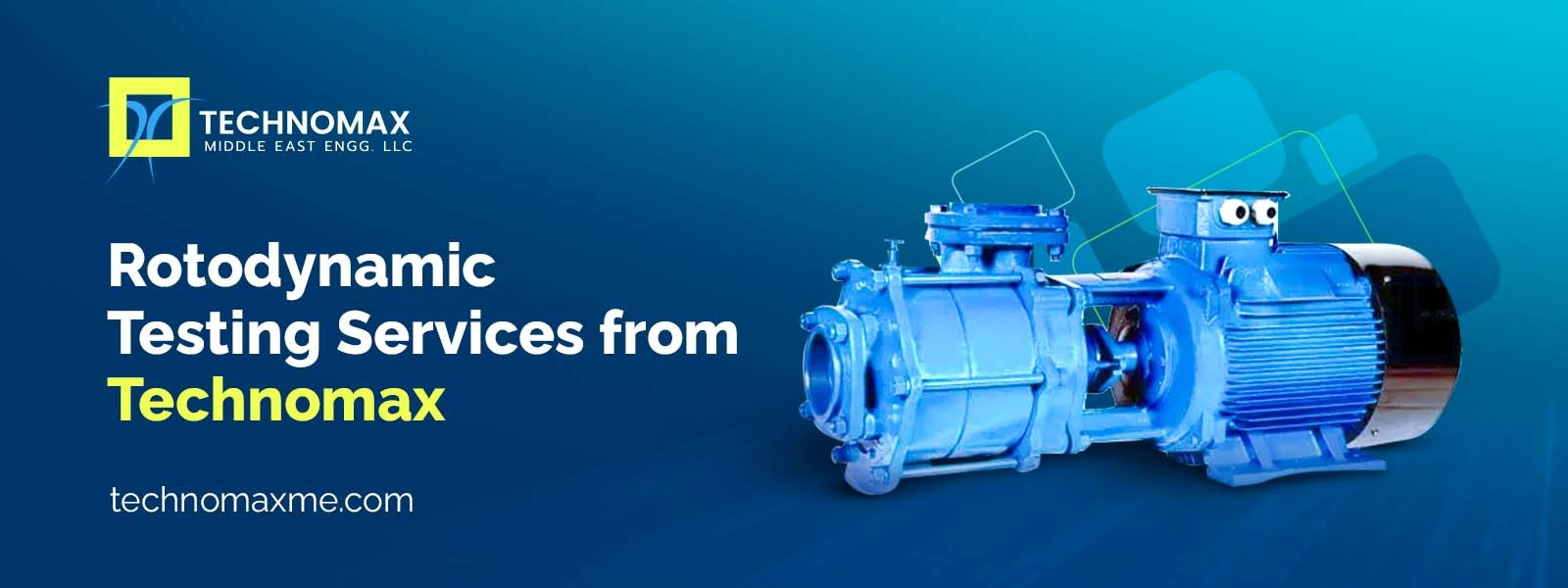
The Importance of Rotodynamic Testing Services
Rotodynamic testing is the method that lets engineers predict and eliminate the major operating concerns of the rotating equipment or machinery.
Rotodynamic testing experts evaluate and define a model that speaks of the survivability of rotating machinery concerning the factors like complex vibrations, instabilities, etc. for the actual operating loads.
With the evolving technology and rotodynamic testing services, Technomax has been able to help various industries quickly fix rotating structures and their concerned issues with ease.
Read further to know more about what the rotodynamic testing services from Technomax offer.
You may also like to read:
What Does Rotordynamics Mean?
Rotordynamics is a dedicated branch of applied mechanics that deals with the characteristics and diagnosis of rotating equipment.
This method is performed generally to investigate the behavior of structures— these could be steam turbines, jet engines, basic computer disk storage, or even auto engines.
Rotordynamics is formed with one or multiple mechanical structures (rotors) that support the bearing. These are influenced by the internal phenomena which rotate across a key axis.
The excitation of amplitude is caused due to the imbalance of rotating equipment, for instance, the engine balance or the tire balance.
Whenever the amplitude of vibration at these cautious speeds becomes high, it leads to catastrophic failures.
Nevertheless, turbo machinery also creates instabilities due to its internal structuring you need to correct. This is the major factor that engineers focus on while designing large rotors.
The Growing Importance of Rotodynamic Testing
Rotodynamic testing is performed to analyze the problems in a design well before commissioning the new machines.
It also engages in the evaluation of the effect of design changes on the equipment dynamics.
The method also works in conjunction with the vibration measurements to find the root cause of major vibration issues.
Why Is Rotor Imbalance a Concern You Should Immediately Address?
Rotor instability is a dangerous concern and the thoughtful prediction of rotor instability is a troublesome task, particularly due to the improved complexities of the system.
The analysis of this machinery lets engineers get deep insights into the sources of imbalance, and causes and thereby eliminate the instability, if any.
Preventing the unnecessary vibrations of the finished prototypes remains a complex and cumbersome task.
Severe shaft failure can rise under any of these conditions:
- Torsional or lateral critical seeds of the machinery align due to the potential excitation that the rotating equipment generates.
- A certain level of damping is present in the machinery
Apart from predicting the critical speeds or the natural frequencies of the shaft, the analysis can compute the stress and deflections through forced response evaluation.
This checks whether the equipment could bear the resultant deflections and stresses and if the damage fatigue will arise or not.
In such circumstances, the design changes will be considered to deflect the natural frequencies and critical speeds from the possible excitation frequencies. This is done with enough separation margin to prevent resonance while operating.
With rotodynamic testing in place, the engineers can quickly address rotor stability, imbalance problems, and issues found by vibration analysis throughout the design cycle.
How Does Rotodynamic Testing Work?
Rotating equipment is monitored with adherence to multiple requirements and standards.
The key objective of rotodynamic testing is to make sure that the equipment operates safely with early detection of any possible damages to the machine.
In addition to the equipment protection techniques, core efforts are expended on machinery diagnostics and technical measurements.
This starts with placing multiple sensors like acceleration sensors, vibration sensors, temperature sensors, etc., and ends with implementing special systems to conduct vibration diagnostic evaluation of rotors and turbine generators.
With these procedures in action, the deviations from the normal operations of the machine and the damage to components are detected prior, along with preventive maintenance techniques in place.
Having testing of rotor dynamics improves the operational availability of equipment while avoiding the failure of central and primary operating components.
By using the relevant measuring technology, production losses or shutdowns can be avoided particularly in the process and energy industries.
Types of Rotodynamic Evaluation Techniques
1. Finite Element Analysis
Finite element analysis involves using complex mathematical models, equations, and simulations to identify the way objects interact with physical forces. It helps engineers in analyzing the durability of the object and the way to optimize it. It has been built to analyze the mode frequencies and shapes of the rotating equipment. The technique has been also established to directly evaluate the modal parameters. The results from the technique for the frequencies and shapes or finally compared following a range of rotational speeds.
2. Computational Fluid Dynamics
Once the initial and detailed turbo machine design is finished, it is wise to evaluate the performance and the behaviour of flow with relevant models before manufacturing and testing techniques. Computational Fluid Dynamics (CFD) uses applied physics, mathematics, and advanced computational software to understand the flow of a gas or liquid and how it impacts the objects. Also, it measures the properties like velocity, viscosity, density, pressure, temperature, etc. based on the predefined operating conditions.
3. ODS & Modal Analysis
Structural dynamics is a structural analysis technique that helps to understand the behaviour of a physical structure while it undergoes dynamic loading. This involves Operating Deflection Shape (ODS) analysis and modal analysis. The technique portrays exact deflection patterns during specific operating conditions. And understands the dynamic properties of a structure that are inherent. The analysis can extract the critical dynamic characteristics of the structures which helps in the diagnosis of machinery by the dynamic structure behavior.
4. Mechanical Natural Frequency Testing
This kind of analysis evaluates the mechanical integrity of the rotating equipment. With mechanical natural frequency testing, you can determine the natural frequency response in both axial and radial directions for the equipment. It avoids the challenges of the conventional method where accidental slippage could occur that damages the rotating equipment, improves the safety of the operating workforce, and reduces the testing cycle time for the entire machinery.
Industrial Applications of Rotodynamic Testing Technique
Rotodynamic testing applies to every rotating equipment that caters to a plethora of industries. The most significant subjects include the medium to high-speed turbomachinery that fluid film bearings could support, where stability and speed would be a concern. However, the process might be advantageous for other kinds of machines kike draft fans specifically for power generation. Industries use rotodynamic testing to determine mode shapes, critical speeds, deflection shapes, and unbalanced responses of the rotating machinery. The analysis also eliminates:
- Resonance issues
- Sensitivity to unbalance
- Problems with stability
- Other rotating machinery troubles
The analysis is a crucial step in the designing procedure when you buy new rotating equipment. Various coupling, compressor, or bearing upgrade projects have got system dynamics impacted due to the design changes. In these cases, the analysis is considered the best solution to alleviate any possible concern about the rotating equipment.
Rotodynamic Testing Services from Technomax
Rotodynamic testing with Technomax gives you direct access to the services of certified engineers, analysts, and consultants who take you through the best process of rotodynamic testing. With experience in field balancing, vibration analysis, preventive maintenance, and other field measurements, Technomax provides a huge array of services to ensure the rotating equipment functions reliably with an in-depth analysis of the rotodynamic phenomena.
Learn More About Our Services
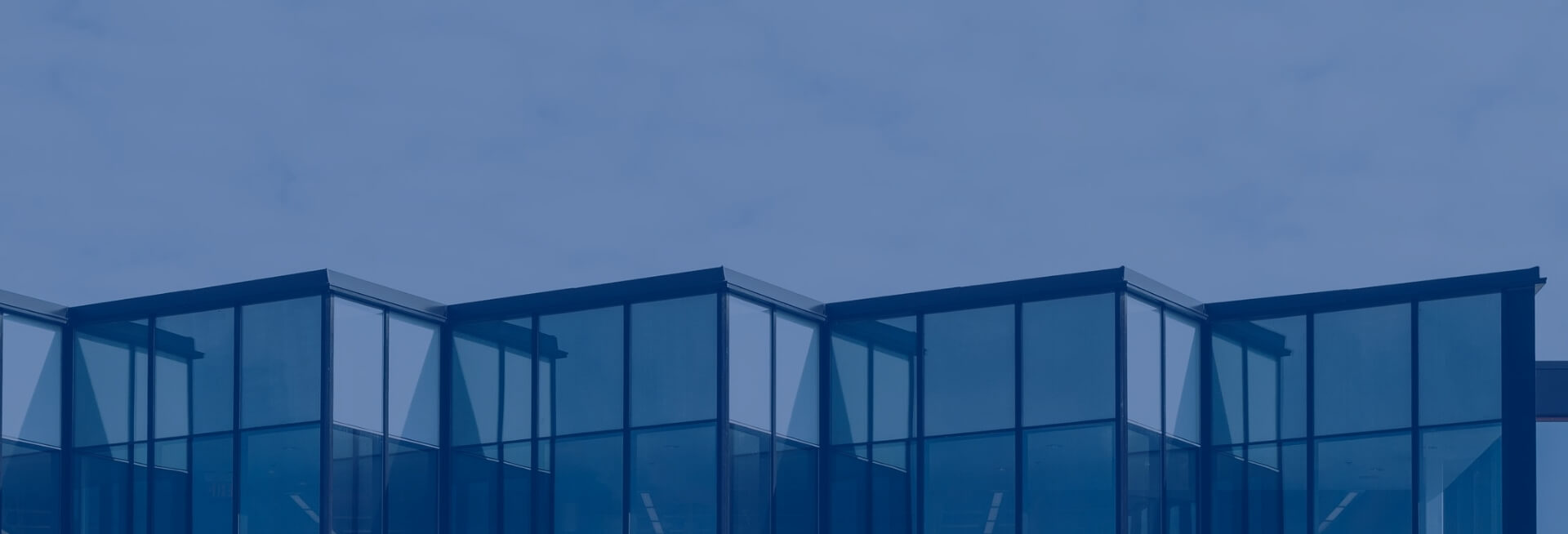
Get Started Now!
It takes less than a minute of your time. Or you may simply call +971 2 555 1 783