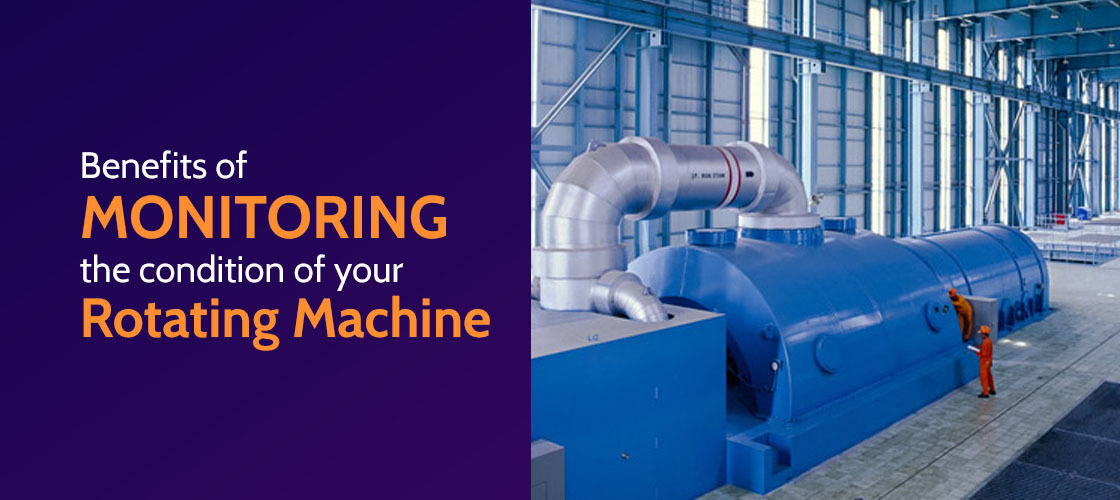
Condition Monitoring For Rotating Machine- Importance and Benefits
Condition Monitoring for rotating machinery
Asset Management should be a pertinent concern for businesses. Most plants and machinery cost almost a fortune! Hence, it arguably becomes a priority to maintain these machines, so as to ensure seamless functioning and uninterrupted production activities, leading to profits and sales. A phenomenon that helps businesses adhere to the precondition of maintaining such expensive assets is known as Condition Monitoring.
Condition Monitoring colloquially known as CM is the process of deciding upon a parameter of condition in machinery like vibration, temperature, etc. and thereby monitoring the same so as to identify a substantial change that is indicative of a developing pitfall in the machine.
It is a major component of the steps for the predictive maintenance plan. Conditional monitoring for rotating machines is, therefore, a maintenance strategy that allows monitoring the actual condition of an asset, extracting information to understand the machines' actual wear degradation, and if any change has occurred in its existing functioning.
It is advisable that maintenance needs to be done only when a consistent decrease in the equipment's performance is observed. The objective of this trajectory is to assess faults and inefficiencies in the machine, so as to avoid unplanned downtime or halt in the production process. Condition monitoring is an important part of any industrial maintenance strategy and can be used in an array of environmental conditions, namely oil and gas, transport, food and beverage, healthcare, local communities, water and wastewater, pulp and paper, etc.
Condition monitoring involves the analysis of asset metrics. The use of condition monitoring allows maintenance to be scheduled, or other actions to be taken to prevent consequential damages and avoid its consequences. Condition monitoring has a unique benefit wherein conditions that would shorten the normal lifespan of the machine and, therefore, this can be addressed before it develops a major failure. Condition monitoring techniques are normally used on rotating equipment.
Hence, condition monitoring is the mechanism of surveillance designed to recognize changes from a norm and warn when the changes exceed safe or limiting values. IT should be able to differentiate between good and bad conditions, and if bad it is, then how bad.
What is a Rotating Equipment?
Rotating equipment is an industry umbrella term, which is generally used in the oil and gas and process industries to describe mechanical components that use kinetic energy to move fluids, gases, and other process materials. These include, though not limited to, engines, compressors, turbines, pumps, generators, blowers, and gearboxes.
Importance of Condition Monitoring for Rotating Machinery
Rotating Equipment plays an important part in most operations. It is often managed separately from fixed equipment because it has a different design, maintenance, and inspiration requirement.
Rotating machine is generally a major safety concern because pump and compressor seals can leak. The material that leaks may explode, catch fire, or cause serious health problems. The following precautions to do with rotating equipment should be considered:
- A fire detection system should be installed for critical items or where the consequences of a leak could be serious. Consideration should also be given to the installation of a closed-circuit TV system.
- Critical rotating equipment should have a dedicated fire water supply. The closer firewater monitor will not only fight a fire but also provide cooling for equipment as it shuts down.
- It must be possible to shut down all rotating machines both remotely and with a manual switch at the location of them.
- It must also be possible to isolate both the suction and the discharge, even if the equipment item is leaking or if it is on fire.
- The lube oil and seal oil systems should also be protected, possibly with a manually activated water fog system.
Benefits of Condition Monitoring for rotating machinery
24X7 Remote Monitoring
Continuous Monitoring and maintenance are performed to understand the "health" or "condition" of the machinery so as to indicate that the maintenance is actually necessary because of the measurable degradation of one or more machine condition indicators such as increased vibration, noise, or temperature.
It is a way of keeping a close eye on the machine so as to receive real-time information about the functioning of the same. This, in turn, helps the managers to have extensive exposure to the machines beforehand so that they do not have to wait for any faulty indications to raise the alarm.
Cost-Effective
Recent advances in the field of sensing telecommunications, micro-electronics and Artificial Intelligence(AI) have enabled the development of a new breed of machine condition-based monitoring systems that, while not having the sophistication of SCADA systems, can enable businesses to achieve many of the benefits of transitioning from reactive and preventive maintenance to a CBM regime on a wide range of machines, without the high up-front cost of traditional CBM System.
Integration Possibility
The use of such technology can greatly facilitate the transition from traditional maintenance practices to condition Monitoring at its own pace.
With the latest advent of better versions of the software, the new Condition monitoring systems are being integrated with computerized maintenance management systems (CMMS), further simplifying the process of transitioning from traditional to condition-based maintenance regimes.
Minimized Unplanned Downtime
All process industries seek to minimize their unplanned downtime, not only because of the high direct cost of these events but because of the disruption that can be caused up and down the production chain, compounding the business impact. This new breed of the condition-based monitoring system can, in many cases, detect changes in the health of machines well before failure, providing maintenance staff with a substantial time window in which to schedule an inspection or a planned outage to investigate and if necessary rectify the problem.
This, in turn, reduces any associated disruption of the whole production chain, with significant consequential cost savings.
Read more about - Laser Shaft Alignment
Maximizing Production Output
Faulty machinery and broken components cost a great deal of money to most manufacturers across the world. Not only does this dig into your potential profit margin, but it can also have adverse effects on delivery schedules and agreements with the clients. With condition monitoring for rotating machinery, you can be sure to maximize your production output and meet your deadlines.
Increasing Lifespan of Machinery
Good machinery and high-quality parts are made to last, and condition monitoring can help to extend the lifespan of components and the longevity of the machine. It can be cost-effective, as well. Studies have shown that fixing those faulty parts of a rotating machine can save up to 40% of the maintenance cost as well as boost performance levels overall. This illustrates that condition monitoring cannot only eliminate hidden costs but can actually boost productivity overall.
Accurate KPI’s and Analysis
With condition monitoring, you have access to a constantly updating pool of data on your machinery. This information can prove invaluable when formulating and analyzing KPIs and measuring your manufacturing and output success. This, in turn, can allow you to make informed decisions when purchasing new equipment and extending contracts with suppliers.
Lowering Maintenance Cost
Condition monitoring is most beneficial for lowering maintenance costs. Although adopting a "Fix as it breaks" approach can initially lower costs, it is always more expensive in the long run. Furthermore, broken machinery can lead to a "ripple effect," where other equipment down the production line also malfunctions causing further damage.
These faults are virtually impossible to trace without the use of predictive maintenance techniques, and as such, condition monitoring is a worthwhile investment for any manufacturing company that values reliability.
Learn More About Our Services
Recent Blogs
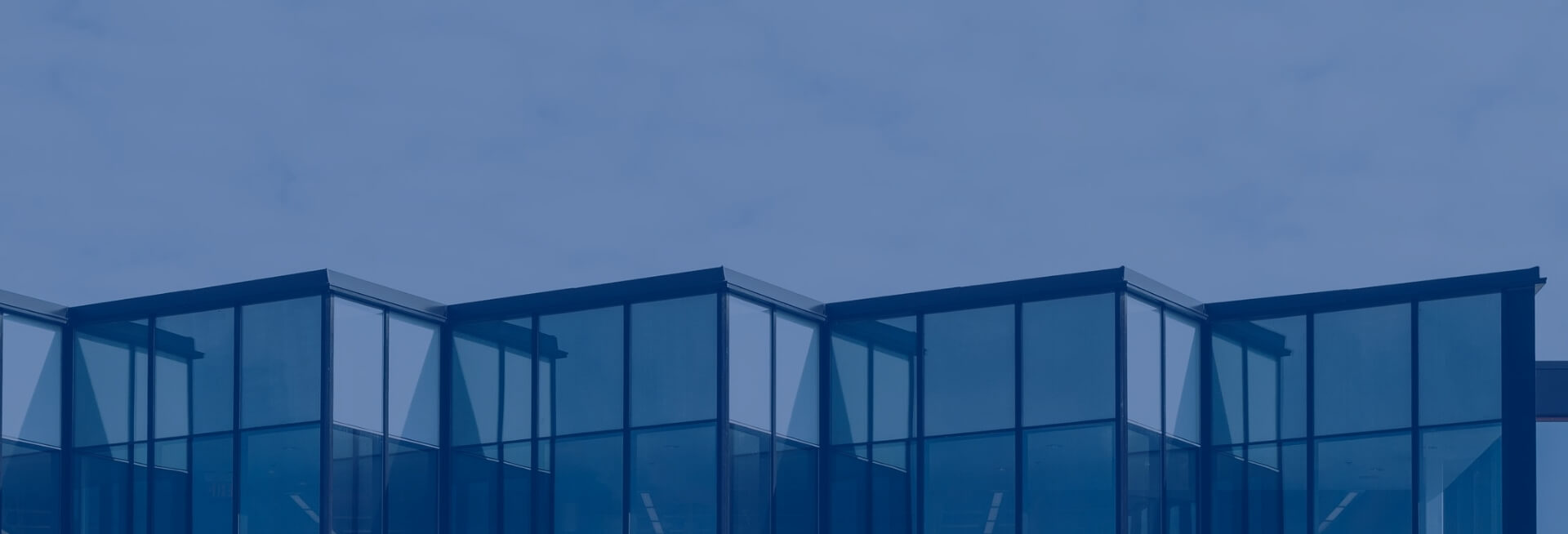
Get Started Now!
It takes less than a minute of your time. Or you may simply call +971 2 555 1 783