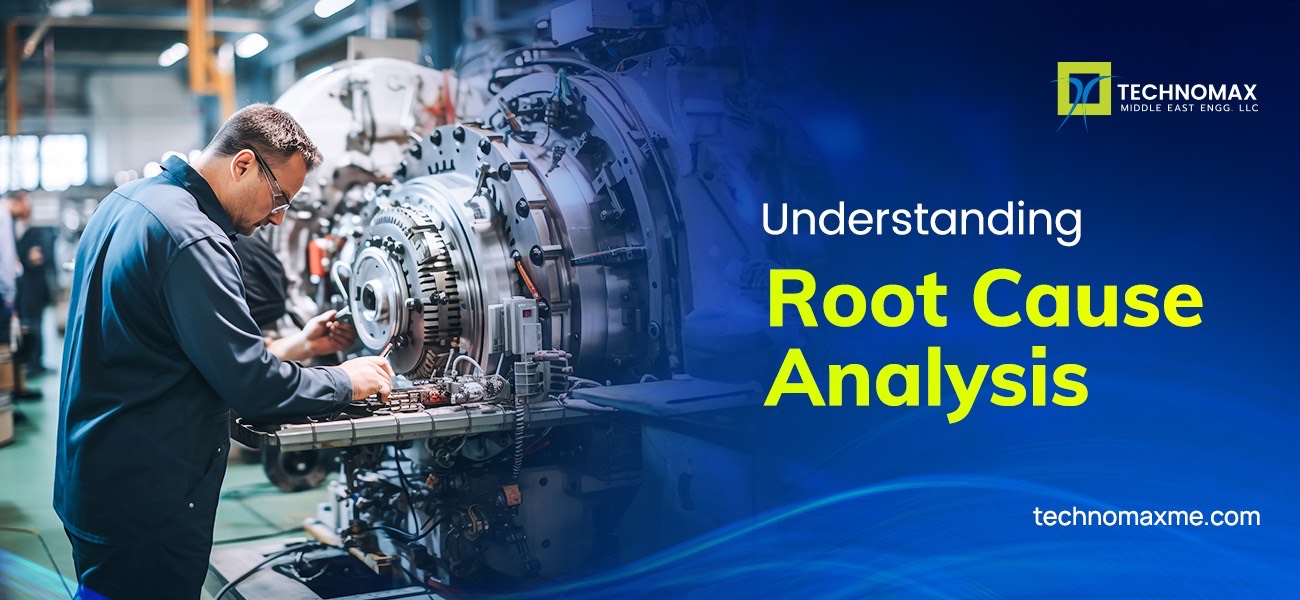
Understanding Root Cause Analysis
Root cause analysis (RCA) is a meticulous problem-solving approach utilised across a wide range of industries to identify and address the fundamental causes of issues rather than just managing their superficial signs and symptoms. This method is indispensable in understanding the root issues that lead to failures, ultimately preventing their recurrence.
This blog post aims to provide a comprehensive understanding of Root Cause Analysis (RCA), guiding you through its principles, execution, and different approaches of RCA with a particular focus on its application in equipment health management and incorporating elements of predictive maintenance.
What Is Root Cause Analysis?
Root cause analysis (RCA) is a systematic investigative method used across various disciplines, including business operations, engineering projects, and healthcare processes. It goes deeper than simply addressing the surface-level symptoms of a problem and helps businesses prevent issues from recurring by tackling the root cause. The RCA process for equipment health primarily involves the following steps:
- Detailed Problem Examination: The RCA process begins with a careful examination involving data collection from diverse sources like witness accounts, performance metrics, and physical evidence. This data may include sensor readings, maintenance logs, operator observations, and physical inspection of the equipment.
- Identifying Potential Causes: Once the equipment malfunction is clearly defined, RCA focuses on looking into all the factors that might contribute to the failure. Techniques like cause and effect diagrams (fishbone diagrams) or brainstorming sessions with maintenance personnel and engineers are used for this purpose. It is crucial to maintain a diverse perspective during brainstorming to avoid confirmation bias.
- Data Analysis and Root Cause Pinpointing: Data gathered during the examination phase is then analysed to evaluate the likelihood of each possible cause. Statistical tools and logical reasoning are applied to pinpoint the most likely root cause, whether it be a singular factor or a combination of factors that initiated the chain of events leading to the observed equipment failure.
- Predictive Maintenance Integration: Integrating predictive maintenance strategies with RCA can be highly effective. By identifying recurring root causes of equipment failures, maintenance schedules, and procedures can be tailored to address these issues proactively. Sensor-based monitoring systems can be used to detect potential failures early and aid in scheduling preventive maintenance interventions before problems occur.
Focusing on underlying causes through RCA, allows organisations to implement effective solutions that significantly improve equipment reliability, performance, and overall operational efficiency over time.
Tracing the Development of Root Cause Analysis
RCA (Root Cause Analysis) has its roots in Total Quality Management (TQM), a comprehensive framework for continuous improvement, optimising machine health, and customer satisfaction. One of the most important aspects of TQM principles is identifying the areas for improvement and ongoing monitoring of machine performance. Over time, the ideas used in TQM changed and became more focused, turning into RCA which is all about finding ways to solve problems when equipment doesn’t work right.
Incorporating RCA into the fundamental maintenance strategies allows companies to shift from merely reacting to problems as they arise to proactively preventing issues before they occur. This proactive approach leads to numerous benefits: equipment operates more reliably, workplace safety is improved, and production efficiency is increased, resulting in a higher output of products.
Understanding the Benefits of Root Cause Analysis (RCA)
As the name implies, root cause analyses are designed to determine what caused a specific issue, comprehend its causative factors, and determine what corrective measures need to be taken to resolve the issue. Effective equipment management plans often include RCA as a key component, identifying and rectifying underlying issues that significantly impact equipment reliability and performance. But what are the benefits of RCA? Let’s have a look.
- Finding Long-Lasting Solutions: RCA is a method that helps organisations identify the true root cause of equipment failures, preventing them from happening again. By focusing on the underlying causes of issues, RCA ensures that solutions are effective and long-lasting, enhancing equipment efficiency and performance.
- Improved Decision-Making: RCA relies on a step-by-step process that leverages data to support informed decision-making. It helps organisations understand why equipment failures occur. By studying the underlying causes, maintenance personnel and engineers can identify trends and establish data-driven strategies for improvement, ultimately leading to better equipment management practices.
- Enhanced Operational Efficiency: RCA targets the main problems directly, leading to more permanent fixes for equipment failures. This results in less downtime, higher productivity, and smoother operations. By continuously addressing these fundamental issues, RCA helps streamline maintenance workflows and reduce the frequency of repetitive equipment problems.
- Predictive Maintenance Enablement: RCA findings can directly aid predictive maintenance strategies. By identifying the root causes of equipment failures, predictive maintenance schedules and procedures can be tailored to address these issues proactively. This can significantly reduce the risk of unexpected breakdowns and improve overall equipment uptime.
In short, Root Cause Analysis is essential for big improvements, smarter decisions, and better operations. Deeply looking into the core problems helps businesses become more reliable and efficient.
What are the Different Root Cause Analysis Methods?
There are several ways to conduct Root Cause Analysis, each suited to different types of problems:
Method | Description |
Events and Causal Factor Analysis (ECFA) | Ideal for investigating major incidents by mapping events and identifying direct causes and contributing factors. Provides a comprehensive view, ensuring all aspects of the problem are addressed. |
Change Analysis | Useful when new issues arise after changes in processes, products, or services. Helps pinpoint how these changes might have led to the problem. Particularly valuable during transformation periods or new implementations to mitigate unforeseen challenges. |
Barrier Analysis | Examines controls in a process to see how well they prevent or identify problems early on. Identifies vulnerabilities in existing controls to strengthen processes. Proactive in preventing problems before they occur. |
Management Oversight and Risk Tree (MORT) Analysis | Useful for complex problems with many contributing factors. Breaks down and visualises elements for systematic problem-solving. Beneficial for untangling intricate issues with multiple root causes. |
Kepner-Tregoe Problem Solving and Decision-Making | Guides users through defining, analysing, and finding solutions to problems while preparing for potential issues with those solutions. Offers a structured approach to problem-solving, ensuring a thorough examination of the problem and its potential solutions. |
These methods provide a toolbox for tackling diverse challenges, offering flexibility and effectiveness in achieving lasting organisational improvements.
Principles of Root Cause Analysis
An effective root cause analysis involves digging deeper to solve problems. The process of deep exploration, relying on evidence, and commitment to improving processes over time leads to long-lasting solutions rather than temporary quick fixes. In addition to solving current operational issues, RCA principles also enable businesses to increase their resilience and efficiency by preparing them for future problems.
What Is the Core of the Root Cause Analysis?
Understanding and effectively applying the core principles of Root Cause Analysis (RCA) is essential for identifying the true origins of problems and implementing sustainable solutions:
- Prioritise Root Cause Over Symptoms: RCA focuses on identifying the root cause of an issue rather than merely addressing its symptoms. For instance, although increasing production speed might seem like a temporary solution to delays, RCA goes deeper to identify fundamental problems such as inefficient processes or outdated equipment. By concentrating on these core issues, lasting and effective improvements can be implemented.
- Employ A Structured and Disciplined Approach: Effective RCA involves a detailed and orderly investigation that uses proven techniques like the 5 Whys or Fishbone Diagrams. The ‘5 Whys’ technique involves asking the question ‘Why?’ multiple times until the fundamental cause of the issue is identified, promoting deep insight into causative factors. Concurrently, ‘Fishbone Diagrams’— also known as Cause-and-Effect Diagrams—provide a visual framework for categorizing potential causes of problems to identify root causes systematically. This structured approach ensures a comprehensive study through consistent data gathering, thorough analysis, and detailed record-keeping to uncover root causes completely. Using analytical tools and software supports this structured process, which in turn enhances the level of detail and accuracy of the investigation.
- Foster A Culture of Continuous Improvement: When RCA is integrated into a business’s culture, it accomplishes more. It becomes not just a problem-solving tool but a key part of everyday operations, promoting an ethos of continual progress. This mentality encourages regular evaluation and refinement of processes, making the shift from responding to issues to preventing them. This not only resolves current difficulties more effectively but also sets a solid base for facing future challenges.
Adhering to these core principles, RCA shifts from being a reactive tactic to a proactive strategy, granting organisations stronger problem-solving skills. This approach doesn’t just confront immediate problems but also builds the organisation’s capacity to adapt and thrive in the long run, leading to sustainable achievement.
What Are the Different Steps in Conducting Root Cause Analysis?
Root Cause Analysis (RCA) is a structured method for pinpointing the fundamental causes of issues to prevent recurrence:
Step 1: Define the Problem:
Start by providing a precise description of the problem, noting its occurrence, scope, and impact. This includes noting when the issue occurred, the extent of the malfunction (e.g., complete breakdown, performance decline), and its impact on operations (e.g., production downtime, safety hazards). Differentiate between the symptoms and the underlying issues.
It’s important to differentiate between the symptoms of the problem and the underlying root cause. Symptoms are the outward signs of malfunction (e.g., increased vibration, abnormal readings), while the root cause is the fundamental reason behind the symptoms (e.g., worn bearings, misalignment).
Step 2: Collect Data:
Gather all relevant data, which may include documents, reports, surveys, and interviews with affected parties. Other data sources may include sensor readings, maintenance logs, operator observations, and physical inspection reports.
Use data analysis tools to spot trends and patterns in the collected data. This can help establish potential correlations between operational parameters and equipment malfunction.
Step 3: Identify Potential Causes:
Form hypotheses about possible root causes through team brainstorming sessions with maintenance personnel, engineers, and other relevant stakeholders and the use of cause-and-effect diagrams. Encourage a collaborative and open environment to explore all possibilities without assigning blame.
Step 4: Analyse and Prioritise Causes:
Further, investigate these causes using tools like the Five Whys and visualise connections with fishbone diagrams. By repeatedly asking “why” for each identified cause, you can progressively peel back the layers and reach the root cause. Rank root causes by their impact and the feasibility of solutions.
Step 5: Implement Solutions and Monitor:
Create and implement action plans targeting each root cause. The plan should outline specific actions, timelines, and resource allocation for implementing the solution. Keep stakeholders updated, implement the solutions, and monitor outcomes with a robust tracking system. Adjust strategies based on ongoing feedback.
Step 6: Documentation and Communication:
Record all findings and actions thoroughly throughout the RCA process. Maintain clear and open communication with all participants, ensuring transparency and collective engagement in solving the problem.
Following these steps in RCA helps resolve immediate problems, strengthens the business’s ability to manage future challenges, and prevents the recurrence of similar issues.
5 Root Cause Analysis Techniques
Depending on the situation, different root cause analysis tools or approaches can be used, each offering unique insights into the problem-solving process. The following are the five main RCA approaches to identifying problems:
- Fishbone diagrams, or Ishikawa diagrams, provide a visual representation for organising potential causes of a problem. Resembling a fish skeleton, the main issue is represented at the head, while branches of the main “bone” represent different categories of root causes. This method is beneficial for team-based brainstorming and is especially helpful in complex sectors such as manufacturing or healthcare.
- Failure Mode and Effects Analysis (FMEA) is another strategic approach designed to preemptively identify ways in which a product, service, or process might fail. By categorising potential failures and evaluating the severity and likelihood of each, teams can implement preventive strategies more effectively. This approach is especially vital in industries where safety is paramount, such as the automotive and aerospace sectors, by helping to mitigate risks before they materialise.
- Fault Tree Analysis (FTA) approaches problem-solving from the endpoint of a failure, working backward to trace its root causes. Using logical diagrams, FTA systematically breaks down each contributing element of the failure, defining primary and secondary causes, which are crucial for ensuring operational safety in high-stakes environments like nuclear energy production and aviation.
- Pareto Charts are utilised to prioritise problems or defects in processes, based on the frequency of their occurrence. Grounded in the Pareto Principle, which suggests that 80% of problems (or significant areas of concern) are typically caused by 20% of the causes, these charts help businesses focus on the changes that will have the biggest impact on improvement efforts. Such data-driven decision-making is invaluable in scenarios where resource allocation must be optimised for maximum effect.
- Is/Is Not Analysis is particularly useful when facing complex or poorly defined problems. By delineating what a problem is and is not, this method helps narrow the focus of investigation, removing ambiguity and ensuring that analysis efforts are correctly directed.
How Technomax’s RCA Approach Empowers Your Business
Technomax’s Root Cause Analysis (RCA) approach is exclusively tailored to optimise equipment performance across multiple sectors. Being the leading engineering company in the UAE, Technomax offers customised solutions, including condition monitoring services that cater to the unique technical requirements of each client’s machinery, ensuring peak performance. With a wealth of expertise in various industries, Technomax delivers targeted advice and strategies that pinpoint and resolve the specific operational challenges of your equipment.
More than just addressing immediate malfunctions, Technomax’s RCA strategy is designed to achieve constant improvements in equipment reliability and maintenance. This method not only solves current problems but also enhances the capability of the equipment to avert future issues, thereby sustaining long-term reliability and readiness against unexpected failures.
Technomax partners with clients to provide customised equipment solutions that address immediate equipment issues as well as establish a strategic approach for continuous performance enhancement. With this partnership, equipment management is improved and competitive advantages are gained.
For more details on how Technomax’s RCA can transform your equipment management for better, long-term outcomes, contact us today.
Learn More About Our Services
Recent Blogs
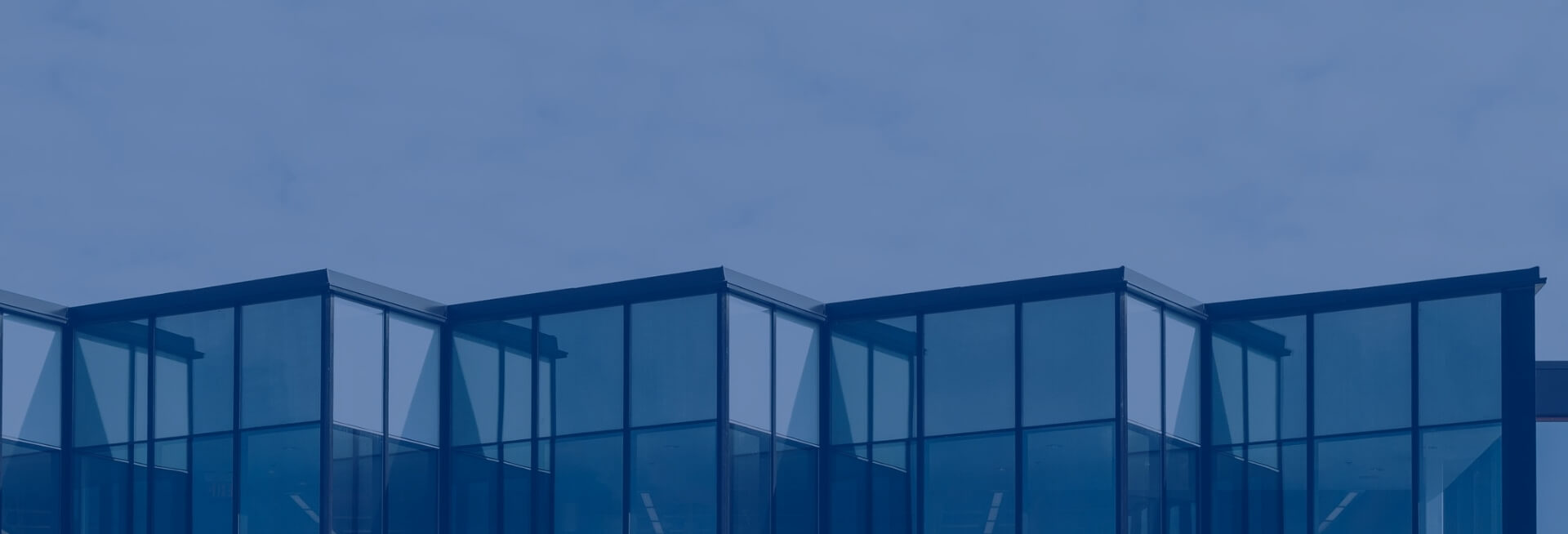
Get Started Now!
It takes less than a minute of your time. Or you may simply call +971 2 555 1 783