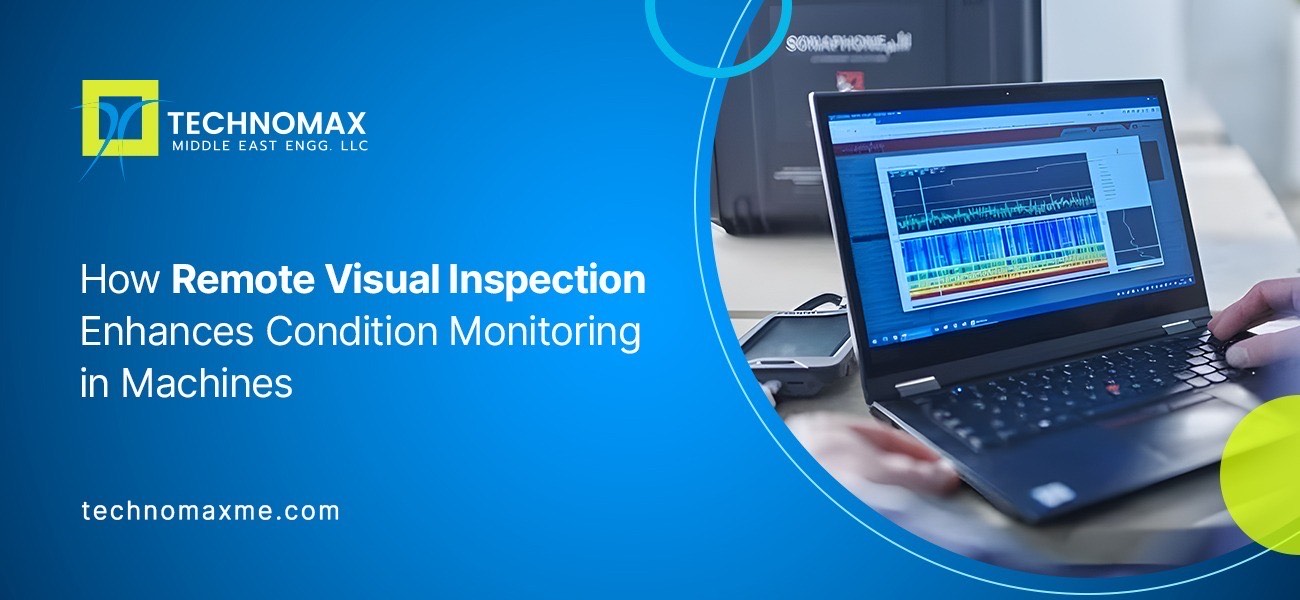
How Remote Visual Inspection (RVI) Enhances Condition Monitoring in Machines
- condition monitoring services
- Infrared Thermography in Condition Monitoring
- Partial Discharge
- vibration analysis
Remote Visual Inspection (RVI) of equipment and machinery is an integral aspect of maintenance across industries. It can be the primary determinant of a machine’s performance, besides being a crucial factor in averting operational downtime. With the latest technological advances, these inspections are now more effective than ever.
One example of such a breakthrough is Remote Visual Inspection (RVI), which is changing many different industries today. Read on to explore how RVI is improving the efficiency of manufacturing and energy production operations.
What Is Visual Inspection?
Visual inspection meaning, in simple words, is the act of using one’s eyesight to examine an object for any deviations from the expected or normal condition. This involves examining systems, equipment, and structures for potential defects, discrepancies, or inconsistencies that could affect their safety or performance. It usually involves looking for visible signs of wear and tear, damage, or inconsistencies in appearance using simple tools like flashlights or magnifying glasses.
What Is the Goal of Visual Inspections?
Visual inspection, which is one of the most reliable approaches, includes assessing the current condition of an asset as part of the overall maintenance process. The main goal of visual inspections is to identify potential issues and resolve them before they turn into significant problems.
Early detection of potential faults allows industries to handle matters proactively. This enhances safety, preserves system integrity, and avoids expensive operational disruptions. The goals of visual inspection techniques are:
- Condition Assessment: Conducts a thorough examination of an item’s overall operational efficiency, such as measuring machine wear or inspecting the exterior of a building.
- Regulatory Adherence: Ensures that objects or systems align with pertinent rules and standards, including safety protocols and fire codes.
- Quality Advancement: Boosts the quality of equipment by identifying flaws and ensuring compliance with standards, thereby facilitating enhanced performance.
- Safety Augmentation: Improves safety measures by identifying and correcting potential hazards, such as repairing cracks, inspecting electrical wires, or replacing damaged machine parts.
- Cost Optimisation: Enables financial savings by anticipating potential issues and preventing them from escalating into serious and costly problems.
Visual Inspection (VI) Techniques
Visual inspection offers two techniques:
- Remote Visual Inspection (RVI)
Through RVI, professionals have the means to conduct remote equipment inspections effortlessly while maintaining a strong focus on employee safety. The process involves employing technological solutions to examine equipment from afar.
- Automated Visual Inspection (AVI)
AVI relies on computerised systems to spot defects that may be overlooked by the human eye, thereby enhancing defect detection accuracy. This technique utilises machine vision systems to detect discrepancies that could potentially escape detection.
Common Methods of Remote Visual Inspection (RVI)
RVI methods can be customised to suit industry-specific needs and requirements for inspection. Below are some RVI methods that can assist in improving equipment inspection and performance:
-
Eddy Current Testing (ECT)
The non-destructive testing technique of Electromagnetic Conductivity Testing (ECT) uses electromagnetic induction to inspect surfaces, focusing on conductive materials such as metals. Its main function is to reveal internal defects, corrosion, alterations in material properties, and more. This is particularly beneficial in sectors like aerospace, power generation, and oil and gas where precise control of material properties is critical. The advantages offered by Eddy Current Testing are numerous, including:
- Fast, sensitive, and accurate.
- Can inspect complex surfaces and distinguish between different conductive materials.
- Doesn't require direct contact, protecting materials from potential damage.
- Provides immediate information and responses.
2. Ultrasonic Testing (UT)
Ultrasonic Testing (UT) employs high-frequency sound waves to perform inspections on a range of materials. With its roots deeply embedded in industries such as manufacturing, construction, and aviation, UT is extensively used for detecting internal defects, attesting to corrosion, and identifying disintegration. Some of its most beneficial features are:
- Can discover small internal defects and discontinuities.
- Accurately measures the depth and size of a flaw.
- Safe for both the material and the operator.
- Allows for real-time inspection and data collection.
3. Acoustic Emission Testing (AE)
Acoustic Emission Testing (AE) operates by monitoring the stress waves caused by the deformation and cracking of materials. The technique is instrumental in inspecting substantial structures such as buildings or pressure vessels and is adept at identifying dynamic processes like crack growth, corrosion, and leaks. The key features of AE include:
- Provides constant monitoring of structures, allowing early fault detection.
- Can inspect large, complex structures with few sensors.
- Doesn't interfere with normal operations.
- Provides real-time information, aiding maintenance planning.
4. Leak Testing (LT)
Engineered to detect leaks in sealed systems or containers, Leak Detection Testing (LT) has wide-ranging applications in industries, including automotive, aerospace, and pharmaceuticals. It’s pivotal in affirming component integrity, delivering assured product quality, and averting safety risks. LT’s benefits include:
- Can accurately detect the location and rate of leaks.
- Ensures the safety and quality of the tested materials or devices.
- Can detect both internal and external leaks.
- Non-destructive method, ensuring no harm to the material.
5. Visual Testing (VT)
Visual Testing (VT), which is a technique that uses an approach that focuses on inspecting the appearance of an object, is an important technique for identifying surface defects. VT is widely recognised for its wide range of benefits in industries such as construction, manufacturing, and aerospace, including the following:
- Simple, affordable, and requires minimal equipment.
- Quickly identifies visual faults.
- Provides immediate results, allowing for immediate action.
- Gives a complete assessment of the material’s condition.
6. Radiographic Testing (RT)
Radiographic Testing (RT) leverages X-rays or gamma rays to conduct thorough inspections of materials' internal structures. This technique enjoys high importance within the oil and gas sector, nuclear power industry, aerospace, and fabrication sectors, delivering various benefits:
- Can uncover internal and hidden defects that other methods may miss.
- Provides a permanent record in the form of a radiograph.
- Can inspect a variety of materials and thicknesses.
- Allows for quantitative evaluation of defects.
7. Magnetic Particle Testing (MT)
Magnetic Particle Testing (MT) is a specialised method that identifies surface and near-surface defects in ferromagnetic materials. The technique finds popularity in the automotive, oil and gas, and power generation sectors. Key advantages of MT include:
- Highly sensitive to surface and near-surface defects.
- Provides immediate results for instant assessments.
- Can be applied to various sizes and shapes.
- Straightforward and cost-effective method.
8. Dye Penetrant Testing (PT)
PT, also known as Liquid Penetrant Inspection (LPI), is Dye Penetrant Testing (PT) that aims to reveal surface-breaking flaws, delivering valuable insights. Its applications spread across various sectors such as automotive, aviation, oil and gas, and nuclear power. The major benefits of PT include:
- Excellent at finding small, surface-breaking defects.
- Flexible — can be used on various materials and applied to complex shapes.
- Simple to apply and relatively affordable.
- Results are accessible directly on the surface, making defects easier to spot.
It’s crucial to select the right strategy that aligns with the specific materials and requirements slated for inspection to achieve optimal results in defect detection and maintenance planning.
Remote Visual Inspection (RVI) Procedure
While implementing a remote visual inspection, a systematic approach is necessary to ensure efficient data collection, analysis, and diagnosis. This process is typically a four-step operation:
- Decide on the right equipment required: Choose an appropriate RVI tool, such as a videoscope, drone, robot, or borescope, depending on what you want to inspect, where it’s located, and its current condition.
- Pre-inspection preparations: Set clear goals for your inspection. Ensure you are familiar with the machinery to be inspected. During this phase, outline what you expect from the inspection, understand the operational conditions, learn about common fault indicators, plan your schedule, and gather all necessary tools.
- Execution of the inspection: This is the key stage where you do the actual checking as per your plan.
- Data collection and analysis: At this stage, you’ll get hold of the data you need, record it, and work out if there are any issues.
This structured visual inspection procedure ensures an exhaustive operation that aids in judicious decision-making and maintenance planning.
Benefits and Importance of Remote Visual Inspection
The use of RVI carries significant advantages in the industrial sector, acting as a valuable tool for equipment maintenance and issue prevention. Its importance cannot be overstated as it enhances efficiency, prevents accidents, and ultimately contributes to an organisation’s bott
om line. The implementation of remote visual inspection offers numerous benefits to the industrial sector, such as:
- Enhancing safety: RVI allows inspections in hazardous or hard-to-reach areas without the necessity for an inspector to be physically present.
- Reducing downtime: By eliminating the need to disassemble equipment for examination, downtime is minimised.
- Increasing efficiency and accuracy in defect detection: This is achieved through the application of advanced inspection technology.
- Delivering real-time monitoring capabilities: Immediate reactions to identified issues are facilitated by prompt and continuous monitoring.
- Minimising human intervention and associated risks: The application of RVI technology minimises the risk of human errors during inspections by significantly reducing human intervention.
- Ensuring compliance with regulations: Regular inspections, made more accurate and thorough with RVS technology, ensure compliance with various industry standards and regulations.
- Promoting cost-effectiveness: The ability to detect defects and potential issues early through RVI reduces the need for more extensive (and often costly) repairs or replacements later. This process significantly cuts overall maintenance costs, contributing to your organisation’s financial performance.
- Ensuring accessibility to hard-to-reach areas: With the help of RVI technology, inspectors can seamlessly access and examine areas that are physically challenging to reach.
By making general remote visual inspection a part of regular maintenance, we can improve machine performance, ensure employee safety, and lower operating costs. RVI is a progressive technology that aids industries in their development and adjustment to ever-changing operational needs.
How does CMMS help with Remote Visual Inspections?
A Computerised Maintenance Management System (CMMS) is a type of software designed to help businesses manage their maintenance tasks in a structured way. This includes evaluating both preventive and corrective maintenance.
By integrating with Remote Visual Inspection (RVI) technology, a CMMS can significantly improve operational efficiency, increase the lifespan of equipment, and enhance data accuracy. This approach standardises maintenance procedures and strengthens quality assurance processes, resulting in better organisational outcomes.
Remote Visual Inspection Services from Technomax
At Technomax, we provide industry-leading Remote Visual Inspection (RVI) solutions, leveraging advanced CMMS software from top-notch leaders like IPEC, SONOTEC, and FLUKE, aiming to boost efficiency with our unmatched data processing and management capabilities.
IPEC, specialists in On-Line Partial Discharge (PD) testing, provides turnkey solutions for asset monitoring and testing. Their CMMS software offers regular checks and comprehensive status updates on your assets and serves a variety of sectors.
SONOTEC, a leading provider of ultrasonic measurement technology solutions, prevents system leaks in areas such as air compressors, gas, and vacuums. Their meticulous analysis and modern features make it ideal for digital industries.
FLUKE Connect Condition Monitoring software, another significant vibration monitoring solution, ensures your machines are running efficiently through constant checks on crucial parameters like vibration. This aids in optimising operations, reducing costs, and improving safety. It allows teams to view asset trends on graphs from interconnected condition monitoring devices.
By incorporating RVI into regular maintenance routines, we can enhance machine performance, guarantee employee safety, and lower operational costs. Contact Technomax to learn more about remote visual inspection and how our other condition monitoring services can benefit your business.
Learn More About Our Services
Recent Blogs
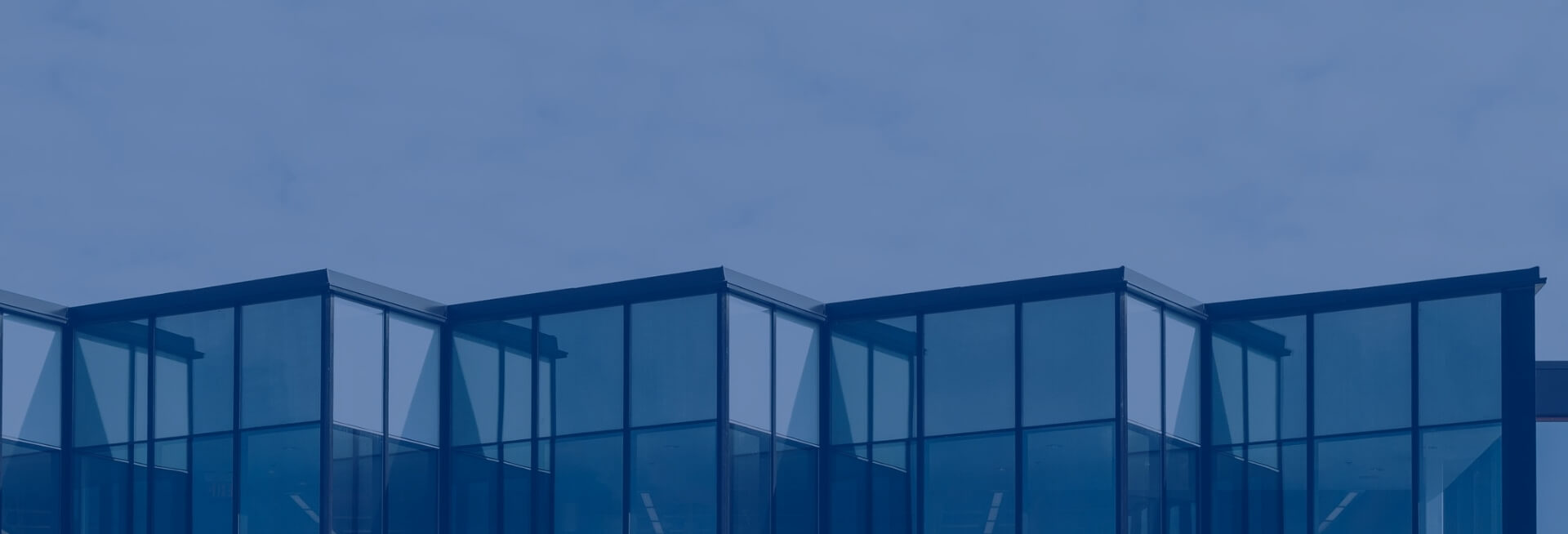
Get Started Now!
It takes less than a minute of your time. Or you may simply call +971 2 555 1 783