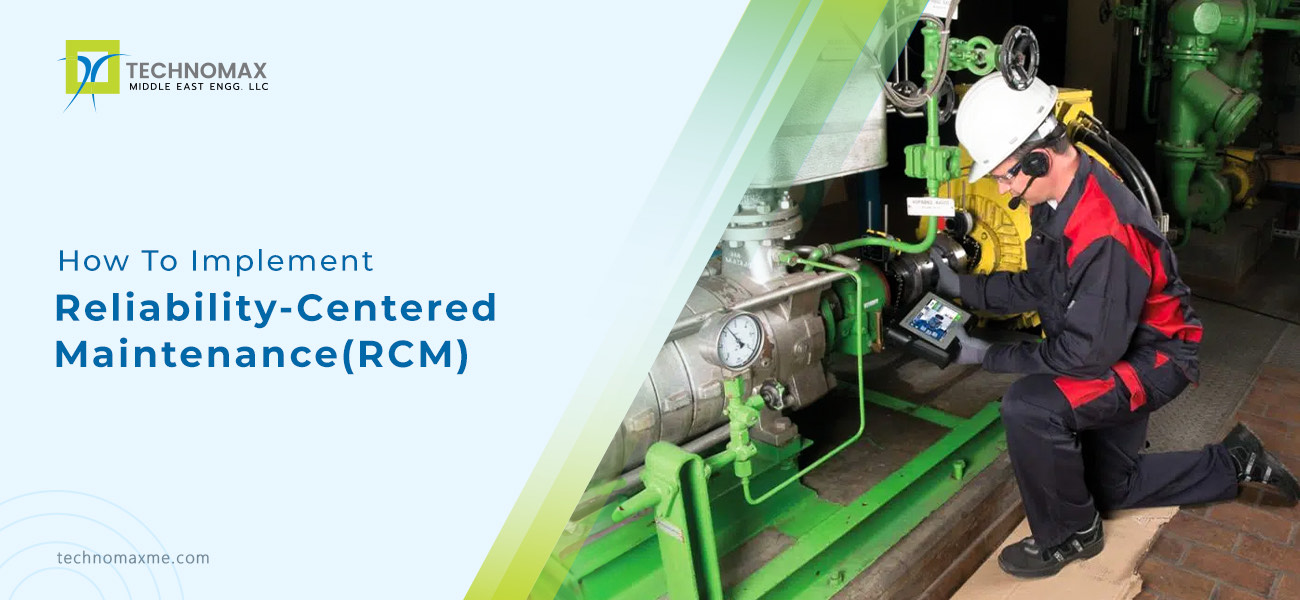
Reliability-Centered Maintenance (RCM): A Complete Guide
Reliability Centered Maintenance (RCM) is a proactive and structured methodology prioritising critical assets and their possible failure modes. It allows businesses to develop customised maintenance plans that ensure smooth and efficient equipment operation. Originally developed in the 1960s for the aviation industry, RCM has become widely adopted across various sectors, including manufacturing, energy, and transportation.
Every business today constantly seeks innovative solutions to maximise equipment performance. Unplanned downtime disrupts production schedules, incurs considerable costs, and compromises safety. This is where Reliability-Centered Maintenance (RCM) comes in.
In this quick blog, we will delve into the complexities of RCM, outlining the core principles, implementation steps, and real advantages it offers for businesses looking to maximise asset performance. We’ll also explore how cutting-edge solutions can further improve the RCM process, ensuring a more reliable and cost-effective approach to maintenance.
What Is Reliability-Centered Maintenance (RCM)?
RCM, at its core, is a systematic methodology that transcends traditional, reactive improvement practices. In contrast to the dependence on fixed schedules or reacting only when equipment failure occurs, RCM adopts a proactive and data-driven approach. By prioritising critical assets, identifying potential failure modes, and selecting appropriate enhancement tasks, RCM delivers manifold benefits for businesses across diverse industries. In the following sections, we will look into the advantages of RCM, detail its implementation process, and elucidate how breakthrough technologies can boost its efficacy.
Implementing RCM: A Systematic Approach to Enhanced Asset Performance
Reliability-Centered Maintenance (RCM) has become a powerful tool across various industries, including manufacturing, transportation, oil and gas, utilities, and construction. It enables businesses to improve operational reliability and safety, reduce costs, and extend asset lifespan. However, successful RCM implementation demands a systematic approach that comprises the following key steps:
- Identifying Critical Assets: The initial stage focuses on pinpointing the assets most crucial for maintaining operational continuity. This process involves a multi-pronged approach, combining reliability analysis techniques, historical performance data from the assets themselves, and valuable expert insights from within the business. Here, it’s critical to consider the potential impact of an asset failure on various aspects, including production levels, safety risks, and environmental factors.
- Defining Functions and Failure Modes: Once critical assets are identified, a thorough analysis of their functionalities and potential failure modes becomes essential. Techniques such as Failure Modes and Effects Analysis (FMEA) come into play at this stage. FMEA facilitates a detailed examination of how each critical asset might fail and the potential consequences of such failures. For example, consider a critical pump in a manufacturing plant. An FMEA analysis for this pump might identify potential failure modes such as bearing wear, seal degradation, or motor overheating.
- Assessing Failure Consequences: The next step involves meticulously evaluating the potential consequences associated with each identified failure mode. This analysis should consider safety hazards that could arise due to the failure, potential disruptions to production schedules, environmental impact, and any non-compliance issues that might emerge. Risk matrices can be a valuable tool in quantifying these risks, ultimately facilitating the ranking of improvement tasks based on their potential severity. Continuing with the pump example, the FMEA analysis might reveal that a bearing failure could result in a complete production shutdown, posing a safety risk to personnel and potentially causing environmental damage due to a lubricant leak.
- Development of Enhancement Strategies: With a comprehensive understanding of both failure modes and their potential consequences, businesses can now develop customised enhancement plans for their critical assets. These plans may encompass a combination of strategies: preventive maintenance practices conducted at predetermined intervals, condition-based maintenance triggered by real-time data collected from sensors, or even a hybrid approach using both techniques. Factors such as the asset’s lifespan, operating environment, and historical reliability data should be carefully considered when crafting these plans. For the critical pump, a combination of preventive maintenance tasks such as periodic lubrication and vibration analysis, alongside condition-based monitoring using vibration sensors to detect bearing wear or overheating, might be the most effective strategy.
- Monitoring and Feedback: Establishing a robust monitoring system is essential to track asset performance and assess the effectiveness of the implemented maintenance strategies. Integration of digital tools such as dashboards, sensors, Internet of Things (IoT) devices, and predictive analytics empowers businesses to adopt a proactive maintenance approach. This allows for identifying potential issues before they escalate into major problems. For instance, data collected from sensors on the pump can be analysed using predictive analytics software to anticipate potential bearing failures, allowing for improvement interventions to be scheduled before they occur.
By following this structured approach to RCM implementation, businesses can gain a significant advantage in terms of asset performance, operational efficiency, and overall business success.
Benefits of Reliability Centered Maintenance (RCM)?
The implementation of Reliability Centered Maintenance (RCM) offers a multitude of benefits for businesses:
- Enhanced Equipment Reliability: By proactively identifying and addressing potential failure threats, RCM ensures that assets operate smoothly for longer durations, reducing downtime and production disruptions. This leads to better output, improved quality of products, and more customer satisfaction.
- Cost Optimisation: RCM’s targeted approach eliminates unnecessary servicing activities for non-critical assets, leading to significant cost savings. Resources can then be strategically directed towards areas with a higher impact on operational efficiency. Reduced servicing costs, combined with minimised downtime and improved equipment lifespan, contribute to a healthier bottom line for the business.
- Improved Safety: RCM prioritises the proactive upkeep of safety-critical components, fostering a safer work environment and cutting down the risk of accidents. Early detection of potential equipment failures safeguards personnel and prevents equipment malfunctions that could lead to injuries or fatalities. This proactive approach fosters a culture of safety awareness within the business, promoting responsible upkeep practices and a commitment to employee well-being.
- Regulatory Compliance: RCM helps businesses comply with industry regulations and standards that govern safety practices and environmental protection. By proactively addressing potential hazards identified through FMEA and other analyses, businesses can minimise the risk of non-compliance issues, avoiding costly fines and reputational damage.
RCM fosters a proactive approach to regulatory compliance, ensuring that upkeep practices align with established standards and contribute to a sustainable operational environment.
Why Is RCM Beyond Implementation Turning into a Cycle of Continuous Improvement?
- Data-Driven Refinement: The implementation process of RCM is not a one-time event; it’s a cyclical approach that encourages ongoing monitoring and data collection. By analysing data on asset performance, servicing activities, and failure occurrences, businesses can refine their RCM strategies over time. New failure modes or consequences may be identified, prompting adjustments to servicing plans. This data-driven approach ensures that RCM strategies remain relevant and effective in a dynamic operational environment.
- Knowledge Sharing and Collaboration: Successful RCM implementation hinges on effective communication and collaboration among various stakeholders. Encouraging knowledge sharing between servicing personnel, engineers, and operational teams fosters a collective understanding of critical assets and potential failure scenarios. This collaborative approach ensures that RCM strategies are well-informed and effectively implemented across the business.
The Role of Advanced Technologies in RCM
Technomax, a leading engineering company in UAE and provider of asset management solutions, offers a suite of innovative tools that significantly enhance the RCM implementation process. These tools leverage advanced technologies to streamline servicing tasks, improve data collection, and facilitate real-time decision-making for servicing teams.
- Digital Dashboards: Technomax’s digital dashboards provide a centralised platform, visualising asset health, servicing schedules, and key performance indicators (KPIs) in real time. This centralised view empowers servicing teams to proactively identify potential issues, optimise resource allocation, and make data-driven decisions regarding servicing activities.
- Predictive Analytics: By leveraging advanced algorithms and historical data, Technomax’s predictive analytics tools can anticipate potential equipment failures before they occur. This enables businesses to schedule preventive servicing interventions proactively, minimising downtime and maximising asset uptime.
- IoT Sensors and Condition-Based Monitoring: Integrating IoT sensors within critical assets allows for continuous monitoring of operating parameters such as vibration, temperature, and pressure. This real-time data empowers businesses to adopt a condition-based servicing approach, focusing servicing activities on assets that require attention based on sensor readings rather than predetermined schedules.
Implementing Reliability-Centered Maintenance (RCM) can give businesses a significant advantage by improving asset performance, reducing servicing costs, and prioritizing operational safety. This proactive and data-driven approach provides several benefits, including better asset performance, reduced servicing costs, and improved operational safety. Get in touch with Technomax today to understand better how to implement RCM and begin your journey towards long-term success.
Learn More About Our Services
Recent Blogs
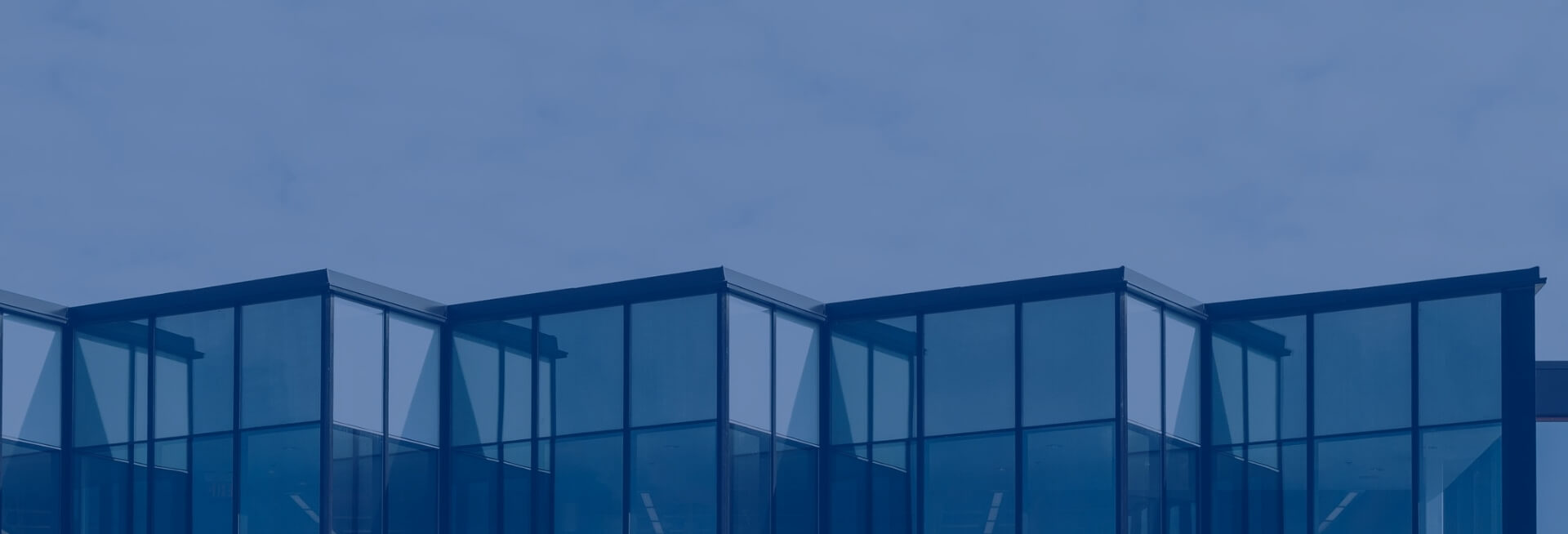
Get Started Now!
It takes less than a minute of your time. Or you may simply call +971 2 555 1 783