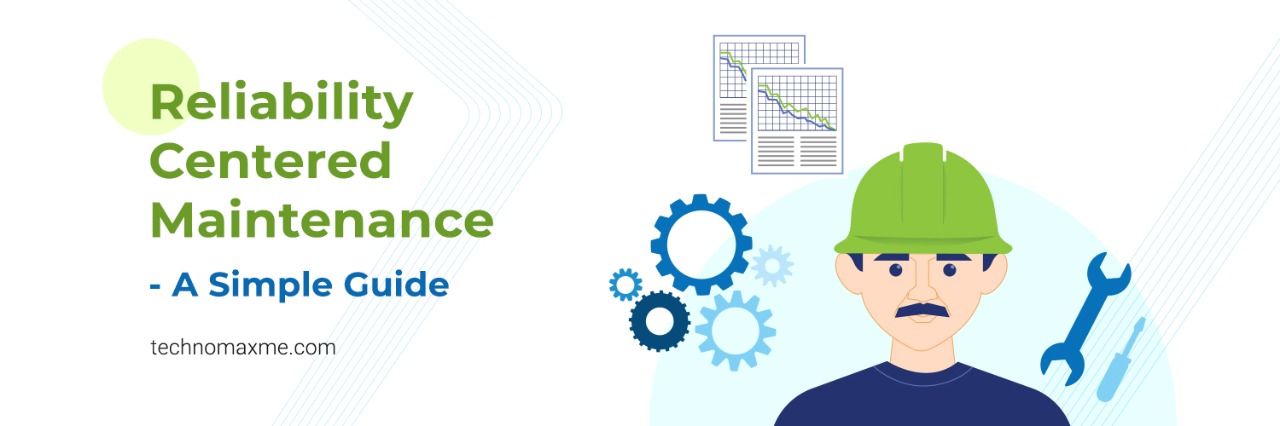
Reliability Centered Maintenance – A Simple Guide
Reliability centered maintenance is an approach to maintenance that seeks to find the most optimal maintenance strategy for the assets in your company in order to ensure maximum reliability and availability of those assets. It is not wise to follow a one-size-fits-all strategy when it comes to maintenance management because various assets have different requirements, capacities, and functionalities – and ways of failing. This means that the reasons they fail, and the resultant consequences vary, as do the strategies to prevent those failures. In a nutshell, Reliability centered maintenance is about establishing what works, and making it work for you in a more efficient way possible.
As we said earlier, various assets need various maintenance management styles; for example, some may need constant hi-tech monitoring – and this is one of the arenas Technomax excels in - whereas some may be simply left till they fail, also called run-to-failure; for most assets, preventive maintenance is the best bet. Though run-to-fail sounds like a poor choice, it is preferred when the asset is less critical, can be replaced by experienced technicians, and there is no safety risk or chance of reduced productivity.
You may also like to read:
- Vibration Structural Analysis - Ultimate Guide
- Everything you need to Know About Dynamic Electrical Motor Testing
- Complete Guide - Cloud Based Vibration Monitoring
- Laser Shaft Alignment- An Overview
How to decide the best strategy for maintenance?
To begin with, you need to look at the record of past asset breakdowns, and what steps you have taken for their maintenance and repair. See what worked best, and it will help you select the best strategy for asset maintenance. Ensuring high reliability levels consistently at the least possible expense is the chief goal of reliability centered maintenance – or to put it simply, to get the most ROI.
At Technomax, we follow these principles while providing our services, which are vital for an Reliability centered maintenance program:
- Preserving system function as primary goal
- Identification of failure modes that may impact system function
- Prioritizing of failure modes
- Choosing the appropriate tasks to control failure modes
We ask these 7 questions, which form the foundation of reliability centered maintenance:
1. What is the asset’s function, and what are its performance standards?
Here, we first establish the maintenance functions of the asset – that is, how it performs, and its ability to fulfil company requirements within environmental safety and regulatory standard ambits. We familiarize ourselves with the scope of functions, their limitations, and usage methods with relevance to safety and environment. Let’s suppose that your company has an industrial scale – obviously it will have a weight limit. When it’s loaded beyond that limit, it may stop functioning or become inaccurate. Manufacturer documentation usually provides this information, along with instructions about placing the items to weigh, and how to store the scale.
2. What is this asset’s purpose, how much is it doing now and how much do you want it to do?
Let’s say you have a conveyor belt to move cartons; at present it moves around 6000 cartons before it breaks down, and this causes a stoppage of two hours. Combining the manufacturer info, and the data in your software, the maintenance team – that is us – may be able to help you increase the number of cartons to 7500 and reduce the breakdown time from two to 1.5 hours.
3.What are the ways the equipment can fail?
In other words, this refers to identifying the modes of failure in an asset, or the nature of asset failure. Like, is it malfunction of a single part, or total? Identifying how exactly an asset has failed, frequency of breakdown, and whether it’s a specific part that fails constantly or various parts are failing, is extremely important. If your company uses several numbers of the same asset – like say dozens of the weighing scale – it’s vital to establish if the breakdown is across all the scales, or just one scale.
4. What are the causes of each failure?
Once we establish the failure mode, the next step is to identify the WHY; also, when and how, the failures usually occur. This is more important for equipment used a lot – it could have operating fatigue. Knowing when the machine is most likely to break down is also important. Let’s say your manufacturing process generates a lot of heat, so you need coolers to be run continuously; it could break down from the constant use. Other reasons include exposure to the elements, human errors, design or manufacturing defects, etc.
5. What happens during each breakdown?
It’s critical that you know the effects of the breakdown – they could be minor, or major. For example, failure of a part or a machine may cause slower production or poorer quality; or, it may release smoke, rattle, and come to a stop. Eventually every machine failure affects operations and productivity, and can cost you in terms of repairs & delayed production and most importantly unsafe for the people. Read more about Reliability centered maintenance.
6. How does each failure impact you?
It’s essential to know about the safety risks for your employees and environmental impacts in addition to the financial burden of machine breakdowns. You must also establish how failure impacts the overall condition and functionality of your machine.
7. What proactive steps can be taken?
Examine the past repair and maintenance records of the machine, and you’ll be able to identify patterns; this will help you to schedule preventive measures to prevent breakdowns. In the conveyor belt example, we saw breakdowns happening after 6000 cartons; so we can schedule an inspection after 5000 or 5500 cartons and quickly fix any potential problems to increase the uptime. Of course, in certain cases, it may be better to simply allow the run-to-failure approach – if the expense and effort of avoiding the failure are more than the value provided by the uptime, etc. Of course, you could have a situation where neither run-to-failure, nor preventive measures are feasible. There are no perfect answers for this; just that you need to be prepared to have a solution that can be implemented when the machine fails, with minimal disruption and cost.
Remember one thing though, that while these 7 questions are critical and mostly permanent, the answers are subject to change. Like, an asset which is highly critical currently, may become less important in a few years; or the expenses for different maintenance strategies may rise or fall due to various factors. So the answers need to be reviewed periodically.
Reliability centered maintenance is different from risk-based maintenance.
- With Reliability Centered Maintenance we choose the most optimal maintenance strategy for an asset
- In risk-based maintenance, we need to prioritize which assets to maintain properly as time and resources are limited; for this, you need to set criticality levels for all assets, and plan maintenance, and assign parts and repairs accordingly. For example, the assets whose failure has high negative consequences will be prioritized, etc.
Reliability Centered Maintenance Implementation
You have to think how bad your business is impacted if a specific asset fails, then factor in maintenance costs, injury risk, environmental damage, production loss, fines for non-compliance and so on, and prioritize assets from highest to lowest. Use the questions above to set the best maintenance strategy for each.
- Knowing the history of maintenance and repairs of an asset makes Reliability Centered Maintenance implementation easy.
- Implement a robust CMMS to have accurate asset data
Are you ready to incorporate reliability centered maintenance for your valuable equipment? Contact Technomax today, and we’ll be happy to explain how it works.
Read more about:
Learn More About Our Services
Recent Blogs
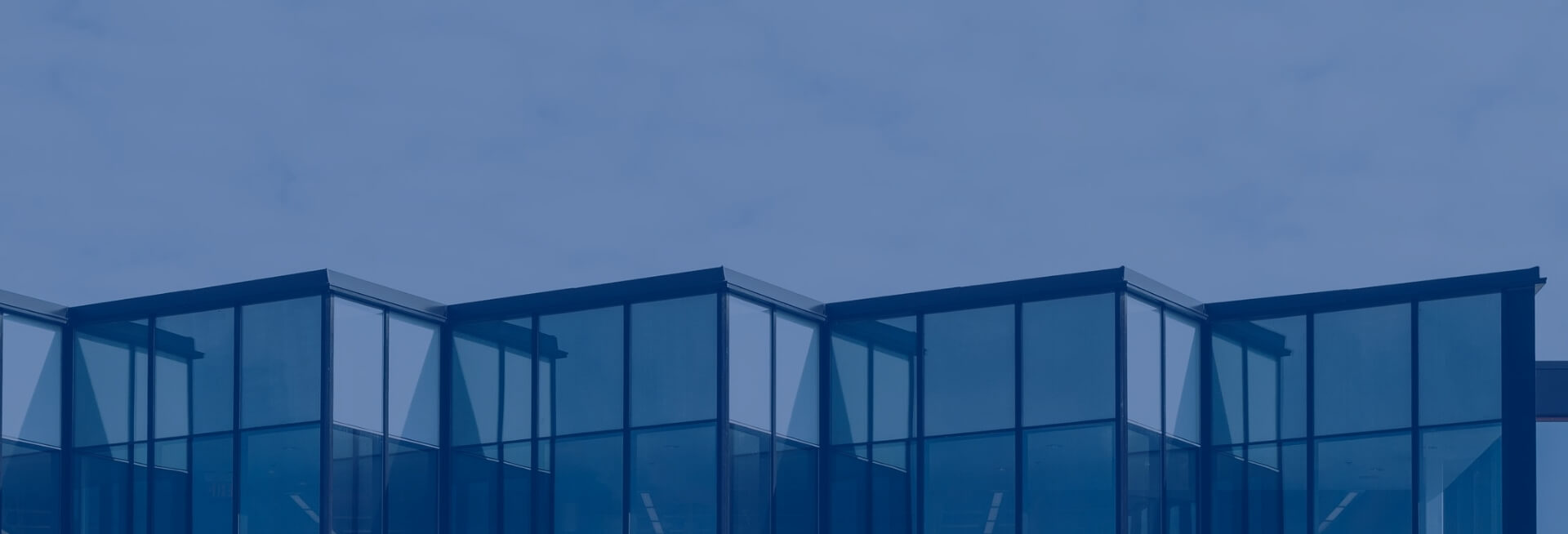
Get Started Now!
It takes less than a minute of your time. Or you may simply call +971 2 555 1 783