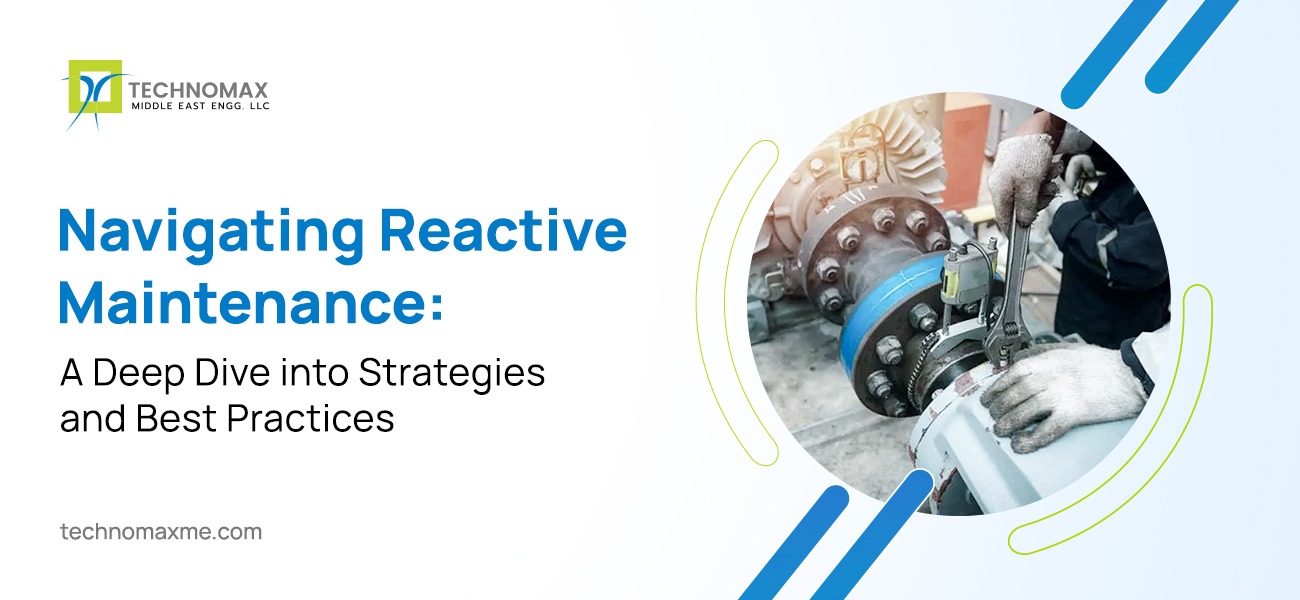
Navigating Reactive Maintenance: A Deep Dive into Strategies and Best Practices
Introduction
Reactive maintenance serves the purpose of addressing problems only when they arise. These problems could be in the form of equipment malfunctions, setbacks, and failures. For instance, would you change a light bulb before it burns out? Logically, you would replace a light bulb only when it burns out. Similarly, if the pieces of equipment are non-critical and low-cost, the run-to-failure approach is the best, as it has no major impact on the equipment or the team's safety.
Significance of Reactive Maintenance
Reactive maintenance is of huge significance in various industries, including the automotive industry and road infrastructure repair. For instance, when the battery of a car dies, the owner either tries to jumpstart the battery or replace it. Similarly, one of the most common problems in road repair is potholes, which can only be fixed when they occur.
This blog post will focus on understanding in detail reactive maintenance, its different types, influencing factors, strategies to make reactive maintenance effective, and more.
Understanding Reactive Maintenance
When we talk about the classical maintenance approaches, reactive maintenance is considered one of the oldest. It is also called the run-to-failure approach and is deployed only after an asset breaks down to restore assets to operating conditions. A Plant Engineering (https://www.plantengineering.com/articles/plant-engineering-2017-maintenance-study/) study shows that 61% of manufacturing facilities use this reactive maintenance approach.
Characteristics of Reactive Maintenance
- Reactive maintenance needs little to no planning, scheduling, or equipment downtime upfront.
- Planning for an unexpected downtime should follow the failure of the equipment in the future.
- Unlike preventive maintenance methods, no manpower is needed for weekly or monthly inspections.
- Lower upfront costs because you won't have to invest in any preventive maintenance strategies.
Pros and cons
Pros:
⦁ The initial cost of implementation is minimal.
⦁ less labor-intensive, hence saving on overhead costs.
⦁ Reactive maintenance reserves resources for other projects.
⦁ Little to no planning is required.
⦁ Ideal for non-critical assets.
Cons:
⦁ The possible impact of an unplanned downtime
⦁ Chance of increased energy costs
Common Types of Reactive Maintenance
Reactive maintenance can be considered the head-banner for all types of responsive maintenance, and opting for an ideal maintenance strategy could vary from business to business.
Breakdown Maintenance
Breakdown maintenance is an unplanned event that calls for emergency action. For example, when equipment malfunctions and requires a major repair or perhaps a replacement to continue production, a breakdown maintenance strategy is imperative. This can result in high repair costs, technician call-out charges, and production downtime. Because of unplanned downtime, manufacturers alone can lose up to $26,000 per hour. If the breakdown is unaddressed in time, businesses can have to bear 10 times more losses than a regular breakdown. Unforeseen malfunctioning of critical systems necessitates a contingent plan and immediate action instead of breakdown maintenance.
Run-to-Failure Maintenance
Run-to-failure maintenance is when you anticipate equipment to wear out until it reaches its usage capacity and then implement a reactive maintenance strategy. The major difference between RTF maintenance and breakdown maintenance is that the former is planned and intentional, whereas the latter is sudden and unexpected. The run-to-failure method always has a plan B and is carried out without causing a disruption in production. This approach is applicable to machines that have a non-critical role and is more cost-effective because replacements are either purchased in advance or a plan is intact beforehand.
Factors Influencing Reactive Maintenance
Multiple factors can influence reactive maintenance processes.
Unpredictable Nature of Failures: It can be affected by the unpredictable nature of machine failures, including safety, time constraints to organize resources following a sudden failure, and production hold-ups or stalls that incur more losses.
Lack of Maintenance Planning: The absence of maintenance planning can lead to abrupt production delays and uncertainties that can affect the lead time and confidence of workers and fuel economic stress.
Budget and Resource Constraints: Mobilizing resources and sourcing maintenance experts on short notice can be an operational nightmare. Reactive maintenance can be more costly than planned maintenance because of repair costs and potential damages from delays.
Impact on Overall Equipment Effectiveness (OEE): If there are no operational delays, the impact on overall effectiveness is value-added. However, as these approaches are unplanned, any delays can have a great impact on OEE, leading to huge losses.
Strategies for Efficient Reactive Maintenance
Quick Response and Rapid Diagnosis
You should have a proactive maintenance plan to minimize losses.
Establishing a responsive maintenance team: It is crucial to establish a highly efficient team that can swiftly and effectively tackle any unforeseen problems with the asset. This team should be equipped with the necessary knowledge and skills to handle complex problems and maintain the asset's optimal performance.
Efficient communication channels for issue reporting: You should establish channels for efficient communication, such as alerts for required maintenance and access to stored information.
Utilizing diagnostic tools for swift problem identification: An asset database is an excellent approach that engineers can use to scan and identify parts that cause issues.
Spare Parts Management
Importance of maintaining a well-stocked inventory: Good inventory management facilitates the maintenance team reaching the required tools promptly.
Techniques for optimizing spare part storage: Label critical components and categorize items in the inventory in ABC and XYZ ways. Stay updated on the billing for tolls. Emphasize inventory control when training employees.
Collaborating with suppliers for rapid part availability: Collaborating with suppliers is advantageous to both sides. Jobs can be executed swiftly. The collaboration has positive impacts on overall business performance.
Documentation and knowledge sharing
Maintaining thorough maintenance records: Record the date, time, and details of the work done for each maintenance task. Add information about repairs, replacements, inspections, lubrication, and any alterations.
Knowledge transfer among maintenance personnel: Keep track of the various procedures that are involved, such as the tool inventory and equipment data, and provide them to the maintenance staff.
Building a knowledge base for recurring issues: Identify the crucial elements, organize, and distribute them to others for faster resolution of reoccurring problems.
You may also like:
- Demystifying Partial Discharge: Understanding Its Impact and Detection
- Exploring Technomax’s Ferrography Services
- Crane Modernization from Technomax
Challenges of Reactive Maintenance
The reactive maintenance strategy works best until the assets fail. The following challenges must be considered:
Downtime and Production Losses: Planned maintenance can be added to the schedule, but unplanned repairs can happen instantly or be cumbersome. Moreover, there's uncertainty around the length of the delay. It can cause heavy production lead times and additional losses.
Safety Concerns for Personnel: To ensure that everything is done correctly, technicians can thoroughly go over standard operating procedures and safety regulations. Reactive maintenance involves technicians taking more impromptu risks to restart the system quickly. This strategy can raise safety issues and go against the goals most businesses have for health and safety.
Escalating Maintenance Costs: As failures are unpredictable, controlling the budget for labour and spare parts is incredibly hard. The company may end up paying a premium for emergency parts shipping, labour, travel time, and support hours. This demands budgeting for maintenance and proper forecasting beforehand. These costs may even escalate.
Negative Impact on Equipment Lifespan: Reactive maintenance doesn't keep the system running in optimal condition. If systems are maintained reactively in the long run, it can lead to faster deterioration. This leads to recurring capital costs. In such cases, the return on net assets (RONA) gets negatively impacted.
Mitigating the drawbacks
To avoid cost hikes, safety issues, delays, and other issues linked to reactive maintenance, use these ways to mitigate drawbacks.
Transitioning to Proactive Approaches: Aim to proactively identify and address issues. Create a tool inventory and maintenance team, and transfer knowledge. This reduces downtime and increases asset reliability.
Establishing a Maintenance Schedule: Creating a maintenance schedule can save on costs incurred by an unexpected event. Take inventory of your assets. Priorities are those assets that are critical for the success of the company, failures that are preventable with regular maintenance, and those that are more likely to fail with age. Determine ideal maintenance intervals using historical equipment maintenance data. Plan recurring tasks and inspections.
Implementing predictive maintenance techniques: estimating and preventing equipment failures through data analytics is predictive maintenance. Identify priority assets. Start training staff with new and advanced tools. Set maintenance standards and baselines, for instance, Prioritize machine service after 10,000 hours of use. Conditions and performance should be in real-time at the baseline. Condition-monitoring devices and sensors, vibration meters, oil analysis tools, or a thermal imagery camera are possible tools. Link these devices to the CMMS (computerized maintenance management system) tool and the database. Initiate your PDM strategy.
Conducting Root Cause Analysis for Recurring Issues: This includes four steps. It starts with addressing the problem, collecting the data, mapping out events in chronological order, and fixing the problem.
The Future of Reactive Maintenance
Companies are either updating systems for proactive maintenance or reshaping the reactive maintenance model.
The Role of Technology in Enhancing Reactive Maintenance: Technology is improving reactive maintenance effectively. Sensors help detect problems beforehand and quickly, which revolutionizes reactive maintenance and minimizes losses.
Integration with Predictive Maintenance Techniques: Predictive maintenance helps industries tackle unforeseen circumstances by using data from sensors before the equipment fails. It alerts staff to problems from escalating, leading up to costly outages.
Balancing Reactive and Proactive Approaches: Reactive management means addressing issues after they occur, and proactive management means identifying and tackling challenges beforehand, It is always prudent to have a contingency plan in place and readily accessible. We want both approaches to be balanced so problems can be tackled both proactively and reactively. An equilibrium of both proactive and reactive maintenance strategies is what we need to deal with unexpected machine failures.
Conclusion
Key takeaways are:
⦁ Under the right circumstances, reactive maintenance can reduce time and maintenance costs.
⦁ Reactive maintenance can be affected by unforeseen circumstances that can be tackled with technological tools.
⦁ Strategize a reactive maintenance approach with rapid diagnosis, establish a response team, and maintain an inventory of tools for efficient maintenance.
⦁ Document data and transfer it to personnel to overcome challenges that occur through reactive maintenance.
⦁ Identify problems, schedule maintenance, and determine unforeseen circumstances with predictive maintenance to mitigate drawbacks.
⦁ When companies are switching to other maintenance approaches, it's also revolutionizing to follow reactive maintenance.
Reactive maintenance is a quality approach if hindrances are sorted out quickly. This is a well-rounded strategy to achieve success in less time.
Learn More About Our Services
Recent Blogs
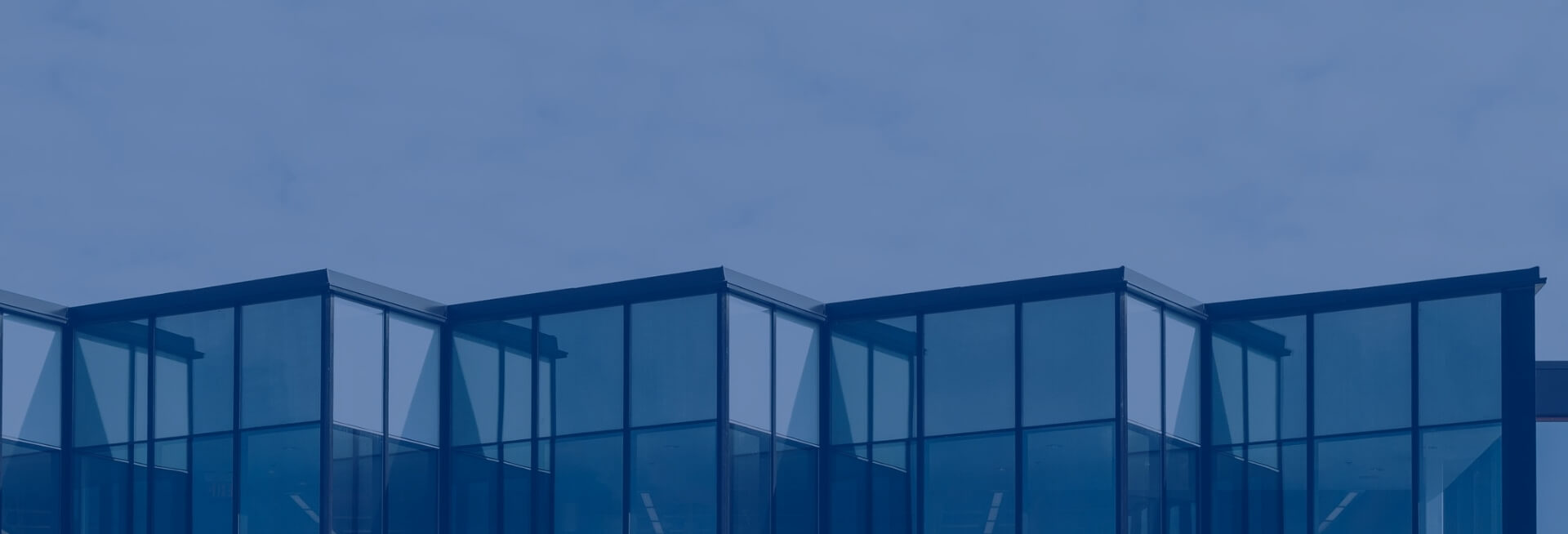
Get Started Now!
It takes less than a minute of your time. Or you may simply call +971 2 555 1 783