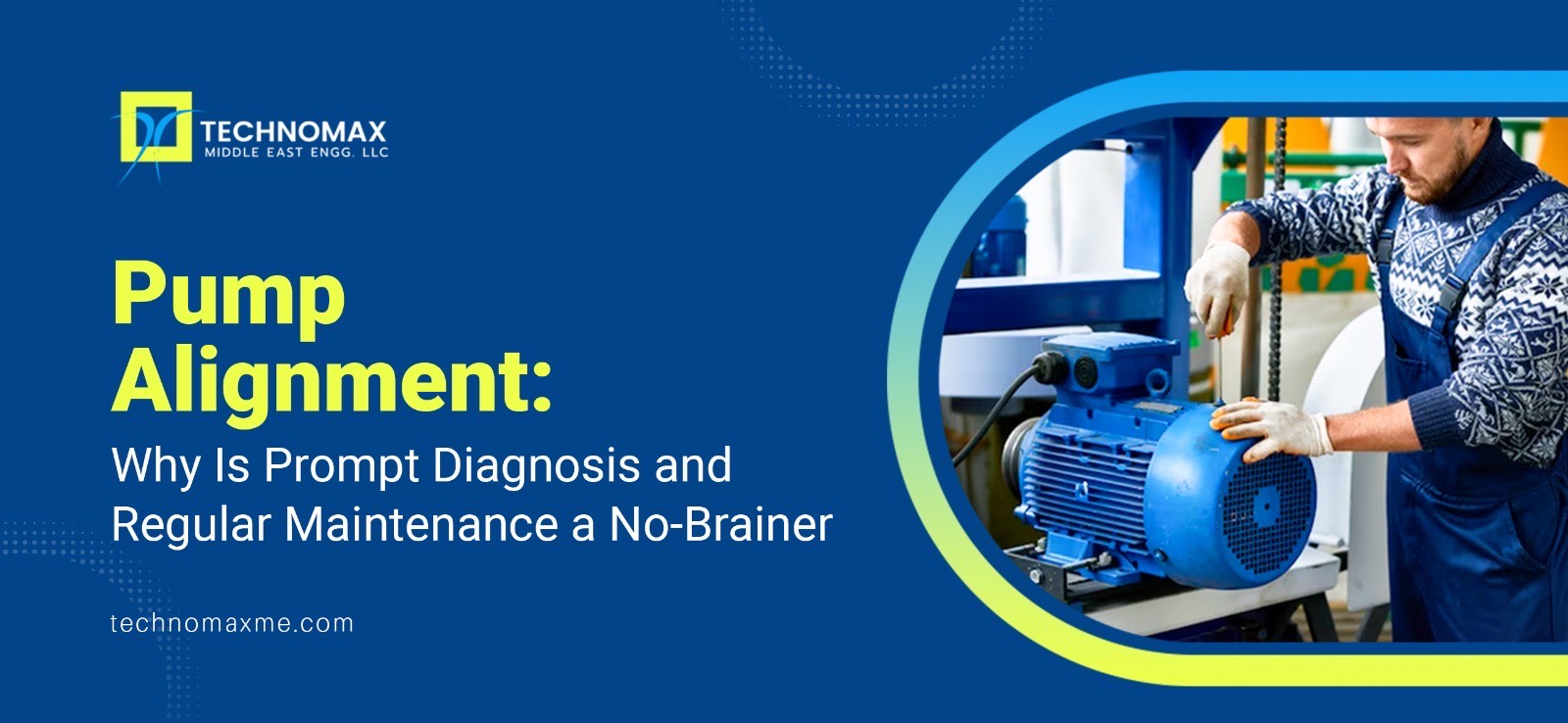
Pump Alignment: Why Is Prompt Diagnosis and Regular Maintenance a No-Brainer
Pump alignment is necessary for the pumps in numerous industries like oil refineries, water-treatment plants, power plants, and many other manufacturing facilities. Like any other indispensable machinery part, pumps ensure that the processes flow uninterrupted and remain efficient and reliable. Even so, achieving optimum performance depends on a crucial aspect: a properly aligned pump.
In this blog, let us examine the consequences of pump misalignment and see practical guidance on detecting such issues. We will also discuss the best practices for maintaining optimal performance and avoiding downtime.
What Is Pump Alignment?
Pump alignment is correcting the centres or shafts of two or more rotating machines, allowing them to operate efficiently, stably, and without causing unnecessary strain or vibration on the components. While pumps and their driving motors are the primary focus, this practice can also be applied to machinery with rotating parts, such as turbines and compressors.
The Importance of Precise Shaft Alignment for Pump Performance and Efficiency
Achieving optimal pump performance, reliability, and operational efficiency is crucial in any industrial setting, and precise shaft alignment is a non-negotiable foundation. Perfect alignment ensures that the power transfer from the motor to the pump happens seamlessly through their direct or indirect connection via a coupling.
Any deviation from this stable alignment would initiate detrimental forces and stresses, resulting in several negative consequences. The three main types of misalignment are:
- Radial Misalignment (Offset or Parallel): occurs when the centerlines of the shafts are parallel but laterally displaced like two parallel lines slightly shifted to the side.
- Axial Misalignment (End Float): This is when the shafts are aligned along their centerlines but exhibit unwanted axial movement, which can be seen as two aligned lines with one sliding back and forth.
- Angular Misalignment: occurs when the centerlines of the shafts deviate from parallelism, similar to two lines tilted at opposite angles.
What will be the repercussions of an unchecked pump misalignment? Ignoring misalignment can lead to a host of detrimental consequences for both the pump and the entire system, such as:
- Premature Component Failure: Critical pump components like seals, packing, shafts, and bearings experience premature wear and tear due to imbalanced forces caused by misalignment.
- Excessive Leakage: Misalignment results in unwanted leakage, wasting resources, potentially causing environmental concerns, and increasing maintenance costs.
- Excessive Vibration and Noise: Pump operation is disrupted by vibrations and noise triggered by misalignment, affecting system performance and equipment longevity.
- Reduced Efficiency: Misalignment significantly drains energy, reducing pump efficiency and increasing power consumption to maintain desired flow rates.
- Increased Power and Maintenance Costs: Reduced efficiency and increased wear and tear lead to higher power and maintenance costs.
How Rectifying Misalignment Can Help Enhance Machine Performance?
Ensuring precise shaft alignment offers several benefits for pump performance and efficiency, including:
- Improved Efficiency: Accurate alignment of the pump and motor system aids in the mitigation of friction and wear, thereby optimising energy consumption and operational effectiveness. This, in turn, leads to financial savings and a reduced ecological impact.
- Boosted Lifespan: Pump components, including bearings, seals, and shafts, receive a considerably prolonged lifespan due to reduced vibration and stress caused by misalignment. This results in decreased maintenance and operational interruptions.
- Improved Operational Safety: Misaligned pumps and motors are prone to excessive vibration, increasing the risk of mechanical failures and creating hazardous working conditions. Proper alignment mitigates these risks, promoting a safer work environment.
- Enhanced System Reliability and Safety: Strict alignment guarantees dependable pump operation and cuts down the likelihood of system failures that may present safety risks, thereby enhancing system dependability and security.
In short, precise pump shaft alignment is essential for maintaining optimal pump performance, ensuring system reliability, and reducing operational costs.
By prioritising proper maintenance and regular alignment checks, pump operators can guarantee a smooth flow within their operations and the continued health of their pumping systems.
Different Types of Pump Alignment
- Shaft Alignment:
This refers to the precise alignment of the pump and motor shafts along their rotational axes. Misalignment can occur in various forms, including offset, angular, or parallel misalignment, each with harmful consequences.
- Coupling Alignment:
The coupling connects the pump and motor shafts. It plays a crucial role in transmitting power while accommodating minor misalignments. Different coupling unbalancing offer varying degrees of flexibility and require specific alignment techniques.
Why Properly Aligned Motors Are Important?
The correct alignment of motors within a pump system is critical, as they provide the driving force for the pump. Misaligned motors can suffer similar consequences as misaligned pumps, including increased energy consumption, reduced lifespan, and increased vibration, ultimately affecting the performance and safety of the entire system.
By aligning pumps and motors, we can ensure smooth and efficient machine operation, reduce downtime, optimise resource use, and create a safe and productive working environment. Regular alignment inspections and adherence to best practices are vital to guarantee the maximum lifetime value of pumps.
Pump Alignment Methods
If you are wondering what tools are used for pump alignment, there are two primary pump alignment techniques:
- Straight Edge or Rim and Face Method: This traditional method uses a straight edge or callipers to measure offset and angular misalignment. It is simple and cost-effective; however, it requires trained personnel, and accuracy may be questionable.
- Laser Alignment: Laser alignment systems have two sensor heads attached to the shafts, communicating wirelessly or via cables to a display unit. The system provides instructions for shimming corrections and adjustments needed. It is accurate and fast, reducing person-to-person variability and labour time.
Pump Alignment Process
In the most common situation involving a pump and its motor, the procedure of pump alignment is adjusting the physical positions of the two components to ensure that a pump's rotational centerline aligns with the motor’s rotational centerline.
Laser alignment tools, feeler gauges, callipers, and dial indicators are some instruments used to measure alignment offsets. Continuous maintenance is needed after installing and initially aligning the pump and motor.
Alignment should be verified and confirmed after the machinery has operated under normal conditions, as thermal expansion can cause components to misalign.
Regularly monitoring machinery vibration is another crucial aspect of maintaining pump alignment, as a sudden vibration increase may indicate misaligned components. Pump alignment is vital in maintaining and operating rotating machinery, affecting operational efficiency, machinery lifespan, and workplace safety. Regular checks and maintenance are essential for keeping rotating machinery optimally aligned.
Understanding Pump Misalignment: Types and Implications
Let us delve into the various types of pump misalignment, each of which imposes substantial mechanical strain on pump components:
- Angular Misalignment: Occurs when the pump and drive shafts are not parallel, yielding excess bending forces on couplings, bearings and shafts. As a result, the components wear down faster, significantly reducing the pump and the machinery's operational lifespan.
- Parallel Misalignment: In this scenario, while shafts run parallel, they do not intersect at the same point, leading to uneven force distribution on the coupling, which results in vibrations and asymmetric wear.
- Vertical Misalignment: Inconsistencies in the vertical plane produce bending forces and strains, negatively affecting pump performance and seal lifespan.
Every misalignment type imparts mechanical damage to the pump, reducing its operational lifespan and often necessitating costly repairs and optimisation.
Importance of Accurate Pump Alignment
Given the substantial impact of alignment on equipment performance and durability, Regular inspections are essential. Scenarios demanding alignment verification include the following:
- During Setup or Major Overhauls: When installing new equipment or performing comprehensive maintenance, verify alignment to reduce component stress, cut energy usage, and prevent frequent equipment downtime.
- Experiencing Abnormal Operational Incidents: Machinery displaying excessive vibrations, significant overheating, or noticeable performance reductions indicates alignment issues. Prompt recognition and quick addressing of these issues can prevent further equipment damage and enhance performance.
- After Inactivity or Severe Environmental Conditions: Idle periods or exposure to harsh environmental conditions can potentially cause alignment issues. After these periods, inspecting and correcting alignment helps maintain operational efficiency and the prolonged lifespan of equipment.
Ongoing monitoring and evaluation of alignment throughout these critical phases serve to safeguard your investment, prolong the lifespan of machinery and maintain operational effectiveness.
Common Causes of Misalignment in Pumps
Misalignment can result from several factors, including:
- Incorrect Installation: Failure to follow manufacturer instructions during pump installation can lead to misalignment, resulting in uneven load distribution, rapid wear and tear, and premature component failure.
- Bearing Wear and Tear: Over time, bearings naturally wear out, potentially causing shaft deflection and subsequent misalignment.
- Soft Foot Conditions: If a motor foot does not rest flatly—usually referred to as a ''Soft-Foot'' condition—it can cause vibrations that lead to pump misalignment.
Other elements, like improper pipe alignment, external shocks, vibration, and thermal variations, also contribute to pump misalignment during its operational life cycle.
Pump Alignment Tools: Dial Indicators vs Laser Alignment Systems
When confirming pump alignment, two main tools come into play:
- Dial Indicators
- Laser Alignment Systems
Both instruments efficiently measure alignment but have distinct pros and cons.
Dial Indicators, both traditional and mechanical, measure small linear distances. They are known for their ability to identify minute alignment discrepancies.
However, they require careful handling and the supervision of a seasoned technician due to the manual process and intricate data interpretation. Despite these challenges, their precision, reliability, and affordability make them popular across various sectors.
On the other front, Laser Alignment Systems embody modern technological advancements. They use laser beams to provide accurate alignment measurements efficiently and simplify measured data interpretation. Despite the requirement of specific trained personnel and laser safety standard adherence, these systems can be cost-effective over time due to their speed and precision.
Choosing between dial indicators and laser alignment systems depends on machine requirements, workforce competence, budget restrictions, and workplace suitability.
Decoding Pump Misalignment
Early detection and correction of pump misalignment are imperative to avoid extensive and expensive repairs and improve overall operation efficiency.
Various signs can indicate misalignment:
- Unusually high vibrations
- Increased noise levels
- Drop in pump efficiency or flow rate
- Premature bearing failures
Fast response to these early warning signs can prevent unnecessary downtime and costly repairs, leading to substantial cost savings. How to ensure correct pump alignment? Maintaining optimal pump alignment necessitates a comprehensive strategy, which includes regular inspections to identify potential problems and implement solutions to prevent severe damage.
Adherence to manufacturer recommendations for pump alignment can ensure these machines run at peak efficiency. Laser alignment systems, known for their speedy, accurate results, can significantly contribute to maintaining optimal pump alignment. They help boost operational efficiency and extend pump lifespan.
Pump Laser Shaft Alignment Services from Technomax
Technomax is a leading engineering company in UAE offering the best Pump Laser Shaft Alignment Services. Why are we the best motor and pump shaft alignment service providers? At Technomax, we tread on the perfect combination of ultra-modern technologies and the expertise of experienced professionals to keep your industrial equipment running smoothly. Working with us assures:
- Increased Accuracy: We deploy cutting-edge laser alignment systems that significantly reduce the possibility of human errors with utmost precision.
- Improved Efficiency: By reducing adjustment time, our services aim to minimise production downtime, maximise operational efficiency and facilitate smooth pump operation.
- Optimised Performance: Our alignment services ensure the smooth operation of your pumps, promising continual high performance.
- Extended Lifespan: Our alignment services aim to prevent unnecessary machinery wear and tear, thereby extending pump lifespan.
As a pioneer in maintaining industrial machinery, we bring a wealth of expertise and an outstanding record in pump alignment, vibration analysis, partial discharge testing, etc. Whether a one-time assessment or a thorough maintenance program, our dedicated team handles alignment troubles effortlessly. We build our solutions to meet your specific needs, guaranteeing long-term reliability and maximum efficiency of your pump.
Technomax's professional alignment services help you address misalignment issues timely and prevent costly downtime, repairs, and reduced efficiency. Our skilled technicians conduct routine maintenance and alignment checks, helping to extend the lifespan and optimise the pump systems, ensuring smooth, efficient operation for many years. For more information, visit Technomax and see how our laser shaft alignment services can make a difference to your industrial operations.
Learn More About Our Services
Recent Blogs
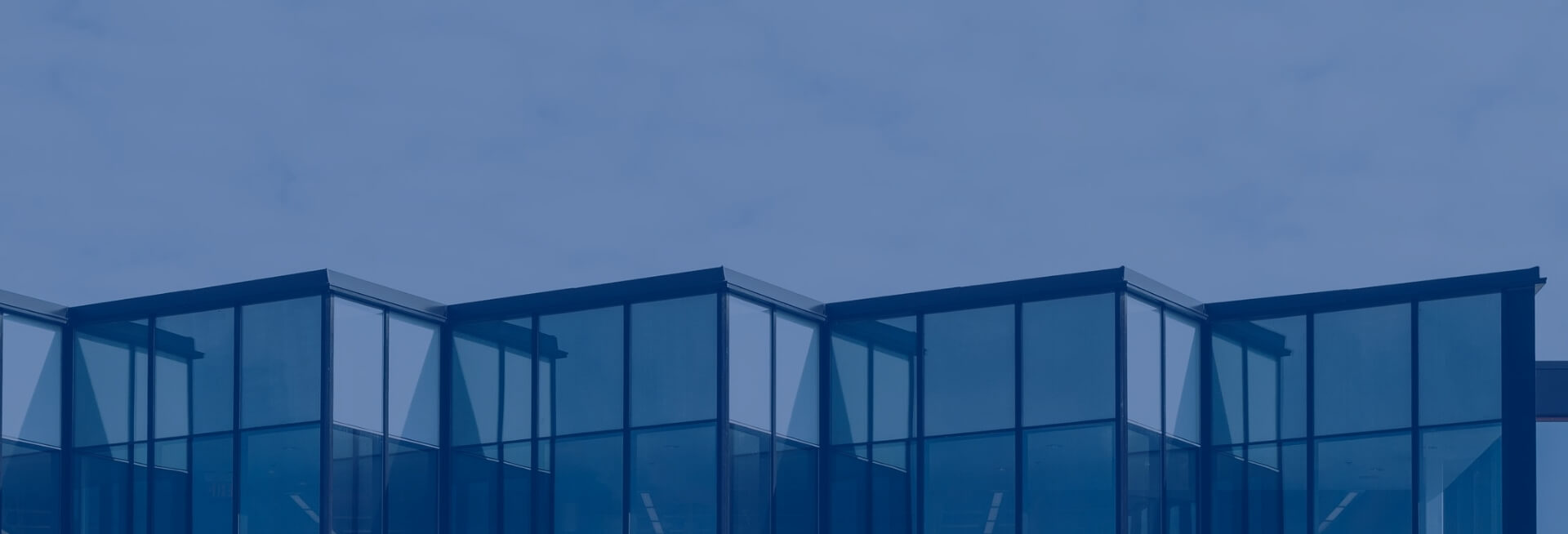
Get Started Now!
It takes less than a minute of your time. Or you may simply call +971 2 555 1 783