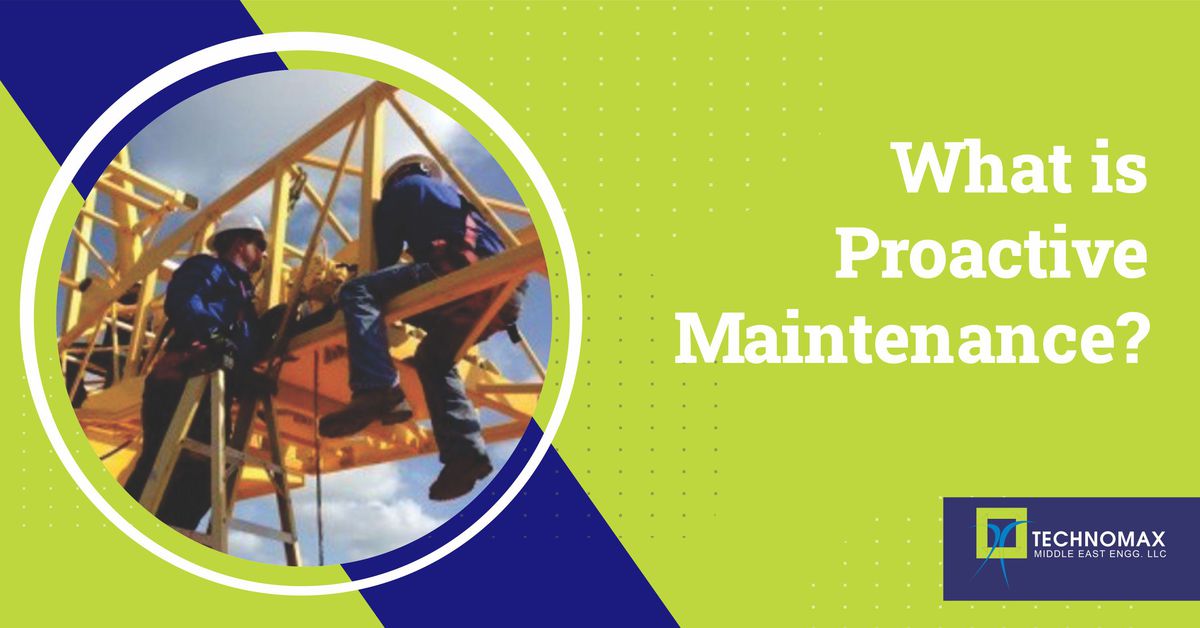
An introduction
Proactive maintenance is a preventive support technique that corrects the main drivers of failure and stays away from breakdowns brought about by underlying equipment conditions. The motivation behind proactive maintenance is to see machine failures as something that can be expected and killed before creating. Making a proactive maintenance program assists associations with finding hidden inefficiencies.
The proactive maintenance approach makes it conceivable to perform maintenance just when required, dependent on accumulated maintenance data. More deliberate components of a maintenance program are addressed instead of machines themselves when associations carry out proactive maintenance. This program permits associations to get enabled to:
- Recognize the underlying drivers of machine failure
- Resolve issues before they become failures
- Broaden the existence of machinery and lessen downtime because of machine failure
Gathering primary data, following continuous patterns and analyzing data to make a move after indications are found are the foundations of proactive maintenance. Numerous proactive maintenance programs are upheld by computerized maintenance management system (CMMS), condition monitoring, integrated data, and connected tools and sensors, and there are a couple of approaches and keys to execution achievement:
- Attention on failure modes
- Purchase in from initiative
- Technologies selection
- Skills enhancement
Benefits of the application of Proactive Maintenance
- Proactive maintenance helps the organization to avoid over and under maintenance cost, maintaining assets.
- It offers a balance of costs, reliability, uptime and asset health.
- It has a positive impact on customer satisfaction and business.
- Proactive maintenance is a time saving and cost-effective mechanism.
- Monitors timely temperatures in large motors and rotating equipment.
- Identify hot spots on electronic equipment.
- Identify timely leakages.
- Helps in finding faulty insulation, terminations in process.
- Proactive maintenance helps in capturing temperature readings.
- Proactive maintenance helps in eliminating a misdiagnosis.
- Helps in integrating thermal reports in data management software.
- Software used in the process helps to track the assets and review conditions over time.
- It aims to increase assets reliability and reduce the risk of downtime.
- It also helps in reducing maintenance and operational costs by addressing hidden operational inefficiencies.
Types of Proactive Maintenance
There are three types of Proactive Maintenance in basics. Organizations may use the mix of these maintenance strategies for different assets or systems.
- Preventive Maintenance (PM),
- Condition-based Maintenance (CBM)
- Scheduled (periodic) Maintenance.
How Proactive Maintenance Works actually?
Proactive maintenance progress can be challenging, with culture change, budget plan, absence of training assets, and full-time employees learning and performing the analysis. There are a couple of approaches to assist associations in starting with, including:
1.Focusing on failure modes: Prioritization of plant frameworks and failure modes with an impact on availability and capacity.
2. Receiving buy-in from leadership: The business choice of where to invest support assets and technologies
3. Technologies determination: Infusion of accessible maintenance technologies with remote abilities
4. Enhancing employee skillset: Increase in the centre competency of the maintenance group.
Conclusion
Proactive maintenance management uses CMMS software to watch, examine and call attention to the underlying drivers of breakdown or equipment failure.
If you have a preventative, predictive or reactive maintenance management in place, a proactive methodology can, in any case, fill in as a compliment. The methodology answers a solution for an issue before other maintenance frameworks get on the issue.
Learn More About Our Services
Recent Blogs
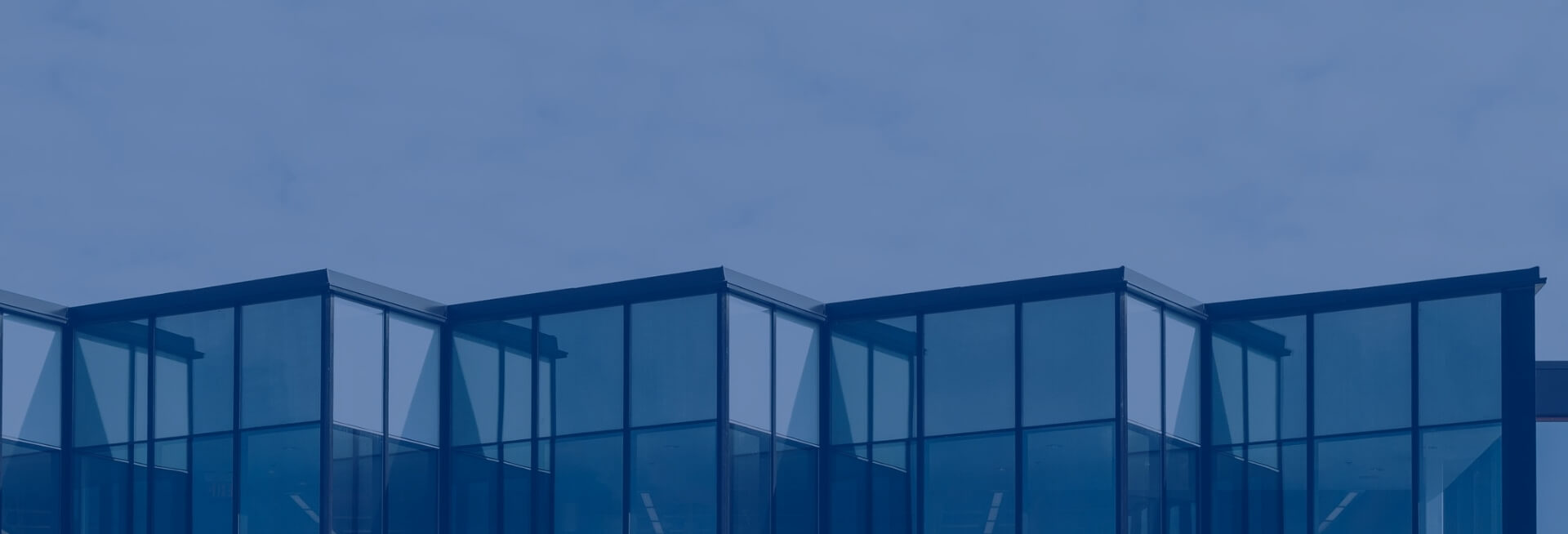
Get Started Now!
It takes less than a minute of your time. Or you may simply call +971 2 555 1 783