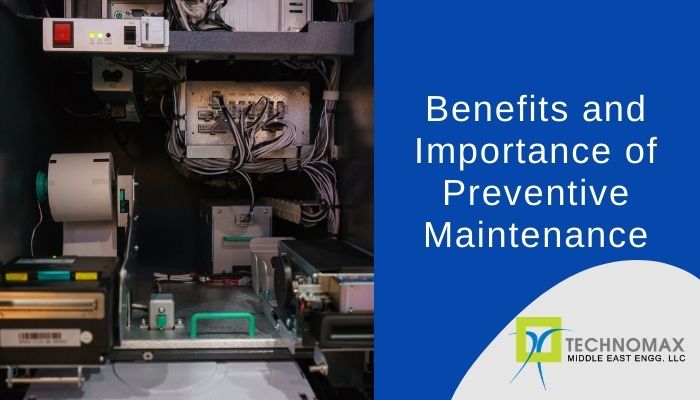
Table of Contents
- Introduction
- What is Preventive Maintenance?
- Planned Preventive Maintenance
- Importance of Preventive Maintenance
- Benefits of Preventive Maintenance
- Preventive Maintenance Checklists for Machines
- Preventive Maintenance Services
- Conclusion
What is Preventive Maintenance?
Preventive Maintenance is the process that helps you maintain the life span of the machinery and equipment and provides the optimum working efficiency of the same. Before diving deep into the importance of Preventive Maintenance let us understand the meaning of Preventive Maintenance. Don't you, as the operational manager or owner of the establishment, want to reduce the cost of production while also ensuring that no fatalities happen in the race to produce more? We had to write it to set the context but in all honesty, we already know the answer.
Preventive maintenance in condition monitoring is a proactive approach to ensuring the optimal performance and longevity of machinery and equipment within an industrial or operational setting. This strategy involves systematically monitoring the condition of assets to detect potential issues before they escalate into costly failures. By employing advanced technologies and data-driven techniques, preventive maintenance in condition monitoring aims to mitigate the risk of unplanned downtime, extend equipment life, and enhance overall operational efficiency.
Key components of preventive maintenance in condition monitoring include regular inspections, scheduled equipment assessments, and the continuous monitoring of critical parameters such as temperature, vibration, lubrication, and fluid levels.
Planned Preventive Maintenance
Planned preventative maintenance (PPM) offers the opportunity to significantly reduce the need for reactive maintenance and maintain assets at the desired quality level. There are two types of PPM: time-based maintenance and condition-based maintenance.
Let's delve into time-based preventative maintenance. This approach relies on a fixed frequency for carrying out maintenance activities, creating a calendar schedule. The maintenance schedule for an asset, equipment, or building structure is established from a library containing maintenance tasks and their predetermined execution frequencies. Warranties, supplier guidelines, legal requirements, or past experience may determine these frequencies. An example of time-based maintenance is the annual inspection of an air-conditioning unit, along with cleaning its filters every three years and replacing them every six years.
The methodology of condition-based preventative maintenance focuses on predicting asset failures and preventing them through the implementation of appropriate maintenance measures. This approach applies to assets capable of providing real-time status updates to the maintenance system. Monitoring enables just-in-time maintenance, minimising costs and averting potential failures and subsequent reactive maintenance efforts. Techniques for condition-based maintenance include vibration analysis, infrared thermography, oil analysis, partial discharge testing, and other methods. Learn more on condition based Vs. Predictive maintenance
In essence, while time-based maintenance relies on predetermined schedules, condition-based maintenance leverages real-time data to predict and prevent failures, leading to more efficient and cost-effective maintenance practices.
Importance of Preventive Maintenance
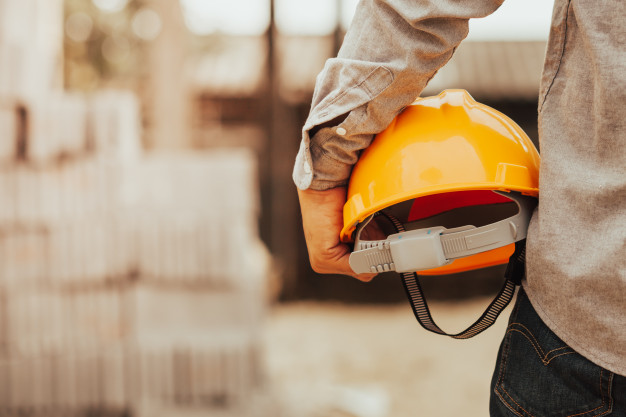
Preventive Maintenance is a mechanism that avoids the waste of time and breakdown of the production line. Preventive Maintenance is one of the important aspects of Facilities management. The consistent practice of Preventive Maintenance improves the performance and safety of the machine or equipment we use in any process. Reactive Maintenance costs small in the beginning but at last, gives a heavy burden and costly affair. At the same time, Preventive Maintenance tackles the cost affair from the very initial stage of operations.
Read more about Laser Shaft Alignment.
Let us read about the importance of Preventive Maintenance in detail-
- Operator safety: The first and foremost importance of Preventive Maintenance is safety. We all know that prevention is better than cure, so if we have opted and planned for Preventive Maintenance, then we are sure that our operator is working under controlled conditions and his life is safe. He is well versed with all the common safety operation tips.
- Machine safety: Like the life of human beings is important, similarly, the machine's life and condition are also important, so Preventive maintenance keeps the machine and equipment under safe mode which means no sudden malfunctioning and no random downtimes
- Time-saving: The time factor is very important while calculating the cost of each unit of production and adequate preventive maintenance ensures that no unnecessary costs are incurred hence. When there is no breakdown or obstructions in the line during the production process, optimum production on time will be possible.
- Cost-effective: The second most important factor is cost reduction or cost-effectiveness that will definitely be achieved because there will be no major fault and no sudden emergency repairs and no need of additional resources or outsourcing.
- Reliability: Preventive Maintenance program gives reliability to the whole system while working on the machines and equipment.
Benefits of Preventive Maintenance
It helps in avoiding unplanned maintenance activity, but it will rely on the creativity, ideas, knowledge, and skills of the managers who are responsible for keeping an eye on the process of the Preventive Maintenance program because the success of a Preventive Maintenance program is totally based on the cooperation of the parties involved. We are not saying that this process is not time taking or costly, but it ultimately saves from the heavy burden of breakdown and replacements.
So a big question arises whether we should install such a Preventive Maintenance system or not. Will it be worthy enough to invest money and manpower in the mechanism? We believe that it's always worth it if the benefits exceed costs. Here are several of the benefits of the Preventive Maintenance mechanism on our premises:
- Provides improved and quality working or operating conditions on the equipment for everyone.
- Time-saving and cost-saving, avoid heavy routine repairs frequently.
- Helps reduce the overtime costs, and workers will be used more economically.
- Avoids premature replacement of machinery and equipment.
- Increases the life expectancy of assets and better conservation of assets.
- Bring value to the users by using a web-based Preventive Maintenance program.
- Reduction of administration workload and they can focus more on maintaining the assets and clients.
- Decrease equipment downtime and improve reliability.
Preventive Maintenance Checklists for Machines
A preventive maintenance checklist for machines ensures the ongoing reliability, performance, and longevity of machinery in industrial or operational settings through its systematic and organized approach. This comprehensive checklist is a proactive approach to identifying and addressing potential issues before they escalate into costly failures, thereby minimising downtime and optimising operational efficiency.
Each machine requires regular performance of a series of tasks and inspections included in the preventive maintenance checklist.
- Inspect lubrication levels
- Examine Belt and Chain Tension
- Check for Wear and Tear
- Review Electrical Components
- Examine Seals and Gaskets
- Evaluate Cooling Systems
- Monitor Vibration Levels
- Check Alignment
- Inspect Safety Devices
- Review Software and Controls
- Examine Pneumatic and Hydraulic Systems
- Calibrate Sensors and Instruments
- Clean and Inspect Filters
- Inspect Wear Plates and Sliders
- Review Operational Logs
- Examine Structural Integrity
- Verify Fastener Tightness
- Evaluate Environmental Conditions
- Conduct Training and Awareness Programs
- Document and Analyze Trends
Preventive Maintenance Services
Machinery and equipment handling is the lifeblood of the system, so each piece of equipment must be inspected at an early stage. Preventive Maintenance services are a small investment that gives great returns by increasing the system's uptime and improving productivity. We have already read about the benefits and importance of Preventive Maintenance in detail.
Preventive Maintenance services are available 24 * 7 and a cloud-based computerized maintenance management system (CMMS) will give positive results. Services like the below mentioned are provided by many agencies that offer the installation of the Preventive Maintenance program. Preventive Maintenance Services depend on the particular type of equipment in use, manufacturer's recommendations, age of the machinery, and local environmental conditions. So inspection, execution, recording, scheduling, and reporting are all essential activities.
- Management of the reactive, preventive, and predictive maintenance of the specific equipment.
- Scheduling, assigning and tracking of the work orders towards the completion.
- Management of the spare parts inventory and track consumption also.
- Provide the updated notifications for the upcoming part orders.
- Monitoring the performance at the plant level, regional level, and organization level as a whole.
- Creates reporting facilities to do compliance management.
- Analyzing maintenance activities to make data-driven decision making.
- We are ensuring that machinery is clear of debris before and after shifting.
- Wiping the machinery surface of lubricants, dirt, and other debris each day.
- Inspection of tools for sharpness regularly.
- Replace the worn or damaged tools.
- Check all machinery fluid levels and air filters regularly.
- Calibrate the machinery regularly.
- Check and maintain the motor's efficiency and other power sources twice a year.
Preventive Maintenance Services from Technomax
The importance of Preventive Maintenance has shown how beneficial it can be. Preventive Maintenance avoids unnecessary production losses and health and safety violations. Ensures greater operational control to users and helps in preventing known problems in the future. The preventive maintenance program is based on factors like a particular type of equipment in use, manufacturer's recommendations, age of the machinery, and local environmental conditions. So inspection, execution, recording, scheduling, and reporting are all essential activities in the Preventive Maintenance program.
Technomax offers condition monitoring services like vibration analysis, partial discharge testing, lube oil analysis, laser shaft alignment services, Acoustic Emission Testing, Infrared thermography testing, CFD analysis services, and much more. Being the leading engineering company in UAE, the dedicated experts in Technomax offer reliable and timely services.
Learn More About Our Services
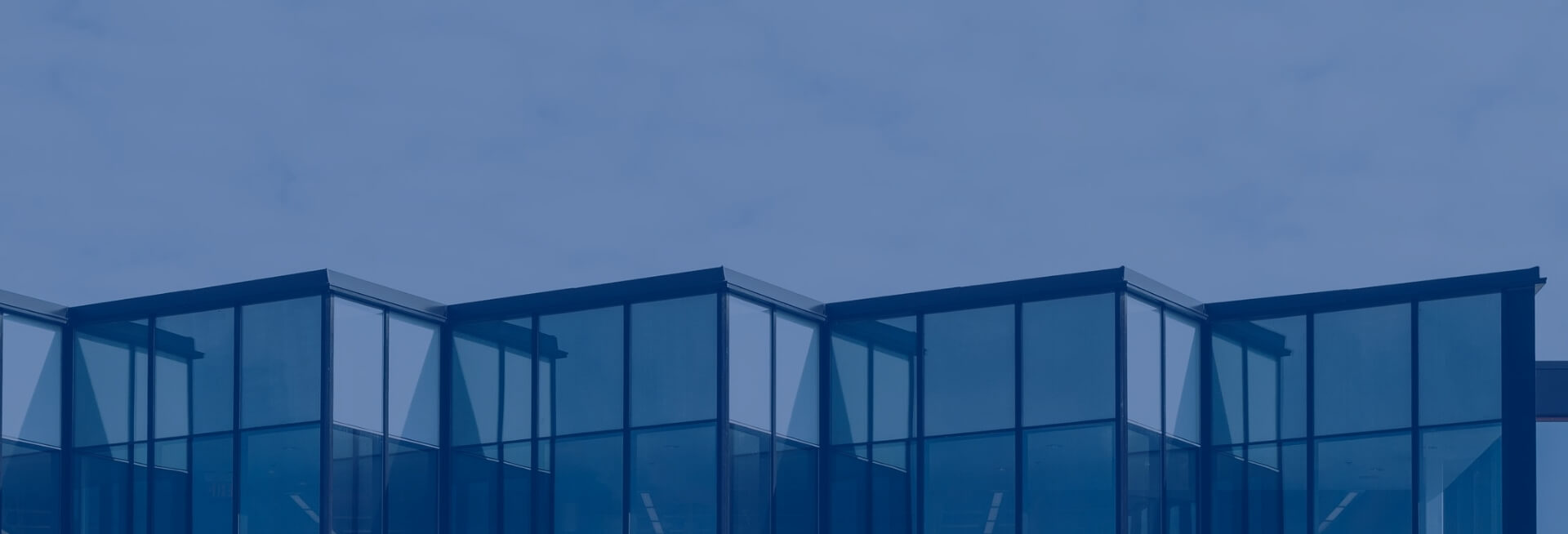
Get Started Now!
It takes less than a minute of your time. Or you may simply call +971 2 555 1 783