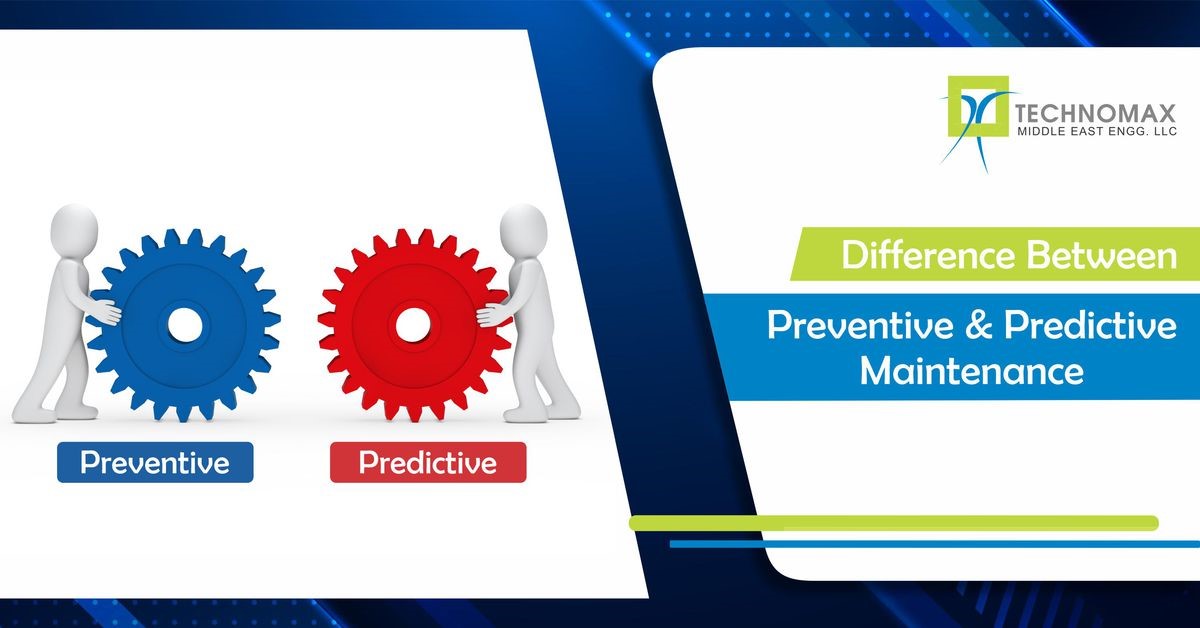
Preventive and predictive maintenance are two sides of the same coin, but they are not interchangeable.
Both are successful asset maintenance techniques, but you must consider the differences and complement one another. Here's a closer look at the differences between predictive and preventive maintenance and what you should know.
What Is Preventive Maintenance?
To avoid unintended equipment downtime or malfunction, facilities managers use a preventive maintenance plan that involves systematic asset checks and routine maintenance. Unlike reactive (or corrective) maintenance, which is performed after an asset has malfunctioned, preventive maintenance is performed before a problem arises.
Different forms of preventive maintenance use different triggers to assess when the equipment needs to be serviced. A few examples of preventative maintenance are as follows:
- Time-based maintenance entails performing routine maintenance regularly, such as regular, monthly, or annually.
- Maintenance is performed based on discovering physical signs of possible asset loss, which is known as condition-based maintenance.
- Preventive maintenance based on use entails undertaking maintenance after a certain amount of time has elapsed, such as hours of use or miles driven.
Preventive maintenance is appropriate for mission-critical assets that are more likely to fail as they age. Its use and the surrounding environment determine the amount of maintenance needed for any asset. The American National Standards Institute (ANSI) has general guidelines for what forms of inspections and maintenance are required and how frequently they should be performed.
Read more about - Laser Shaft Alignment
How Do You Implement Preventive Maintenance?
Preventive maintenance is not the same as merely watching equipment and observing the manufacturer's recommended repair plan. To properly enforce preventive maintenance, the facilities team must keep comprehensive asset profiles for each piece of equipment in the organization, including asset age, inspection dates, service history, and expected lifetime.
Asset management software provides FMs with on-demand access to all of these critical data in one convenient location. They can see this information at a glance and use it to handle service requests in conjunction with facility management tools. They can also set up workflows to send out service requests automatically when an asset hits a certain age or usage level.To know the difference between preventive and predictive maintenance we should know both.
What Is Predictive Maintenance?
Although preventive maintenance is highly reliant on industry averages and best practices to direct maintenance decisions, predictive maintenance includes determining when to conduct maintenance based on an asset's actual use.
Predictive maintenance (PdM) is a developing area, with new networking and data collection options being introduced all the time. According to the McKinsey Global Institute, implementing PdM activities around the manufacturing sector would result in a $240-$627 billion cost savings. It's a constructive technique, similar to preventive maintenance. To know more click here.
Although preventive maintenance relies on best practises and historical data, predictive maintenance collects data from system operations in real time and uses it to raise red flags when signs of a problem are detected. In conclusion, predictive maintenance entails:
- relying on interconnected measurement and data collection processes, as well as equipment and personnel to interpret the data
- Potential issues are identified and addressed,
- allowing repairs to take place before a malfunction occurs.
- Can be done when the machines are in their normal development modes.
The following are the significant differences between preventive and predictive maintenance:
- Whether or not preventive maintenance is needed, it happens on the same schedule every cycle. Preventive maintenance is intended to keep parts in good working order, but it ignores the state of a system or operation.
- Predictive maintenance is performed as required, based on real-time data collection and analysis of machine activity data, to detect issues early before they disrupt development. Repairs occur during system service and solve an actual problem with predictive maintenance. If a shutdown is necessary, it would be more focused and shorter.
Although scheduled downtime during preventive maintenance is inconvenient and reduces overall capacity availability, it is preferable to unplanned downtime during reactive maintenance. Costs and length are uncertain before the issue is diagnosed and resolved.So it is all about difference in preventive and predictive maintenance
Learn More About Our Services
Recent Blogs
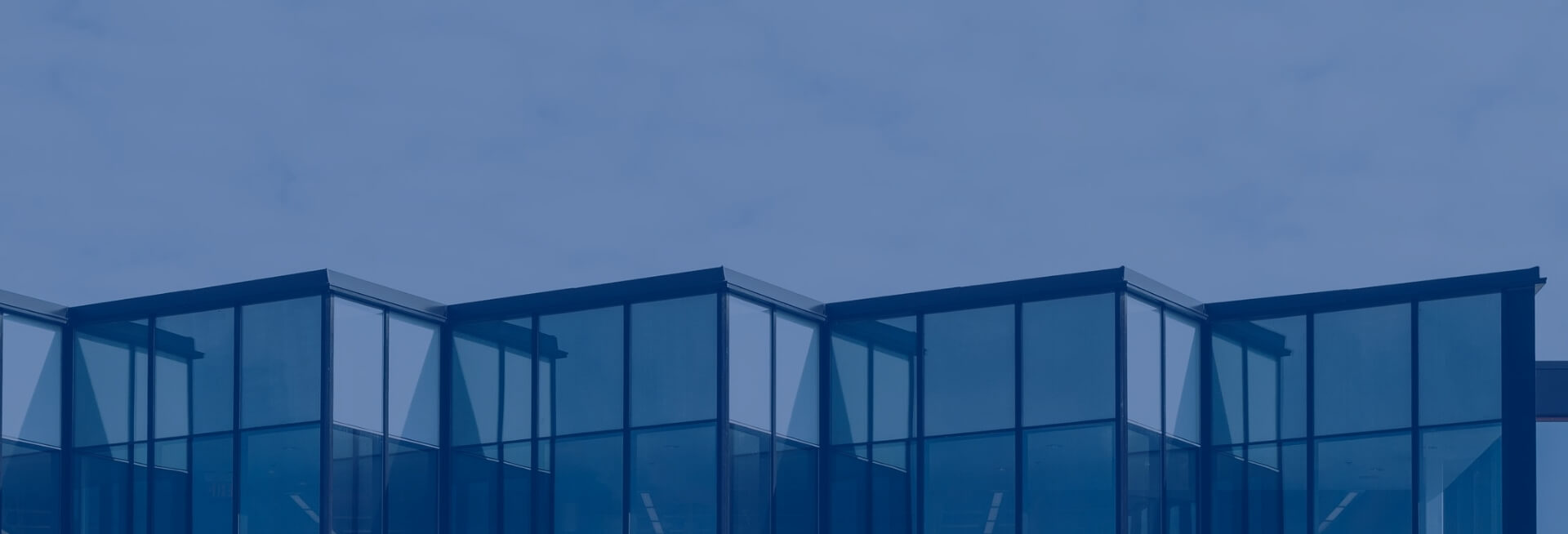
Get Started Now!
It takes less than a minute of your time. Or you may simply call +971 2 555 1 783