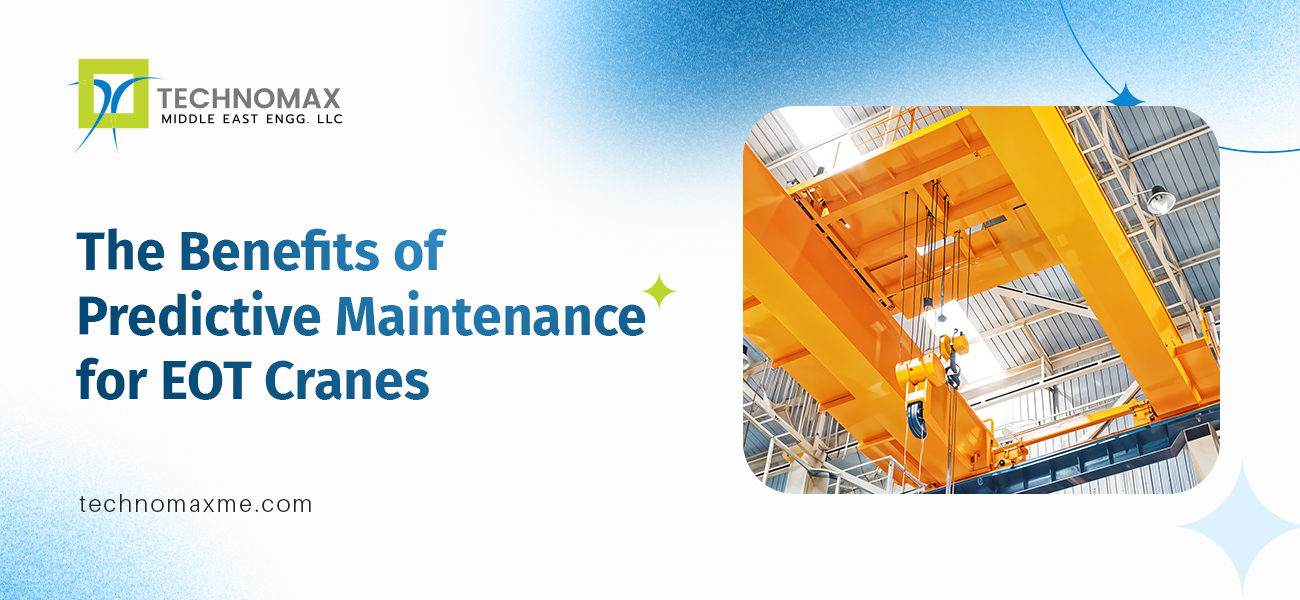
How Predictive Maintenance Improves EOT Crane Performance ?
In industries where efficiency and safety are paramount, maintaining your EOT (Electric Overhead Travelling) cranes is not just a routine task—it's a necessity. Predictive maintenance offers an innovative approach to identifying potential issues before they escalate, reducing downtime, and optimising performance. By utilising advanced technologies like IoT sensors and data analytics, predictive maintenance ensures your cranes operate at peak efficiency, minimising costly repairs and unexpected failures. Continue reading to know more about the benefits of predictive maintenance in EOT cranes and how it assists in operations.
What Is Meant by Predictive Maintenance?
Predictive maintenance is a proactive maintenance strategy that uses advanced data analysis, sensor technology, and machine learning to monitor equipment conditions and predict when a component is likely to fail. The goal is to perform maintenance tasks before a failure occurs, minimising downtime and reducing repair costs.
How Does Predictive Maintenance Work?
Predictive maintenance is done by installing sensors on the critical components of EOT cranes to gather data. These sensors monitor key indicators, including temperature, vibration and operational load, which give a clear insight into the condition of the crane. The collected information is then fed into predictive maintenance software, which uses algorithms and machine learning to analyse the data for patterns and trends that indicate potential issues.
If a concerning trend is found, such as consistent overloading or irregular movement, an alert is sent to maintenance teams, enabling them to take corrective action. By analysing real-time data and adapting maintenance schedules to each crane's actual needs, predictive maintenance systems help prevent unexpected breakdowns, improve efficiency, and extend equipment life.
How Does Predictive Maintenance Help Increase Productivity?
Equipment malfunctions can trigger a chain reaction that disrupts terminal operations. Major crane failures that require intervention from control system specialists can be expensive. Additionally, the ripple effects, such as delays in container handling and vessel schedules, compound the problem. Implementing predictive maintenance technology is essential to avoiding these challenges. Here are the different ways where predictive maintenance can boost productivity:
-
Tailored to Your Particular Crane Type
A single maintenance plan cannot be applied to all types of cranes, as each has unique specifications, configurations, and users. Therefore, it is essential to adopt a maintenance routine that can be customised to suit the specific needs of your crane.
Preventive crane maintenance offers a comprehensive approach that includes compliance inspections, addressing performance issues, and conducting routine upkeep. This all-in-one strategy boosts its efficiency and overall performance. The innovative tools not only streamline preventive maintenance procedures but also help ensure better compliance with safety codes.
-
Follow Manufacturers Manuals
Adhering to the manufacturer’s guidelines and monitoring the crane’s height, weight and load capacity are crucial aspects of an effective preventive maintenance strategy. This approach minimises the risk of accidents that could cause injuries or lead to material damage, such as slipping or swaying loads. However, to optimise your crane’s maintenance plan, it's essential to customise it based on detailed information about its service history, duty classification and operating environment.
-
Identifying Tasks
The third and most significant advantage of preventive crane inspections is the means to identify and mitigate risks promptly. Adopting a comprehensive risk mitigation framework enables crane operators to thoroughly evaluate all components, both large and small.
Key elements to include in this framework are:
- Inspecting crane equipment for visible damage.
- Identifying corrosion or early signs of rust or crane components.
- Ensuring the brake system operates smoothly and efficiently.
- Testing the hydraulic pressure system to avoid operational delays.
- Check wire ropes and slings thoroughly for damage indicators like warping, rust, or cracking.
The above-mentioned key elements provide better operational visibility and alert operators to lay inefficiencies, improving overall performance.
-
Early Repairs Reduce Bigger Cost Savings
Preventive maintenance is undeniably a cost-effective strategy in the long run, helping businesses address unexpected threats to crane operations with a comprehensive maintenance plan.
With advancements in technology, manual effort in maintenance routines is greatly reduced. Latest software tools now integrate with hardware components to provide timely alerts about potential issues, such as engine leaks, control box malfunctions, or jammed brakes.
Ultimately, postponing crane preventive maintenance leads to higher repair expenses over time. Crane safety can also be enhanced with tools like crane-rated capacity indicators. Be sure to include sling inspections, downtime evaluations, and hoist checks as your daily maintenance practices.
Artificial Intelligence and Machine Learning to Predict a Possible Standstill of Equipment
Artificial intelligence (AI) and machine Learning (ML) technologies play a significant role in predictive maintenance. These advanced technologies improve the accuracy and efficiency of maintenance predictions, making it easier to manage complex equipment such as EOT cranes.
- Pattern Recognition and Anomaly Detection: AI-driven predictive maintenance systems analyse extensive crane sensor datasets to detect anomalies in real-time. Machine learning algorithms learn to identify patterns in crane operations, flagging any deviations that could indicate potential issues.
- Increased Precision: AI’s ability to process large amounts of data results in precise maintenance predictions. This level of accuracy is specifically important for complex cranes that operate in high-demand environments, as it enables maintenance teams to prevent standstills and unexpected downtime.
- Self-Learning Capabilities: Over time, machine learning models become more accurate by adjusting to new data patterns. As these models gather information, they “learn” from past events, improving prediction quality and reducing the likelihood of false alarms. This self-learning aspect of AI and ML is advantageous for long-term maintenance strategies, where the system continually enhances its ability to forecast maintenance needs.
EOT Crane Installation and Maintenance with Technomax
When it comes to EOT crane installation and maintenance, Technomax stands out as an industry leader, providing end-to-end solutions for efficient, reliable crane operations. Being the leading engineering company in UAE, Technomax specialises in both initial crane installation and long-term maintenance, providing clients with comprehensive support tailored to their specific needs.
We are known for our comprehensive installation services, predictive maintenance solutions, and client-centric approach. Partnering with Technomax for predictive maintenance services empowers companies to maintain their EOT cranes at peak performance while avoiding costly downtime, making it an investment that enhances efficiency and profitability.
Learn More About Our Services
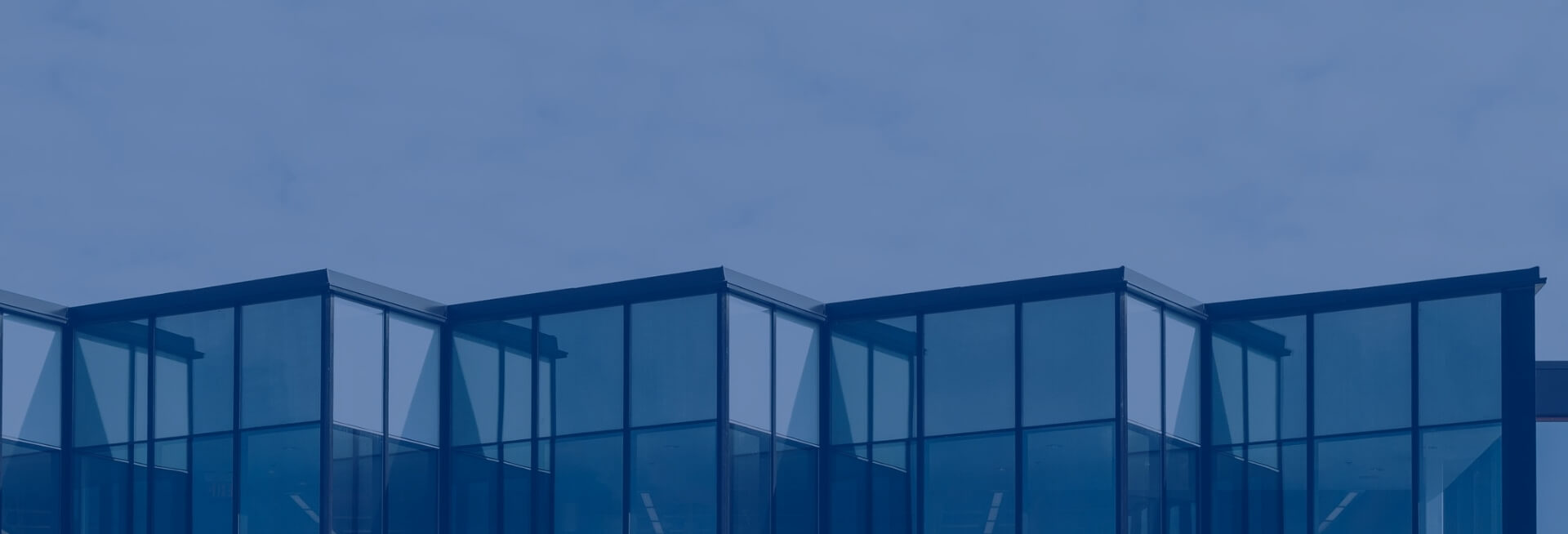
Get Started Now!
It takes less than a minute of your time. Or you may simply call +971 2 555 1 783