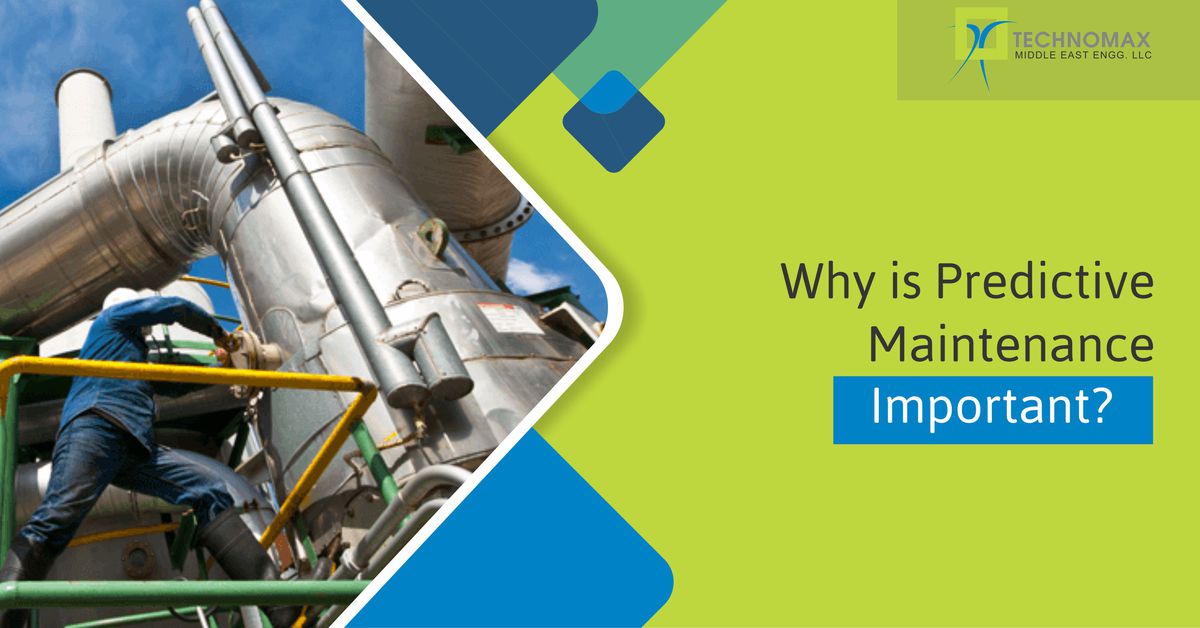
What is the bare minimum of maintenance work needed to maintain top working order assets and prevent unforeseen equipment failures? It's a difficult question that can only be resolved with the assistance of predictive maintenance. The ability to forecast a part's or asset's remaining useful life based on real-time data provides companies with a new way to control and maximize their maintenance capital.
According to Market Research Future's predictive maintenance study, the global predictive maintenance market is projected to reach $2.3 billion by 2025. The automotive industry has the most predictive maintenance implementations, but all companies with a lot of capital invested in their equipment are very interested.
To determine if predictive maintenance is a technique that could benefit your business, you must first understand what it is, how it works, what its benefits and drawbacks are, and how to go about implementing one.
You've come to the right place if you're searching for a resource that can answer all of those questions and more.
What is predictive maintenance (PdM)?
Predictive maintenance is a proactive maintenance technique that employs condition monitoring software to identify deterioration signs, irregularities, and equipment efficiency problems. Based on these calculations, the company will run pre-programmed predictive algorithms to predict when a piece of equipment may malfunction, allowing maintenance to begin just before it does.
Predictive maintenance seeks to maximize the efficiency of your maintenance capital. Maintenance managers can plan maintenance work only when required by understanding when a specific component will malfunction. This avoids unnecessary maintenance while also preventing accidental equipment failure.
Predictive maintenance, when properly implemented, reduces operating costs, reduces downtime, and increases overall asset health and efficiency.
How does predictive maintenance work?
Condition-monitoring equipment is used in predictive maintenance to measure an asset's performance in real-time. It uses condition-monitoring equipment to evaluate asset output in real-time. Predictive Maintainance provides an accurate method for gathering and analyzing asset data by integrating condition-based diagnostics with predictive formulas and a little support from the Internet of Things (IoT). This information enables the detection of any areas that need or may need attention.
Implementing predictive maintenance is easy. These are the steps:
- Schedule maintenance
- Install Internet of Things (IoT) devices
- Analyze failures modes
- Identify critical assets
- Connect devices to software
- Analyze and establish failures modes
- Establish a database
Predictive maintenance tools
Sensors, analytics and tracking software, and scheduling tools are the three forms of predictive maintenance tools. These tools may be used by your repair technicians or by hiring a specialized third party to come in daily to monitor your equipment.
IoT sensors
Sensors have always been an essential part of any maintenance strategy because they help us track changes and make improvements to keep minor issues from becoming major issues. Having several sensors to track various metrics will help you gain a deeper understanding of the processes and avoid early failures.
IoT sensors, which detect critical changes in components, are an essential part of this area. Different sensors can collect and exchange data using IoT technology. Predictive Maintainance heavily relies on these sensors to link the assets to a central system that stores the data.
Sensors enabling vibration, sonic, and ultrasonic analysis
Sensors provide data to the systems that are linked to them. A device can detect and record any irregular vibrations that can occur due to various factors once it has been calibrated.
In addition to the sensors, Predictive Maintainance software can access various data sources in real-time, predicting asset failure or quality issues. Predictive analytics is used in these solutions to identify irregularities and failure patterns, allowing them to predict where problems or disappointments are most likely to occur.
Thermal imaging sensors
Excessive heat can kill many devices, and it's a major maintenance problem for telecom companies. Thermal imaging employs infrared images to measure temperatures in such a way that any anomalies are easily detected. Like other change-sensitive monitors, they activate scheduling systems, which in turn cause the necessary action to be taken automatically to avoid component failure.
Oil and lubricant sensors
This sensor effectively measures the components of the primary complex impedance of oils. The sensor's measuring signals can be sent online to a web-based monitoring system via the sensor's LAN, WLAN, or serial interfaces. The key benefits of using these types of sensors are the ability to access lubrication conditions in severe conditions and equipment that is not readily available and develop an excellent predictive and proactive maintenance programme to identify early stages of lubricating oil degradation. Both of these advantages would result in substantial maintenance and operating cost savings.
Monitoring and industrial analytics tools
The 'fourth industrial revolution,' which is the convergence of conventional industrial processes, modern technologies, and IT improvements, includes industrial analytics. Data analytics, machine learning, and networking developments across the Internet of Things are among these advancements. This means that a growing number of decisions and activities are focused on data that can be measured. The previously collected data is analyzed using predictive algorithms, which classify patterns to predict when an asset may need to be repaired, serviced, or replaced.
Maintenance scheduling and planning tools
With the click of a button, we may delegate work to others. Your company's time and money will be used more efficiently thanks to scheduling solutions.
The following activities will benefit from the scheduling tools:
-Assigning personnel and arranging for programmes and projects to be completed.
-Proactive optimization of production schedules.
-Use countermeasures even faster if they are needed, increasing the number of adjustments to balance any problems that may arise.
-Detection of bottlenecks in various departments and introduction of practices to alleviate the problems.
How to implement predictive maintenance?
Data from predictive maintenance software is used to guide asset management decisions in a predictive maintenance strategy. Managers can make better decisions when they have a better understanding of the state of complex machinery.
How do you put a predictive maintenance plan in place, you may wonder? To begin, you must first determine the problem(s) you are attempting to resolve. Then you must evaluate your current situation or establish a baseline of machine performance data. You may use your guidelines, OEE standards, or other industry standards to accomplish this.
Second, you must look for trends in the historical data to determine which metrics suggest an issue. Finally, once you've started using these trends and data, you'll need to set up a system for updating and checking the data regularly to ensure that it accurately represents the current state of your equipment.
Accurate data is essential for implementing a successful predictive maintenance strategy. Another significant move is to choose the best framework for data analysis. With such a platform in place, the image of a mechanic dragging his toolbox into a breakdown with no idea what they'll find can be replaced by the appearance of a concentrated team following process instructions based on real-time data. Predictive maintenance reduces the amount of time spent searching for the source of a problem, making it a much more productive operation.
Benefits of predictive maintenance
Investing in predictive maintenance software would provide the organization with tangible benefits such as those mentioned below.
Reduce maintenance costs
Companies can save money if they can foresee and prevent equipment failure. Improving maintenance planning will save a lot of money in asset-intensive industries. Predictive maintenance based on IoT helps you systematically prepare the best care and inspection schedule to prevent unplanned downtime and wasted effort.
Reduce breakdown time
Every industry has a standard rate of machine failure, which is typically expressed as a percentage. Breakdown numbers can be minimized by implementing a more robust approach to equipment failure, saving money for the entire enterprise through improved productivity and retaining high-quality product performance.
Optimize productivity
Maintenance that is planned Reduce the amount of time and frequency at which critical equipment failures are repaired. The number of breakdowns decreases and factory conditions vastly improve, resulting in fewer worker injuries. Both of these elements contribute to increased efficiency.
Improve safety and compliance
Companies may anticipate and address potential safety threats and foresee potential problems with predictive asset maintenance until they affect staff. By analyzing data from multiple sources, including data provided by IoT devices and sensors, they may take appropriate action to reduce safety risks. You can detect potentially unsafe conditions and quantify their effects on working conditions by analyzing data over long periods. To Know more about crane maintenance click here.
Are you looking for the best laser shaft alignment service in UAE? Contact Technomax for Laser Shaft Alignment.
Condition Monitoring Services-Artificial intelligence can help oil and gas companies predict when their machines and equipment need maintenance. Oil and gas companies can repair these machines before their breakdowns result in lengthy downtime or employee injuries that can cost millions in legal fees and damages. All companies in this report claim to help oil and gas, energy, and utility companies with at least one of the following:
• Monitoring the condition of machine resources
• Predict the likelihood of future machine failures
• Make proactive maintenance decisions
• And, consequently, reduced operating costs resulting from catastrophic machine failures We began analyzing how energy companies can use artificial intelligence to predict when their machines will fail with condition monitoring.
Technomax offers its condition monitoring services, which claim to help oil and gas companies monitor their machine resources, predict future machine failures, and make proactive maintenance decisions using machine learning. Technomax states that various digital technologies and artificial intelligence drive the condition monitoring services.
The company says the machine learning model behind the software has been trained on more than 800 types of assets used in the energy, chemical, manufacturing, and mining industries, millions of components, and the thousand ways they can fail. The application can be applied on edge and in the cloud. The company says the client company's oil and gas experts should determine where to install the sensors on the cylinder. These sensors would then collect telemetry data from those parts of the cylinder, such as pressure. This data would then be used as a reference for a properly functioning cylinder.
Machine Learning in Predictive Maintenance
The machine learning model behind condition monitoring services would have to be trained on millions of these telemetry data points, and data on when certain parts of the cylinder require maintenance and how long it took to service those parts, and possibly how long take time Spare parts to get to the site. The data would then be executed using the software's machine learning algorithm.
This would train the algorithm to discern which of all these data points is related to parts of the cylinder that are in good working order, when the cylinder has needed maintenance in past, which of its features required repair. The software then predict when certain parts of the cylinder need care before breaking.
Technomax advised a team of engineers and asset management from the client, providing condition monitoring services in the United Arab Emirates. After a physical inspection of the tower, the resource management team discovered the problem as expected by the application. This early diagnosis allowed the team to repair the wind turbine at $ 5,000 and reduce downtime. This customer also reports that within about three months of using the Technomax software, the customer has generated high-value information from 10% of their turbines.
We offer condition monitoring services as a preventative maintenance application that helps in various sectors like oil and gas, aerospace, defense, financial services, healthcare, manufacturing, prioritizing equipment maintenance, maximizing uptime, improving worker safety, and reducing expenses using predictive analytics.
By implementing condition monitoring services in the UAE, we can integrate our software into enterprise databases. The model behind our software has been trained on historical fault data.
The user can then upload sensor data, supervisory control and data acquisition (SCADA) data, legacy data, and data such as technical notes and external data sources such as weather that are not tagged in the software.
The algorithm underlying our software system used in condition monitoring services would then be able to detect anomalies in assets and calculate the risk of failure score for each asset by analyzing the asset's operating conditions and performance data. The system estimates the probability of failure over different periods, such as 14 days, 30 days, or six months.
In Recent years TECHNOMAX Middle East Engineering LLC has become a world leader in providing condition monitoring services in Abu Dhabi, UAE.
The growth of the manufacturing sector in the past couple of decades have been commendable and overwhelming. With the development of population, global demand has increased leaps and bounds. Hence, intending to hit the nail on the head, the manufacturing sector expanded pervasively. The 90s witnessed another revolution with the advent of the internet. The terms "big data", "machine learning", "Internet of Things" have been sprinkled in most tech articles in the last couple of years. These emerging technologies have been significantly aiding to maintain overall production processes. However, all of them have a common denominator, that connects them all, which is known as Predictive Maintenance, reason why a proper Predictive Maintenance Plan is very crucial. The potential of this market is so huge . Studies show that the predictive maintenance market is said to grow to 6.3Billion by 2020.
What is Predictive Maintenance (PdM)?
Predictive Maintenance is a practice primarily directed towards Maintenance of overall health of machinery or equipment in a manufacturing unit. It is a proactive manoeuvre that is undertaken to predict if there is any faulty piece of the machinery which might stop working and thereby disrupt the entire manufacturing process. Predictive Maintenance is designed to assess the condition of the in-service equipment so that necessary maintenance steps can be taken to restore the same so that the day-to-day production process is not hampered. With the advances in telecommunications, Artificial Intelligence(AI), predictive Maintenance is getting its recognition which was long overdue.
Predictive Maintenance plan involves the analysis of asset metrics, that lead to savings of enormous maintenance expenses. The underlying idea of predictive Maintenance is to allow an efficient mechanism of corrective Maintenance so as to avoid unexpected equipment failure. This can consequently help in reducing accidents with negative environmental impact by increasing the safety measures of the overall plant.
Predictive Maintenance also helps in stretching the overall useful life of the machinery by predicting any fault or glitches in advance. It also helps in reducing unplanned downtime costs incurred due to some failure, which ultimately tampers the profits of the organization. It is more about predicting the future trend of the condition of the equipment. It studies various performance or maintenance data points to analyze the present health condition of the machine. Predictive Maintenance is incredibly helpful in estimating the future degradation probabilities of the machinery and optimizing the production capacity. Its huge benefits is what makes it very crucial to have a proper Predictive Maintenance Plan
Steps of Predictive Maintenance Plan
Predictive Maintenance is the buzzword among executives and business professionals. It is a cutting-edge maintenance strategy that needs to be adopted by the manufacturing industry at the earliest. Given below are specific steps of Predictive Maintenance Plan.
Determining the goal
It is necessary to have a clear and crisp definition of the scope of implementation of Predictive Maintenance in the business process. The company should know precisely why it is taking up the project of predictive Maintenance. The most prevalent glitch in these projects is that most companies are oblivious of the fact that what they want to predict. Hence, before transitioning into predictive Maintenance, it is necessary to determine precisely what is required to be expected. With different assets, the approach of predictive analysis is also different. So, having a clear goal is of utmost importance.
Data Quality
The next step of this maintenance manoeuvre is data analysis. Data should be of both historical nature and real-time data. The sources of such information must also be reliable like IoT devices, back-office systems etc. Data should be primarily about past performances, failures, maintenance history, current condition etc. Reliability and quality of data should also be taken into account.
Data Analysis and Conclusion
Once the data is collected, the analysis of the past and present performance of the asset will help in reaching conclusive insights about the health of the same. With today's technological advancements, processing of data has been automated in most cases and the system is able to predict the upcoming failures, which the asset is susceptible to encounter. This, in turn, helps in providing preventive measures to increase the efficiency of the purchase.
Creating a Plan
A road map needs to curate based on the data analysis of the previous step. It is advisable to create a list of all the part of the assets, where predictive Maintenance is intended.
Communication
It is not only the machines and technologies that do the necessary alterations and predict failures, but professionals also play a pivotal role. It is advisable to conduct meetings among the team members that are involved in machine maintenance and repairs so that communication becomes easy and straightforward. Suggestions and opinions can be exchanged regarding the health of the assets, manufacturing information, etc., which will help in creating a road map ahead with everyone onboard.
Condition Monitoring Program
At this step, the concept of condition monitoring becomes very important. Condition Monitoring or colloquially known as CM is the process of deciding upon a parameter of condition in machinery like vibration, temperature etc. and thereby monitor the same so as to identify a substantial change which is indicative of a developing pitfall in the machine. It is also advisable at this stage, to do a pilot study of a small piece of the plant so that nothing gets missed out.
Implementation
Once, the pilot study is successfully done, the next step is to implement the plan on the entire asset. The necessary course of action should be adopted, so as to ensure smooth implementation of the same.
Feedback
Predictive Maintenance is a continuous process. Hence a good Predictive Maintenance Plan should always have room for feedback and opinions. This will help in adjusting the task, routes, frequency and duration of activities.
Conclusion
It is necessary to have a reliable predictive maintenance plan to ensure the proper functioning of the machinery and equipment so that the production process is not disrupted and profitability does not get compromised.
Learn More About Our Services
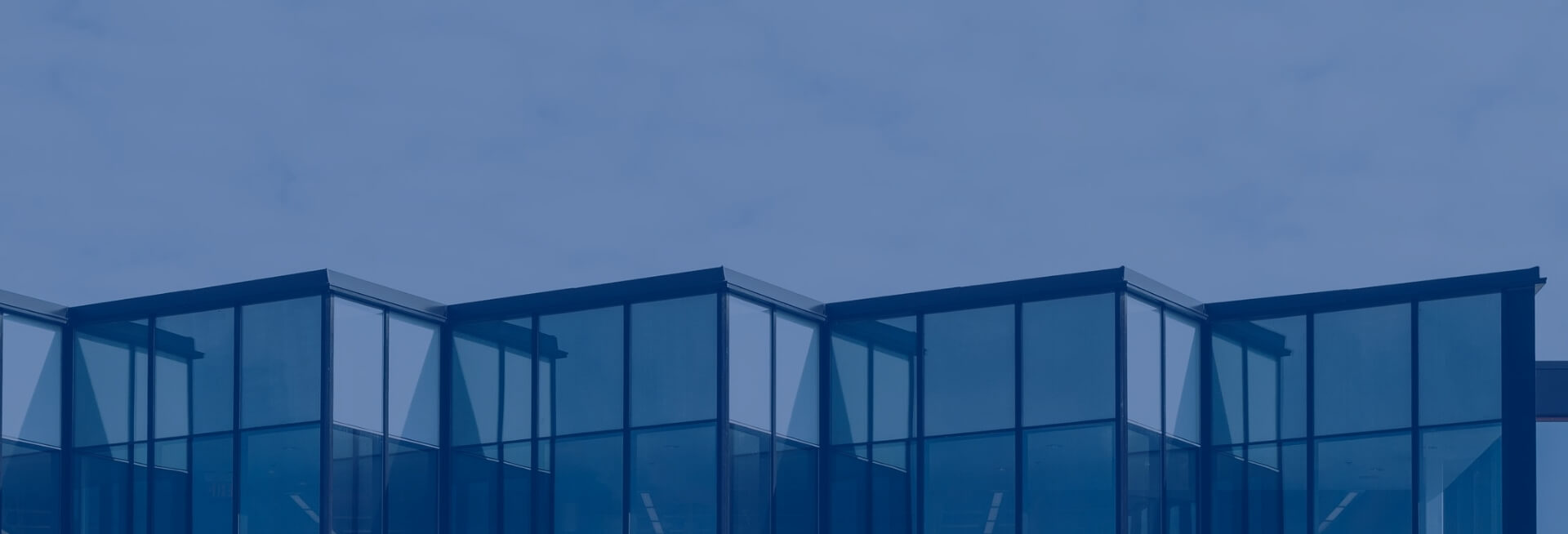
Get Started Now!
It takes less than a minute of your time. Or you may simply call +971 2 555 1 783