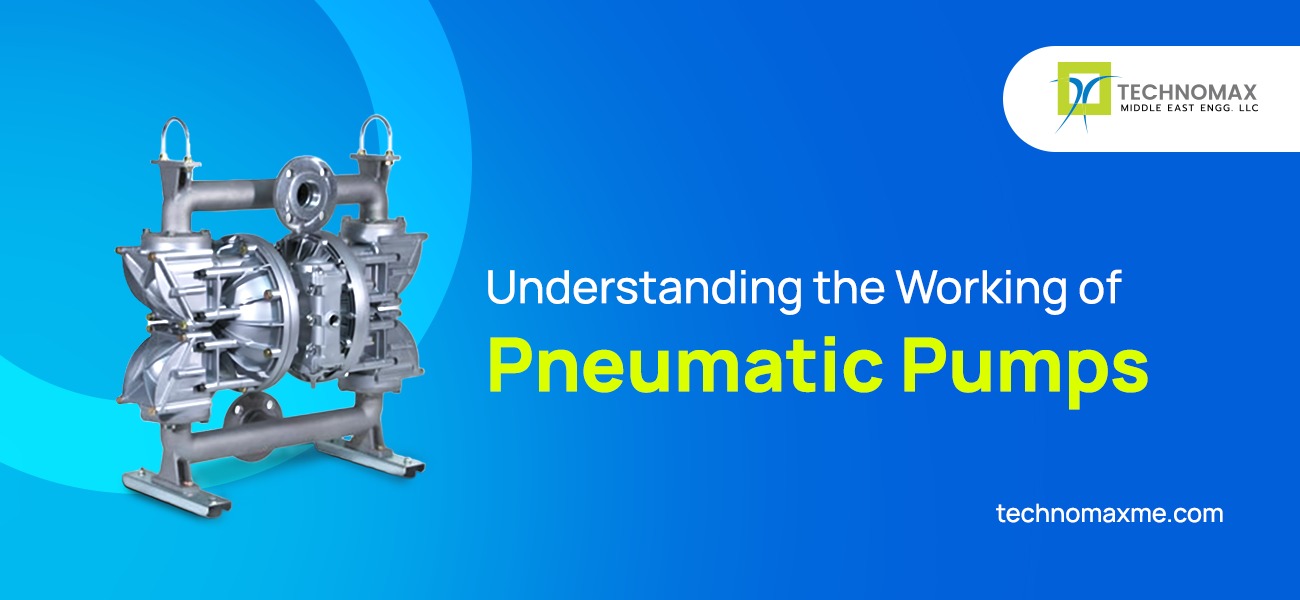
Pneumatic air pumps work by using pressurised air or gas to facilitate the motion of different media. A basic bicycle pump, pumps that aerate ponds and aquariums, vacuum pumps, vacuum cleaners, etc. are typical examples of pneumatic pumps that run on compressed air or compressed inert gases.
Pneumatic pumps are largely used across multiple industries and are available in different sizes. The pumps adopt a unique design that makes them perfect for transferring viscous products easily. In this blog, let’s explore more about pneumatic pumps and how they work.
Types of Pneumatic Pumps
Recognised for the role of positive displacement pumps, pneumatic pumps work as double-acting mechanisms with no return spring. They use different pressurised fluids or gases to operate. Among the various types of pneumatic pumps, let us get familiar with the most prevalent ones in the industry:
- Pneumatic Diaphragm Pumps: Powered by electric, pneumatic, hydraulic, or steam energy, they use a piston mechanism for media propagation along a cylindrical chamber.
- Pneumatic Liquid Pumps: Specifically designed to serve the purpose of liquid transportation.
- Pneumatic Refrigerant Pumps: They are two-stage pumps mainly used to transport refrigerant.
- Pneumatic Test Pumps: Engineered to assess the potential performance of a particular pneumatic system.
Being the top engineering company in UAE, Technomax offers air-operated diaphragm pumps that facilitate precise control of fluid flow across a range of systems.
With innovative pressure-driven flow control, we enhance the integration potential for exceptional performance in flow regulation that sets new standards for reliability and efficiency in fluid dynamics.
Enquire Now for Pneumatic Pump in UAE and MENA region
Overview of Pneumatic Systems: Components Used
Typical pneumatic systems involve using different components that serve well for general system control, i.e.; to regulate airflow and material movements. Pneumatic pumps rely on the principle of compressed air, used in small amounts to fuel small devices to transport and maintain air production consistently.
- Air Compressor: It generates compressed air that pressurises and gets supplied to the pneumatic pump.
- Pneumatic Pump Body: It includes fluid inlet, outlet ports, and components inside, that make fluid transfer smoother.
- Diaphragm/Piston: It works as the moving element that makes fluid displacement easier.
- Valves: They analyse the direction of fluid flow inside the pump, to make sure the fluid takes the expected direction.
How Do Pneumatic Pumps Work? Step by Step Process Breakdown
Pneumatic pumps utilise pressurised gas or air to move the medium. Pneumatic pumps are used for industrial applications with the help of compressed air or compressed inert gases.
These pumps use a double piston system in which one of the pistons has a smaller diameter than the other, and they get separated by an airtight chamber containing a liquid or compressed gas.
Compressed gas applies an external pressure to the piston with a large diameter, and then applies pressure to the intermediate chamber of gas/liquid. A smaller piston achieves amplified force, which then gets converted to strong mechanical action.
Here is the breakdown of the process flow of pneumatic pumps:
1. Compressed Air Input
Compressed air can be directed from the air compressor to the pump body via an air inlet port.
2. Diaphragm/Piston Movement
As the compressed air passes through the air chamber, it lets the piston/diaphragm circulate within the body of the pump.
3. Fluid Input
The movement of the piston or diaphragm builds a pressure difference in the pump, causing fluid to be driven in via the inlet port into the pump chamber.
4. Fluid Discharge
Moving the piston or diaphragm increases the exclusion of fluid from the pump chamber through the outlet port.
5. Valve Action
The role of valves is to regulate the fluid’s flow, confirm it moves in the preferred direction, and obstruct the backflow.
6. Continuous Flow
Fluid intake and discharge occur continuously as long as the compressed air supply remains active. This ensures the uninterrupted flow of the fluid.
Key Features That Make Pneumatic Pumps Stand Out
Different industries and applications rely on pneumatic systems to carry out essential operations. To ensure the long-term functionality of these systems, it is crucial to utilise the appropriate components designed for maintaining efficient operations.
- Reduced Energy Consumption
Well-known for minimising energy consumption, pneumatic pumps are great for their affordability and versatility, especially in applications like pressure sensors and backing systems.
- Flexible Diaphragm
Operating mainly on a diaphragm design, the air-driven fluid pumps leverage a flexible diaphragm that implements a back-and-forth motion, thus generating a pumping action.
- Self-priming capabilities
Pneumatic pumps have self-priming features that enable them to eliminate the air from the suction line, thus creating a vacuum to let the pump suck fluid from the source.
- Adaptability
The adaptability of these pumps extends to holding fluids with different viscosities, including those that contain abrasive materials and solid particles.
- Ease of maintenance
As pneumatic pumps are easy to install and maintain, they are widely adopted across various industries. They present the least complicated setup and reduce maintenance costs while upholding the standards of durability and serviceability.
Integral Applications of Pressure-driven Flow Control Technology
Pressure-driven flow control is suited to many applications, like sucking all types of sewage, chemical corrosive agents, mud, oil, toxic and flammable liquids, acids, alkali, abrasive liquids, and high-temperature liquids (up to 150°C).
Specifically engineered to fulfil the growing demands of oil and gas production, the pumps also serve well in the paper industry, water treatments, food processing, fertilisers and chemicals, the textile industry, the chemical industry, and the petrochemical industry.
Pneumatic pumps are highly prevalent in the automotive industry since they can be implemented in railway coaches, automobiles, printing presses, and waggons. Pneumatic systems are also useful in material handling equipment, metal-forming processes, and logic-controlling operations.
Pneumatic pumps cost comparatively less when compared to other positive displacement pumps, and they don’t need expensive controls or motors for their operation. They are versatile, reliable, and deliver a high cost-benefit ratio for companies compared to conventional technologies.
Advanced pneumatic pumps have a range of applications and the key industrial uses include:
- Droplet Generation: precision control to create uniform droplets in conducting microfluidic experiments;
- Alginate Bead Generation: Enabling the production of alginate beads that serve encapsulation and delivery systems;
- Emulsion Stability Studies: Necessary to analyse the emulsion stability in food, cosmetics, and pharmaceutical products.
- Dynamic Perfusion: The flow conditions are controlled to help with cell culture experiments and simulate physiological conditions.
Conclusion
Pneumatic pumps are used across various industries and take in compressed air to move fluids in multiple applications. The basic principle of building low-pressure areas with the dynamic movement of diaphragms and related components marks the effectiveness and versatility of pneumatic pumps.
They play a major role in facilitating fluid transfer and control across applications like oil & gas production, water treatment, chemical processing, automotive systems, etc. With self-priming capabilities, budget-friendliness, and adaptability to changes in viscosities, they are easy to maintain and offer top-notch efficiency and reliability.
Being a well-known provider of pneumatic pumps, Technomax supplies Yamada diaphragm pumps in the UAE and other parts of the Middle East. We deliver products compatible with advanced pneumatic pumping technology to ensure top performance, serviceability, and durability to meet the needs of diverse industries.
Learn More About Our Services
Recent Blogs
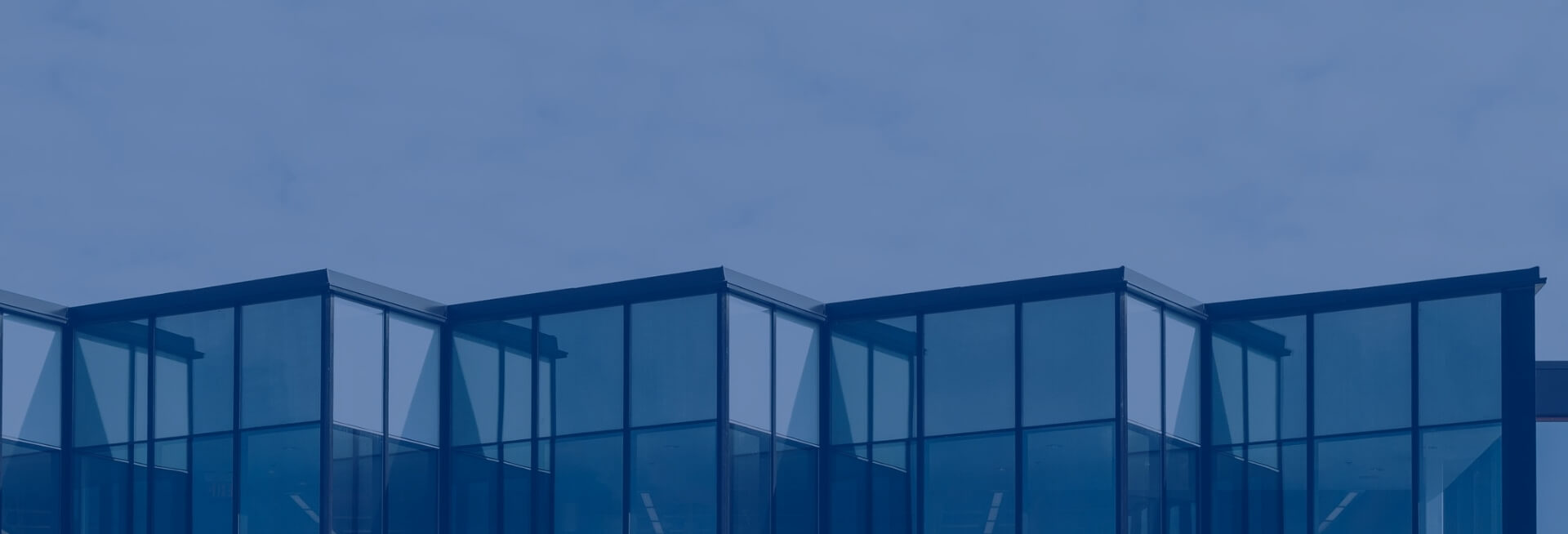
Get Started Now!
It takes less than a minute of your time. Or you may simply call +971 2 555 1 783