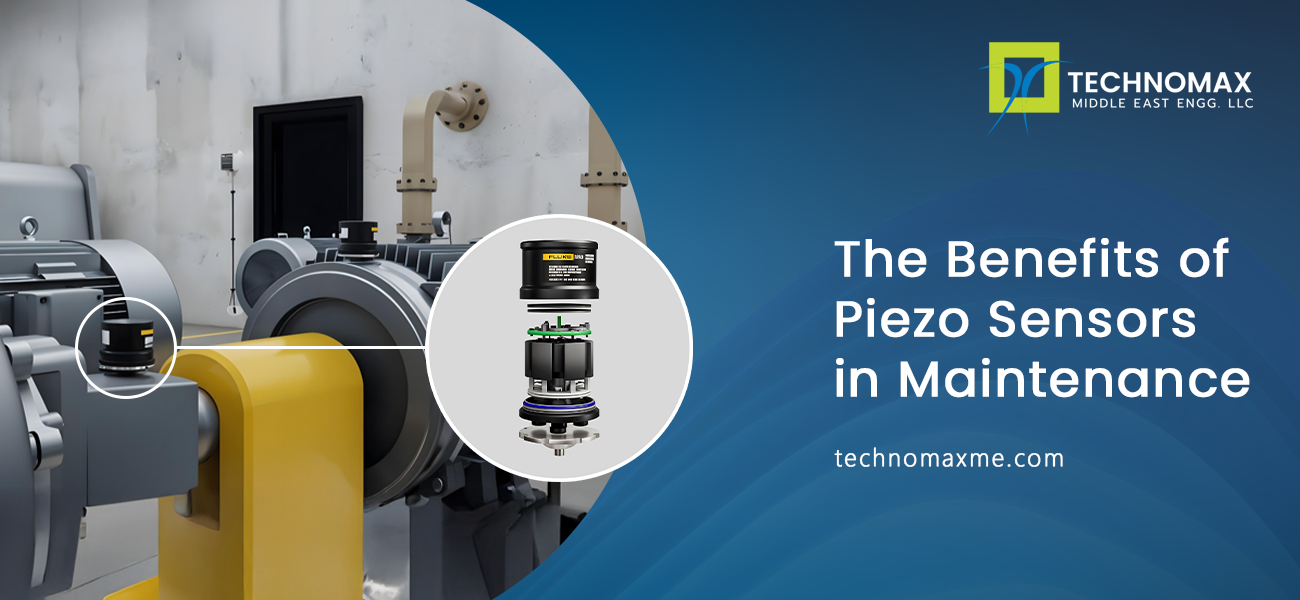
The Benefits of Piezo Sensors in Maintenance
Piezo sensors, or piezoelectric sensors are devices that utilise the piezoelectric effect to measure changes in pressure, acceleration, strain, force, or vibration by converting them into electrical signals. These sensors are widely used in industrial maintenance to monitor and diagnose equipment performance, ensure operational efficiency, and prevent breakdowns.
Industries demand equipment reliability and efficient maintenance strategies are critical to achieving optimal performance and minimising downtime.
One solution for this challenge is piezo sensors, an innovative tool at the core of vibration monitoring systems. These sensors enable timely intervention and prevent costly failures by providing real-time insights into equipment performance. These sensors are celebrated for monitoring vibrations, detecting abnormalities and enhancing safety across various industries.
In this blog, we will dive deep into understanding piezo sensors in detail and why they are so effective. We will also explore their technology, applications, and benefits and showcase their crucial role in industrial maintenance strategies.
Piezo Sensors and Their Role in Equipment Performance
Wear and tear is inevitable for industrial machinery operating in very challenging environments. Without the help of precise monitoring tools, even minor issues like misalignment or bearing wear can lead to critical breakdowns. There comes the usage of piezosensors. It's short for piezoelectric sensor, a device that measures changes in pressure, acceleration, temperature or force by converting them into an electrical charge.
These sensors are excellent at detecting even the slightest irregularities in equipment vibrations. Take a manufacturing plant where motors and conveyors are crucial elements of production as an example. A piezo sensor installed on a motor shaft can detect even subtle changes in vibration patterns, alerting the maintenance teams to potential failures. Addressing such issues early minimises disruptions, reduces repair costs and improves equipment longevity.
What is Piezoelectricity?
At the heart of piezo sensors lies the principle of piezoelectricity, derived from the Greek words piezein (to squeeze or press) and piezo (push). This phenomenon occurs in materials such as quartz crystals or ceramics, which generate an electric charge when subjected to mechanical stress.
Although it sounds quirky, piezoelectricity is surprisingly common in everyday life. For instance, it powers the ignition mechanism in gas lighters, where pressure on a crystal generates a spark. Similarly, in industrial settings, this principle is harnessed to convert mechanical vibrations into electrical signals, enabling precise equipment monitoring.
How Does a Piezo Sensor Work?
Piezo sensors are equipped with piezoelectric materials that can respond to external mechanical forces, including vibration, pressure or stain. The capacity to transform mechanical stress into electrical impulses makes them important in industries that require precise monitoring. Let us take a closer look at their operation.
-
Mechanical Input
The sensor detects external forces or mechanical stimuli such as vibration, stress or impact from equipment. For instance, in manufacturing plants, rotating machinery like compressors or turbines often undergo wear and tear. Vibrations caused by imbalance, misalignment or bearing issues are first picked up as mechanical inputs by piezo sensors.
-
Piezoelectric Response
Inside the sensor, piezoelectric materials like quartz or synthetic ceramics generate an electric charge proportional to the mechanical force applied. For example, when a pump starts vibrating due to cavitation (formation of vapour cavities in a liquid), the piezo material produces an electric signal reflecting the intensity and frequency of vibration.
-
Signal Processing
The electrical charge produced by piezoelectric material is weak and requires amplification. Built-in electronics process produces measurable and interpretable signals. For example, in Fluke’s vibration monitoring systems, this processed signal can be visualised in real-time on an intuitive dashboard. This visualisation allows engineers to spot anomalies and identify their root causes quickly.
-
Actionable Insights
The analysed data gives actionable insights that help predict maintenance needs assessing machinery health and ensuring operational safety. A practical example can be found in wind farms, where piezo sensors monitor turbine blade vibration levels. During vibration analysis, If anomalous vibrations are identified, then maintenance staff can respond quickly to avoid catastrophic failure, saving costs and reducing downtime.
Applications of Piezo Sensors Across Industries
The versatility of piezo sensors makes them indispensable in various sectors. Explore the multiple applications.
-
Manufacturing
Piezo sensors monitor machine tools, robotic arms, and assembly lines. In a car production factory, for example, piezo sensors help detect early symptoms of wear in welding robots. This allows manufacturers to schedule timely repairs, assuring consistent production quality and reducing downtime.
-
Energy
Power plants rely on piezo sensors to monitor turbines and generators, which are subject to high-speed rotation and stress. In hydroelectric plants, piezo sensors are used to monitor turbine vibration. Detecting imbalances early prevents potential energy production losses and costly repairs.
-
Automotive
Automakers use piezo sensors to evaluate the health of engines, drivetrains and suspension systems. For instance, during vehicle testing, piezo sensors monitor engine vibrations to identify any issues that might lead to inefficiencies and failures.
-
Aerospace
In aircraft, piezo sensors are crucial for monitoring jet engine components and detecting fatigue in airframes. For example, during routine maintenance of a commercial aeroplane, piezo sensors can detect microcracks caused by repetitive stress, ensuring that critical repairs are made before flights resume.
-
Oil and Gas
Drilling equipment and pipelines experience intense operational pressures. Piezo sensors help monitor vibrations in drill strings to detect imbalances or failures during deep-sea drilling operations. In pipelines, they monitor structural integrity, ensuring safe transportation of oil and gas.
The Benefits of Piezo Sensors in Maintenance
The adoption of piezo sensors in maintenance strategies brings numerous advantages:
-
Early Fault Detection
The subtle changes in vibration patterns that are undetectable to the human ear can be captured by piezo sensors. For example, detecting turbine imbalance in a power plant can prevent catastrophic failure.
-
Minimised Downtime
By addressing faults before they escalate, piezo sensors reduce unplanned downtime. It's a benefit in industries like oil and gas, where every second counts.
-
Cost Savings
Predictive maintenance powered by piezo sensors eliminates costly equipment repairs. A case in point is the energy sector, where piezo sensors in wind turbines can detect faults early, avoiding major overhauls that could cost millions.
-
Extended Equipment Lifespan
Regular monitoring ensures machinery operates within optimal parameters, reducing wear and prolonging life.
-
Improved Safety
Piezo sensors mitigate risks by detecting hazards early. For instance, identifying abnormal vibrations in a chemical processing reactor allows operators to prevent leaks or explosions.
Conclusion
Piezo sensors are transforming maintenance practices by providing precise, real-time insights into performance. From early fault detection to enhancing safety and efficiency, their benefits are unparalleled.
Heavy-duty industries, including manufacturing, energy and aerospace, cannot afford to ignore the benefits of these sensors. The ultimate purpose of these sensors is to ensure safety, reliability and efficiency.
Technomax, a leading engineering company in the UAE, offers customised solutions to utilise the power of piezo sensors. With advanced diagnostic tools and experienced technicians, we ensure the smooth performance of various electrical systems, like complex industrial installations. Take your next step towards better and smarter maintenance by connecting to Technomax and elevating your operations.
Learn More About Our Services
Recent Blogs
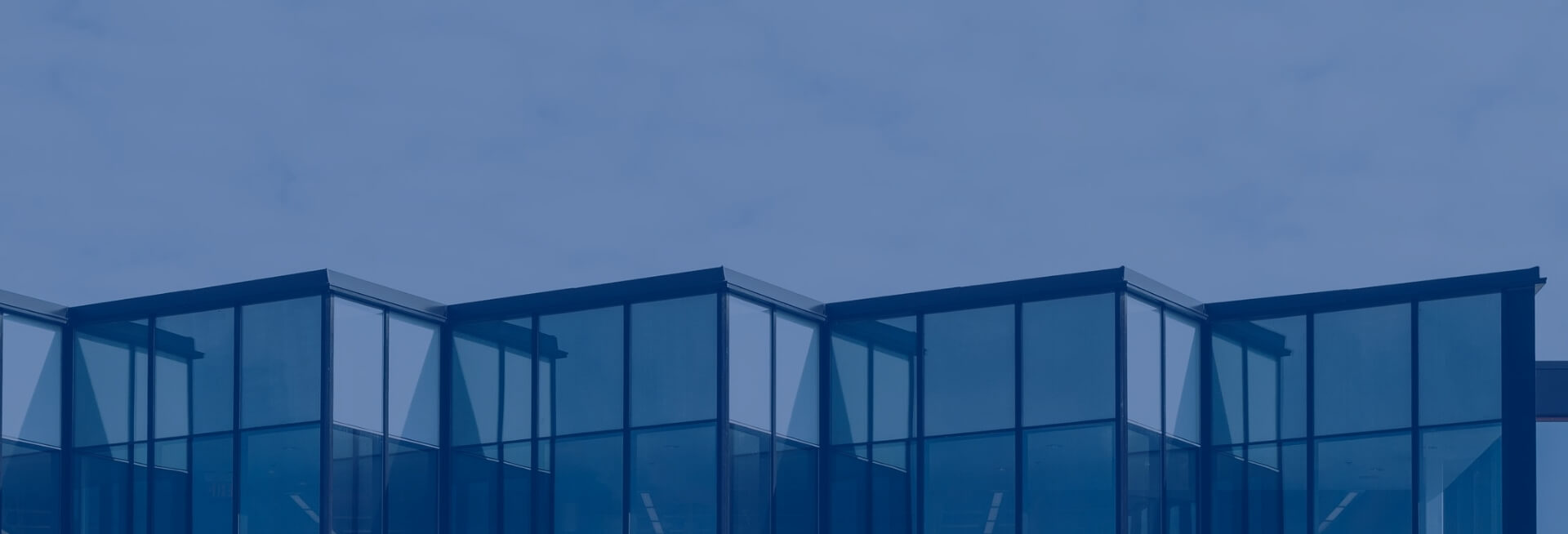
Get Started Now!
It takes less than a minute of your time. Or you may simply call +971 2 555 1 783