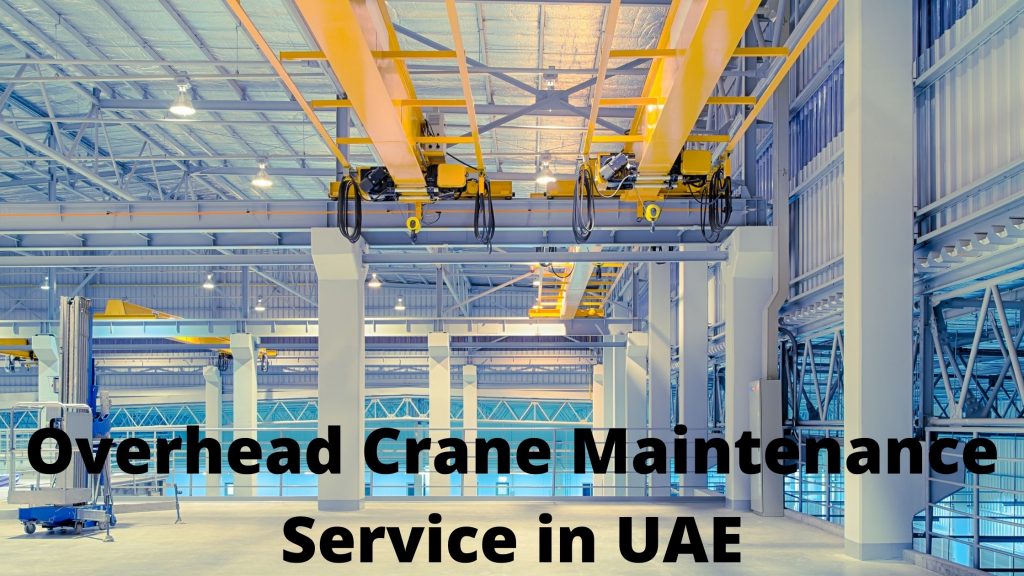
Overhead Crane Maintenance Service In UAE
Your overhead crane will need regular maintenance, just like a car or any other part of the machine, to increase its life and keep it running efficiently. Crane-related issues are something every machine owner should worry about, as buying a crane can be a significant investment, the investment you need to take care of. So it is about overhead crane maintenance service in UAE.
It is recommended that a regular inspection schedule be established for the crane. One must follow the manufacturer's advice for service and maintenance intervals and consider cycle and environmental factors when designing the crane to help extend the life of the crane and crane components. TECHNOMAX Middle East Engineering LLC provides comprehensive Overhead Crane Maintenance Service in UAE.
Common problems with overhead cranes:
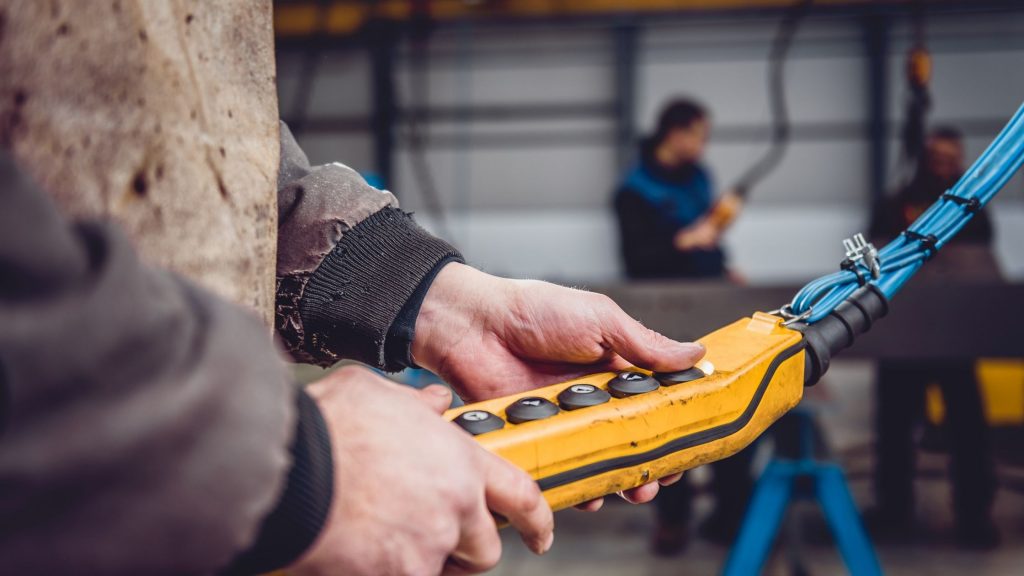
1. Damage to the Wire Rope:
Damage to the wire rope is considered a common problem that you may experience with an overhead crane. Several common wire rope problems like the wire rope may jump out of the reeving system, Reduction of rope diameter below nominal – loss of core support, internal or external corrosion, wear of outside wires, Broken or worn outside wires, Corroded or broken wires at end connections. Therefore, Overhead Crane needs Maintenance Services. Contact us to avail Overhead Crane Maintenance Service in UAE.
The best way to prevent the failure of a wire rope is to inspect it before each shift. If any evidence of damage is observed, the wire rope should not be used to prevent further usage. Also, make sure that the wire rope is adequately lubricated.
2. Crane Skew & Alignment problems:
The problem with a crane that is not working correctly is the overtime forces that didn't consider in the design and installation of the overhead crane can cause stresses to the runway beams.
These stresses can result in undesirable Accidents, Crane failure, Equipment downtime and productivity loss, cost repair, and parts replacement. Due to these problems, Technomax is specialised in providing Overhead Crane Maintenance Service in UAE.
3. Excessive Wear to End Truck Wheels:
End truck wheels are components of overhead cranes that can require time to time maintenance, replacement, or adjustment. Over time, the wheels will wear down due to everyday use of the crane and will need to be replaced.
The wheels can be made from various materials, including gantry crane, polyurethane, alloys and low carbon steel. The more carbon there is in the steel, the more complex the wheel will be. There are also heat treatment methods that can be used to increase the hardness of a wheel, increasing the durability and load capacity of the wheels.
If the wheels, bearings or wheel flanges begin to wear or break, it could indicate that the crane is leaning and not following the track properly. Tilting the crane can cause excessive wear and stress on the wheels and the rails and support structures. Overhead Crane Maintenance Service in UAE is yet another condition monitoring service provided by Technomax.
4. Issues with the Electrification System:
There are several problems with the electrification system of an overhead crane that may require service or future maintenance. One of the most frustrating problems that a crane operator can encounter is contacting interruptions between the conductor bars and collector.
In the collector, a carbon graphite brush can wear out, which can cause the accumulation of carbon graphite. Since carbon graphite powder is a conductive material, this build-up can cause short circuits in the electrical connection. Overhead Crane Maintenance Service in UAE provided by Technomax are considered one of the best in the entire UAE.
In older crane systems, the copper rails on the conductive bars can also rust or oxidize due to the operating environment or extended periods when the crane is not used. To prevent this from happening, conductor bars and manifolds should be inspected and cleaned regularly to ensure contact between the collector and the conductor bar is uninterrupted.
5. Bent or Damaged Hooks:
It is designed to hold a load in a specific and precise direction. When the weight is not directed as per the design, it compromises the creation of the hook and can increase the possibility of bending, stretching or breaking. The load can also slip off the hook if it extends from the throat opening. At the beginning of each shift, a regular inspection of the hooks and other fasteners should be performed to check for deformity or damage. We have solution for your every problem of Overhead Crane Maintenance Service in UAE.
While there are no clear guidelines on the use of hook latches, we train our employees and inspectors. We advise the end-user to evaluate the work activity concerning the safety of their employees. If the action makes using the lock impractical, unnecessary, or more dangerous, the end-user can choose to delete the lock. It is also recommended that each lifting activity be considered independently of the use of a hook lock.
Contact us for Overhead Crane Maintenance Service in UAE. Contact Us
Effective Overhead Crane Maintenance Practices
Proper maintenance of overhead cranes is vital for ensuring safety and prolonging the life of the equipment. Regular upkeep not only protects workers and assets but also maximizes the return on investment (ROI) by minimizing downtime and preventing costly breakdowns. The risks of accidents and injuries can be significantly reduced by implementing a structured maintenance program and that leads to a safer and more efficient work environment.
Here are some key practices for maintaining overhead cranes:
1. Conduct Regular Inspections
Routine inspections are essential for identifying potential issues before they escalate. Inspections can be categorized as daily, monthly, or annual, based on their scope:
-
Daily Inspections:
Operators should examine cranes before each shift for any signs of wear, damage, loose parts, or unusual noises. Testing critical safety devices such as emergency stop buttons and limit switches is also crucial. -
Monthly Inspections:
A more detailed assessment is conducted to check electrical connections, wire ropes, chains, and structural components for wear, damage, or deformities. Following a checklist and the manufacturer’s guidelines ensures thoroughness. -
Annual Inspections:
These comprehensive evaluations should be performed by certified professionals. They include an in-depth review of all crane components, such as brakes, hoists, load-bearing structures, and control systems.
2. Follow Manufacturer’s Recommendations
Every crane comes with a manual or maintenance guide specific to its design, usage, and duty cycle. Adhering to the manufacturer’s maintenance schedules, lubrication guidelines, and service intervals ensures optimal performance and reduces the likelihood of failures. This approach also safeguards warranties and extends the crane's lifespan.
3. Ensure Proper Lubrication and Cleaning
Regular lubrication of moving parts such as gears, bearings, sheaves, and wire ropes minimizes friction and reduces wear. Cleaning the crane frequently helps eliminate dirt, debris, and corrosive substances that could damage components over time. Using the recommended lubricants and cleaning agents is essential to prevent chemical reactions or incompatibility issues.
4. Account for the Operating Environment
The working environment can significantly impact the crane’s durability. Exposure to extreme temperatures, moisture, dust, chemicals, or steam can cause corrosion, oxidation, and other damage.
- Use protective coatings on metal components to combat harsh environmental conditions.
- Implement preventive measures during the crane’s design phase to address specific environmental challenges.
5. Prioritize Operator Training and Awareness
The effectiveness of a maintenance program depends on well-trained operators and maintenance personnel.
- Operators should be educated on safe operating practices, potential hazards, and the importance of regular inspections.
- Maintenance staff should be skilled in lubrication techniques, troubleshooting, and recognizing abnormalities.
Continuous training programs ensure that both operators and technicians are equipped to maintain the crane efficiently and address issues promptly.
The Future of Overhead Crane Maintenance
"Don't fix what isn't broken." For centuries, the idiom has been accepted wisdom. However, there was a time when it was also accepted wisdom that the Earth was flat. The problem with traditional knowledge is that views change over time, which sometimes necessitates a paradigm shift in our approach. It's no different in the world of overhead crane repair, where small and large shifts continue to influence how we perform our duties as well as the future of overhead crane maintenance. Any of these changes are relatively minor. On the other hand, others are radical improvements that transform everything we thought we learned about overhead crane maintenance on its head.
Increasing Automation
Automation, is one of the most prevalent phenomena currently sweeping the overhead crane industry hence it has significance in the future of overhead crane maintenance. While automation has been a constant presence in manufacturing for many years, recent technological advances have made overhead crane automation much more sophisticated. It's becoming more popular to see overhead cranes and hoists execute tasks entirely on their own, with limited guidance from a human operator, thanks to features including advanced computer controls, laser-guided sensors, and sophisticated object-avoidance systems.
This degree of complexity has had far-reaching consequences for the industry's maintenance. To fully comprehend and service the many highly complicated and technologically advanced elements of the modern overhead crane or hoist system, technicians have had to expand their expertise. Since automation is often used to increase a plant's efficiency, any downtime caused by a malfunction in one of these automated crane systems can have severe consequences. As a result, maintenance and repair technicians must quickly get the equipment back up and running.
Proactive Maintenance
Proactive maintenance is another trend that is having a significant effect on the future of overhead crane maintenance. As previously said, don’t fix what isn't broken." has long been a popular belief. However, when it comes to their devices, many overhead crane and hoist operators are starting to realise there is a weakness in that line of thought. The problem with waiting until something is broken before repairing it is that it causes downtime, which can be fatal to any company. When overhead crane or hoist equipment fails for some reason, hours, if not days, of work pile up and go unfinished. Any drop in productivity is a big issue for a company. Furthermore, waiting before a problem arises to fix it guarantees a loss of efficiency.
On the other hand, proactive maintenance works to resolve this issue so that overhead crane and hoist equipment can remain operational for as long as possible. Rather than waiting for equipment to fail before conducting maintenance, proactive maintenance aims to detect potential issues before they cause the equipment to fail and take it offline. This, like automation, has been made possible by using advanced technologies to track the condition of vital components and compile accurate data on how the equipment is used.
Based on this information, a maintenance service provider should create and execute a proactive maintenance plan that includes replacing worn components and resolving minor functionality issues before becoming more severe. What's the end result? Equipment remains online for more extended periods of time, increasing the productivity that owners and operators can expect.
Many people believe that overhead crane maintenance hasn't been broken in a long time. However, this side of the market is being fixed in a way that will help the entire trade even in the future of overhead crane maintenance, thanks to the efforts of forward-thinking producers and service providers. Click here to Know about Predictive Maintenance.