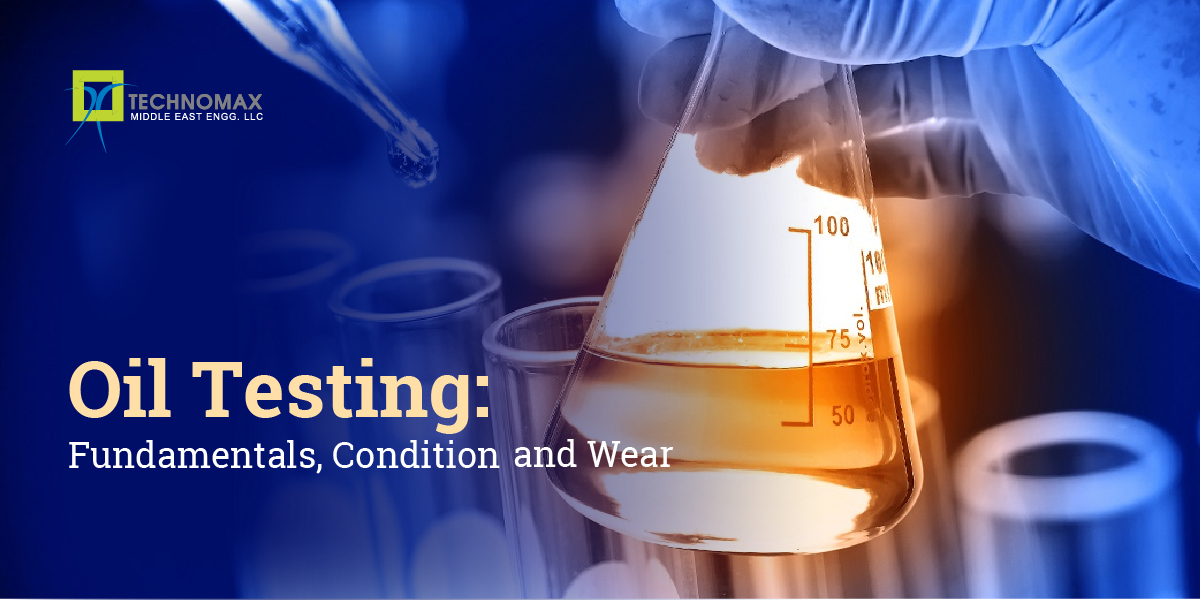
What is Oil Testing?
Oil testing may be defined as a systematic analysis of oil health, oil contamination, and wear at regular intervals. The purpose of oil testing is to validate the fact that a lubricated machine is operating according to expectations and predetermined standards. It can be seen as a routine predictive maintenance activity so as to furnish meaningful and accurate information on lubricant and overall condition monitoring of the machine. An obvious reason to perform oil testing is to understand the condition of the oil, but it is also intended to bring to light the condition of the machine from which the oil sample has been taken. By doing oil testing and sample results over the life of a particular machine, trends can be established, which can help eliminate costly repairs. The existence of any amount of debris and particles from worn parts, erosion, and contamination provides critical insights into the issues affecting the performance and reliability of the machine. Through oil analysis, one can schedule maintenance before a critical failure occurs, like crane operation failures, and thereby save substantial expenditure on the same.
Types of Oil Testing
There are three main categories of oil testing :
Fluid Properties
This type of oil testing focuses on identifying the oil's current physical and chemical state as well as defining its remaining useful life. It is a form of inspection of the constituents of the oil pertaining to the age and composition of the same, so as to deter the same from wearing out the machine and its useful life. It is a way of answering the following questions:
- Does the sample match the specified oil identification?
- Is it the correct oil to use?
- Are the right additives active?
- Have additives been depleted?
- Has the viscosity shifted from the expected viscosity? If so, why?
- What is the remaining useful life of the oil?
Contamination
This is a process of testing the quality of oil so as to identify the extent of purity and the contaminants(if any) that tend to reduce the useful life of the oil, leading to the erosion of the machine. By detecting the presence of destructive contaminants and narrowing down their probable sources, either external or internal, oil analysis can help answer questions such as :
- Is the oil clean?
- What types of contaminants are in the oil?
- Where are contaminants originating?
- Are there signs of other types of lubricants?
- Is there any sign of internal leakage?
Also read:
- How Do We Hydro Test In Oil And Gas Steel Pipeline?
- Offshore Oil and Gas Lubricant Condition Monitoring Services
- What are the Risks for Oil Rig Workers?
Wear Debris
Wear debris is arguably the most popular form of oil testing. It is primarily concerned with the determination of the presence and identification of particles produced as a result of mechanical wear, corrosion, or other machine surface degradation. It answers questions relating to wear and tier, which essentially include:
- Is the machine degrading abnormally, or is the rate of depreciation higher than expected?
- Is wear debris produced?
- From what internal component is the wear likely originating?
- What is the wear mode and cause?
- How severe is the wear condition?
Steps must be taken to keep the machine healthy and to extend the life of the oil. What oil testing is for the machine is essentially what blood analysis is for the human body. Hence, it is pertinent to do it as part of your regular condition monitoring schedule.
Rules for Oil Testing
With oil testing, careful oil samples are taken, and elaborate machine yields are considered for test results. Laboratory personnel interpret the data to the best of their ability, but without crucial details about the machine, a diagnosis or prognosis can be inaccurate. Some of these important details include:
- The machine's environmental conditions (extreme temperatures, high humidity, high vibration, etc.)
- The originating component (steam, turbine, pump, etc.) make, model, and oil type currently in use
- The permanent component ID and each ample port location
- Proper sampling procedures to confirm a consistent representative sample.
- The occurrence of oil changes or makeup oil added, as well as the quantity of makeup oil since the last oil change.
- Whether filter carts have been in use between oil samples.
- Total operating time on the sampled component since it was purchased or overhauled
- Total runtime on the oil since the last change.
- Any other unusual or noteworthy activity involving the machine that could influence changes to the lubricant.
Benefits of Oil Testing
The benefits of oil testing are primarily of two types
Maintenance Cost Savings
Oil mix-up is one of the most common lubrication problems contributing to machine failure. Putting the right lubricating oil in a machine is a simple task that can improve machine reliability. Checking the viscosity, brand, and grade of incoming oil and checking for contamination of alien fluids helps reduce the chances of oil mix-up and keeps the machines running at optimal efficiency. In order to keep the oil dry, clean, and free of contaminants, seals and filtration systems need to work properly, and oils should be checked regularly. Sand and dirt in oil cause abrasion. Moisture in oil causes corrosion. Fuel or coolant in engine oil changes viscosity and causes abrasion again. It is necessary to keep the lubricating oil clean and dry at all times. This, in turn, keeps the machine healthy and avoids any failure of the same, which consequently is known to reduce maintenance costs and unwanted repair charges.
Read more about - Laser Shaft Alignment
Increase Productivity
With a well-defined schedule for condition monitoring and preventive maintenance involving a thorough testing routine for oil contamination, one can ensure that the machine keeps working efficiently. This can then lead to a reduction in production losses due to any unwanted failure of the machine, as well as saving on manhours that could have gone to waste.
Conclusion
Oil testing provides for a healthier production process, contributing to seamless work access and increased productivity. Avoiding potential engine failures helps the production process to abstain from unwanted disruptions in production, and thus oil testing is of utmost importance for proper machine functioning.
Thus, it goes without saying that oil testing is an indispensable production exercise which needs to be undertaken without fail
Learn More About Our Services
Recent Blogs
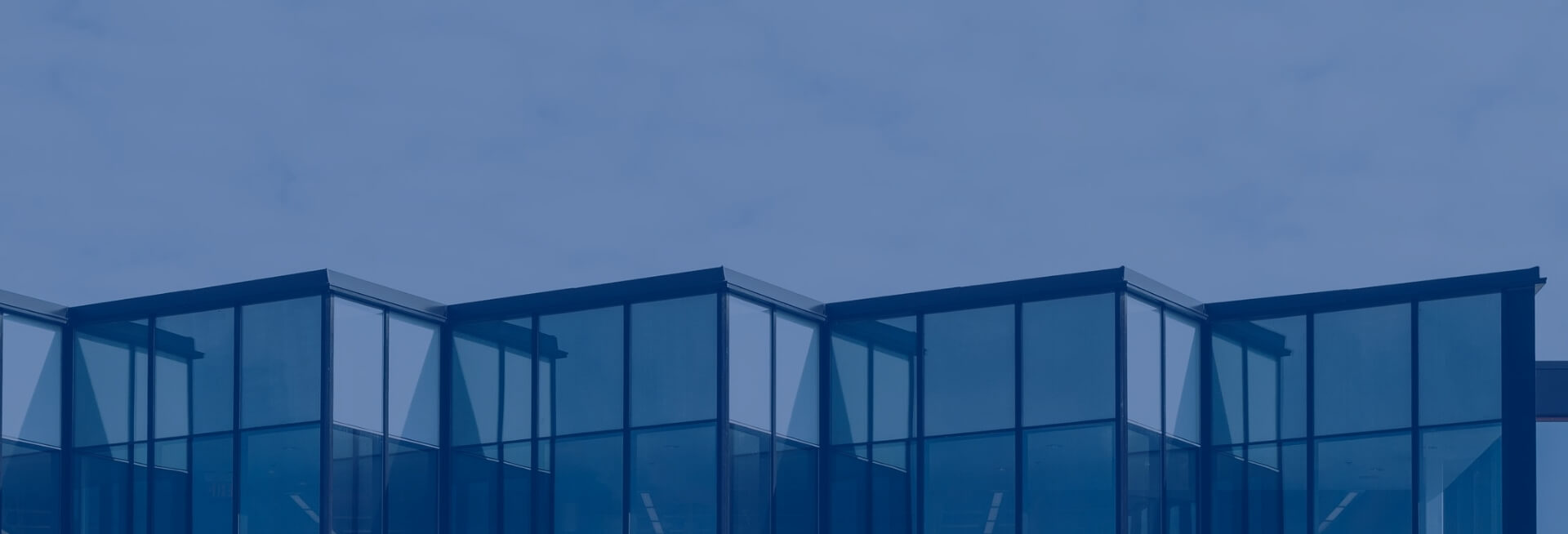
Get Started Now!
It takes less than a minute of your time. Or you may simply call +971 2 555 1 783