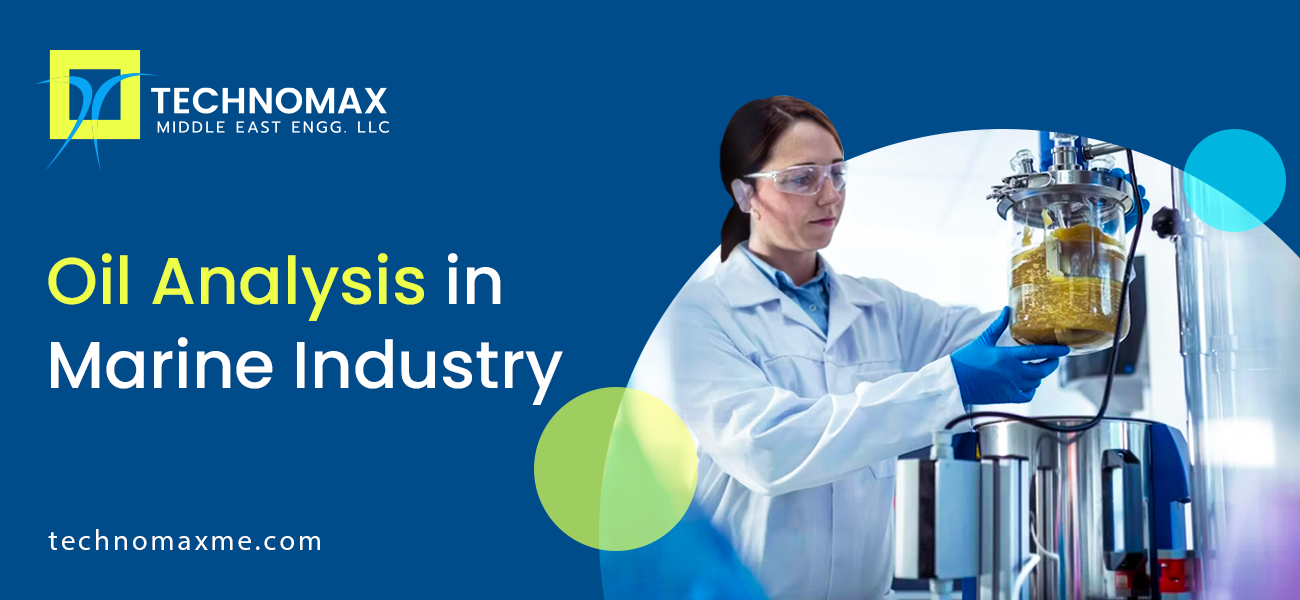
Oil Analysis in Marine Industry
Oil analysis in marine industry is a must-have regularly performing technique for monitoring operating problems of the equipment. This analysis helps you monitor the ideal condition of the machinery system and support the appropriate maintenance scheduling. This is also a perfect indicator before any problems which might develop in accordance with the oil health, level of contamination, wear, and tear of machinery, etc. This blog takes you into detail into the importance of lube oil analysis and the steps to consider while performing the oil analysis in Marine Industry.
You may also like to read:
- Offshore Oil and Gas Lubricant Condition Monitoring Services
- Oil Testing: Fundamentals, Condition, and Wear
Why Has Lube Oil Analysis in Marine Industry Become Important?
Oil analysis is the best procedure that helps you to detect the problems related to machinery. These can include lube oil degradation, abnormal wear, contamination due to toxic agents, and so on. All the aforementioned effects can cause possible machine failure or failure of the components. The failure can result in blackouts or loss of propulsion which brings consequential incidents like damage to third-party property, major collisions, groundings, and many more. The regular oil analysis helps you to adopt a proactive maintenance approach, ensure component durability, avoid early component failure, and trigger MTBO (Mean Time Between Overhauls).
As an economic impact, prevention of breakdown can help you save expenses on repair costs, loss of hire, downtime etc. thereby also promoting the safety of operations. The lube oil analysis results are unique for all mechanical systems and also can be checked against various manufacturers’ standards based on International regulations. These analyses determine if the key performance factors are confined to the operating ranges and thereby certify that the oil is fit for use.
In some cases, further investigation that involves additional analysis is required to ensure that the lube oil suits the mandatory fitness for usage. Modern hydraulic/lubricating oils are well-built to function under certain durations and specified conditions. Deviation from the suggested limitations can affect the major properties of the lube oil which results in poor performance.
Factors to Look For During Lube Analysis in Marine Industry
The testing of Lube oil samples takes place in specialized laboratories which tell the following features:
- Viscosity: The major part of lubricating oil that gives enough film thickness to maintain relative motion of the equipment parts.
- Closed flash point: It indicates the extent of oil contamination, dilution, or blowby of the engine fuel.
- Infrared spectroscopy: It defines the concentration of toxic insoluble solid particles like dirt, metal wear debris, combustion soot, oxidation materials, etc.
- Total Base Number or TBN: It measures the reserve alkalinity of lube oil and the capability to neutralize dangerous acids.
- Acid number: It depicts the acidity of the oil, and detects the potential to produce harmful deposits of equipment. It also indicates the presence of organic acids that oil oxidation generates.
- Oxidation level: This occurs during the aging process of oil with an IR test to evaluate the change in the lube's molecular structure.
- Water percentage: Defines the entire volume of water getting contaminated.
- PQ index: Measures the number of Iron particles contained.
- Asphaltenes: The presence of heavy components from the raw fuel ingress or even the combustion products that are blown by.
- Various metal levels in elemental analysis denote the wear and tear of equipment components. These metal levels include Aluminum, chlorides, chromium, copper, iron, lead, silver, manganese, tin, molybdenum, nickel, potassium, zinc, calcium, silicon, vanadium, etc.
Additional sampling and novel analyses could be needed in certain conditions where it is crucial to determine the suitability of some machinery for regular use. This is because taking off vessels from the service can make machine repairs costly. The delayed spare accessibility can cause owners to keep critical repairs away for a long time.
Important Keys To Effective Oil Analysis in Marine Industry
The following steps need to be adopted while an expert performs oil analysis for machinery or any equipment:
- Identify the equipment significant for your operational productivity:
Lubricants should be regularly monitored at least which means that all lubricants you utilize at the facility need to be tracked.
- In-Laboratory registration of equipment:
The registration helps the lab experts to conduct necessary tests to serve specific applications.
- Leverage appropriate sampling methods:
Improper sampling can create errors in the test results. The missed and untreated issues can result later in costly maintenance. The misdiagnosed state of conditions could result in irrelevant and unwanted money-wasting effects.
- Give complete and relevant information for the submitted sample:
Missing information could result in misdiagnosis. Fill in all the fields on the submission form, which include the components it can service, the lubricants in use, the number of hours oil is in use, etc. Additionally, make sure the information is legit to prevent misinterpretation.
- Submit samples for lab analysis:
Though the delays have no inherent effects on the sample, it improves the chances of contamination. The condition of the oil used in the equipment also could change with time. The more time that flows between when the sample is considered and when it is analyzed, the less alike is that the sample will find the fluid still passing in the machine. Hence, the results of the analysis have the least relevance.
- Appropriately Review and respond to test results
Review and analyze the documentation to ensure that they function well and determine if any further action is required.
- Conduct regular oil analysis
Oil analysis is to be performed regularly, not only when a problem occurs. As a part of the preventive maintenance technique, the regular oil analysis lays grounds for the lubricant's condition and the component where these are utilized. The periodical screenings, collection of data, and analysis over time help you to find trends and understand potential complications in the initial stages. This when corrected in prior, will avoid becoming big problems in the future.
In a Nutshell
Oil analysis has many benefits and applications as we've discussed in the above sections. Through regularly spaced lubricant testing, you may:
- Extend the life and reliability of the equipment through appropriate lubrication and detection of issues like wear, contamination, etc.
- The extent of the durability of lubricant through monitoring its condition., cleaning and treating it, and allowing it for longer periods between fluid changes are also necessary.
- You can also reduce the overall downtime of the equipment while spotting and correcting the possible lubrication issues, well before they turn into serious concerns.
Technomax is engaged in providing the best lube oil analysis in Marine Industry to customers with vital early signs of any possible problem and ensuring lubricant quality. The oil testing services help you validate the operation of the lubricated machine to ensure it works based on predetermined standards and industry expectations.
Learn More About Our Services
Recent Blogs
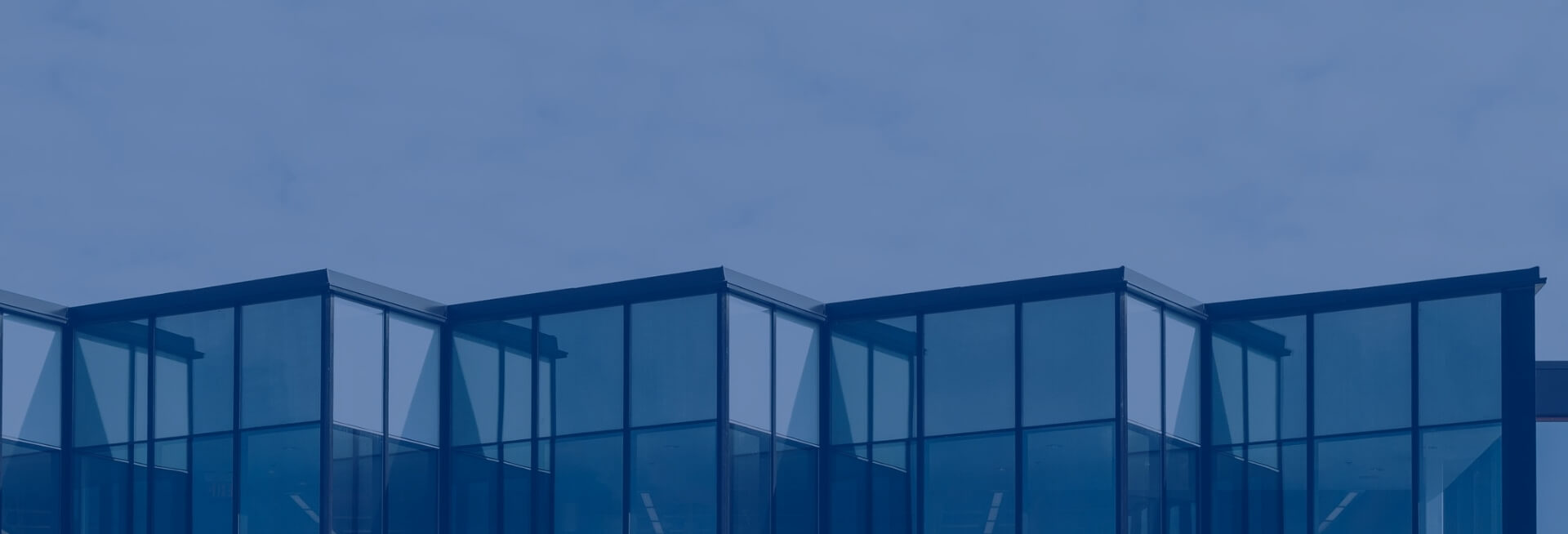
Get Started Now!
It takes less than a minute of your time. Or you may simply call +971 2 555 1 783