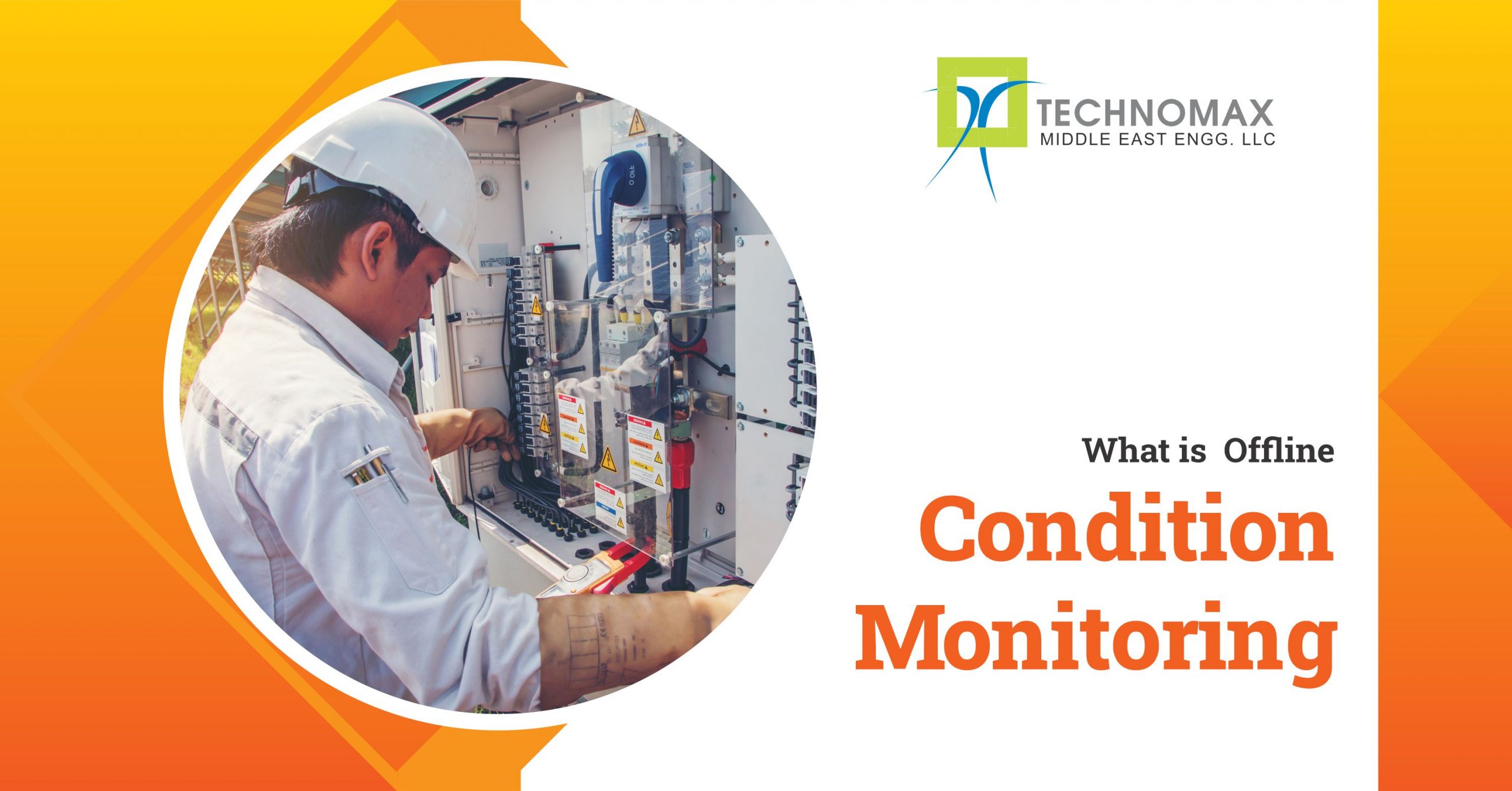
Introduction
Before knowing what is offline condition monitoring, let us know what conditioning monitoring is?
The measuring of specific equipment parameters and noting any significant changes that could indicate an impending failure is condition monitoring.
There are three types of condition monitoring: offline condition monitoring and online condition monitoring, and route-based condition monitoring.
Offline Condition Monitoring
For less critical or semi-critical assets where periodic scanning is good enough to observe the current condition, offline condition monitoring is generally used. Offline monitoring is commonly utilized with oil analysis when oil is sent to a laboratory for testing and with vibration analysis when a periodic check of the pulse will suffice for a less binding machine. Some organizations use sampling kits for testing certain oils' viscosity and water levels for immediate results with offline oil analysis. Semi-automated, in-house testing equipment is available to test for things like nitration, wear metals, oxidation, and additive depletion.
Other definitions of Offline Condition Monitoring
When managers and supervisors at a shop floor perform condition monitoring personally and some equipment, it is known as offline condition monitoring.
It is a tedious job for supervisors to use offline condition monitoring as no advanced technologies are used. Since diagnosis and fetching data take time may be up to five days, analyzing the data becomes more difficult. Unless managers and supervisors use some algorithms themselves, no prediction facility is available in offline condition monitoring. Also, as there is limited scope for sensor usability, data accuracy is challenging to maintain. For acquiring high power, accurate data, gigantic and costly computer systems are required. The whole process is expensive; thus, it is impossible for every organization to afford it and is usually used in some industries such as the nuclear power plant.
A Story About the Condition Monitoring
Keeping equipment running without failure became crucial as the cement industry evolved. And because the demand for cement increased, loss in production due to equipment failure was no longer affordable. Maintenance is costly and simultaneously time controllable expense in the cement industry. Reactive maintenance was the initial concept of equipment maintenance and scheduled, or preventive maintenance replaced reactive maintenance, which resulted in better equipment availability. Although preventive maintenance is very beneficial but unprecedented failures do occur even with scheduled preventive maintenance.
At present, the industry's focus is shifting from scheduled maintenance to the new technology of always observing machine conditions and predicting the situation in advance, and the process is predictive maintenance. The source of equipment abnormality is identified and corrected, which prevents failure in the future, known as reliability based maintenance. For preventing sudden failure, more concentration is focused on providing advanced warning signs of trouble. Also, condition monitoring through vibration monitoring and oil analysis is the latest maintenance technique for achieving higher equipment availability.
Through condition monitoring, Holcim has evolved in the last decade from preventive maintenance to reliability-centered maintenance. The center of maintenance activity at the Holcim Portland Plat in Florence, Colorado, is condition-based maintenance. The Plant in Colorado has been in operation since May 2002, and as part of the condition monitoring program, the Plant has installed online vibration monitoring systems on every critical equipment. Through PLC's, the online transducers are connected to the centralized control room, and the equipment has settings for alarm and shutdown in case of excessive vibration. An online surveillance system is another vibration monitoring tool utilized by the Plant that combines both continuous monitoring and Fast Fourier Transform analysis. The Plant consists of an offline condition monitoring route where data is collected manually by filed technicians and then analyzed. And this technical report presents information about the function of online and offline condition monitoring.
Conclusion
An offline condition monitoring system is even used by different organizations to collect data in a database for analysis and charting.
There are a few companies that have two views while investing in condition-based maintenance. A company in one situation prefers to invest money for increasing the number of resources and their competencies in having offline condition monitoring rather than having some online condition monitoring in more critical places in which safety factor is also essential.
However, other companies that do not have a specific organization and work with CBM tools and techniques work with small offline condition monitoring since a CBM is not always an advanced method, so a little offline condition monitoring is considered as CBM.
Know more about our Condition Monitoring Services.
Learn More About Our Services
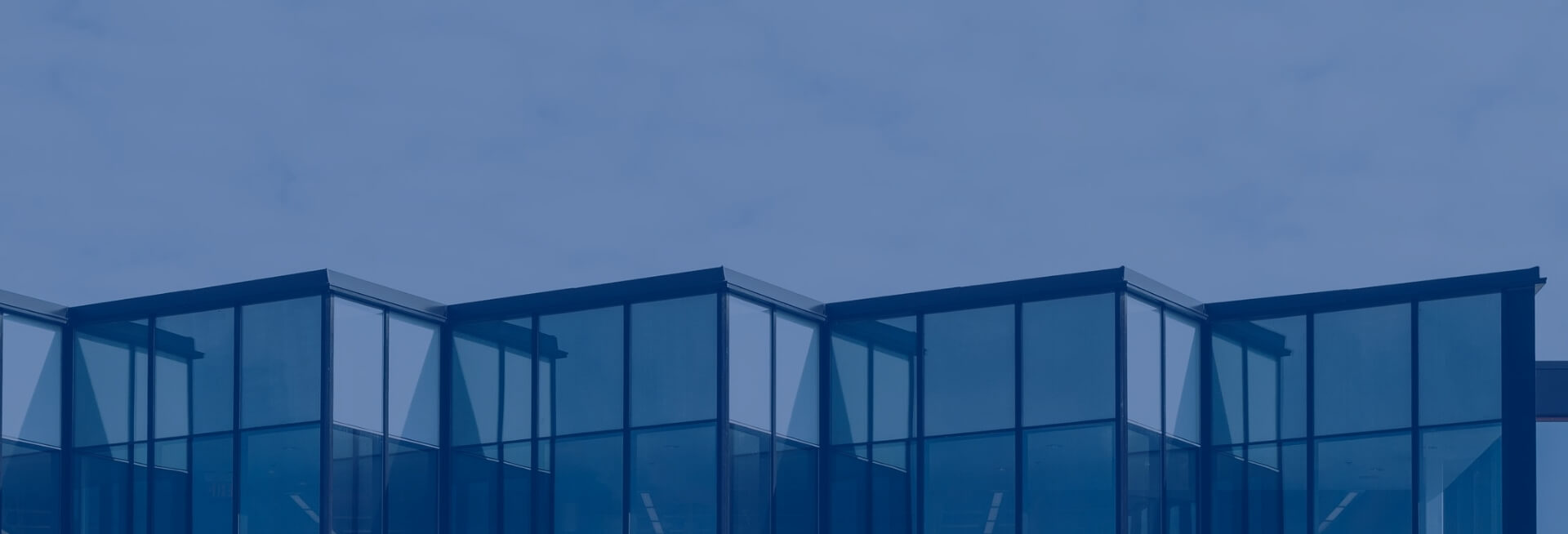
Get Started Now!
It takes less than a minute of your time. Or you may simply call +971 2 555 1 783