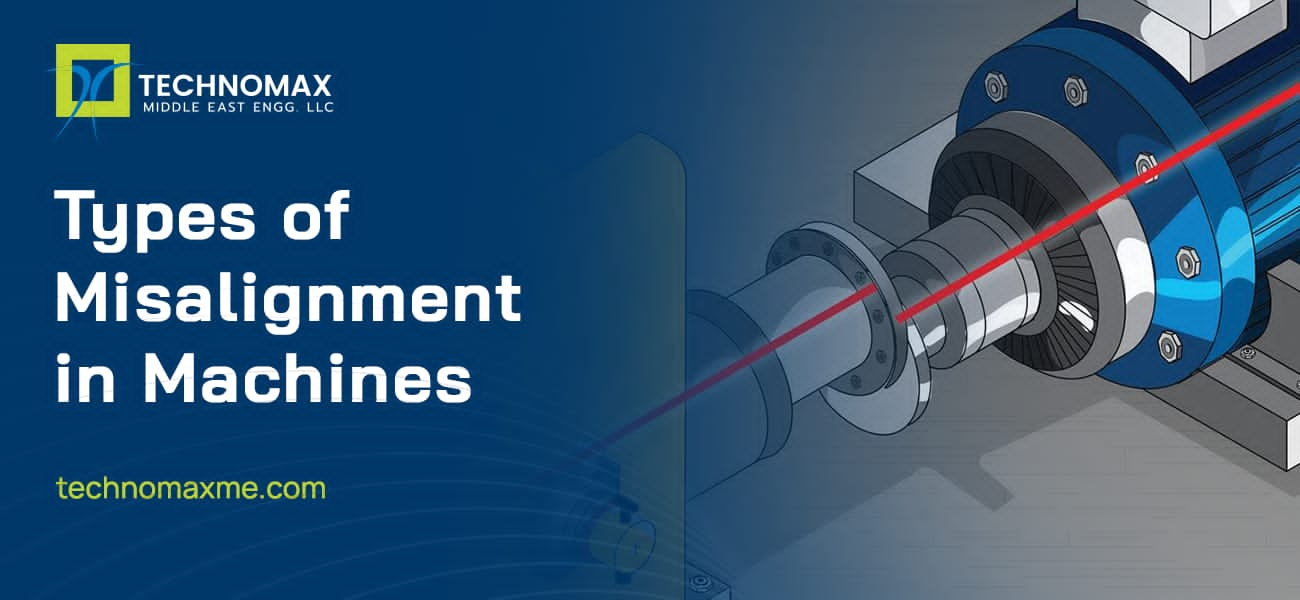
Misalignment in the machine causes various reasons, When any deviation of the shaft position occurs concerning the axis rotation, it leads the equipment to stop working, and it causes misalignment in the machine.
Many factors contribute to misalignments in the installation of couplings. In most cases, shaft misalignments produce vibration noise.
In this blog, let's distinguish the types of misalignments and understand the possible consequences in the absence of proper coupling alignment.
You may also like to read about:
- Preventive Maintenance Using Vibration Analysis in Electric Induction Motors
- Rotodynamic Analysis Services from Technomax
- The Influence of Lubrication, Vibration Infrared Analysis Results
Types Of Misalignment
Shaft alignment or coupling alignment is a process to arrange multiple rotating shafts in a collinear line, i.e., with their centers falling on the same line.
Now you might wonder what are the common types of misalignment. The principal causes of misalignment between the shafts are:
- Seal failure
- Bearing damage
- High vibration and noise
- More power consumption and less performance
- Excessive heat
How Does Misalignment Happen?
Misalignments result from two rotating shafts not falling parallel to each other, either through an angled gap or a moderately offset gap at the coupling.
But, in real life, when these both occur together, it causes compound misalignment. There are many reasons for misalignment to occur:
- Pipe strain
- Human-made error
- Thermal expansion
- Wear that causes sheave deformation
The irregular settlement of the base plate forms a soft footing that causes incorrect component assembly, generally for motors and pumps.
The key point to note is that the unsteady movement or motion to the shaft centerline which moves against the ideal motion of the machine can create stress in bearings and couplings.
This also creates damage to the seals, which needs quick repair.
Recognizing 5 Common Types of Misalignment
- Parallel Misalignment
This happens when two sheaves or shafts slip out of the parallel plane. It means the centrelines can be parallel, but keep the actual centreline offset. So sheave alignment is important here
- Horizontal Angle Misalignment
This takes place when the angle of a shaft differs from the angle of the next shaft along a horizontal plane.
- Vertical Angle Misalignment
It happens when the angle of a shaft varies from the angle of other shafts across a vertical plane.
- Horizontal angled and offset misalignment
In this compound misalignment, one shaft offers both offset and differently angled views compared to the other shaft placed horizontally.
- Vertical angled and offset misalignment
This compound misalignment occurs at a varied angle when compared to the other shafts alongside a vertical plane.
How to Detect Misalignment Issues?
While it is necessary to identify the root causes of misalignment and the methods in which they occur, the most vital factor to know is recognizing misalignment before it can minimize the life of seals, shafts, bearings, and couplings.
Precision-aligned equipment runs more efficiently and is durable. Hence misalignment detection is often considered a part of preventive maintenance instead of a reactive outcome.
Here are five methods you can use primarily to implement common misalignment detection:
This application is popular for its characteristics to detect misalignment in the machine, particularly in belt drive projects.
The ideal indication of misalignment is an improvement in friction in terms of the offset or angular shafts.
These are likely pulling apart one another and can cause a rise in machine temperature in the affected area.
Using the thermal-imagery technique helps to measure the hot spots, and analyze the source of the problem.
Thermography is an indicator to denote the rise in temperature damage caused mechanically.
Vibration analysis is best at monitoring the micro-vibrations of a machine and understanding when it reaches or exceeds the desired parameters.
These small observations performed proactively, just like thermography, help to recognize a concern with the misalignment.
It further stops this well before the belts and bearings wear down to catastrophic levels.
The increase in the variable of micro-vibrations in terms of degree and complexity also results in outcomes more than imbalance, misalignment, and looseness with time.
Accelerometers can help to conduct and correct sampling to make expected failure mode predictions.
The key aspect of the technique is phase analysis which diagnoses and specifies the kind of misalignment.
These tools together help analysts to know what causes the disruption and the methods to prevent it from escalating.
This is one of the comparatively complicated measures for detecting common misalignment issues.
In this process, the analyst can measure the misalignment with general wear and tear and contaminants in the machine oil.
While specialists conduct an appropriate oil analysis, the outcomes can't be that effective for preventative maintenance in misalignment.
- Laser Shaft Analysis
Compared to the most common types of misalignment checks, laser shaft analysis can give you a perfect calculation.
It measures the degree to which the coupling can be offset and lets the accurate measure of remedy get on an even plane.
With the experience and training of the operator, you can obtain great results in precision laser alignment.
This method is the easiest among the user interfaces to perform visual diagnosis of misalignments.
It also helps to visually understand the root cause of the misalignment.
You don’t have to be an expert or an engineer to view the video of motion amplification to see if there is a misalignment.
How to Correct Misalignment Issues?
The hardest aspect of misalignment is understanding where it exists and the extent to which it exists.
Solutions to misalignment can range from simple to complex.
Mostly, this could be to replace couplings, belts, and bearings.
This should be done to maintain the pieces in good enough shape— hence you need a slight alignment correction or a soft-footed correction.
If misalignment occurs too long unnoticed, this could be because the machine is under repair.
On the contrary, preventive maintenance and the scheduled analysis of misalignments can help you confirm longevity, trigger energy efficiency, maximize output, and save money to mitigate problems before they end up beyond repair.
Read more about:
- Why Do Steam Traps Fail: Causes, Factors & Preventive Methods
- Equipment Performance Monitoring – Our Approach
- Oil Analysis in Marine Industry
The growing importance of having the right coupling alignment
Appropriate alignment reduces failures in bearings, shafts, and coupling, the bearing and coupling temperature, energy consumption, and vibrations.
Additionally, great alignment can extend the life of the equipment between scheduled maintenance intervals.
Appropriate alignment not only prevents equipment failure but also offers the additional benefits as follows:
-Operate under lower bearing temperature
-Minimized vibration levels
-Extended equipment life
-Extended maintenance intervals
Misalignment Detection and Correction from Technomax
Laser Shaft alignment is an ideal technique leveraged during the installation and maintenance of rotating equipment. Using a high-precision laser shaft alignment tool combined with the dual position detector can replace the conventional way of measurement making it more accurate.
Being the leading engineering company in UAE, Technomax understands the demands of high precision and unique measurement instruments with calculation capacity and implements laser shaft alignment services to ensure the uninterrupted working of the machines.
Technomax also focuses on vibration analysis, oil analysis, laser shaft analysis, motion amplification, and other techniques to positively cater to the durability of industrial machinery/equipment.
Learn More About Our Services
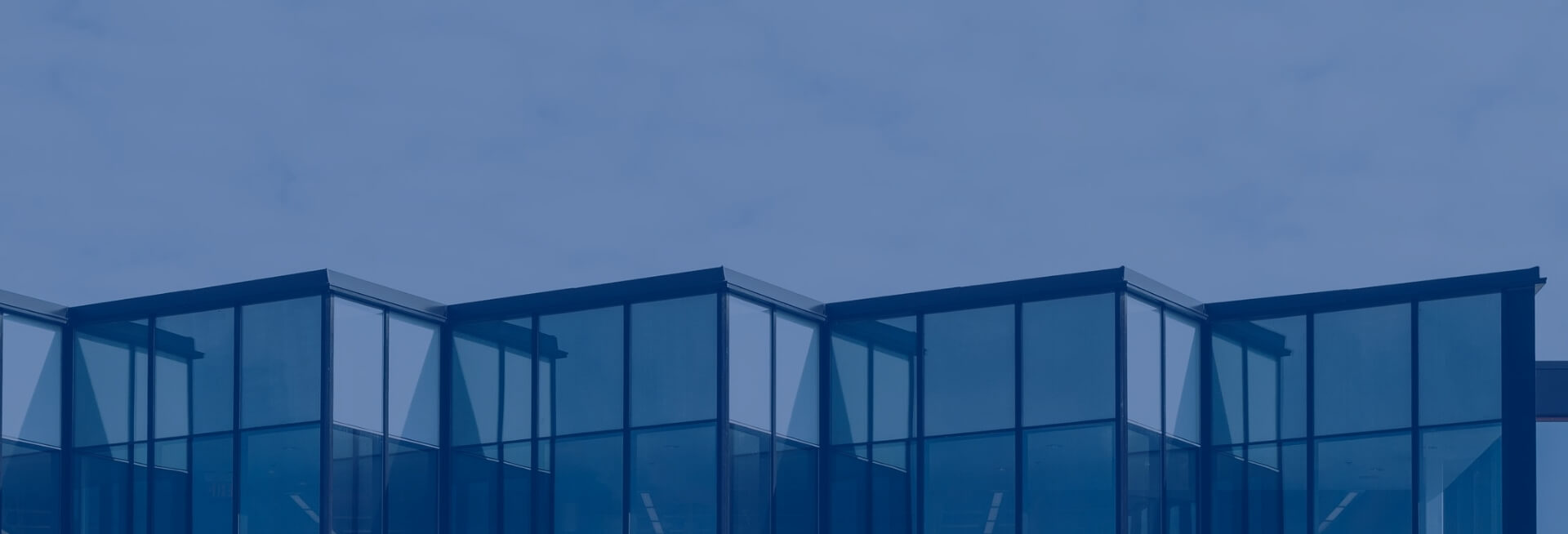
Get Started Now!
It takes less than a minute of your time. Or you may simply call +971 2 555 1 783