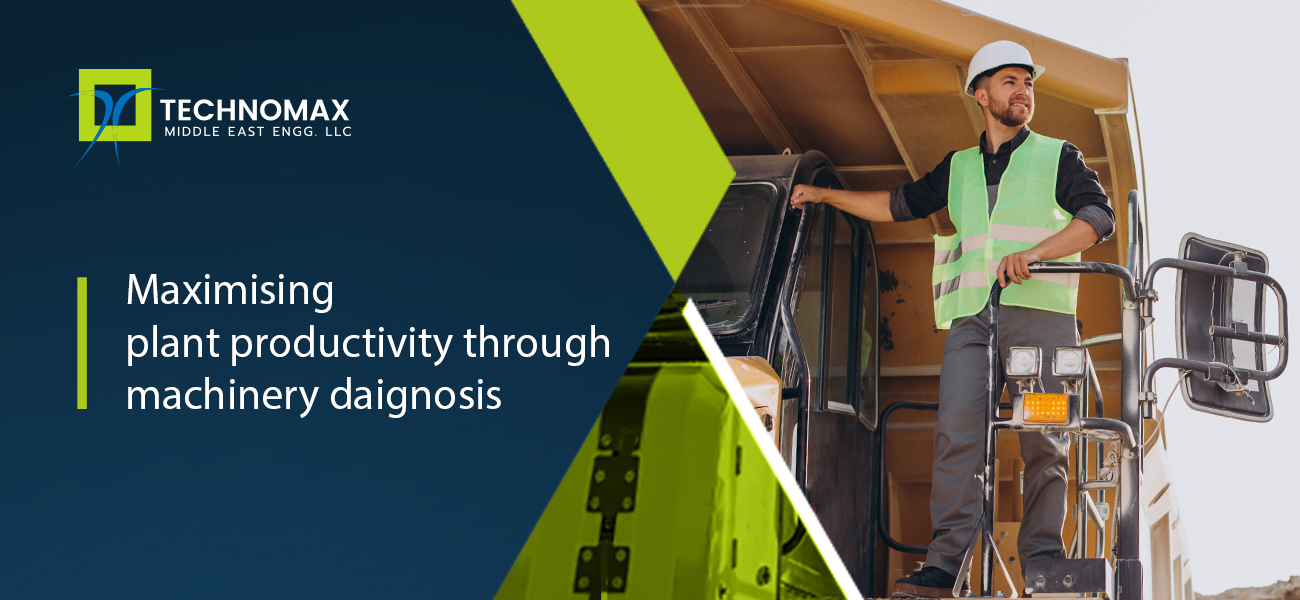
Maximising Plant Productivity Through Machinery Diagnosis
Digitally Forecast and Enhance
Software for plant simulation aids operations in identifying and resolving bottlenecks and takes some of the guessings out of plant design. This tool provides an overview of the entire operation's efficiency in order to optimise operations and identify improvement opportunities. These programmes evaluate dozens of distinct pieces of industrial equipment, including crushers, vibrating screens, washers, and conveyors.
In addition to equipment, the systems employ scientific methodologies to monitor the input, output, and waste heaps of the operation. OEMs utilise plant simulation software to create plant flow diagrams by estimating mass and volumetric flow rates using machine-specific operational parameters while considering machine placement. The programme is also perfect for performing product pre-calculations when goods or production rates change, including dry and wet crushing, screening, and sorting processes.
There are numerous brands of plant simulation software, but few are produced by equipment manufacturers. Undoubtedly, software functionality is a crucial factor, but possibly even more critical is a thorough comprehension of the equipment and process that the software is intended to optimise. Choosing equipment manufacturer-programmed software enables the most accurate simulations and increased functionality based on real-world application experience. Software that integrates on-site training increases the program's effectiveness.
Read more about:
- Keeping it on the rails: The Importance of Overhead Crane Runway/Rail Inspections
- Electrical Preventive Maintenance and Scalable Services
- The Influence of Lubrication, Vibration Infrared Analysis Results
Understand The Core of Your Operation
The vibration analysis technique for vibrating screens, the core of each processing operation, is another advanced diagnostic tool. Screening equipment is where the money is made, whereas crushing equipment is where the majority of the investment goes. Therefore, it is essential that vibrating screens operate as efficiently as possible.
Advanced vibration analysis systems enable users to evaluate the condition of a vibrating screen and detect anomalies that are not evident to the naked eye.This could be a hairline fracture in a side plate or a twisting of a side plate that could compromise its durability.
The ability to identify and address these issues early can result in substantial savings in terms of downtime and repair costs by preventing a domino effect of damage caused by the first problem. A defective spring creating abnormalities on a vibrating screen, for instance, may not be immediately visible during regular operation, but if left unrepaired, it could lead to substantial costs.
In a recent instance, a manufacturer in British Columbia employed vibration analysis, and the data showed a problem. This led to the discovery of a broken spring and foundational damage to the vibrating screen, but the producer saved money by identifying and repairing the issue quickly.
Vibration analysis also permits producers to optimise the operation of their equipment by fine-tuning. Although the concept began with wired sensors, current versions contain eight wireless tri-axial sensors that are attached to crucial locations on a vibrating screen.
These systems can measure orbit, acceleration, deviations, and other significant data points that indicate the condition of the machine. The captured data is transmitted through Wi-Fi to a tablet, allowing users to maintain a safe distance during the process.
The data can also be transmitted to an internet dashboard for storage, allowing operations to access past data and monitor machine performance. Some manufacturers offer to have their engineers analyse the data and provide technical insight and recommendations without the requirement for an on-site visit. Then, if necessary, on-site inspections can be planned for further evaluation.
Practical Approach to Maximise Plant Productivity Through Machinery Diagnosis
In conjunction with a hands-on approach, plant simulation software and vibration analysis are appropriate for setup, optimization, and problem identification.
Service programmes that include total site visits by seasoned OEM staff are vital for determining the optimal solutions for a business. Some manufacturers provide extensive inspections of vibrating screens and screen media, followed by detailed reports highlighting areas for efficiency enhancement. These can be supplemented by diagnostic services like vibration analysis and plant simulation.
This programme can increase service intervals, improve the performance of vibrating screens and peripheral equipment, and save money for operations. It is possible to conduct inspections while equipment is operating so that they do not disrupt the flow of activities. Following this, the OEM can make recommendations supported by knowledge.
For instance, production problems caused by blinding and pegging could be resolved by switching to a different type of screen media or by blending media based on its placement on the deck. To increase durability, polyurethane wear liners are an alternative.
Using this technique, it may be possible to identify general maintenance issues that, if left unresolved, would incur substantially higher costs in the future. Regular OEM inspections help guarantee that operations continue to run as efficiently as possible.
Talk to the OEM about warranty packages that include biannual site visits, equipment inspections, vibration analyses, and screen media assessments and suggestions when searching for new equipment. Some manufacturers provide warranties of up to three years.
Utilize Emerging Technology
To maximise uptime and keep up with infrastructure demands, producers must utilise the most recent technologies; otherwise, they need to catch up.
Innovations such as simulation software and vibration analysis make it simple to collect the necessary data to remain competitive. Combined with evaluations and recommendations from a knowledgeable manufacturer, this results in increased uptime and profitability.
Learn More About Our Services
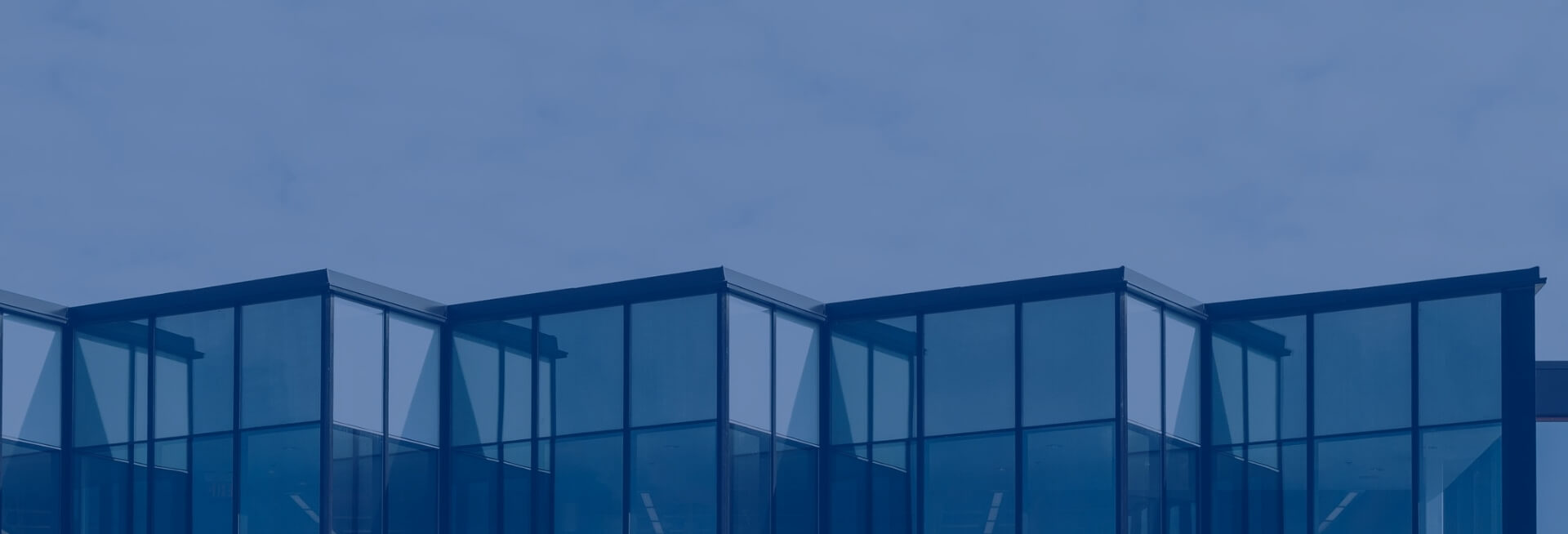
Get Started Now!
It takes less than a minute of your time. Or you may simply call +971 2 555 1 783