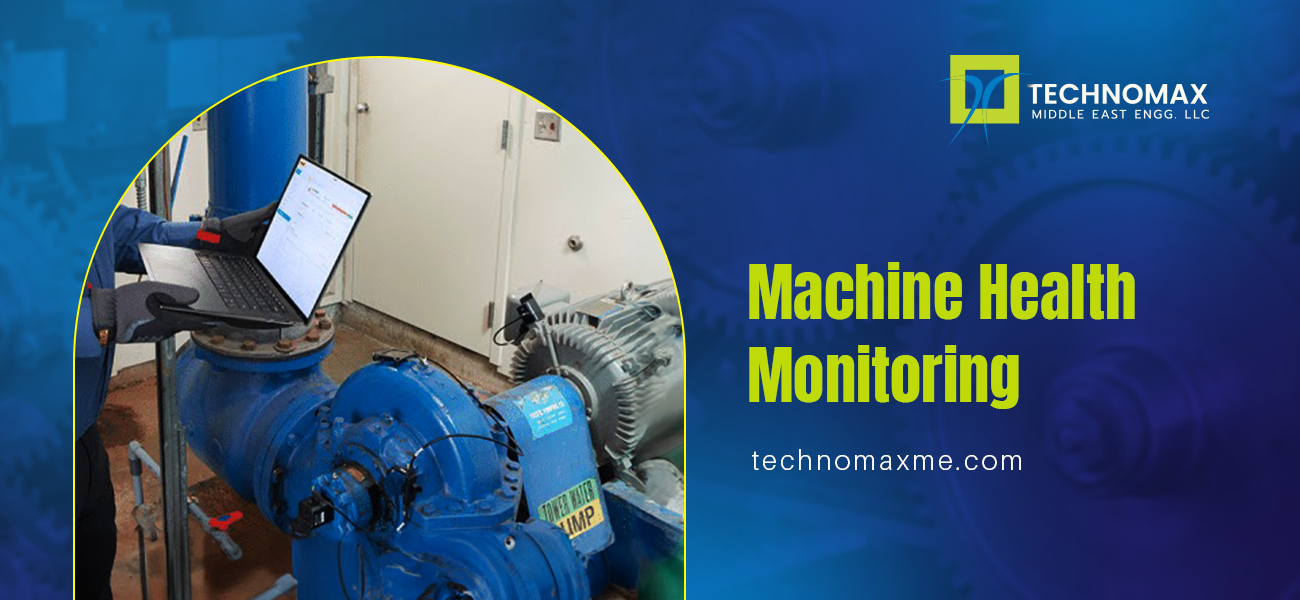
Machine Health Monitoring: The Essential Tool in Keeping Your Machines in Top Shape
Machine Health Monitoring is the process of optimising machine performance in the industry to ensure efficiency and reduce downtime. This approach uses Internet of Things (IoT) tools to give you a clear picture of the performance of the assets. This feature enables the maintenance team to correct faults quickly and save your machine from failure.
This blog gives you detailed information on the working of machine health monitoring and its significance in modern plants. Machine health monitoring provides insights into the foundation of an effective predictive maintenance (PdM) approach. This overview will also explain how these monitoring systems contribute to a proactive maintenance strategy.
What is Machine Health Monitoring?
Machine health monitoring is a systematic approach to evaluating the operational condition of industrial equipment in real time. This process involves conducting various analyses, including vibration, thermal imaging, and power consumption, while also tracking other crucial performance metrics during routine operations.
After establishing this baseline, the system continuously assesses the equipment's condition by monitoring data trends over time. Even subtle deviations from the norm, such as slight changes in temperature or vibration patterns, can indicate potential issues. By examining these data progressions, maintenance personnel can enhance their asset management strategies and ensure that machinery operates at optimal efficiency.
This proactive method allows for early detection of potential problems, enabling timely interventions to prevent more serious malfunctions. By leveraging this information, organisations can make informed decisions about maintenance schedules, extending equipment lifespans and reducing unexpected downtime.
Condition Monitoring vs. Machine Monitoring
Machine health monitoring and condition monitoring are both crucial for predictive maintenance. While they may seem similar, they focus on different aspects and serve slightly different purposes. Machine health monitoring provides a comprehensive view of equipment health, while condition monitoring focuses on specific parameters and conditions. Machine health monitoring aims to understand overall equipment health, while condition monitoring is more concerned with detecting and diagnosing specific issues. Health monitoring involves a wide range of data sources and general equipment performance analysis, while condition monitoring focuses on specific metrics and detailed diagnostic analysis.
In practice, these two approaches often complement each other. Effective maintenance strategies may use both machine health monitoring and condition monitoring to ensure a thorough understanding and management of equipment performance and reliability.
How Does Machine Health Monitoring Work?
Machine health monitoring harnesses the power of IoT in manufacturing equipment to provide valuable insights into equipment conditions. At its core, this approach relies on extensive data collection from various sources, including:
- Sensors measuring vibration
- Devices detecting thermal changes
- Equipment monitoring electrical parameters
- Instruments assessing oil condition
The continuous nature of sensor-based data collection is crucial, offering technicians a comprehensive view of asset health. While spot checks with tools like vibration metres provide useful snapshots, sensors deliver more detailed information, including full-time waveform and Fast Fourier Transform data, rather than just averages or peak readings.
These IoT sensors can transmit asset health data to cloud storage for analysis. Software solutions, particularly computerised maintenance management systems (CMMS), play a vital role in organising and interpreting this data.
Some advanced CMMS platforms can identify irregularities and automatically generate work orders. Additionally, specialised tools are available to help teams gain deeper insights by analysing data across multiple inputs and formats, enhancing their understanding of overall asset health.
Benefits of Machine Health Monitoring
Machine health monitoring integrates data from diverse sources, providing a comprehensive view of the plant’s maintenance requirements. It’s comparable to having a constant surveillance team overseeing plant operations.
Many facilities currently face workforce challenges, particularly as experienced technicians retire. Machine health monitoring helps maximise limited resources by offering data-driven insights crucial for maintenance prioritisation, forecasting, and scheduling.
This approach enhances productivity by increasing overall uptime. Teams can anticipate and plan for issues rather than reacting to them, significantly reducing unexpected downtime. This proactive stance also improves safety for both employees and equipment.
Beyond preventing failures, machine health monitoring optimises performance, ensuring production goals are met without compromising speed or quality. It also liberates maintenance crews from unnecessary scheduled tasks, allowing them to focus their efforts where they are most needed. This shift from calendar-based to condition-based maintenance leads to substantial cost reductions over time.
The following are some of the key advantages of machine health monitoring:
- Enhanced productivity
- Extended equipment lifespan
- Lower maintenance expenses
- Reduced equipment wear
- Increased operational uptime
- Improved plant-wide safety
By providing actionable insights and enabling proactive maintenance strategies, machine health monitoring helps facilities operate more efficiently and effectively in the face of modern industrial challenges.
Machine Health Monitoring and Artificial Intelligence
Managing the extensive data collected for machine health monitoring can be challenging for many facilities, as they often need more resources or expertise to process this information effectively.
This is where AI-powered tools become invaluable. These technologies can rapidly analyse large datasets, significantly enhancing machine health monitoring programs. AI excels at identifying anomalies. With the appropriate software, technicians can receive alerts whenever asset data deviates from established baselines.
Some advanced AI tools offer capabilities beyond basic anomaly detection. For instance, certain platforms utilise AI-driven diagnostic engines capable of identifying numerous distinct asset and component faults using machine health monitoring data. These systems often feature continuous learning capabilities, refining their diagnostic accuracy over time.
By leveraging AI in machine health monitoring, facilities can:
- Efficiently process vast amounts of data
- Detect subtle changes in equipment performance
- Receive early warning of potential issues
- Benefit from increasing accurate fault diagnostics
This technology enables a more proactive and precise approach to maintenance, which helps overcome the challenges of data overload and resource constraints.
Machine Health Monitoring with Prüftechnik
Prüftechnik is excellent in delivering a wide range of machine health monitoring, including data collection hardware, analytics software, and expert consultation to assist with maintenance strategies.
Fluke Connect™ serves as a centralised platform, enabling teams to gather and analyse data from various sources, giving them a holistic view of the plant’s maintenance requirements.
Remote Condition Monitoring (RCM) gives professional insights and support throughout the entire process from initial setup to ongoing monitoring and data analysis. With the assistance of our global experts, you can acquire full clarity in maintenance properties and diagnose equipment issues using cloud-based data streaming.
Assess Your Machine Health with Technomax
Being the leading engineering company in the UAE, Technomax offers advanced machine health monitoring facilities. These will assess the condition and performance of machinery and equipment to ensure they are operating efficiently and to prevent unexpected failures. This practice involves collecting data from machines such as vibration, temperature and pressure readings to identify any signs of wear, damage and malfunction.
Our services include conditional monitoring, installation and maintenance services where we employ only reliable and accurate service for betterment. We assist companies in putting proactive and approachable maintenance plans into practice, which boosts output and guarantees accurate machinery health monitoring.
Learn More About Our Services
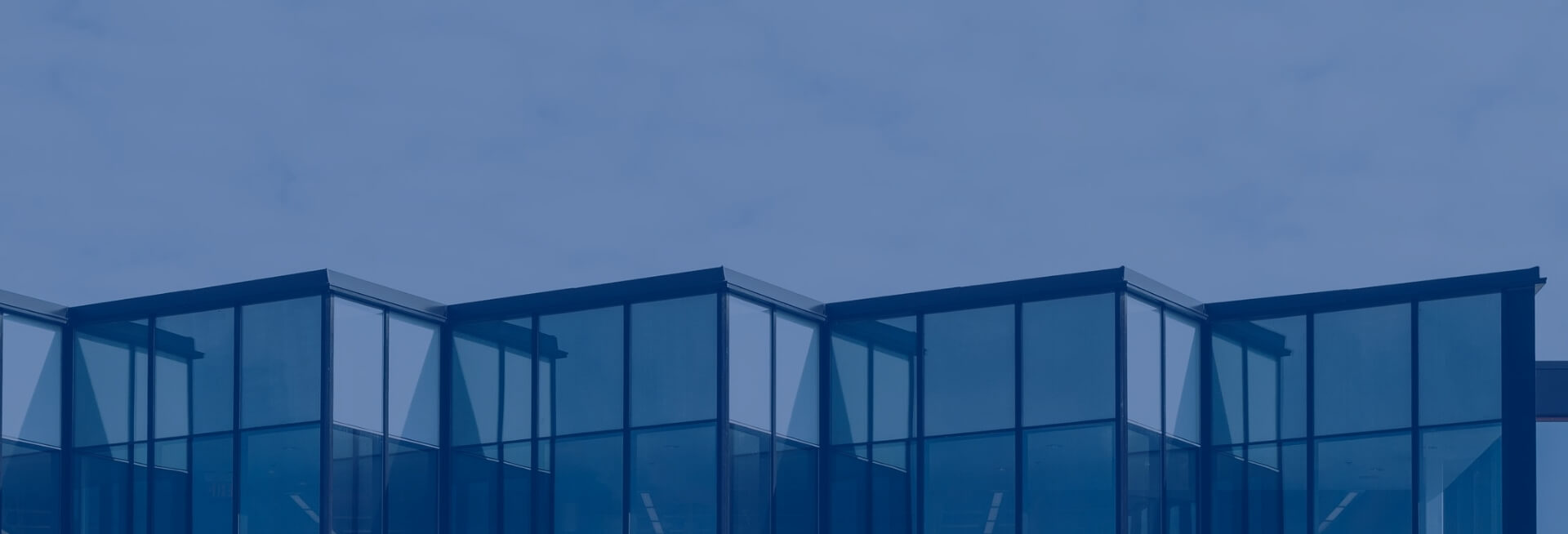
Get Started Now!
It takes less than a minute of your time. Or you may simply call +971 2 555 1 783