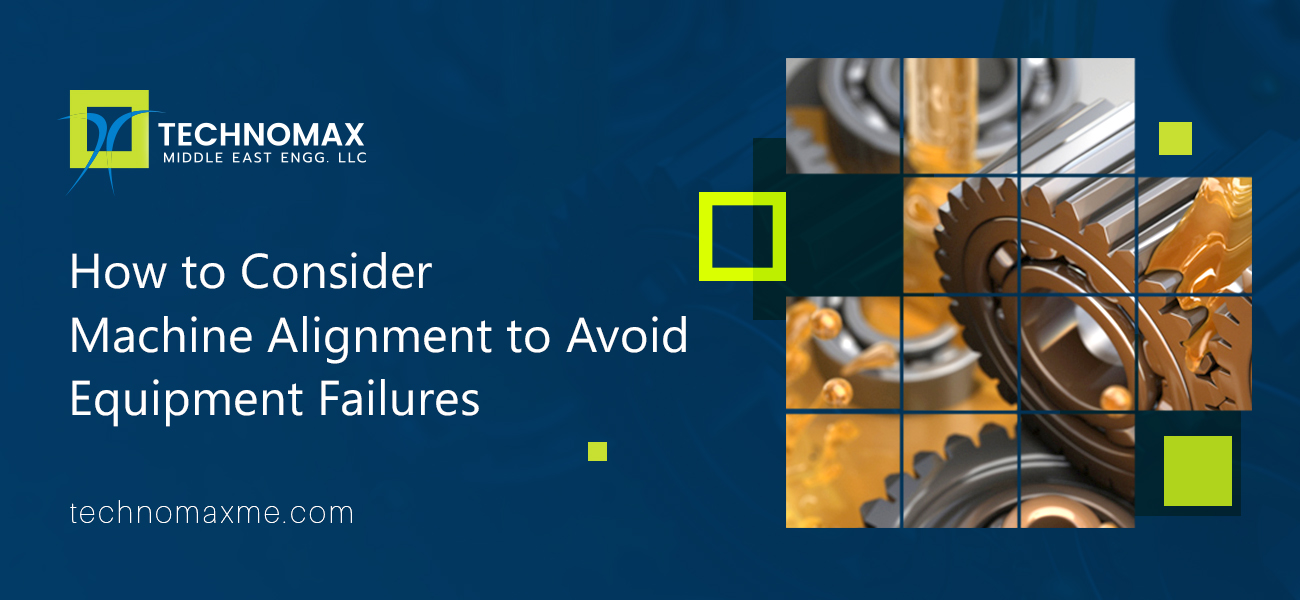
How to Consider Machine Alignment to Avoid Equipment Failures
If properly done, machine alignment can become an important element in a proactive maintenance plan. Misalignment can cause many problems, like coupling damage, bearing premature failure, seal failure, more load consumption etc. Let us see how to get around these issues.
Identifying Misalignment
When both the coupling hubs are aligned properly in Radial & Axial planes, the machine is said to be in proper alignment. When the shafts are not parallel there is parallel misalignment; it can also occur due to angular misalignment in a shaft. Parallel misalignment means shafts are offset, and angular misalignment is one where the shafts are placed at an angle from one another. In some cases, both types of misalignments may occur.
Parallel misalignment can be vertical or horizontal. By adding or removing shims from the machine feet, the motor can correct vertical misalignment. The motor needs to be moved from side to side with the help of jacking bolts till the centre lines fit, to remedy horizontal misalignment. Angular misalignment also shall be corrected by moving vertical or horizontal. Read more about Machine Alignment.
You may also like to read:
- Key factors to check when sourcing for EOT cranes
- Common causes of Piping Vibration and their effects on piping systems
- How Can IoT Condition Monitoring Methods Enhance Machinery Health
Effects of Misalignment
Misalignment can damage machines severely. These are the most common problems:
- Coupling damage – during internal inspection, coupling halves are pulled apart, damaging the grid or teeth, necessitating replacement of the whole coupling. This is a pointer to the actual problem inside the machine.
- The friction along the bearing surfaces rises, causing excessive energy consumption, more wear, and premature machine breakdown.
- Seal damage during the process can cause leakage, and if prolonged, the shaft also may get damaged.
Mere replacement won’t suffice once parts deteriorate; it’s important to identify and rectify the misalignment to prevent recurrent problems.
Unfortunately, most technicians don’t consider that misalignment can cause failure, blaming other factors instead. Hence, they need to be trained properly so that they can recognize the hazards of misalignment and learn to align shafts correctly.
Predictive Technologies
Laser Alignment
This technology helps in the accurate and easy alignment of shafts by directing a laser into a different sensor. This sensor sends data to a device to interpret the information and delivers precise data that helps in adjusting the equipment.
The laser and sensor are fitted to the driver and the machine, and the shafts are rotated, with readings taken over several points to figure out where the driver needs to move.
In a live alignment, the technician aligns the shafts as best he can, starts the machine alignment and runs it till it reaches the operating temperature. Then the alignment readings will be re-measured immediately on switching off to measure the machine’s expansion.
Vibration Analysis
By studying differences in machine stability, vibration response, and critical speeds against a baseline, vibration analysis helps in detecting misalignment. For radial vibration, the readings are in the 2X range, and for axial vibration, they are in the 1X range. Irregular readings need not always point to misalignment; this can be established by taking various samples from both ends – drive and driven.
Thermography
Misalignment-based friction causes increase in temperatures, a technician can take a heat map of the bearing regions to identify abnormal heat zones. Temperature increase is not always indicative of damage during machine inspection. The technician must compare similar machines and perform spot checks consistently.
Oil Analysis
By examining the overall status of the equipment, oil and contaminants, oil analysis can help detect misalignment. If carried out properly, it can detect active machine deterioration earlier than vibration analysis. Samples need to be taken from the proper location, new sampling hardware must be used, sample lines must be flushed, and so on. It is also critical that you know the machine bearing metallurgy; failing this, it may be tough to determine a direct connection to misalignment.
Elemental analysis testing may show tiny increases in iron, lead, copper, aluminium, and other common bearing materials. This information could be the earliest indication of a problem with the machine alignment.
For best results, it would be prudent to combine oil analysis with vibration analysis as this can help in early identification of problems, along with the root cause.
Final Thoughts
Proper alignment can help extend the working life of your machine. At Technomax, we have trained professionals who can perform proper alignment accurately and swiftly with the help of advanced instruments..
We also have all the latest equipment and trained personnel that enable us to carry out all the above mentioned methods of predictive maintenance so that your machinery stays in top working condition, without needing expensive repairs.
Learn More About Our Services
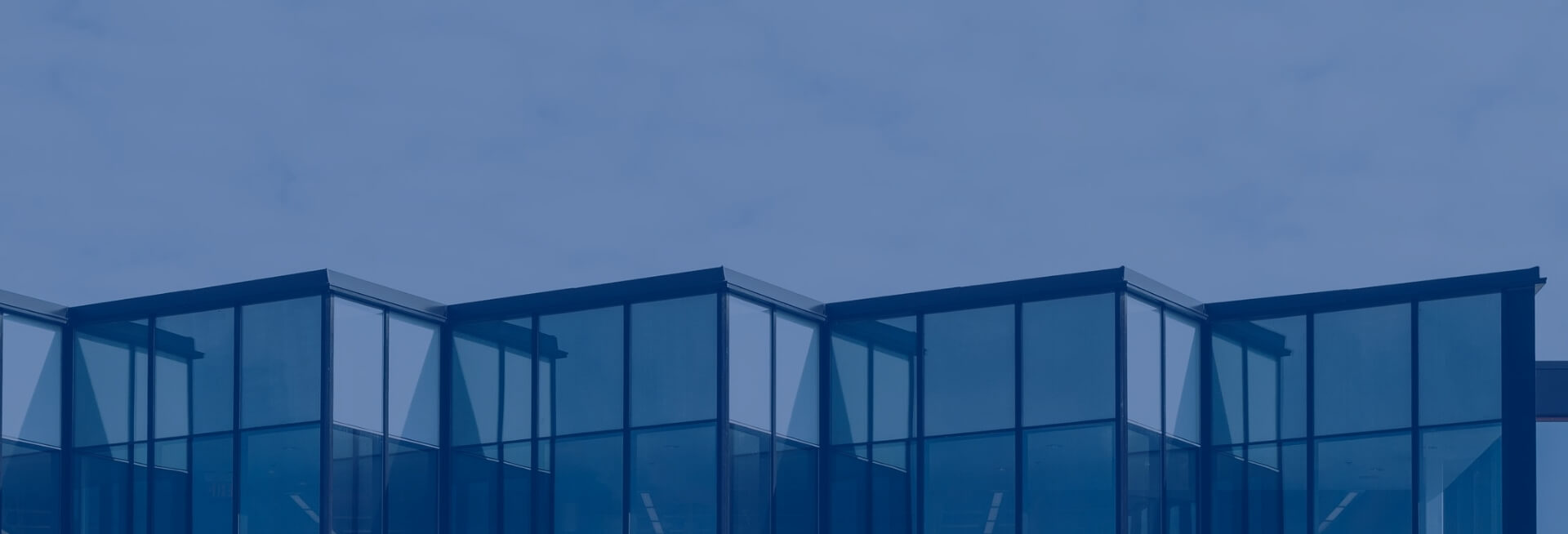
Get Started Now!
It takes less than a minute of your time. Or you may simply call +971 2 555 1 783