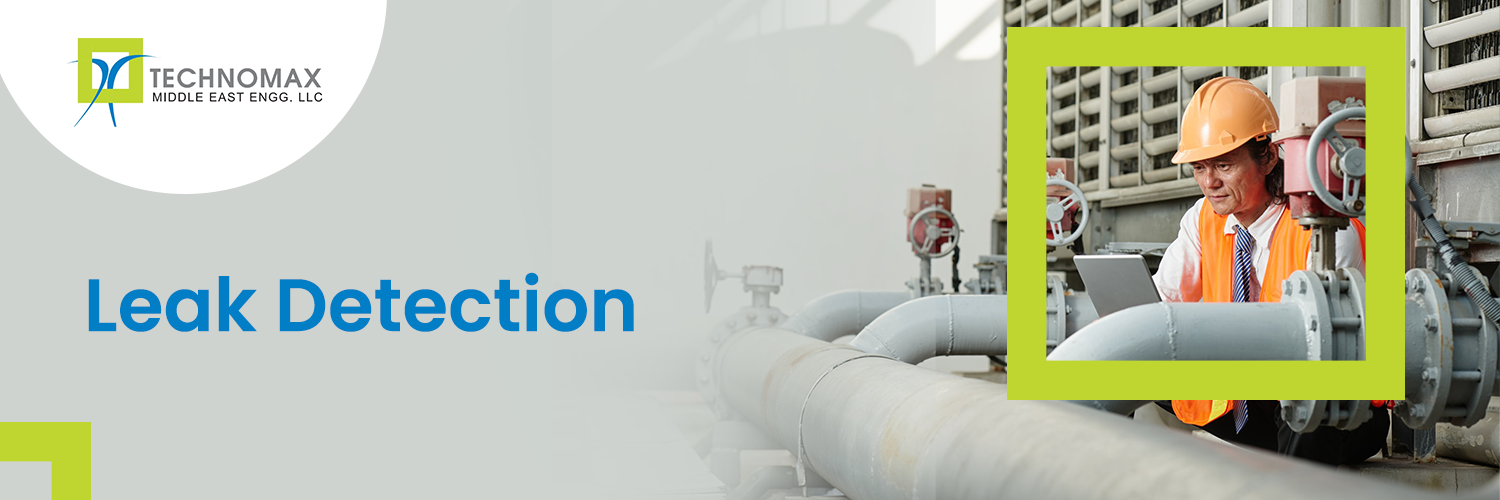
Pipeline Leak Detection in UAE
Pipeline networks are used to transfer oil, gases, and other fluids over great distances, and they are currently regarded as the safest, most dependable, and effective method of doing the same. Corrosion can occur in a pipeline if it is not maintained correctly, particularly near construction joints, low spots where moisture collects, and areas where the pipe has faults.
As a result, having a monitoring system in place is essential for lowering risk and protecting assets. Depending on the type and extent of the pipeline failure, the population and the areas around the pipeline may suffer various impacts. Read more about Pipeline Leak Detection.
You may also like to read:
- Why Do Steam Traps Fail: Causes, Factors & Preventive Methods
- The Influence of Lubrication, Vibration Infrared Analysis Results
- Vibration Motion Magnification by Technomax
Leak detection is a technique for determining whether or not a leak has occurred in a system that contains liquids or gases. Leak detection systems (LDS) are designed to assist pipeline controllers in detecting and localising leaks. To aid in leak detection, LDS provides alarms and presents other related data to pipeline controllers.
A detection device that can identify leakage regardless of size, burial depth, or substance could be an effective solution for leak detection. Pipeline leak detection systems can increase production and system reliability by detecting leaks independent of size, depth of burial, or composition, reducing downtime and inspection time.
Internally-based LDS and externally-based LDS are the two types of LDS. Internally-based systems monitor internal pipeline characteristics with field instrumentation such as flow, pressure, and fluid temperature sensors. Externally based systems use a different set of field instrumentation to monitor external pipeline parameters, such as infrared radiometers or thermal cameras, vapour sensors, acoustic microphones, or fibre-optic cables.
The methods for detecting leaks differ depending on the type of pipeline and the substance transported through it.
The following are some of the most frequent pipeline leak detection methods used in the oil, gas, and petroleum industries:
1. Acoustic monitoring technique
Acoustic sensors rely on changes in the background noise pattern to identify leaks. Acoustic sensors are placed outside the pipeline to identify leaks by measuring noise levels at various points along the network. This information is used to generate the pipeline's noise profile. The leak alert is triggered when the noise profile has deviated from the baseline.
For underground pipelines, acoustic sensors can be fixed directly to the pipeline or linked to the pipe wall using steel rods. A high number of acoustic sensors are required to monitor longer pipes.
2. Gas sampling method
A flame ionization detector contained in a portable or vehicle-mounted probe is commonly used to detect methane or ethane in gas sampling methods. Gas sampling methods have the major advantage of being extremely sensitive to very low gas concentrations.
As a result, utilising gas sampling procedures, even the tiniest leaks can be discovered. This approach is quite accurate, and the likelihood of a false alarm is minimal.
3. Digital oil leak detection
Internal semi-permeable conductors are shielded by a permeable insulating moulded braid in digital sensing cables. An electrical signal is sent through the cable connector's internal conductors and is monitored by a microcontroller embedded within the connector. Excess fluids travel through the permeable braid on the outside and make contact with the semi-permeable conductors on the inside.
The microprocessor detects a change in the cable's electrical characteristics as a result of this. The microprocessor can find the fluid along its length with a 1-meter resolution and send a signal to monitoring systems or operators.
The sensing cables can be wrapped around pipes, buried with pipelines underground, or put as a pipe-in-pipe system.
4. Infrared radio system pipeline testing
Infrared thermographic pipeline testing has proven more accurate and effective in detecting and finding subsurface pipeline leaks, erosion voids, deteriorating pipeline insulation, and poor backfill. Infrared video cameras with a customised filter sensitive to a specific range of infrared wavelengths can detect gas leaks. This spectrum absorbs infrared radiation, which is absorbed by some hydrocarbons.
This allows the leaks to be detected on the video display as a smoke image. Infrared cameras can also be used to detect liquid leaks since the thermal conductivity of wet ground differs from that of dry ground.
In this scenario, the temperature pattern above the leak location is different.
Read more about:
- Equipment Performance Monitoring – Our Approach
- Preventive Maintenance Using Vibration Analysis in Electric Induction Motors
- Maximising Plant Productivity Through Machinery Diagnosis
5. Fibre-optic leak detection
Fibre optic cables are used to monitor leaks from the outside due to physical changes at the leak location. One of the most common physical alterations is a shift in the temperature profile. To detect any changes in the pipeline, a fibre optic link is inserted. A laser then emits pulses that are reflected by the molecules in the fibre optic wire. The magnitude of the reflected laser pulse reveals the temperature at the point where the photon collides with the molecule.
A temperature profile can be created by combining these reflections, allowing the leak site's unique temperature shift to be detected. Fibre optic cables can be used to monitor pipelines and pinpoint leaks. It's also essential to give attention to the monitored media when installing the cable.
If gas is being monitored, the cable should be put above the pipeline because gas rises naturally. When it comes to liquids, it's logical to run the cable beneath the pipeline.
6. RTTM methods
The term "Real-Time Transient Model" (RTTM) refers to a model that simulates the behaviour of a system in real-time. RTTM LDS employs basic physical laws such as mass conservation, momentum conservation, and energy conservation to create mathematical models of flow within a pipeline.
With the use of mathematical algorithms, RTTM can determine mass flow, pressure, density, and temperature at any point along the pipeline in real time. In a pipeline, RTTM LDS can readily mimic both steady-state and transient flow. Leaks can be identified during steady-state and transient circumstances using RTTM technology.
Leak rates are approximated using known formulas.
The application's needs are taken into account when choosing the appropriate leak detection methods. Proper selection is based on various factors, including the desired results, the cost of installation, operation, maintenance, and servicing of the leak detection system, and the installation conditions.
Modern leak detection systems can operate in a wide range of situations, including those with severe temperatures.
Learn More About Our Services
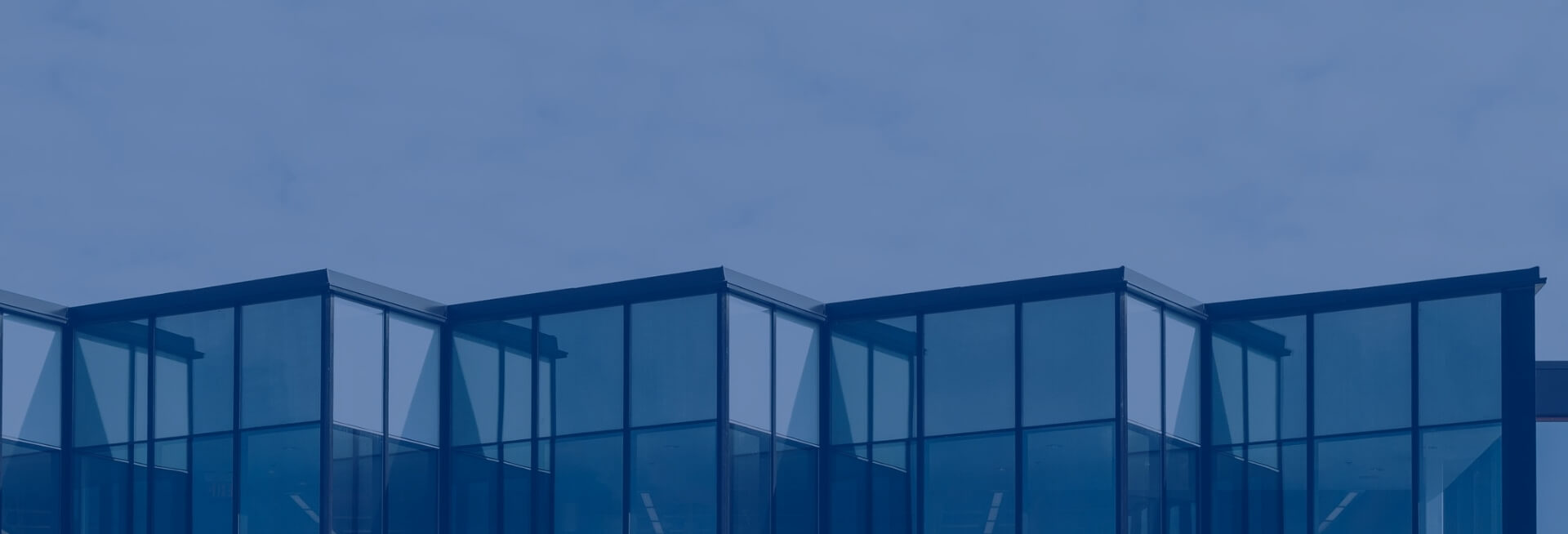
Get Started Now!
It takes less than a minute of your time. Or you may simply call +971 2 555 1 783