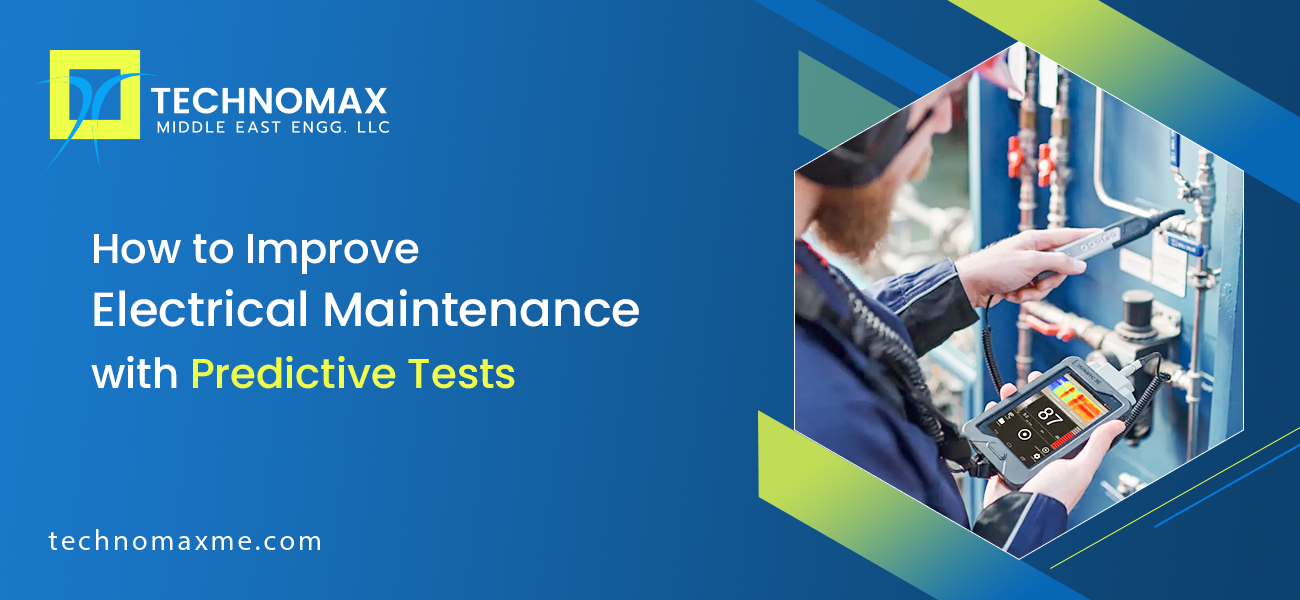
How to Improve Electrical Maintenance with Predictive Tests
Electrical maintenance with predictive maintenance (PdM) improves condition-based monitoring by continuously analyzing equipment health in real-time to optimise performance and lifespan.
In this blog, we delve into the complexities of predictive maintenance, investigating its methods, underlying mechanisms, and implementation options. We will also look at online predictive maintenance testing and reporting practices, as well as the benefits and challenges of this method.
What is Predictive Maintenance?
Predictive maintenance (PdM) is an approach that employs data analysis and machine learning to identify operational anomalies, prevent equipment defects and optimise performance. It is simply a method of monitoring the performance and condition of the equipment by employing software, algorithms and sensors. The primary objective is to minimise maintenance frequency and avoid unplanned outages and unnecessary preventive maintenance costs.
PdM contrasts with preventive maintenance, which schedules maintenance based on predetermined intervals or usage thresholds regardless of the actual condition of the equipment. On the other hand, predictive maintenance is condition-based maintenance, which means that it only carries out maintenance when the data warrants it.
You may also read:
- Navigating Reactive Maintenance
- The Importance of Vibration Analysis in Maintenance
- Reliability Centered Maintenance – A Simple Guide
What are Predictive Maintenance Methods?
Predictive maintenance procedures are used to evaluate the condition monitoring services of electrical systems and identify potential problems before they cause failures. Being the leading engineering company in the UAE, Technomax offers the following predictive maintenance methods, which help extend the life of electrical equipment.
Vibration analysis is a condition-monitoring technique that uses vibration produced by the system to identify faults in the machine. By analyzing these vibration signatures, one can gain insights into the health condition of the system. Vibration testing and diagnosis can help in detecting and addressing both chronic and repairable problems that arise from electrical, operational and electrical irregularities.
Partial discharge testing is a more sophisticated predictive maintenance procedure that can detect small discharges of electrical energy within the insulation. These discharges can be caused by a variety of factors, including contamination, ageing insulation or mechanical stress. If left undetected, partial discharges can eventually lead to insulation failure and equipment breakdown. This testing is typically performed using ultrasonic or acoustic sensors and these sensors can detect the high-frequency sounds that are emitted by partial discharges.
Infrared thermographic surveys use infrared cameras to detect heat signatures on electric equipment. Heat signatures can be caused by a variety of factors, such as loose connections, overloaded circuits or failing components. By identifying hotspots, infrared surveys can help prevent electrical failures. Infrared surveys are typically performed at night when the electrical system is under load. This is because the heat signatures are more profound when the equipment is working harder.
- Insulating Fluid Sampling and Analysis
Insulating fluid sampling and analysis is a predictive maintenance procedure that is used to evaluate the condition of insulating fluids. It can be used to protect electrical equipment from short circuits and other electrical hazards. Over time, insulating fluids can become contaminated or degraded, which can reduce their effectiveness and increase the risk of electrical failures. Insulating fluid sampling and analysis typically involves taking a sample of the fluid and testing it for things like:
- Dielectric strength
- Water content
- Acidity
- Presence of contaminants
- Visual Inspection
Visual inspection is the simplest and most basic predictive maintenance procedure. It involves inspecting electrical equipment for signs of water, damage or corrosion. Visual inspections should be performed regularly and any problems that are found should be corrected immediately. This can be done by looking for things like:
- Loose connections
- Cracked or damaged insulation
- Overheating
- Signs of arcing or tracking
How Does Predictive Maintenance Work?
In predictive maintenance, various techniques are used to collect and process the data from every piece of equipment, including temperature, vibration, voltage, current, and performance metrics. This data is then analyzed using machine learning algorithms and statistical methods to identify patterns and anomalies that indicate potential problems. Based on these insights, maintenance schedules are proactively adjusted to address the identified issues before they lead to costly breakdowns or downtime.
How to Implement Predictive Maintenance?
To implement predictive maintenance, it is important to consider the power system's specific needs and objectives, and it also involves a strategic approach that encompasses data collection, analysis, and corrective action. The process typically begins with identifying and prioritizing assets based on their criticality and potential impact on operations. Next, personnel are trained in predictive maintenance techniques and data analysis tools. Baselines for normal equipment operation are established using historical data and sensor readings. Sensors are installed to collect real-time data on equipment health and performance. This data is integrated with existing maintenance management systems to provide a holistic view of asset health. Finally, the predictive maintenance strategy is initiated with regular data analysis and proactive maintenance interventions to prevent failures and optimize asset performance.
Online Predictive Maintenance
Online predictive maintenance systems collect data from sensors that are installed on the equipment. This data can include information about the equipment's vibration, temperature, pressure, and other parameters. This data is then sent to a cloud-based platform, where it is analyzed using machine learning algorithms. These algorithms can identify patterns in the data that indicate potential problems with the equipment.
Online Testing and Maintenance Reporting
By following the execution of online testing and maintenance services, a standardized report will be generated with the recommended follow-up actions. A quality report should include:
- Recommend corrective actions with priority
- Identify findings that require immediate investigation/repairs
- Identify findings that require additional monitoring
- Identify findings that require additional diagnostics
What Are the Benefits of Predictive Maintenance?
Predictive maintenance provides numerous advantages that can dramatically improve asset efficiency, reliability, and durability. Utilizing data analysis to predict possible equipment breakdowns before they happen, predictive maintenance allows for proactive actions that minimize unplanned downtime, lower maintenance costs, and increase the useful life of valuable assets. Furthermore, predictive maintenance enhances safety and resource allocation by recognizing and correcting possible hazards before they escalate into serious occurrences. AI predictive maintenance techniques are also used in the industry for accuracy.
What Are the Challenges of Predictive Maintenance?
Predictive maintenance has its own set of challenges, including data security, data integration and data quality. The poor quality of data leads to situations such as missed detections, inaccurate predictions or false alarms. Data security demands encryption, backup measures and authentication to secure the system from harm. Moreover, for data integration, interoperable and compatible systems are required that can communicate and exchange data without causing any issues.
Conclusion
Predictive maintenance is a key technique for improving electrical system dependability, minimising downtime, and prolonging the lifespan of critical assets. With procedures like visual inspection, partial discharge testing, infrared/thermographic surveys, and sampling and analysis of insulating fluid, companies can get a full picture of the health of their electrical infrastructure. This lets them make timely repairs and maintenance plans. Predictive maintenance's capabilities will surely grow along with technology's constant advancement, giving organisations even more ability to protect their electrical systems and accomplish their strategic objectives.
Learn More About Our Services
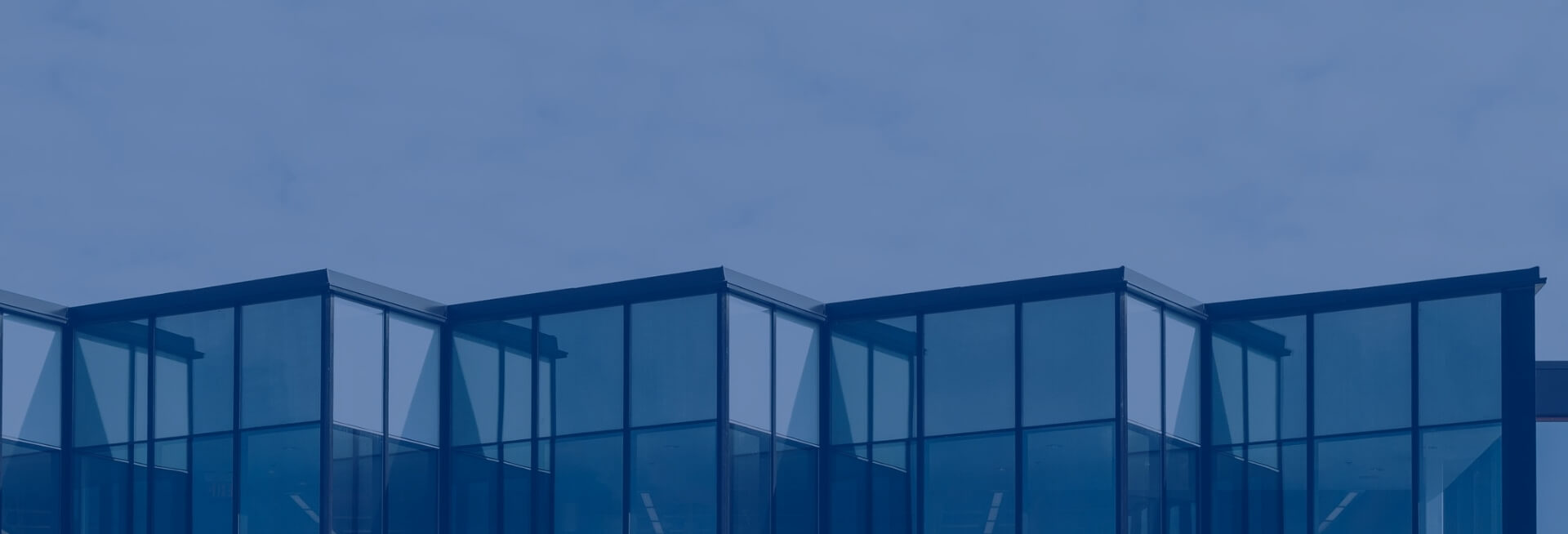
Get Started Now!
It takes less than a minute of your time. Or you may simply call +971 2 555 1 783