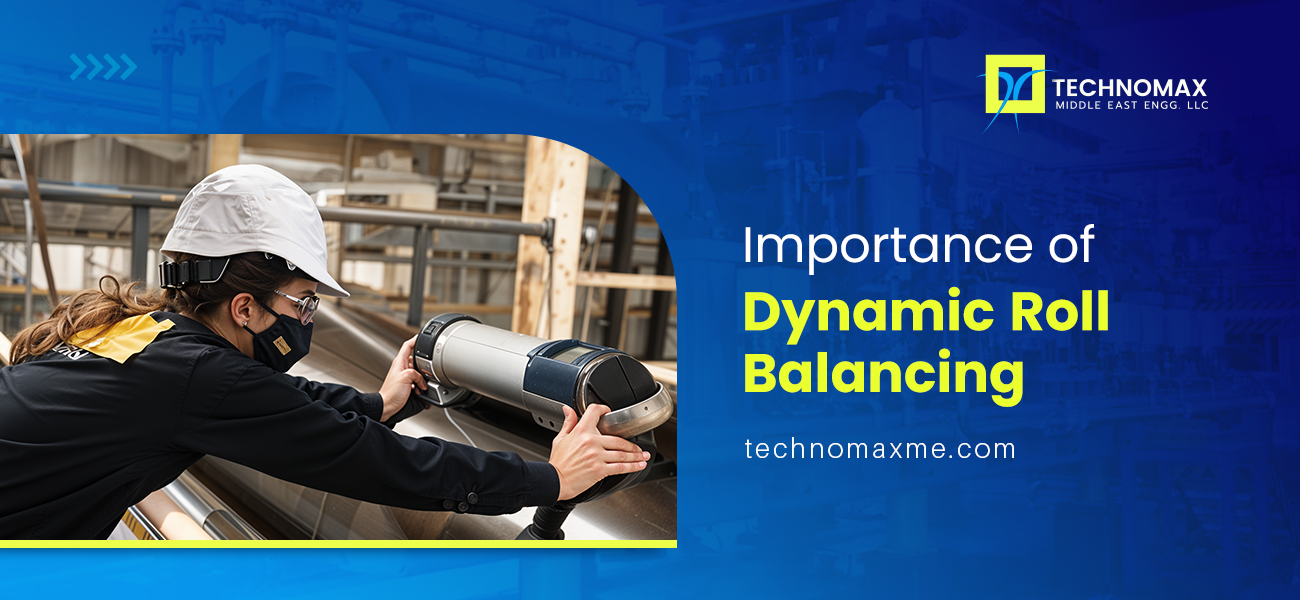
Importance of Dynamic Roll Balancing
Dynamic roll balancing is critical in maintaining the health of rotating parts in different machines. The faster the rotating parts function, the greater the possibility of the system going out of control. The roll-balancing technique keeps the system in its optimal working environment. It analyses the performance of the rotating part, identifies any imbalances, and corrects them using advanced techniques. Voila! The system is back on its feet at optimal speed and performance. This blog will explore the importance, types, and advantages of roll balancing and its role in enhancing machine performance.
Understanding Dynamic Roll Balancing
Dynamic roll balancing is a process that ensures the imbalances on rotating parts in machinery are properly aligned and balanced. The process is employed to establish operational efficiency and to reduce excessive wear and vibration. The major task is to facilitate hassle-free and stable rotation of components such as shafts, rollers, and spindles. Failing to balance the rolls may result in severe consequences, including enhanced roll-bearing fatigue, lower performance, and increased risks associated with possible accidents. This technique improves the balance of rotation and distribution of mass so that the mass centerline will align with the axis of rotation to reduce vibration and other potential damage during operation.
The dynamic roll balancing mechanism begins with mounting the rotating part on the balancing machine. The balancing machine spins at the rotating part's operational speed, and the sensors will detect vibrations that might be caused by imbalances. The data from these are processed and used to calculate the location and extent of the imbalance. Once the imbalance is recognized, adjustments are made by adding or removing weight from particular locations. This is done by assigning some weight to some parts or drilling some holes. The part is then returned to confirm that the rotational imbalance has been corrected and the overall vibration levels are within the tolerance level. This process continues until the part reaches the exact balance to the required precision.
Why is Dynamic Roll Balancing Important?
Dynamic roll balancing is crucial for several factors regarding rotating machinery’s performance, risk-free operation, and durability. It is vital for several reasons:
- Performance: Balanced rolls ensure the machinery's proper functioning, increasing efficiency. An unbalanced roll may lead to vibrations, which increase inefficiencies and affect the quality of the output products.
- Longevity: Balancing effectively minimises the oscillation movements that stress the machinery's bearings, shafts, and other assemblies. This, in turn, increases the life span of these components, meaning less frequent maintenance and replacement, which in the long run translates to less cost.
- Safety: Imbalanced rolls can be a matter of life and death. The vibrations caused by unbalanced rolls may result in catastrophic results, such as structural failures or major machinery breakdowns, and even risks for the operators, with the likelihood of severe accidents. Dynamic balancing mitigates these risks, providing stability and achieving smooth operation.
- Efficiency: Balanced rolls work more smoothly than out-of-balance rolls as they do not waste much energy through friction and vibrations. This efficiency decreases energy usage and running expenses as the machinery operates with less strain and resistance.
- Reduced Downtime: Dynamic balancing can reduce the probability of machinery failure amidst operation, which would lead to unpredicted downtime. With properly balanced rolls, there are few or no chances of an unexpected breakdown, facilitating continuous production and reducing expensive interruptions.
Types of Balancing
There are two ways in which roll balancing can be done: static and dynamic balancing.
1. Static Balancing
Static balancing ensures the roll does not rotate when placed on a knife edge or balancing supports. This type of balancing is adequate for components that operate at slow speeds or are subjected to nominal dynamic forces.
2. Dynamic Balancing
Dynamic balancing considers the mass distribution and the forces acting on the roll during rotation. It is used on parts that run at high speeds or where dynamic force coefficients are large. It corrects for both static and couple imbalances.
3. Flexible Roll Imbalance
Flexible roll imbalance occurs when there is an imbalance in long and slender rolls. This causes an inequality in the thickness of the roll wall and other imperfections, like a rise in thickness at the centre or shoulders. Balancing these rolls and restoring the operational conditions require specific balancing techniques.
How is Dynamic Roll Balancing Done?
Dynamic roll balancing is a unique process that includes several steps. It is designed to ensure optimal machinery operating conditions by eliminating unnecessary vibrations. The process involves measurement, analysis, correction, and verification. Let’s take a detailed look at the process.
1. Measurement
The primary inspection looks for signs of wear, damage, or deformation on the roll and takes down the roll’s size, weight, and material measurements. Next, the roll is installed in a balancing machine, initiating the operational conditions by rotating at the required operating speeds. Vibration and displacement sensors are positioned in critical areas to detect imbalances.
2. Analysis
At first, the rotating speed is set to low and gradually increases to the optimal operational speeds. The sensors placed in strategic positions will collect data on displacement and vibrations. The vibration amplitudes and phase angles at various rotational speeds are analyzed and noted. This data will then be used to calculate the imbalance vectors, representing the extent and location of the imbalance in the roll.
3. Correction
Once the imbalance has been identified, it is time to use correction techniques. Methods such as adding extra material, say balancing weights or removing material through drilling, can be done at positions identified during analysis. Temporary weights can be used to define the position and quantity required for the correction. The weight can be welded or brazed onto the roll for a permanent solution.
4. Verification
Once the corrections are made, it is time to re-test the roll at different rotating speeds to ensure that the imbalance no longer exists. Additional adjustments can be made if necessary based on the observations. The tests are conducted at actual working conditions to check whether or not it has smooth operation without much vibration. The roll, once balanced, becomes certified to have attained the industry standards.
Dynamic Roll Balancing Techniques and Tools
ParAlign Technology
ParAlign is a dynamic roll-balancing technique that utilizes IMUs to orient and balance rolls. It reduces downtime to a minimum and offers high accuracy in identifying imbalances or lack thereof.
Dynamic Balancing Machines
Modern balancing machines have a computerized system that provides real-time information and controls analysis. These machines can align rolls to fine tolerances to get the best performance.
ParAlign: Fastest Dynamic Roll Measurement Technique
ParAlign is an advanced dynamic roll-balancing technology that leverages inertial measurement units to analyze roll alignment in machinery precisely. Here are some of the advantages of choosing ParAlign services:
- Speed and Efficiency: ParAlign facilitates quicker analysis than traditional methods, minimizing downtime and maximizing productivity.
- Accuracy: Since ParAlign leverages IMU technology, the results are exact and accurate. This reduces errors and ensures precise roll alignment.
- Non-Contact Method: The noncontact method is another factor that makes ParAlign stand out from the traditional techniques.
- Comprehensive Data: ParAlign's roll alignment information is more detailed and extensive, leading to highly accurate corrections and enhanced roll performance.
- Versatility: The ParAlign service can be applied to various industries, such as paper and pulp, steel and aluminium, textile, and printing. Therefore, it offers a solution for roll alignment needs in different sectors.
Features of ParAlign
- Uses Inertial Measurement Units (IMUs)
- Rapid measurement - Measures up to 10 rolls per hour.
- Provides real-time data
- 3D visualization
- High accuracy
- Minimal downtime
- User-friendly interface
Roll Balancing from Technomax
Technomax offers advanced balancing services designed to ensure optimal performance and longevity of machinery. The skilled technicians at Technomax ensure that the rotating parts inside the machinery are perfectly balanced and capable of maximum productivity. By partnering with Fluke, Technomax offers top-tier roll balancing tools and services to customers and helps maintain machinery health.
Fluke's alignment and vibration analysis tools enable one and two-plane field balancing and provide detailed vibration analysis. A perfectly balanced roll will have minimal vibrations and be prone to less wear and tear. Being the leading Engineering company in UAE, Technomax creates custom roll-balancing services to meet its customers’ unique requirements. They have catered to various industries, including textile production, paper manufacturing, printing, and steel and aluminium processing.
Learn More About Our Services
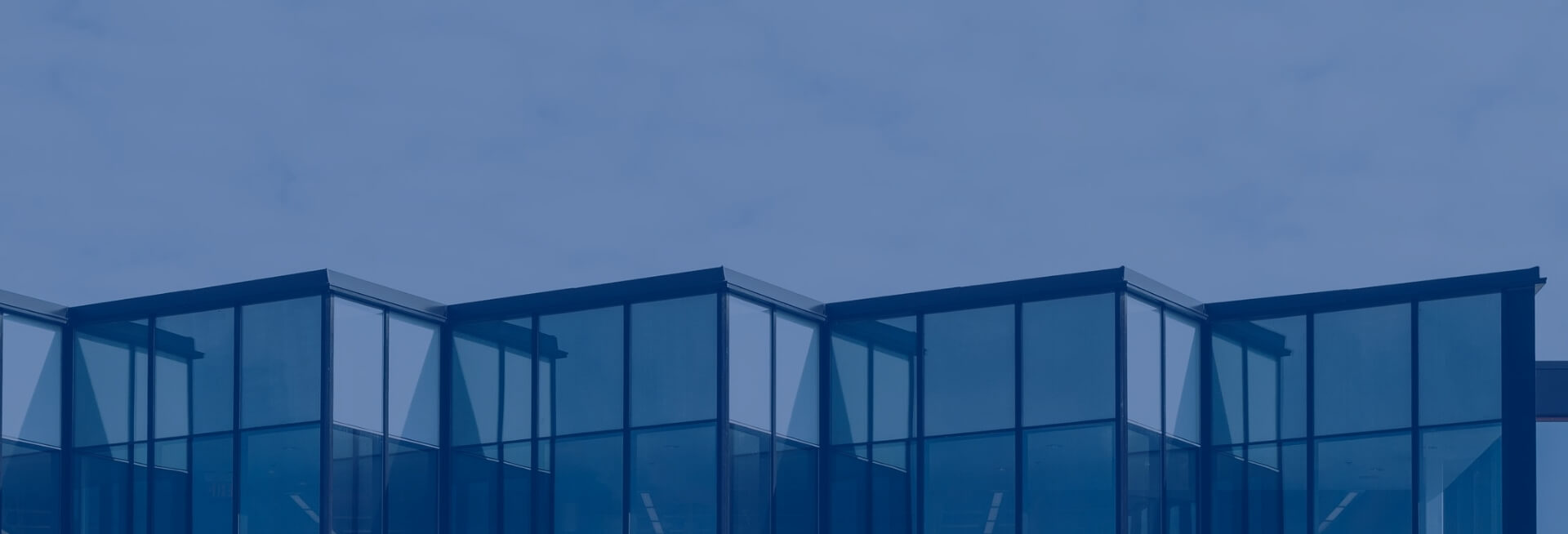
Get Started Now!
It takes less than a minute of your time. Or you may simply call +971 2 555 1 783