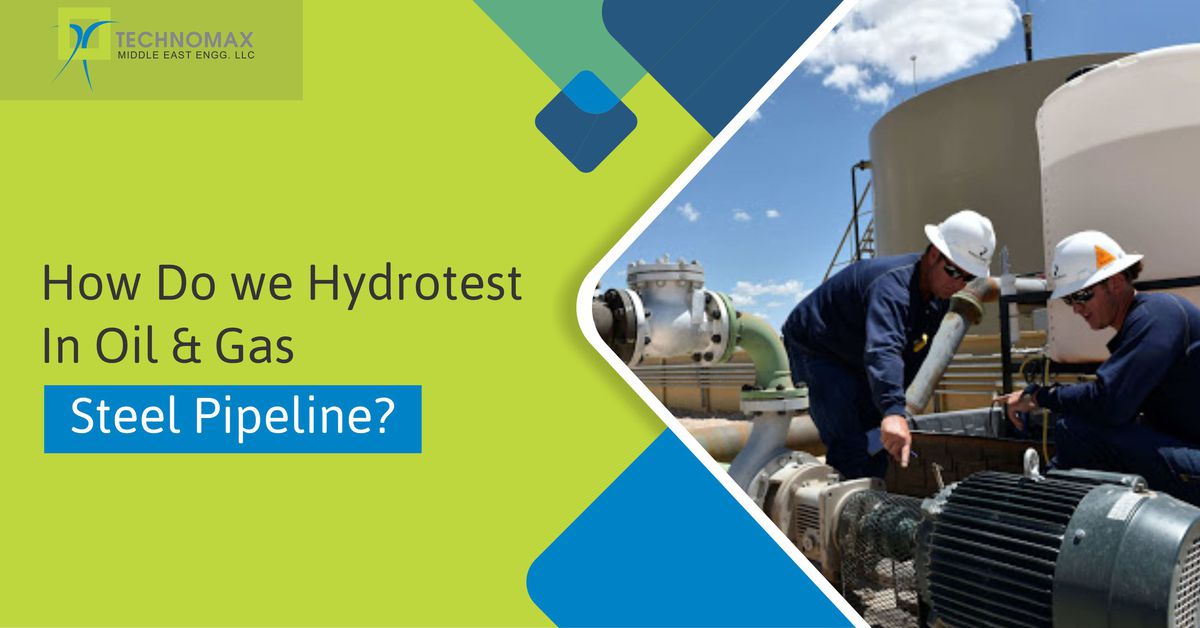
Hydrostatic (Hydro) Testing is a method used to assess the strength and leak resistance of components like piping systems, gas cylinders, boilers, and pressure vessels. This test is commonly conducted after maintenance or repairs to ensure the equipment can safely function under operating conditions when put back into service. The hydro test is usually used for post-construction testing of hazardous substances in pipelines for liquids and pipelines for high-stress natural gas. In a pressure test, water inside the pipeline is pressurized by using specialized pumps to increase the test pressure water to a level above the maximum operating pressure of the pipeline.
In this test, the pressure is maintained for several hours to ensure no leaks in the pipeline. Read more about Hydro Test in oil and gas steel pipelines.
Any indication of a leak requires identification and repair of the leak. The pipeline is then pressurized again, and the test is repeated.
Operational integrity at the time of the weld, hydro test in the field, and even more important than the tube itself, is guaranteed if the pressure test is completed successfully. Hydrostatic testing is widely used to periodically reassess the integrity of hazardous liquids and transportation pipelines.
How Does Hydrostatic Testing Work?
Hydrostatic testing is a pressure assessment method where a component is fully filled with water, air is removed, and the system is pressurized up to 1.5 times its design pressure limit. The pressure is maintained for a set period while the system is visually inspected for leaks. To enhance leak detection, tracer or fluorescent dyes may be added to the water, helping identify cracks and weak points.
New Hydro Test Protocols for Pipelines
It is defined in current federal standards that minimum pipeline safety is not integrity management crack tests, as has been demonstrated in many recent cracks in duct cracking. Inside pipeline evaluations using the hydro test, hydrocarbon products are moved from the section or sections being tested and replaced with water to minimize the risk of test failure and environmental damage resulting from leaks or breakage.
If a pipe successfully passes a hydrostatic pressure test, it can be assumed that it does not have any defects in the tube tested at the time of the hydro test. This is particularly important when dealing with pipe sections that are susceptible to cracking hazards, such as stress corrosion cracking, or SCC, or break threats produced before about 1970 using low-frequency electrical resistance welding (LFERW) and longitudinal seam back welding (LW).
Experience has shown that, in some cases, depending on the operation, the pipe threatening to crack may be susceptible to breaking. Under pipeline safety regulations (subpart E of 49CFR§195), hydrostatic test Tubes for hazardous liquids require testing at least 125% of the maximum working pressure (MOP), for at least four continuous hours and another 4 hours at a pressure of at least 110% of MOP if the tubing is not visible.
If there is concern about latent cracks that can grow due to a phenomenon known as "pressure reversals," then a test at the maximum pressure of 139% of the MOP can be conducted for a short period of about 1/2 hour. The peak test will serve to "clean" any cracks that may otherwise grow during pressure reductions after hydrostatic testing or as a result of short-term pressure cycles.
Studies have demonstrated the acceptability of piping for extended service after an appropriate peak hydrostatic pressure test. Some factors would accelerate the growth of cracks, such as corrosion or aggressive pressure cycles. Hydro test pressure should also define the minimum and maximum pressure range on a parameter used for fracture mechanics evaluation—test pressures as a percentage of the specified minimum yield stress. The hydro test is considered one of the tests for condition monitoring services.
Also read:
- Principles and Applications of Infrared thermography
- What Are Vibrations, Torsional Vibrations & Shaft Twist?
- Single Girder vs. Double Girder Crane – Know The Difference
Problems for hydro testing in deep waters
The hydro test is one of the quality control measures and condition monitoring services used to protect the installed piping systems during condition monitoring services. The individual components of the pipeline for the planned benefits are an integral part of the design process.
Hydrotest loads are one of the loads of an experience of the pipeline system in its useful life, and these loads are also considered in the project Law Suit.
For deep-water subsea systems, external pressure loads should be considered in the design to be consistent with fundamental physics. Hydrostatic conditions, both internal and external, are essential to determine internal and external pressure loads in all positions. All guidelines, industry standards, or RPs and design documents (including requests for authorization) must be explicit, whenever possible, about the definitions of the word "pressure." Wherever "pressure" is described, the position must be defined for the wellhead, at the inlet valve, or at the flow line's deepest point.
If the pressure is internal, external pressure, or differential pressure (that is, the difference between internal and external pressures). API RP 1111 is consistent with this terminology and is based on the use of differential pressure. However, it is recognized that currently, some regulations do not use the term "differential" pressure, but piping design codes do in condition monitoring services. Technomax provides in-class condition monitoring services in the UAE.
FAQs
1. What is the hydro test?
A hydro test is a pressure test that checks the strength and integrity of pipes, tanks, and pressure vessels by filling them with water, pressurizing them, and checking for leaks.
2. What is the difference between a hydro test and a pressure test?
A hydro test uses water to check for leaks and structural integrity, while a pressure test can use gases or other fluids. Hydro tests are safer since water is non-compressible, reducing explosion risks.
3. What is a hydro flow test?
A hydro flow test measures water flow and pressure in a piping system, commonly used in fire protection and water supply networks to ensure adequate water delivery.
4. What is the duration of a hydro test?
The duration varies based on standards and equipment, typically ranging from 10 minutes to 24 hours, with most tests lasting 30 minutes to 2 hours.
Learn More About Our Services
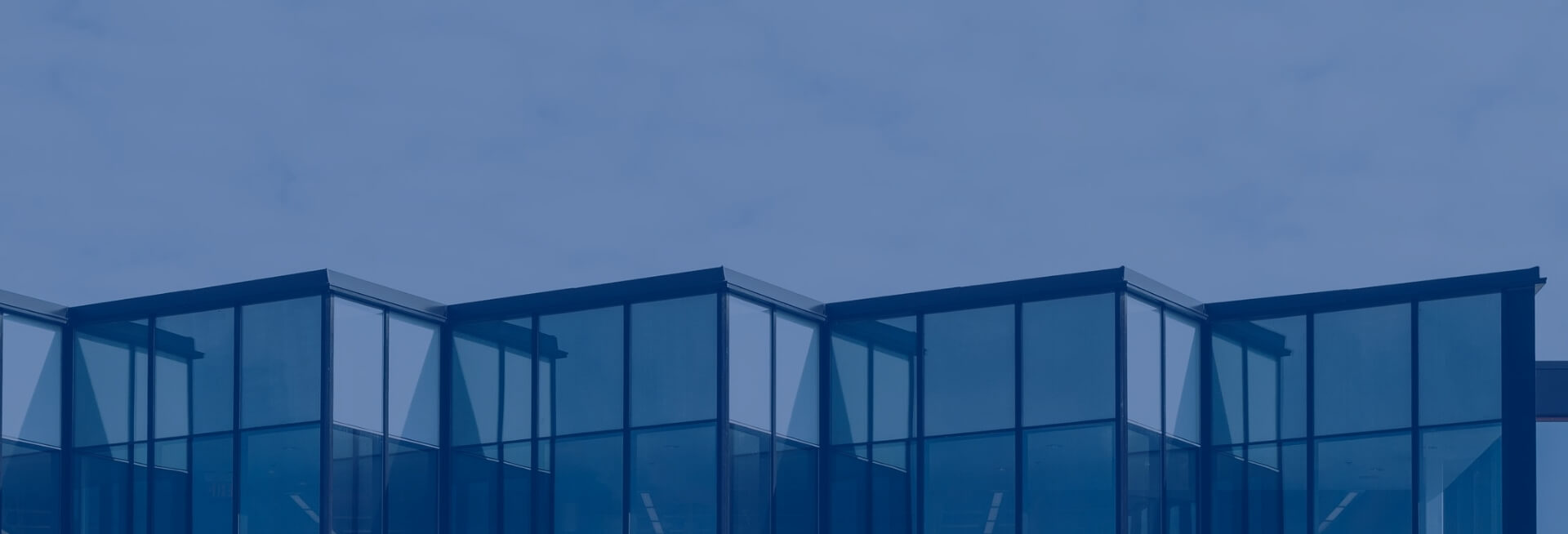
Get Started Now!
It takes less than a minute of your time. Or you may simply call +971 2 555 1 783