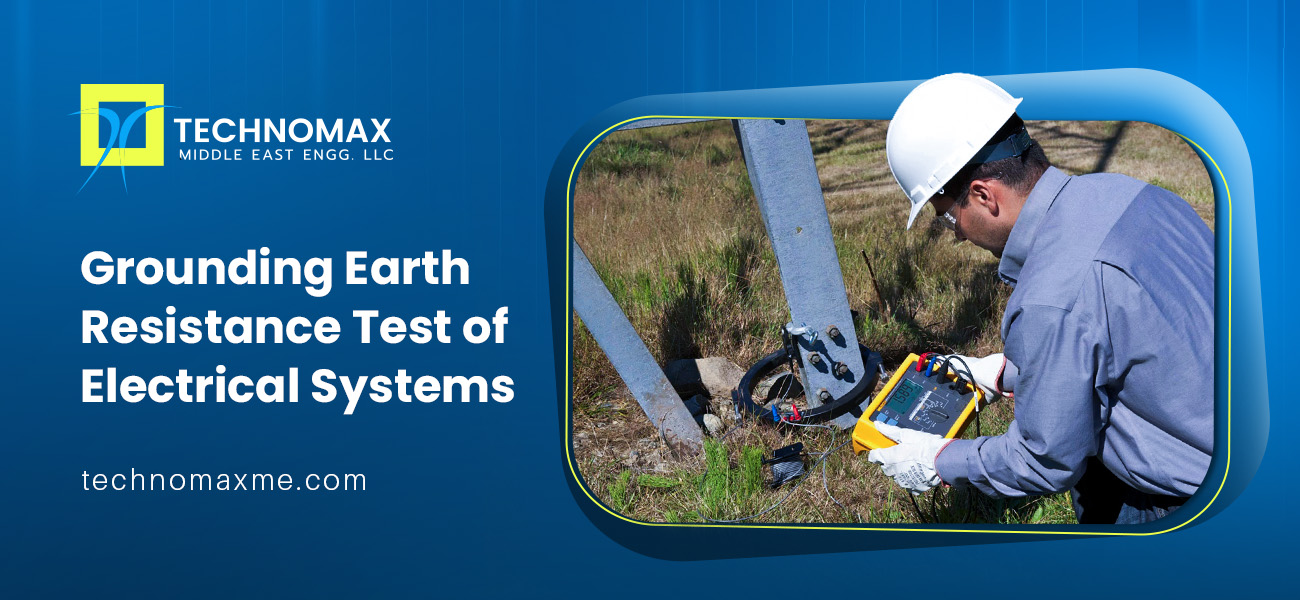
Grounding Earth Resistance Test of Electrical Systems
Did you know improper grounding can lead to catastrophic failures and serious risks to equipment and personnel? Electrical grounding, or earthing, is important to safety and reliability, providing a direct path for fault currents to safely dissipate into the earth. But how does grounding work, and why is ground resistance so important?
This blog answers these questions, exploring the fundamentals of grounding, the significance of maintaining low ground resistance, and the various methods for ground resistance testing. Read on to discover the key aspects of grounding and the practices needed to keep your systems safe and reliable.
What Is Electrical Grounding?
Electrical grounding is the process of connecting an electrical system to the earth. It is usually done during building construction and involves the use of a special wire known as a grounding wire to direct excess electricity into the ground safely.
A grounding wire is essential for safety and efficiency, as it provides a safe path for excess electrical current. It keeps people and equipment safe from electrical shocks and fires. Grounding ensures the safe and efficient operation of electrical systems by preventing dangerous electricity buildups.
Why Is Electrical Grounding Important?
Electrical grounding is crucial because it greatly enhances the safety and performance of electrical systems. It provides a safe pathway for excess electricity to enter the ground, reducing the risk of electrical shocks, fires, and electrostatic discharge (ESD). Grounding is vital for protecting both people and electronic equipment from electrical hazards, like fault currents and lightning.
The main purpose of grounding is to keep people and sensitive equipment safe from electric shocks and other electrical dangers. It helps to dissipate dangerous fault currents and lowers the risk of electrical shocks, thus preventing injuries, fatalities, and damage to electrical parts.
Grounding also stabilises voltage levels in an electrical system and protects against surges. It allows excess current to safely flow into the ground, which helps protect the system and connected devices from lightning strikes or power surges. Regular ground resistance testing is crucial to ensure grounding systems remain effective. This testing can identify issues like soil composition changes or corrosion, which might compromise the grounding system's effectiveness.
Proper installation and maintenance of grounding systems are imperative for the reliability and safety of electrical operations. It prevents unstable electrical behaviour, protects against equipment malfunctions, and ensures safety against hazardous conditions, highlighting the necessity of correct grounding practices.
The Significance of Grounding in Industrial Electrical Systems
Grounding in industrial settings ensures personnel safety and prevents system damage in the event of a fault. It provides a low-resistance path for fault current, allowing circuit protective devices to operate swiftly and disconnect the supply. In industrial environments, where equipment and machinery are more complex and powerful, the importance of effective grounding cannot be overstated. Earth grounding involves connecting a circuit conductor to a ground electrode, while equipment grounding ensures all operational equipment within a structure is properly grounded.
In industrial settings, reliable electrical grounding is crucial for ensuring safety, protecting equipment, and maintaining operational reliability. It provides a safe path for fault currents, static discharges, EMI, and RFI signals and interference, reducing the risk of electrical shocks and preventing fires or explosions.
Grounding also protects sensitive machinery from damage due to electrical faults or surges, extending equipment lifespan and cutting maintenance costs. It also reduces electromagnetic and radio frequency interference, ensuring the precise and efficient operation of industrial processes.
Adhering to grounding standards is necessary for meeting legal and insurance requirements, while effective grounding also controls static electricity, mitigating hazards in environments with flammable materials or sensitive electronics. Over time, these benefits enhance operational efficiency and provide significant financial savings for industries.
What Is the Purpose of Ground Resistance Testing?
Ground resistance testing assesses the resistance between the grounding electrode and the earth, which is important for detecting faults and hazards. Frequent testing ensures the grounding system remains effective, allowing for proactive maintenance and guaranteeing long-term reliability and safety.
Measurement Principles for Multi-Grounded Systems
In multi-grounded systems, multiple interconnected grounding points offer several paths for fault currents. Testing ground resistance in these systems requires careful planning, the right equipment, and a thorough understanding of the system's layout. Proper measurement techniques are essential for obtaining accurate results and ensuring that the grounding system operates effectively under all conditions.
Clamp-On Test Method
The clamp-on test method measures the resistance of grounding systems using a clamp metre. This method is useful for testing multi-grounded systems without disconnecting them, allowing measurements while the system is in operation. The clamp-on tester measures the resistance between the grounding electrode and the earth, providing accurate results with minimal disruption. This method is especially valuable in industrial settings where maintaining continuous operation is critical.
Minimum Grounding Resistance Values
For various network installations, grounding resistance typically needs to be within the range of 5 to 25 Ω. Maintaining these values ensures the effective dissipation of fault currents into the earth, enhancing system reliability and safety. Low resistance values indicate a strong and efficient grounding system, capable of handling fault currents and preventing potential hazards.
Factors Influencing Ground Resistance
Several factors can impact ground resistance, including:
- Soil Composition and Resistivity: Soils rich in minerals and salts have lower resistivity and, consequently, lower ground resistance. Conversely, dry, sandy, or rocky soils exhibit higher resistivity. Understanding soil composition is key to designing effective grounding systems.
- Moisture Levels: Moist soil conducts electricity more efficiently than dry soil. Seasonal changes and weather conditions can impact soil moisture and ground resistance. Routine testing helps monitor these changes, ensuring the grounding system remains effective.
- Electrode Material and Configuration: Different materials like copper, galvanised steel, and stainless steel offer varying levels of conductivity and durability. Deeper and more widely spaced electrodes generally provide lower resistance. Selecting the appropriate electrode material and configuration is crucial for optimising ground resistance.
- Contaminants: The presence of metals, salts, or substances like oil can influence ground resistance. High concentrations of salts can reduce resistance, while oil can increase it. Identifying and mitigating contaminants improves the effectiveness of the grounding system.
- Mineral Content: Soils containing minerals, such as igneous rocks, have higher resistivity, while mineral-rich soils with ores have lower resistivity. This factor must be considered when designing grounding systems for various geographical locations.
- Temperature: Cold or frozen ground has higher resistivity compared to warmer soil. Temperature variations affect soil resistivity and grounding system performance. Regular testing across different seasons ensures the grounding system performs reliably year-round.
Understanding these factors and principles helps ensure more accurate ground resistance testing and maintains a reliable and safe grounding system.
What Are the Different Methods for Earth Ground Testing?
Earth ground testing is essential for verifying the effectiveness and safety of grounding systems. Let’s take a closer look at how grounding systems are tested using different methods:
- Stakeless Testing: Also referred to as clamp-on testing, this method allows us to measure ground resistance without the need for extra electrodes or interrupting the system. It’s particularly useful in environments where continuous operation is crucial, such as industrial plants or office buildings. Tools like the Fluke 1630-2 FC Earth Ground Clamp ease the process by bypassing the requirement for temporary ground stakes.
- Selective Testing: Sometimes a broader approach isn't enough. Selective testing allows one to zoom in on specific components or sections of a grounding system. Tools like the Fluke 1625-2 GEO are designed for this precision work. They help isolate and measure the test current applied to individual electrodes, providing detailed insights into the performance of complex grounding setups.
- Soil Resistivity Testing: Soil resistivity testing measures the resistivity of soil to determine its suitability for grounding. Here the method involves strategically placing electrodes in configurations similar to the Wenner method and measuring resistance over specified distances to determine the soil's conductivity. This information is essential for designing grounding systems that maintain safe resistance levels across different soil conditions.
Soil resistivity is measured in ohm-metres (Ω·m), with typical values ranging from 1 Ω·m in highly conductive soils to over 10,000 Ω·m in dry, rocky soils. Accurate soil resistivity measurements are crucial for designing grounding systems that maintain resistance levels within safe limits, typically below 25 ohms, to ensure effective performance.
- Fall-of-Potential Testing: This method is also known as the three-point method and the testing involves placing three electrodes in the ground: a test electrode, a potential electrode, and a reference electrode. By passing a controlled current through the testing electrode and measuring the resulting voltage drop between the other two, we can accurately calculate the resistance of the grounding system. This method, also known as the three-point method, is widely accepted for comprehensive assessments of grounding effectiveness due to its reliability.
Each of these methods ensures that grounding systems comply with safety standards and are optimised for peak performance in diverse operational environments.
How to Improve Ground Resistance?
Improving ground resistance involves a series of systematic steps to ensure that grounding systems effectively conduct fault currents and maintain safety and performance. The following are some key steps to be followed to improve ground resistance
Step | Description | Implementation |
Increase the rod diameter | Provides a larger surface area for better conductivity and reduced resistance. | Choose grounding rods with a larger diameter to enhance performance. |
Use multiple grounding rods | Distributes the load among several rods and improves overall conductivity. | Install multiple rods in a linear or triangular pattern, spaced according to guidelines. |
Increase the length of the rod | Reaches deeper into the ground to access more conductive soil layers. | Select longer rods to penetrate deeper and improve contact with conductive soil strata. |
Treat the soil to reduce its resistivity | Adds to soil conductivity to improve ground resistance. | Apply soil conditioning materials such as:
|
Improve electrode material and quality | Uses high-quality materials for better conductivity and durability. | Opt for materials like copper or high-grade galvanised steel for electrodes. |
Optimise electrode placement and configuration | Ensures effective grounding through proper placement and configuration of electrodes. | Follow industry standards for spacing and depth. Install electrodes in areas with the best soil conductivity. |
Regular maintenance and inspection | Maintains ground resistance over time through routine checks and upkeep. | Periodically inspect electrodes, connections, and soil conditions. Address any signs of corrosion or damage promptly. |
Addressing the above can help improve ground resistance and the safety, reliability, and performance of the grounding system.
What Is A Ground Earth Resistance Tester?
The ground resistance tester is an essential tool used to evaluate the resistance of an electrical ground system. It plays a critical role in ensuring the safety and efficiency of electrical setups by verifying the system’s ability to redirect fault currents away from both equipment and individuals, thus minimising potential hazards.
This tool is characterised by its capability to measure resistance within a range from just a few ohms to several thousand ohms. It utilises testing methods that involve 3-point or 4-point configurations to ensure accuracy in its assessments. The ground resistance tester is indispensable for ensuring compliance with safety standards, as it aids in conducting routine inspections, performing maintenance, and pinpointing any issues within the grounding system.
Earth Ground Resistance Testing from Technomax
Grounding and earth resistance testing are essential for the safety and reliability of electrical systems. Proper grounding directs excess electrical current safely into the earth, protecting people, equipment, and structures from potential hazards. Understanding the principles of grounding, the importance of maintaining low ground resistance, and the various methods for ground resistance testing enhance the safety and performance of electrical systems. Regular testing and adherence to industry standards are necessary for maintaining the effectiveness of grounding systems.
Technomax, the leading engineering company in the UAE, leverages state-of-the-art ground resistance testers and adheres to stringent industry-standard protocols to ensure the utmost accuracy of measurements. Our team of experts employs inventive earth ground testers from prominent manufacturers like Fluke, enabling the generation of detailed ground resistance testing reports.
For details on ground resistance testing, electrical switchgear safety, cable testing, and condition monitoring services, reach out to us and find out how Technomax can add to the reliability of your electrical systems and other machinery.
Learn More About Our Services
Recent Blogs
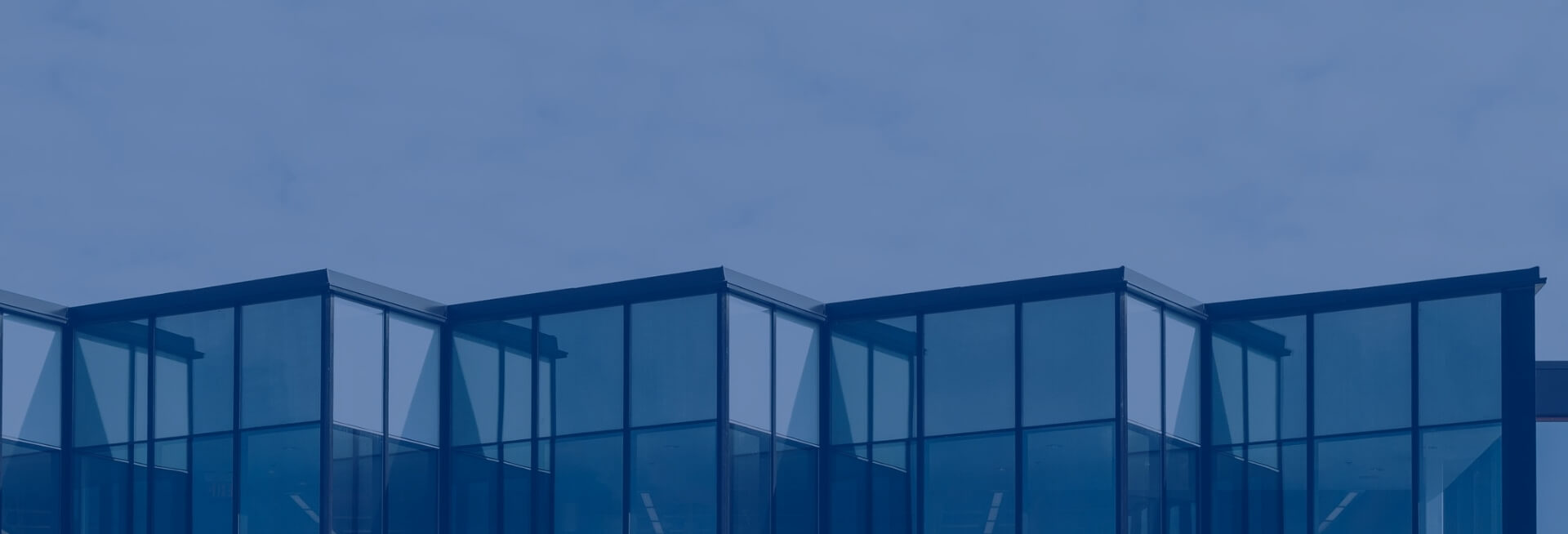
Get Started Now!
It takes less than a minute of your time. Or you may simply call +971 2 555 1 783