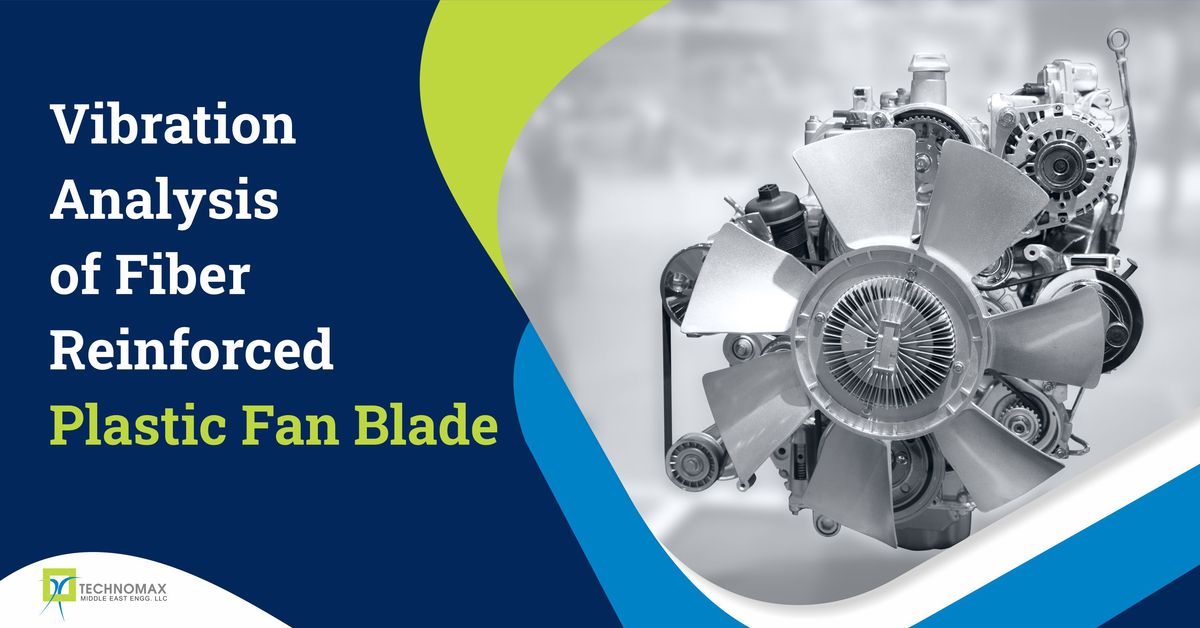
Vibration analysis is part of condition monitoring systems. Structural vibration problems cause severe risks and design limitations for a wide range of engineering products, especially fan blade. Therefore, it can harm their dynamic behaviour, leading to structural damage, such as the collapse of the cooling tower. Consequently, it is necessary to analyze the vibrations to avoid the excitation of the blades at their natural frequencies and, therefore, the resonance phenomenon.
In these circumstances, the blade structure must be designed strong enough to function in the frequency range of interest, withstand severe conditions, and survive maximum fatigue resistance. It is of prime importance to promptly perform vibration analysis and condition monitoring of the fiber-reinforced plastic fan blade.
Its high rigidity rates for density and strength for density and greater freedom to use these properties in the desired orientation and position. In addition, these lightweight structural materials have some definite goals that cannot be achieved with other conventional materials.
These intriguing advantages led positively to integrating these materials in the construction of the fan blades of the cooling towers. Vibration analysis is performed on slides of different sizes that can be used for various applications.
Much research is done on vibration analysis and condition monitoring of different types of blades by other methods. The frequencies can be determined by performing modal analysis using ANSYS. The detailed modal analysis determines the fundamental forms of the mode of vibration and the corresponding frequencies. The analysis of the vibration of a non-uniform composite conical blade was carried out using analytical and experimental methods.
A numerical prediction of vibration behaviour is required for the efficient use of composite materials in rotors. To avoid permanent fatigue condition monitoring and vibration analysis are of paramount importance.
You may also like:
- What is a Festoon Cable System? Types and Benefits
- Electric Overhead Travelling Cranes-Applications and Types
- Vibration Analysis of Fiber-Reinforced Plastic Fan Blade
Vibration Analysis of Fiber-Reinforced Plastic Fan Blade
Failure of composite materials due to insufficient damage predictions occurs very often. Damage to composite materials can exist as visible or invisible damage with different configurations and identities. Therefore, the investigation of the existence of damage in composite materials must have preventive attention to avoid breaking the structures. To prevent injury, vibration analysis and condition monitoring of the fiber-reinforced plastic sheet should be performed.
While the number of failures for a given component may be small, they are essential because they can affect the manufacturer's reputation for reliability. In some cases, primarily when the failure results in personal injury or death, this will lead to costly legal action.
To avoid such problems, vibration analysis and condition monitoring must be implemented from time to time. In any fault analysis, it is vital to obtain more information from the faulty part itself and an investigation of the condition at the time of the fault. The possible causes of failure in the case of the fan blades are the following:
• Inadequate heat treatment of the fan blade of the radiator
• Pressure difference across the length of the entire blade
• Other different causes
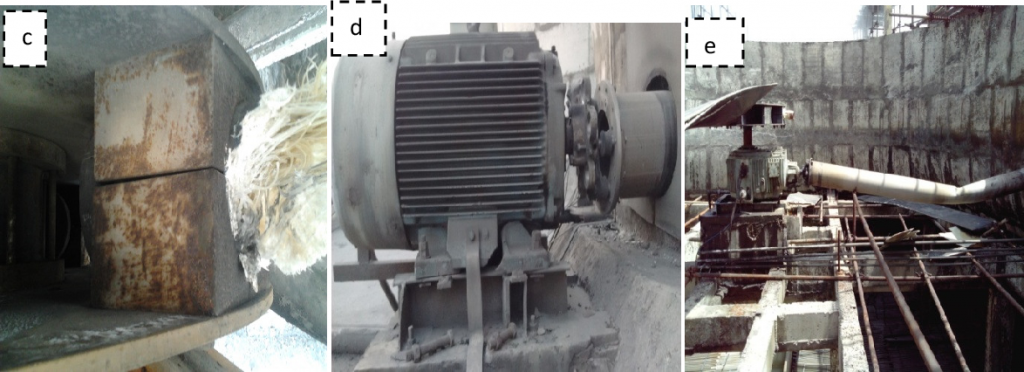
Inadequate heat treatment of the radiator fan blade:
Adequate heat treatment must be carried out after the casting process, that is, precipitation hardening, to increase the strength of the material. The objective of precipitation hardening is to increase the strength and hardness of heat-treatable aluminum alloys which is achieved through a sequence of heat treatment in solution, tempering, and natural or artificial aging.
However, some alloys, which are relatively insensitive to cooling rates during quenching, can be hardened by precipitation by air or water cooling directly from the high-temperature formation process followed by aging treatment.
Performing some laboratory tests, it is observed that the heat treatment was not carried out correctly, and some defects, such as:
i. Holes or porosities were detected (in groups in critical areas and a scattered pattern in other positions of the fan blades).
ii. Deep dents or notches were observed at the edges of the fan blade hub and close to them. It can be seen that the fractured faces reveal two distinct areas of opaque and luminous nature.
Pressure difference along the length of the entire blade:
As the fan rotates beyond the fluid (air), this fluid exerts a particular pressure variation along the blade's cross-section. Due to these pressure variations creating lift and drag forces, these forces depend on the design and conditions of operation. For the radiator fan, the lifting force must be minimal. Otherwise, it can cause the blade to break.
Other miscellaneous causes:
The radiator fan of diesel locomotives is necessary to work in a dangerous environment, with increased oil dust and rain. It can be exposed to roadside dust or fiber from various organic materials in the locomotive's operation, such as calcium carbonate, silica sand, aluminum, carbon black, fiber from different organic materials, oil, dust locomotive slider brakes, etc. TechnoMax Provides condition monitoring and vibration analysis testing.
RADIATOR BLADE SCAN:
First, the slide is designed to identify resources for scanning. The blade is divided into sections accordingly. More sections are made near the raised region and in the folded part. In all the identified sections, the survey is performed to obtain the data from the point cloud. The entire outer edge of the slide is scanned to get the size of the point cloud data. The following procedure is followed to get the coordinate point data.
i. Select the appropriate probe depending on the complex geometry of the blade. Here, a straight probe of 0.5 mm in diameter is used.
ii. Attach the blade to limit degrees of freedom.
iii. Select the Element option in the Usoft main menu to probe the edge coordinate of the blade's root.
iv. Probe at various points along the aerodynamic leaf section of the blade.
v. The output file provides the coordinates of the points detected along the length of the blade. These coordinates are obtained from the fixed reference point. Technomax provides accurate and authentic vibration analysis and condition monitoring facilities in the UAE.
Learn More About Our Services
Recent Blogs
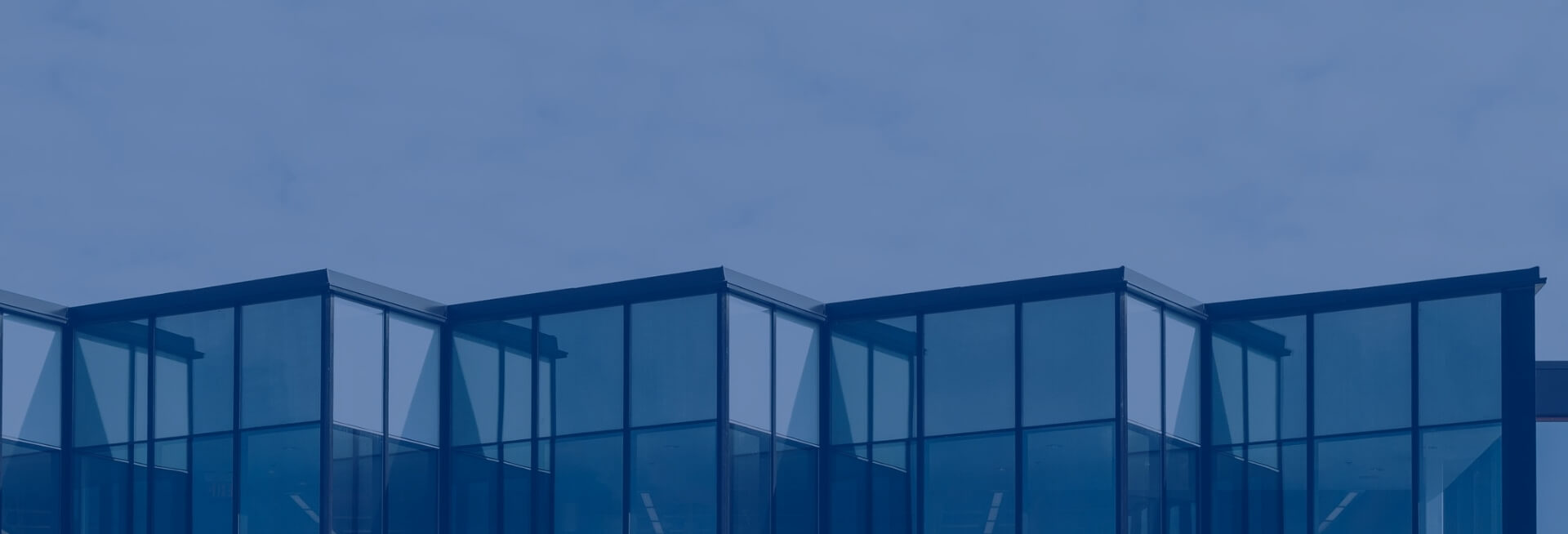
Get Started Now!
It takes less than a minute of your time. Or you may simply call +971 2 555 1 783