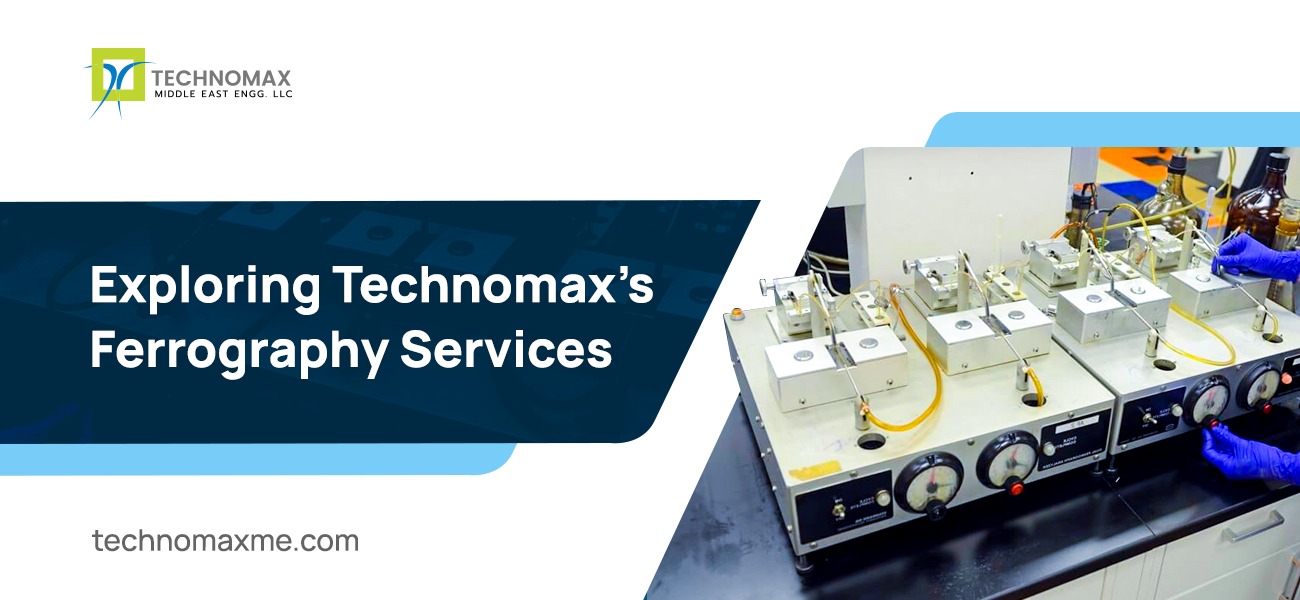
Exploring Technomax’s Ferrography Services
Mechanical failures and botches can be a dreadful situation for industries, causing losses in production, delays, and even safety concerns. Fortunately, modern technology offers us a strong tool for tackling these challenges - ferrography.
The site and degree of mechanical hurdles with the equipment can be determined with the use of this diagnostic tool which evaluates wear particles in the oil.
By detecting wear particles early, ferrography can be the shield that offers protection from serious breakdowns.
Here in this blog, let’s explore ferrography services by Technomax and delve deeper into the process, the pivotal role of ferrography in maintenance and reliability, the unique benefits of choosing Technomax, and their exceptional expertise and commitment.
You may also like to read:
- Crane Modernization from Technomax
- Bearing Fault Condition Monitoring Techniques
- Dynamic Balancing Of Gas Turbine Rotor
What is Ferrography?
Ferrography is a non-destructive diagnostic tool used to examine wear particles in oil. It is a method that can be applied to identify wear particles and assess the level of wear without putting the machinery at risk.
Ferrography can also be used to monitor the condition of machinery and identify potential issues, thereby lowering maintenance charges and costly downtime.
Non-intrusive ferrography, developed by Vernon C. Westcott in the 1970s, studies particles that indicate mechanical wear without interference. The word “ferrography” is derived from the Latin word ferrum, meaning iron. Due to this, the main material that ferrography uses to evaluate wear particles is iron or other ferrous metals.
However, ferrography can also be used to gauge wear on pieces made of non-ferrous metals like copper and aluminium.
What is the Ferrography Analysis Method?
Magnetic separation and microscopic inspection are the two-step procedures in the ferrography analysis procedure. As the first step, the wear particles are taken out of the oil through magnetic separation. This is done by using a magnet to pull the ferrous wear particles to it.
Here, the non-ferrous wear particles remain in the oil as they are not attracted to the magnet.
In the second step, which is microscopic inspection, the wear particles are examined under a microscope as the name suggests.
Factors like the type, size, shape, concentration, and composition of the wear particles can be used to identify the cause of wear and the severity of the problem.
The Role of Ferrography in Maintenance and Reliability
Across industries, early problem detection is imperative for averting expensive downtime and equipment failures. Ferrography can identify wear particles in oil at an early stage before they put machinery at risk.
This would increase the longevity of the machinery and tools and also lower maintenance expenses.
Ferrography can also be employed to pinpoint where the problem was initiated and how much wear has already occurred.
The technique might also be able to further aid in preventing breakdowns by utilising this data to develop and carry out necessary maintenance.
Read more about:
- What is Couple Unbalance – Definitive Guide
- Preventive Maintenance Using Vibration Analysis in Electric Induction Motors
- Vibration Sensors: An Overview- Types Of Vibration Sensors
What are the Different Types of Ferrography?
The three main areas that ferrography falls under are reading, analytical, and online visual. Direct reading ferrography is a simple and inexpensive kind of ferrography for determining whether wear particles are present in the oil. However, it cannot be used to figure out the exact number or severity of the wear particles.
Analytical ferrography is a more advanced technique for finding, assessing, and evaluating the extent of wear particles. This type of ferrography is the most common and works by diligently examining contaminants and particles.
Online visual ferrography is another technique that captures images of wear debris in machinery and equipment while running.
By connecting an electromagnet, flow controller, and image sensor to the oil circuit, ferrous particles are deposited, and various details such as images of debris with relative wear debris concentration and particle coverage area can be collected. Ferrography is an important tool to increase the reliability of machinery.
Since it is a powerful diagnostic tool, it can help identify and prevent issues before they become major concerns. If you’re apprehensive about machinery’s health and performance, consider using ferrography to determine the type of wear.
Understanding Technomax’s Ferrography Process
An equipment’s longevity can be increased by using Technomax’s ferrography services, starting with an in-depth inspection of the equipment and its state of functioning. If specific samples are collected from the indicated areas, this information is then added to a unique sampling method.
At this point, Technomax uses cutting-edge equipment and the assistance of skilled specialists to remove entire oil samples from the machinery.
Technomax’s cutting-edge lab takes over once the wear particles have been removed from the oil. The lab meticulously studies these oil samples to determine the size, type, content, and form of the wear particles using cutting-edge magnetic separation technology. High-resolution microscopy helps to further clarify the physical characteristics of these particles.
So in short, Technomax offers a wide range of ferrography services, including sample collection and analysis, interpretation of results, recommendations for corrective action, training on ferrography techniques, etc.
Benefits of Using Technomax’s Ferrography Services
Ferrography is a more accurate and reliable process to assess wear particles when compared to more conventional techniques like eye inspection and standard oil analysis.
This is because ferrography can provide comprehensive data about the size, type, composition, and shape of particles as well as the ability to find wear particles that are too small or invisible for the bare eyes.
There are a number of advantages over customary methods to utilising Technomax ferrography services, like greater accuracy, earlier and efficient detection, more detailed information, etc.
The following are the benefits of using Technomax’s ferrography services:
- Accurately identifying wear particles: Technomax’s experts are able to precisely identify the size, shape, and composition of wear particles, which provides them with crucial knowledge regarding the condition of your machinery.
- Practical and timely insights: In order to help you stop downtime and expensive repairs, Technomax provides timely and helpful information.
- Solutions customised for various industries: Technomax offers specialised solutions for a variety of industries, ensuring that you receive the assistance you need to meet your unique needs.
- Lowering the cost of maintenance and downtime: Ferrography can reduce downtime and maintenance costs by identifying wear particles early and preventing catastrophic failures.
Before starting the Technomax ferrography procedure, an inquiry will be sent to you regarding your requirements. Following this, a team will collect an oil sample from the machinery and analyse it in the lab. The size, shape, and composition of the wear particles in the oil will be determined during this examination.
With the use of this information, a report comprising insights on the equipment’s state and recommendations for improvement will be made.
As a result, Technomax ferrography services can help you improve the reliability and performance of your machinery by detecting wear particles early and taking corrective action before major failures occur.
If you are concerned about the wear of your machinery, then Technomax ferrography services will help you protect your investment and prevent costly failures. Contact us today to learn more about our services.
Learn More About Our Services
Recent Blogs
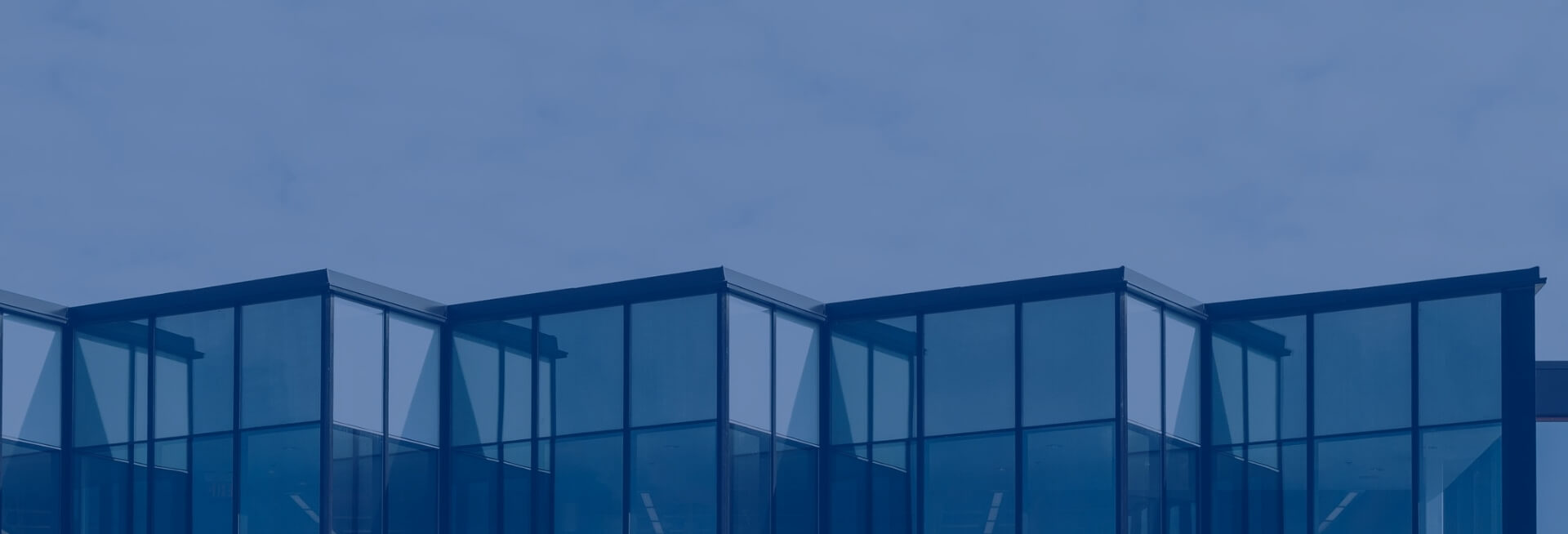
Get Started Now!
It takes less than a minute of your time. Or you may simply call +971 2 555 1 783