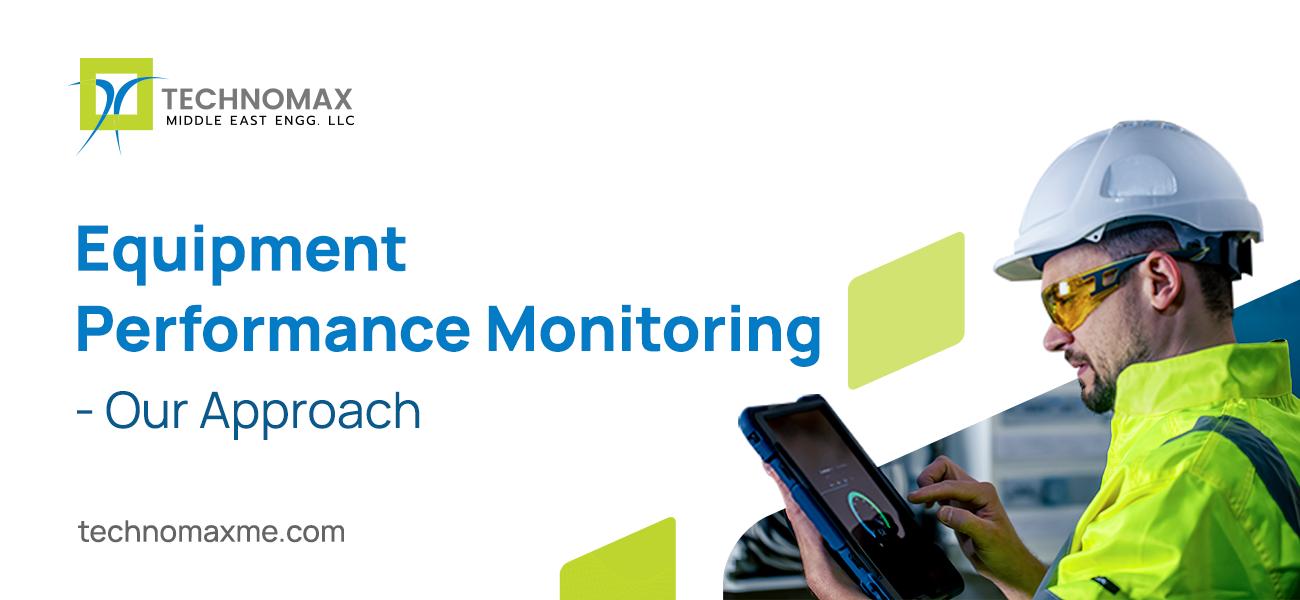
Equipment Performance Monitoring – Our Approach
Many Industrial sectors working for equipment performance monitoring to evaluate business digitization to utilize it as a major target for business optimization.
In both situations, equipment performance monitoring can scale the service times, build efficiency, and trigger uptime.
In this blog, let’s understand more about equipment performance monitoring and how Technomax takes a crucial role in supporting businesses with performance monitoring services for their business equipment.
Growing concern over the Degradation of Equipment Performance
The performance of equipment such as pumps, turbines, compressors, etc, deteriorates with time.
This leads to a decrease in their efficiency, improved power consumption, reduced throughput, and a rise in operating costs.
Degradation of equipment can occur with the physical changes that affect machine parts.
It could be mechanical wear due to the long operation hours, or any physical wear like corrosion of pump impellers.
It can also arise from the surface degradation that happens on heat exchanger plates.
When you deploy appropriate maintenance, you can avoid reduced productivity and the loss of quality.
To preserve the performance of systems in process plants, the maintenance personnel should be aware of when the machine would degrade and appropriate maintenance needs to be scheduled.
Ensuring the efficiency and performance of the plant equipment can let you win the battle against degrading equipment, thereby contributing more to the plant's productivity.
Read more about:
- Rubber Tyre Gantry Cranes(RTG Crane): An Overview
- Maximising Plant Productivity Through Machinery Diagnosis
- Keeping it on the rails: The Importance of Overhead Crane Runway/Rail Inspections
What is Equipment Performance monitoring?
Equipment performance monitoring refers to inspection, analysis, graphing and benchmarking with design data.
- Data Acquisition: Site field information like vibration, temperature, operation parameters shall be collected with the help of portable device.
- Analysis: The data from devices need to be analyzed for abnormalities and need to be graphed with respect to the operation curves.
- Benchmarking: All the plots shall be benchmarked with design graphs and anomalies will be highlighted for further analysis.
For instance, if you track the machinery or the equipment continuously, then there is less chance of an immediate breakdown.
You can take faster corrective action when you would know prior that the equipment doesn't exhibit optimal performance.
Consider yourself as a heavy equipment manager, and you have noticed a sudden rise in the fuel bill compared to the usual monthly costs.
You would now check the fuel usage of all equipment and gather the idling reports to understand which particular equipment consumes more fuel.
From this point, you can determine if the higher bill has been a normal expense or a result of the equipment's condition.
Condition monitoring and its significant benefits
Condition monitoring takes the equipment parameters under consideration and uses them to explore the problems like machine vibration, temperature, etc. prior.
It analyzes the specific characteristics or conditions of machinery as a part of equipment monitoring. This is how condition monitoring can help you:
- Improve the installation lifespan of the equipment;
- Keep the efficiency throughput of the product high;
- Minimize the anticipated downtime;
- Plan the maintenance and inspection.
The condition monitoring system lets you schedule preventive and proactive maintenance that eradicates sudden failure in the equipment. It also avoids the need for any costly repairs.
In the absence of equipment monitoring technology, the floor or site managers will need to do walkarounds to check the equipment.
This is a time-consuming and tiring task. However, condition monitoring replaces it with real-time monitoring of power, temperature and vibrations of the equipment.
You can develop custom dashboards and notifications to get alerts in case things go wrong.
It also can develop predictive maintenance, where businesses use real-time data and analytics from sensors to let you know in advance when an equipment failure could happen.
Businesses can also make use of wireless sensors that detect the health of equipment like pumps, compressors, fans, etc.
You can enable the fast deployment of sensors to track machine vibration and temperature conditions of equipment quickly.
How Technomax does equipment performance monitoring
Technomax offers performance monitoring services that allow businesses to deploy preventive maintenance before issues arise.
With advanced technology, Technomax benefits businesses through a considerable reduction in repair costs, thereby preventing unnecessary and expensive downtime.
It provides prior notifications on the fault abnormality in the equipment and produces alerts to remind the machine of its health.
You may also like to read:
- Electrical Preventive Maintenance and Scalable Services
- The Influence of Lubrication, Vibration Infrared Analysis Results
- Motor Current Signature Analysis
To conclude
Equipment Performance Monitoring technology helps organizations enable end-to-end troubleshooting of the machinery and implement proactive maintenance.
Nevertheless, performance monitoring is also about huge savings on labour and service costs.
Technomax adopts a holistic integrated performance monitoring technology and incorporates it into the products, to ensure effective condition monitoring.
This helps you to monitor efficiency equipment, and extend the life of your equipment.
To know more about how Technomax does equipment monitoring, contact us.
Learn More About Our Services
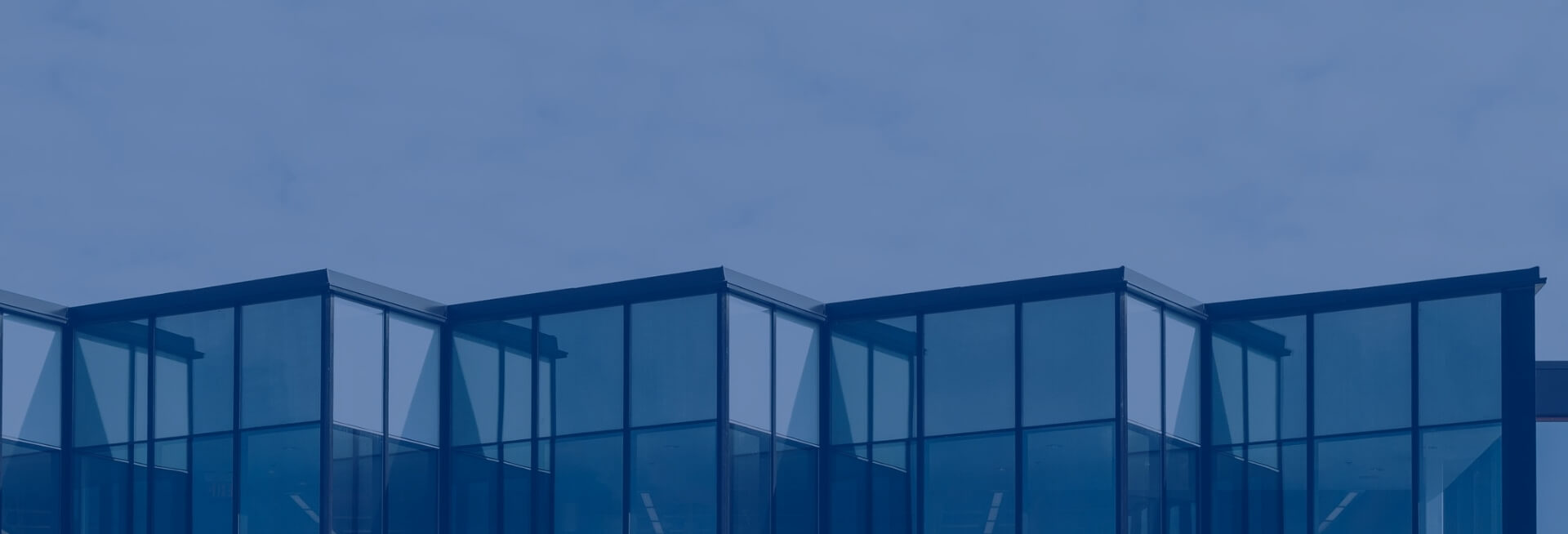
Get Started Now!
It takes less than a minute of your time. Or you may simply call +971 2 555 1 783