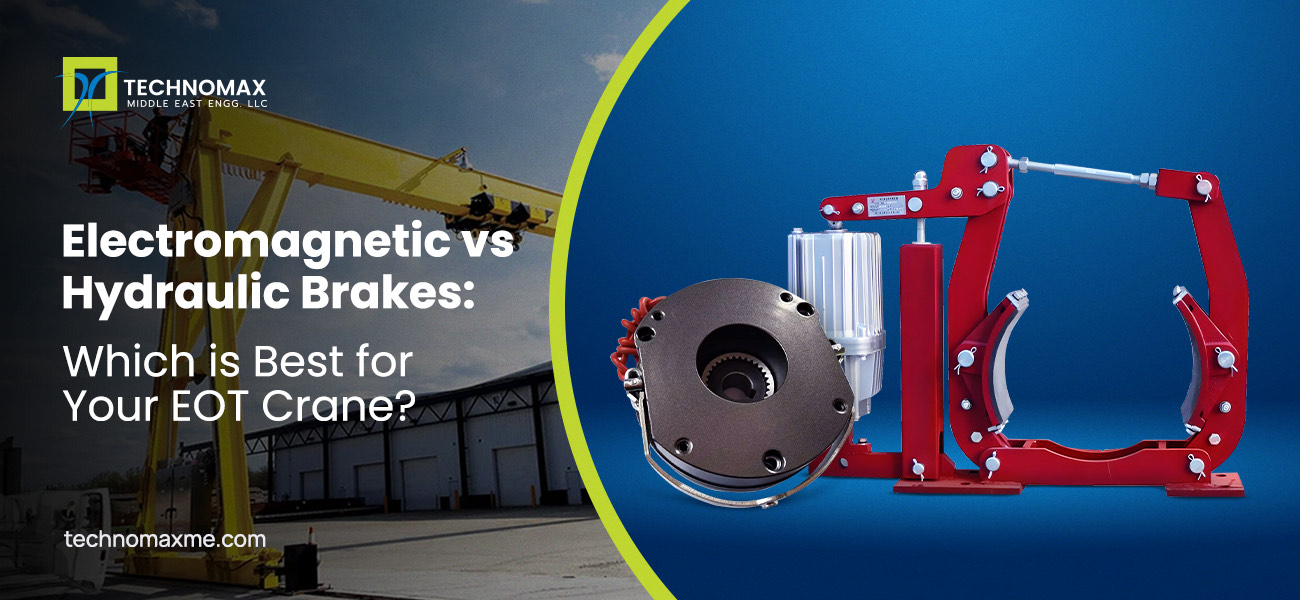
Electromagnetic vs. Hydraulic Brakes: Which Is Best for Your EOT Crane? Selecting the right braking system for your EOT (Electric Overhead Traveling) crane is crucial for safety, performance, and operational efficiency. Among the common options, electromagnetic and hydraulic brakes stand out, each with distinct advantages.
Brakes are integral to the safe operation of machinery, particularly in overhead cranes such as Electric Overhead Traveling (EOT) cranes. These systems are responsible for controlling the motion of heavy loads, ensuring they can be stopped or slowed safely and effectively. The choice of brake system can significantly impact operational efficiency, safety, and maintenance requirements.
Here we will explore the two primary types of braking systems used in EOT cranes: hydraulic brakes and electromagnetic brakes, helping you choose which is best suited for your specific needs.
Standards and Hold Control
Safety standards play an important role in crane operations. Organisations such as the Occupational Safety and Health Administration (OSHA) and the American National Standards Institute (ANSI) set forth guidelines that govern the design and functionality of crane braking systems.
According to OSHA 1910.179, each hoisting unit must be equipped with at least one holding brake that automatically engages when power is lost. This feature is critical for preventing accidents during power failures.
Hold Control refers to the ability of a brake to maintain a load's position without movement when not actively controlled. Both hydraulic and electromagnetic brakes must meet stringent hold control standards to ensure they can safely secure loads under various conditions.
Types of Brakes
There are two primary types of brakes used in EOT cranes:
- Hydraulic Brakes: These brakes utilise hydraulic fluid to generate pressure that engages the braking mechanism. They are known for their ability to handle high braking forces and dissipate heat effectively, making them ideal for heavy-duty applications. Hydraulic brake SBD100 is an example of this type.
- Electromagnetic Brakes: These brakes like the Electromagnetic Safety Brake Ap75/30 operate using electromagnetic forces to engage the brake. They offer quick response times and are often preferred in applications requiring precise control over load movements.
Crane Hydraulic Brake vs. Electromagnetic Safety Brake
When selecting the appropriate brake system for your EOT crane, understanding the differences between hydraulic and electromagnetic brakes is essential. Here is a quick table that outlines their key features:
Feature | Hydraulic Brake | Electromagnetic Brake |
Response Time | Moderate response time due to the nature of hydraulic fluid dynamics, making it suitable for controlled applications. | Quick response time due to the instantaneous action of electromagnetic forces, is ideal for precision operations. |
Braking Force | Capable of generating high braking forces, making it suitable for heavy-duty applications and large loads. | Provides moderate braking force, usually sufficient for lighter loads and applications requiring precision control. |
Heat Dissipation | Excellent heat dissipation due to the use of hydraulic fluid, allowing continuous use without overheating. | Limited heat dissipation, may lead to wear during prolonged or high-frequency usage. |
Maintenance Requirements | Requires regular checks of hydraulic fluid levels, inspection for leaks, and proper sealing of components. | Needs periodic inspection of electrical components, magnets, and connections to ensure proper functionality. |
Safety Features | Includes fail-safe mechanisms, ensuring engagement during system failure or power loss, and enhancing operational safety. | Immediate engagement upon power loss due to electromagnetic forces, offering reliable safety during emergencies. |
Noise Level | Operates quietly, making it preferable for environments where noise reduction is essential. | It can produce noticeable noise due to friction during engagement, which may be a concern in noise-sensitive areas. |
Durability | Long-lasting when properly maintained, as it has fewer wear-prone components. Suitable for prolonged and intensive use. | Shorter lifespan compared to hydraulic brakes due to wear of electromagnetic components over time. |
Ideal Applications | Heavy-duty industrial cranes, high-load environments, and operations requiring extended use with minimal overheating risks. | Precision load handling, light to moderate loads, and applications where rapid response is critical. |
Maintenance Tips for Overhead Crane Brakes
Proper maintenance is crucial to ensure the longevity and safety of crane braking systems. Some maintenance tips are:
- Regular Inspections: Conduct routine inspections of both hydraulic fluid levels and electromagnetic components to identify potential issues early.
- Testing Functionality: Regularly test holding and control functions to ensure they operate correctly under various loads.
- Cleaning Components: To avoid premature wear, keep brake components clean from dust and debris.
- Lubrication: Ensure all the moving parts are adequately lubricated to minimise friction and extend lifespan.
- Documentation: Maintain detailed records of inspections, repairs, and maintenance activities for compliance with safety regulations.
Choose Technomax for Reliable Crane Installation & Maintenance Solutions
Selecting between hydraulic and electromagnetic brakes requires a better understanding of factors like operational requirements, load capacities, response times, and maintenance needs. Aligning these considerations with your application ensures safety, reliability, and operational efficiency in crane systems.
If you are looking for the best performance and safe operation of your EOT cranes, choose Technomax, a trusted leader in crane maintenance in the UAE. Offering tailored solutions for installation, servicing, and upgrading all types of cranes, including advanced brake system integration, we ensure your systems run efficiently, adhere to safety standards, and minimise downtime.
Contact us today to learn how we can improve your crane operations and maximise productivity.
Learn More About Our Services
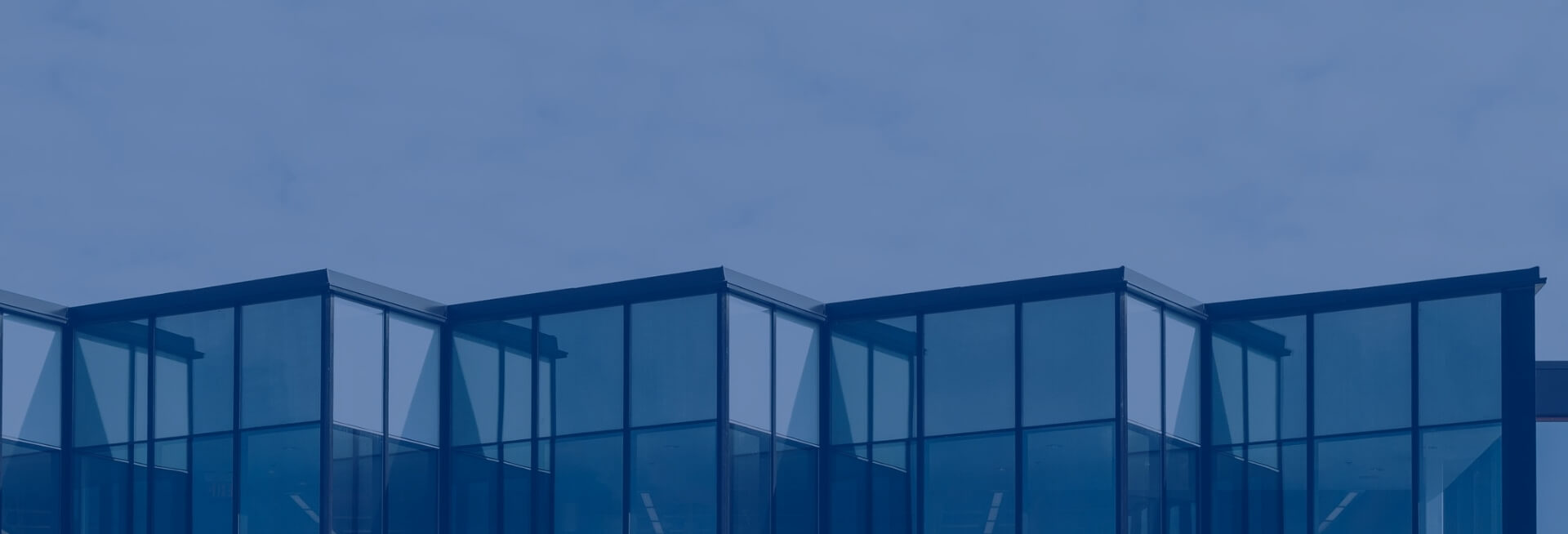
Get Started Now!
It takes less than a minute of your time. Or you may simply call +971 2 555 1 783