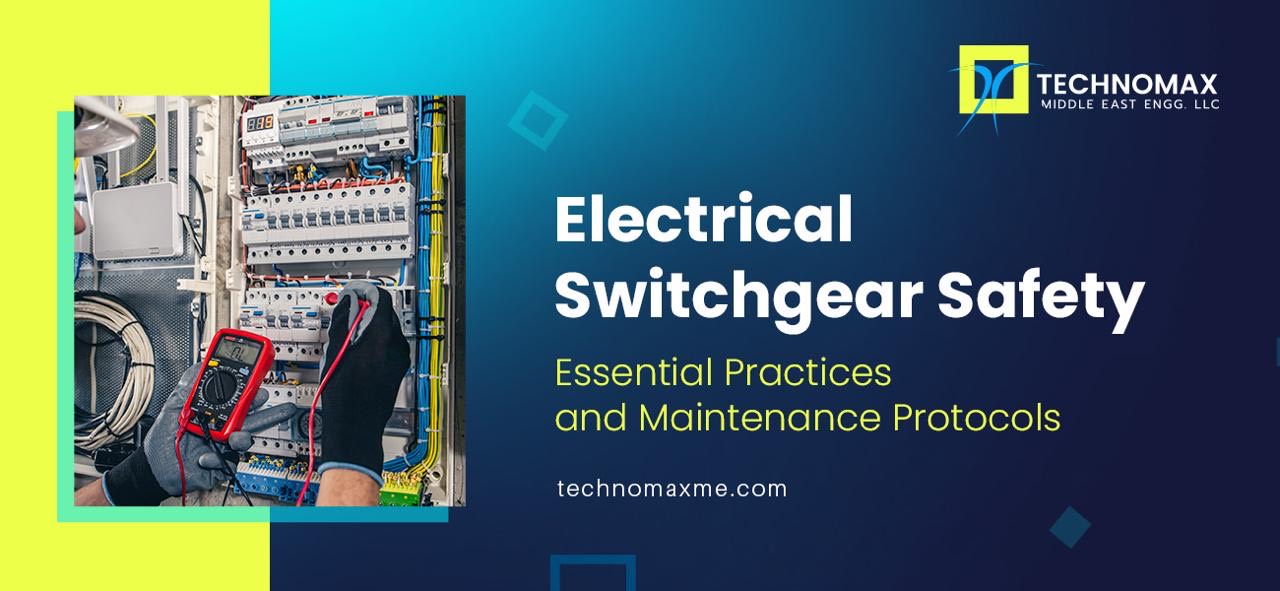
Electrical switchgear is an integral part of every electrical system, from massive industrial giants to our homes. It controls power flow and isolates electrical equipment, and it acts as a central hub. Recent studies indicate that up to 70% of electrical distribution system failures originate from electrical switch gear malfunctions. These failures can be dangerous and expensive, causing power outages for entire cities or leading to significant downtime for industrial facilities. But how do you maintain a switchgear?
This blog delves into the importance of safeguarding switchgear, underscoring the role of condition-based maintenance, diagnostic testing, and prioritising a safety-first approach.
What Is Meant By Switchgear?
An electrical switchgear is a broad term that includes diverse switching devices that control, protect, and isolate electrical equipment in an electricity supply system. Switchgear manages electrical power distribution and safeguards electrical circuits from overload and short circuits. There are different types of switchgear, such as
- High Voltage Switchgears: Commonly found in power generation plants and substations, these central switchgears are used in electrical distribution systems with voltages above 36 kV.
- Medium-Voltage Switchgears: These are usually used in commercial buildings, industrial installations, and critical power supply systems. Medium voltage switchgears work with voltages ranging from 3 kV to 36 kV and can accommodate voltages.
- Low-Voltage Switchgears: These low-voltage switchgears are used both in commercial and residential areas and support voltages up to 1 kV.
Switchgear helps to keep us safe, ensure smooth operation and increase productivity and efficiency.
How Important Is Switchgear in Electric Power Systems?
As an important component of an electrical power system, switchgear ensures safe and reliable operation. It impedes the damage from short circuits and overloads, which are possibly devastating events that threaten their security and dependability. A common type of switchgear is an air circuit breaker, an overcurrent and undervoltage relay, an earth fault relay, a power fuse, a power isolator, a disconnector, or a MoldedCase Circuit Breaker (MCCB).
Protecting electrical equipment such as transformers, capacitors, generators, and distribution panels (below 450 volts), this kind of switchgear power system is typically found in low- and medium-voltage applications, such as industrial plants and promotes system performance and minimises the risk of costly. The following are some of the key points that reiterate the importance of power system protection and switchgear in an electrical power system:
- Overload Protection: Switchgear averts potential damage to circuits from excessive currents, thereby preventing fires and equipment failure.
- Fault Isolation: In the event of a malfunction, switchgear ensures minimal downtime and protects other parts of the grid by enabling safe equipment deactivation.
- Controlled Outage Management: It facilitates safe maintenance or emergency intervention by allowing manual or automatic disruption of power.
- Power Distribution & Control: Optimising power flow, switchgear plays a role in managing power distribution within a system.
- Enhanced Personnel Safety: By securing and controlling high-voltage circuits, the switchgear reduces the risk of accidents.
- Increased Reliability: It assures a more consistent power supply, thus enhancing the reliability of commercial and residential settings.
- Load Management: Modern switchgear can better handle electrical loads, encouraging energy efficiency and reducing wastage.
Switchgear plays a crucial role in ensuring the safety, reliability, and efficiency of electrical power networks through its power management capabilities and protective features.
What Are the Benefits of Electrical Switchgear Maintenance?
Regular, proactive switchgear maintenance is key to averting electrical failures, thereby circumventing extensive downtime, damage to equipment, and risks to human life. Effective maintenance boosts the durability of switchgear components, assures system dependability, and adheres to safety standards. Below are some of the top benefits of electrical switchgear maintenance:
- Prevents Equipment Failure: Regular maintenance helps identify and address potential issues before they escalate into major failures. This proactive approach minimises downtime and associated repair costs.
- Extends Equipment Life: By catching problems early and addressing them through electrical preventive maintenance, the overall lifespan of switchgear components is significantly extended.
- Ensures System Reliability: A well-maintained electrical system experiences fewer interruptions and delivers consistent power flow, enhancing overall system reliability.
- Upholds Safety Standards: Regular maintenance ensures that switchgear operates within safe parameters, reducing the risk of electrical accidents and arc flash incidents.
The Shift to Condition-Based Maintenance (CBM)
Regardless of the actual working condition of the equipment, maintaining electrical distribution switchgear is usually done at fixed intervals. This usual practice, not necessarily aligned with the actual condition of the equipment, was revolutionised with Condition-Based Monitoring (CBM), with real-time monitoring and assessment of data collected through sensors that determine the right time for maintenance. Here is how it works:
- Data Collection: Continuously monitor switchgear health through sensors tracking temperature, vibration, and partial discharge.
- Data Analysis: Leverage data analysis to identify trends and predict potential issues before they cause unplanned outages.
- Maintenance Scheduling: Optimise maintenance by scheduling interventions only when necessary, maximising resource efficiency.
The Role of Diagnostic Testing in Switchgear Maintenance
Diagnostic testing plays an important role in CBM programmes and overall switchgear maintenance. These tests - both intrusive and non-intrusive - enable early detection of potential issues that could lead to equipment failure. Some of the most common diagnostic tests include the following:
- Infrared Thermography: This non-intrusive technique utilises infrared cameras to detect abnormal temperature rises in switchgear components. Identifying hot spots allows for repairs before they develop into serious problems.
- Partial Discharge Testing: A crucial test for high-voltage switchgear, partial discharge testing identifies insulation degradation before it leads to failure. The recommended minimum voltage level for online PD testing is 5KV and above. Techniques like Transient Earth Voltage (TEV) measurements and Airborne Ultrasonic Detection are employed for this purpose.
- Insulation Resistance Testing: This test measures the resistance of electrical insulation to current flow. A decrease in resistance indicates potential insulation breakdown, prompting further investigation.
- Contact Resistance Testing: This test measures the resistance between contact points to detect potential issues such as loose connections, corrosion, or wear in the contacts that could cause localized heating and affect the reliability and performance of the switchgear.
- Operational Tests: These tests verify the proper functioning of mechanical and electrical components within the switchgear, ensuring reliable operation during fault conditions.
Safety Precautions When Working with Switchgear
Working with electrical switchgear inherently carries risks, including the possibility of electrical shocks, arc flashes, and other hazards. Therefore, adhering to stringent safety procedures is an absolute necessity.
Lockout/Tagout (LOTO) is a safety practice that ensures equipment’s proper isolation from all energy sources using approved lockout devices. In addition to LOTO practice, using Personal Protective Equipment (PPE) like flame-resistant clothing, insulated gloves, safety glasses with side shields, hard hats, and leather boots, are essential as well. Along these lines, conducting a thorough risk assessment helps identify potential hazards associated with the specific work, like understanding the type of switchgear being worked on, the presence of energised components, tasks being performed, environmental conditions, etc. Here are some safe work practices to be followed to minimise risks during switchgear maintenance:
- Working with a qualified professional: It is crucial to never work alone or near energised components on switchgear, and a qualified person with expertise should always be present to provide necessary assistance in case of emergencies.
- Maintaining a safe working distance: Always maintain a safe distance from energised components as specified by electrical safety regulations and the specific switchgear being worked on.
- Using appropriate tools and equipment: It's important to only use electrical tools and equipment that are rated for the application and are in good condition.
- Proper grounding: Ensure proper grounding procedures by doing electrical ground testing are followed to prevent electrical shock hazards. Safe grounding helps dissipate any unintended electrical current.
- Clear communication: Maintain clear communication with colleagues working on the electrical system to ensure everyone is aware of the maintenance activities being undertaken. This communication helps prevent accidental re-energisation of equipment while maintenance is in progress.
By adhering to these safety precautions, workers can significantly reduce the risks associated with electrical switchgear maintenance and ensure a safe working environment.
Why Safety Maintenance Is Important for Electrical Switchgear?
Electrical switchgear safety is extremely important. You might have heard about some of the best switchgear, including underground switchgear, automated switchgear, control gear, and switchgear. By utilizing Condition-Based Maintenance (CBM) and diagnostic testing, switch gears are regularly and predictably maintained to operate within safe limits, significantly reducing the risk of electrical accidents, arc flashes, and equipment failures. By prioritising safety practices and maintaining electrical systems effectively, a safety culture is fostered, resulting in a safer work environment for everyone. Below are some reasons why maintenance and safety go hand-in-hand:
- Reduced Risk of Electrical Accidents: Regular maintenance of main electrical switchgear helps identify and address electrical issues before they escalate into accidents. Early detection of problems like loose connections, overheating components, or degraded insulation minimises the chance of electrical shocks, arc flashes, and other electrical hazards.
- Prevention of Arc Flash Incidents: Arc flash incidents are particularly dangerous electrical explosions that can cause severe burns, blindness, and even death. Proactive maintenance through cleaning, tightening connections, and replacing worn-out components significantly reduces the risk of arc flash by minimising potential ignition sources.
- Improved Equipment Reliability: A well-maintained switchgear system experiences fewer equipment failures. This translates to improved operational reliability and reduced downtime, ensuring a consistent flow of power for critical processes and facilities.
- Lower Maintenance Costs: By catching problems early and addressing them through preventive maintenance, the need for costly repairs and emergency replacements is minimised. A proactive approach leads to a more predictable maintenance budget and avoids the financial burden of unexpected equipment failures.
- Enhanced Worker Safety: When switchgear safety is prioritised during switchgear maintenance, workers are less likely to be injured or killed due to power hazards. This protects individual well-being and promotes a positive safety culture within the organisation.
- Compliance with Regulations: Electrical safety regulations mandate specific maintenance practices for switchgear. Regular maintenance ensures compliance with these regulations, avoiding fines and legal repercussions.
Effective maintenance practices and a commitment to safety are paramount for safeguarding electrical infrastructure integrity, maximising lifespan, and avoiding potential risks. By adopting a proactive approach with industry experts like Technomax, organisations can ensure continued, efficient, and safe operation.
Being the leading engineering company in UAE, Technomax provides condition monitoring and machinery diagnostics services by using a combination of condition-based maintenance, diagnostic testing, and stringent safety protocols. It is essential to stay updated on best practices and prioritize safety in an ever-changing electrical industry to ensure a safe and reliable electrical system.
If you want to learn more about the importance of switchgear maintenance in creating a safe work environment, feel free to connect with us today.
Learn More About Our Services
Recent Blogs
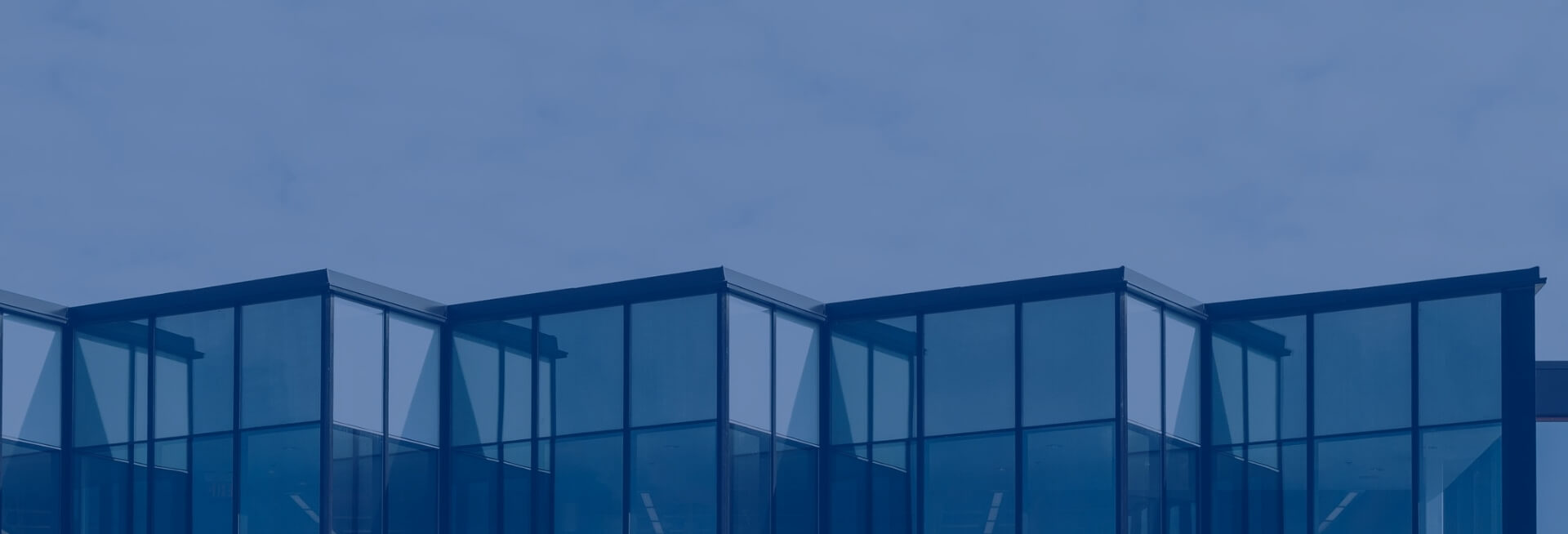
Get Started Now!
It takes less than a minute of your time. Or you may simply call +971 2 555 1 783