
The rapid Industrial development has paved the way for many innovations, Dosing and metering pumps being one of them with characteristics to offer a precise flow rate with ideal chemical dispersion.
Apart from the water pumps and the water supply equipment, metering pumps have gained importance due to their diverse range of applications and various types that work using different principles.
Let’s discuss the dosing metering pumps and how they work from this blog.
You may also like to read:
- Turbo Machinery Analysis and Balancing
- Equipment Performance Monitoring – Our Approach
- Ultrasonic Flow Measurement Services
What is A Dosing Metering Pump?
A dosing pump, also called a metering pump or dose pump refers to a positive displacement pump, well-designed to push a chemical or similar substance to the flowing gas, steam, or water.
These pumps are usually small and offer accurate flow rates with maximum control. They make an essential part of the integrated metering system developed to perform automatic chemical dispersion.
The dosing pumps enable the process of dispensing certain amounts of fluid while also maintaining the flow.
The chambers for expansion and contraction help to move fluid along the pumps. Metering pumps have gradually evolved to be highly accurate to pump a wide variety of chemicals and liquids which include acids, bases, corrosives, viscous fluids and slurries.
Major Components of a Dosing System
Before delving into the working principle of a dosing metering pump, let’s understand the various parts of a dosing system in detail.
- Chemical vessel/tank: It holds the product which requires dosing.
- Pump: There are various types and sizes of pumps, including material and sizes: contain inlet, suction and dosing tubes.
- Injector: One-way valve used to inject chemicals into the product. This overcomes the pressure present in the piping and lets chemicals combine with the flowing liquid.
- Bottom Valve: One-way valve linked to the suction line and placed in the product drum to maintain the pump in the beginning position.
- Dosing Line: This is a rigid or reinforced hose which could be used for high pressure with PVC, PE, or stainless steel.
- Control System: This makes sure about accuracy while opening and closing during specific intervals. It can be a regular flow switch/timer for various sensors. This could be further integrated into a huge system.
Working principle of a Dosing Pump
A dosing metering pump sucks a particular amount of liquid and feeds to the pump chamber to add liquid into the process.
The pump gets controlled with an electric motor or air actuator. It has a controller to switch the pump on and off, hence regulating the flow.
Let’s understand the working principles of various types of dosing pumps in detail:
Diaphragm metering pump:
It utilizes a specially constructed and designed flexible diaphragm that replaces the piston. It thus realizes the reciprocating movement with a driving mechanism to implement suction discharge. The isolation effect helps the diaphragm to realize the isolation of the structure between the lubrication mechanism and metered fluid.
Plunger metering pump:
The Plunger metering pump sucks the working medium and discharges directly with a reciprocating motion of the plunger. As the seal and plunger are in direct contact with the medium, you should choose the relevant plunger material and sealing to make sure that the pump performs well during the operation.
Peristaltic metering pumps
These positive displacement pumps are somewhat similar to the diaphragm metering pumps. But they function with some differences. They use rotating rollers to squeeze a flexible tube that moves the fluid in a pressurized motion. Since the low-pressure volume rises, it leaves a vacuum that pushes liquid inside the tube. The fluid flows along the tubing with every rotating or oscillating motion.
Lobe Pump
This pump lets a specific volume of fluid move through the meshed gear impeller. This is not precise like a diaphragm pump and is suitable only for fluids with high viscosity that have the least wear due to the self-lubricating effect. They are not designed for low flow rates since it is hard to make sure they are accurate.
Solenoid Dosing Pumps
These metering pumps have the simplest design and are the least expensive. Solenoid valves monitor and regulate a spring-loaded reset piston with is used to push out a particular amount of fluid per stroke. Increasing the frequency of strokes helps in regulating the flow rate. These types of pumps are utilized for low-flow applications.
Multi-diaphragm dosing pumps
These dosing pumps are designed to take care of high-flow processes like water treatment procedures. In such applications, you analyze and control the chemistry of water. In these pumps, you can inject various chemicals to control the chemical properties. This design includes a flexible diaphragm driven by the moton adjustable stroke lever. To control the flow rate, stroke frequency and the chemicals delivered for each stroke can be varied. In water treatment systems that involve multiple pumps, you can control motor speed and chemical delivery with a chemical analyzer.
Applications of dosing pumps
The major applications of metering pumps are as follows:
- Taking care of maintaining a consistent flow rate irrespective of the fluid viscosity or differential pressure.
- Maintaining system parameters like pH through the delivery of variable flow.
- Injecting discrete dosing procedure, especially for batch processing.
- Use of metering in various industries like water treatment, waste processing, pharmaceuticals, chemical processing, power generation, oil and gas extraction, petrochemicals, etc.
- Liquids may range from fragrances, or the pigments used in the production of food, toiletries, etc. It could also be the alkaline solutions or acidic solutions utilized in water treatment and chemical processes.
In a Nutshell
The meaning of Dosing varies in every industry since different applications demand various levels of accuracy/flow. As a result, we provide a wide range of dosing pumps that offer dosing in multiple levels of accuracy and flow.
Compared to the expensive conventional gear pumps of the olden days, an ideal metering pump can help you with affordable and reliable alternatives. It offers continuous dosing procedures in low-flow and high-pressure applications.
The dosing metering pumps ensure a seamless pumping action without pulsation and with minimum shear, making them perfect for continuous and intermittent tasks.
At Technomax, our team ensures superior, durable and reliable pumping technology with high-quality dosing metering pumps for all industrial applications. With the best technicians available, we offer customers the required support in the installation and maintenance of these pumps for smooth industrial processing.
Learn More About Our Services
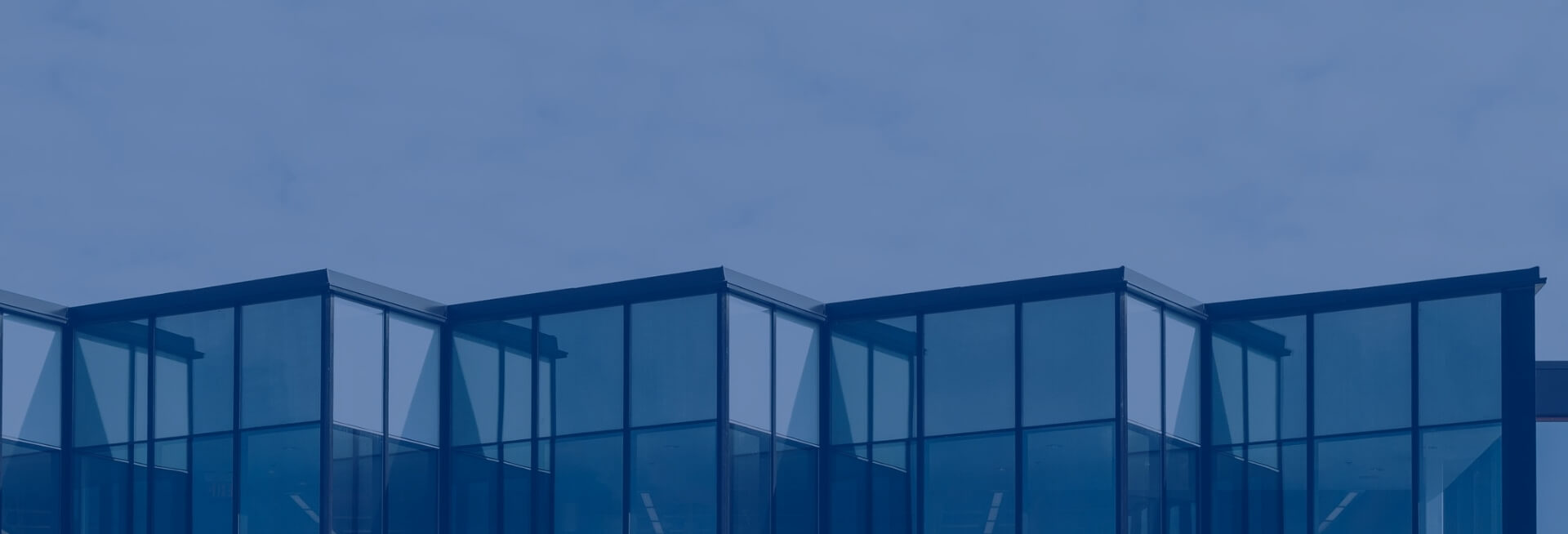
Get Started Now!
It takes less than a minute of your time. Or you may simply call +971 2 555 1 783