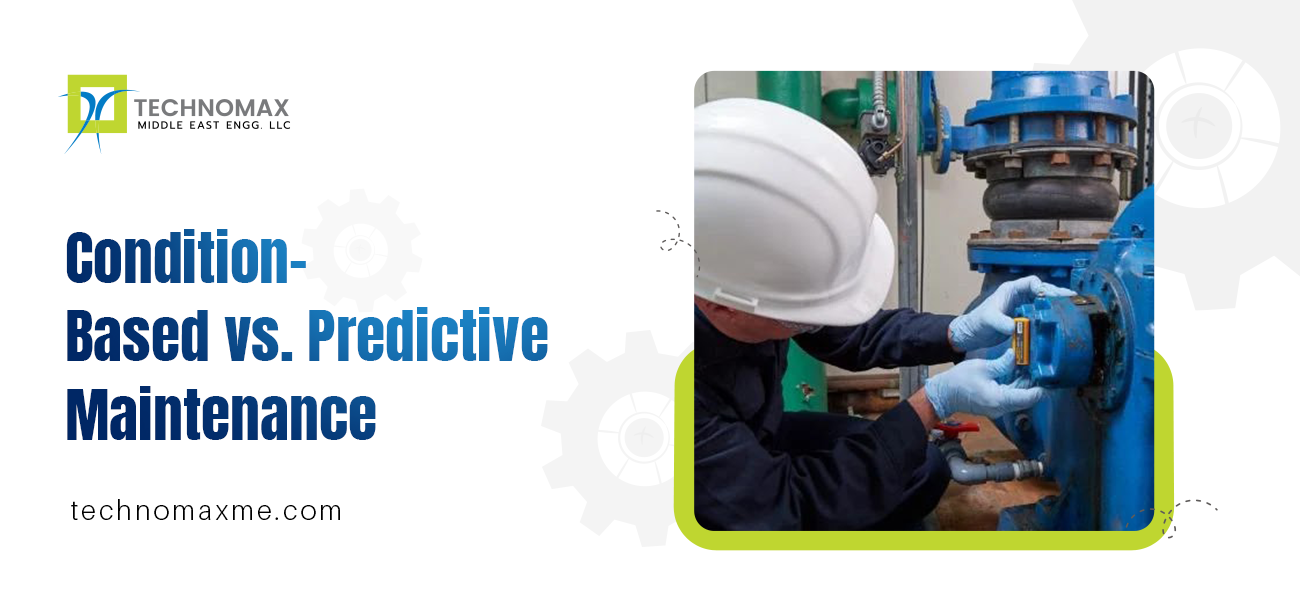
Condition-Based vs. Predictive Maintenance
Maintenance strategies have dramatically changed over the years, mainly due to the introduction of technology-based and data-based solutions. CBM and PdM remain two of the most recognisable and widely used techniques in today’s industrial maintenance approaches. Although monitoring downtime and optimising asset performance have similar objectives, they achieve them through varied approaches.
This guide will look deeper into the details of CBM and PdM to understand more of the flow of the entire process, the strengths and weaknesses of CBM and PdM, and the different sectors that can benefit from the two.
What is Condition-based Maintenance?
Condition-based maintenance, or CBM, is planned maintenance in which the actual condition of the equipment or machinery is monitored to determine when maintenance should be performed. CBM is based only on real-time sensor data, which are used to identify the condition of the equipment in the real world. Maintenance personnel are deployed every time a specific parameter elicits an unsatisfactory value. This means that condition-based maintenance systems carry out work when required.
In CBM, various detection techniques and instruments collect information about machinery parameters like temperature, vibration, pressure, and all other executable measurements. Maintenance is then scheduled based on the actual condition of the equipment.
Condition-Based Maintenance Workflow
The CBM starts with data collection. Monitoring devices and sensors are placed on the components and parts of machinery in the industrial system to measure different characteristics like temperature, vibration, pressure, and other parameters. This information is constantly monitored to identify any irregularities from normal operating conditions.
- Data Collection: Temperature, vibrations, and other controlling values are acquired by attaching sensors or monitoring devices to certain machinery parts. This includes temperature, vibration level or intensity, pressure, state of lubricating oil, and other conditions that can indicate the condition of the equipment.
- Data Analysis: The accrued data is processed by specialised software and algorithms to identify abnormalities. This is very helpful in discovering signs or anomalies that indicate potential issues like wear and tear, misalignment, or future failure.
- Decision Making: The system decides whether a maintenance session is necessary. If the data show signs that the equipment is wearing out or is beyond the standard performance parameters, a maintenance alert is raised.
- Maintenance Execution: After deciding, all the required maintenance works are carried out to bring the equipment to its desired standard state. This could involve replacing worn components, changing settings, or making other adjustments or remedial actions.
- Review and Feedback: The performance of the equipment is also monitored after maintenance to confirm the nature of the existing problem was duly fixed. The data-gathering phase can also help fine-tune the CBM process, improving the accuracy of future maintenance decisions.
Pros and Cons of Condition-Based Maintenance
Pros | Cons |
By limiting maintenance procedures to only when needed, CBM ensures no unnecessary repairs. | CBM can only be implemented with a considerable investment in costing equipment, monitoring instruments, and analytical software. |
Maintenance is done according to the equipment's actual conditions and excludes failures and unexpected downtimes. | CBM entails knowledge of the equipment, the conditions under which it operates, and data analysis capability. |
With the help of CBM, it is possible to distribute maintenance resources rationally, paying attention to assets that will require action soon. | The constant monitoring of equipment can produce large volumes of data, which can be overwhelming to manage and interpret without the right tools. |
What is Predictive Maintenance?
Predictive Maintenance (PdM) is an advanced maintenance strategy that employs data-driven methodologies and predictive analytics to anticipate when equipment or machinery is likely to fail. The primary strategy of PdM is to perform maintenance on equipment just when it is about to fail, minimising downtime, reducing maintenance costs, and extending the lifespan of assets.
Predictive maintenance is based on exact formulas and measurements, and the repair activity is done based on the analysis of parameters such as temperature, vibration, and noise. Unlike other approaches in maintenance techniques like reactive maintenance (performed after a failure) or preventive maintenance (performed on a regular schedule), PdM anticipates failure patterns using real-time data analysis, historical data, and statistical analysis. If problems can be foreseen before they occur, then the right time for maintenance intervention can be arranged to minimise disruptions to operations.
Predictive Maintenance Workflow
Predictive Maintenance involves several key steps that allow for the accurate prediction of equipment failures:
- Data Collection
- Data Analysis and Modeling
- Prediction
- Maintenance Planning
- Maintenance Execution.
Advantages of Predictive Maintenance
Predictive maintenance is a strategy that plans maintenance and repairs in anticipation of a subsequent immediate failure. This allows for precise maintenance that reduces unwanted inspections and repairs, enabling early intervention to prevent complicated problems.
Longer Equipment lifespan: Well-maintained equipment leads to enhanced performance and longevity. Predictive maintenance minimises wear and tear, reduces the number of breakdowns, and helps maintenance service act quickly if there is an anomaly.
Lower maintenance costs: According to the PRSM 2012 HVAC Benchmarking Report, reactive service calls after equipment breaks are, on average, three times as expensive as proactive calls. It means you would have to spend $400 more on average for a single call. These savings are even more significant when using a predictive maintenance approach, contributing to optimising maintenance frequency. Accuracy of prediction enables organisations to reduce, if not eradicate, unplanned reactive maintenance while at the same time decreasing overall costs of preventive maintenance.
Less downtime: Predictive maintenance enables engineering departments to minimise reactive maintenance while minimising planned downtime. Aside from reducing equipment maintenance downtime, predictive maintenance allows engineers to plan downtimes better to minimise disruptions.
Enhanced routine maintenance activities: The same machine learning technology for predictive maintenance can also optimise routine maintenance work because, with real-time data, it can suggest optimal measurements to take. It gives data fault detection and diagnostics with better and more accurate real-time equipment appraisal than the conventional way. This assists in reducing the time required by the technicians and contractors to identify and evaluate the problem by providing root-cause analysis insights into the issue.
Disadvantages of Predictive Maintenance
- High Initial Costs: PdM entails considerable expenditure on sensors, especially condition-based sensors, sophisticated software, and possibly cloud software.
- Technical Expertise Required: PdM involves using data science, machine learning, and knowledge in operation to create and sustain predictive models.
- Data Dependency: For accurate PdM results, the collected data must be rich in quality and preferably in quantity. Unsurprisingly, flawed data results in lousy prediction and potentially unplanned downtime.
Types of Predictive Maintenance
Predictive Maintenance (PdM) utilises several methods by which the condition of the equipment is continually assessed to identify possible failures and set a suitable maintenance strategy. These techniques are based on distinct forms of data and analysis. They can help maintenance teams realise a potential problem before it significantly affects production time or further expensive repairs. Here are the most common types of predictive maintenance techniques:
1. Vibration Analysis
Vibration analysis is one of the most effective and commonly used methods of predictive maintenance for equipment such as motors, pumps, compressors, and fans. This method tracks the vibration of any piece of equipment in a bid to detect any sign of irregularity in a specific piece of equipment because this may be an indication of misalignment, imbalance, looseness, or bearing wear.
The accelerometers are attached to the machinery to monitor the vibration frequencies and amplitudes. The data is then processed to determine if there is an abnormal operation compared to the standard procedures. Problems including angular misalignment, axial misalignment, radial misalignment, end-play and pre-load, faulty or worn-out bearings, worn-out gears and keyholes, slackness, wear, etc can be observed.
2. Oil Analysis
Oil analysis evaluates the characteristics of oil used in equipment to determine the state of the oil and the equipment. Companies that depend more on lubricants, such as manufacturing companies, automobile companies, and companies that deal with heavy equipment, tend to adopt this technique.
Oil or lubricant samples are collected from machinery and analysed in a laboratory or on-site testing equipment. It also considers factors such as the actual viscosity of a particular oil, the amount of contamination, the level of tiny wear particles, and the oil's chemical composition.
3. Infrared Thermography
The thermographic technique is infrared thermography, where infrared cameras are utilised to identify heat patterns on the equipment's casing. Since excess heat can indicate electrical faults, mechanical wear, or insulation breakdown, thermography is particularly useful in identifying electrical systems, mechanical components, and process equipment issues. Infrared cameras capture thermal images of machinery, which are then analysed to detect hotspots or unusual temperature variations. These thermal images provide a visual representation of heat distribution across the equipment.
4. Ultrasound Analysis
The non-invasive diagnostic technique, ultrasound analysis involves applying high-frequency sound energy to locate flaws in equipment. This technique is more useful when the problem creates sound at higher audible frequencies, such as air leaks, fluid leaks, electrical discharge, and mechanical issues, such as bearing defects.
Acoustic Ultrasound monitors or acquires the emission of higher-pitched sound signatures from the tools. The captured sounds are converted to audible signals or visual data to be analysed or for display purposes. It detects gaseous and air leaks, electrical sparking, bearing defects, and pump cavitation.
5. Motor Circuit Analysis (MCA)
Motor Circuit Analysis (MCA) is a refinement of the traditional condition monitoring technique. It is particularly applied to electric motors to diagnose electrical faults before they cause a breakdown. MCA is advantageous in every sector where electric motors are a decisive factor, including manufacturing, utilities, and transportation.
MCA requires electrical testing of a motor's stator, rotor, and windings. The analysis detects issues like insulation breakdown, rotor bar defects, and phase imbalances.
Condition-Based vs. Predictive Maintenance
CBM focuses on immediate response to equipment conditions, and PdM anticipates future issues, allowing for more strategic maintenance planning. The choice between the two depends on factors like the complexity of the equipment, available resources, and the desired balance between short-term and long-term benefits. Let's analyse some factors:
- Approach: CBM is reactive, responding to real-time conditions, while PdM is proactive, predicting future failures.
- Complexity: PdM is generally more complex and data-intensive compared to CBM.
- Cost and Benefit: CBM is cost-effective in the short term with immediate benefits, whereas PdM involves higher upfront costs but provides longer-term savings and efficiency.
Being the leading engineering company in UAE, Technomax provides condition monitoring services to assist oil and gas companies in overseeing their machinery, anticipating potential failures, and making predictive maintenance choices through machine learning. At Technomax, these services are provided by combining digital technologies and artificial intelligence. Entrust your machine health with Technomax.
Learn More About Our Services
Recent Blogs
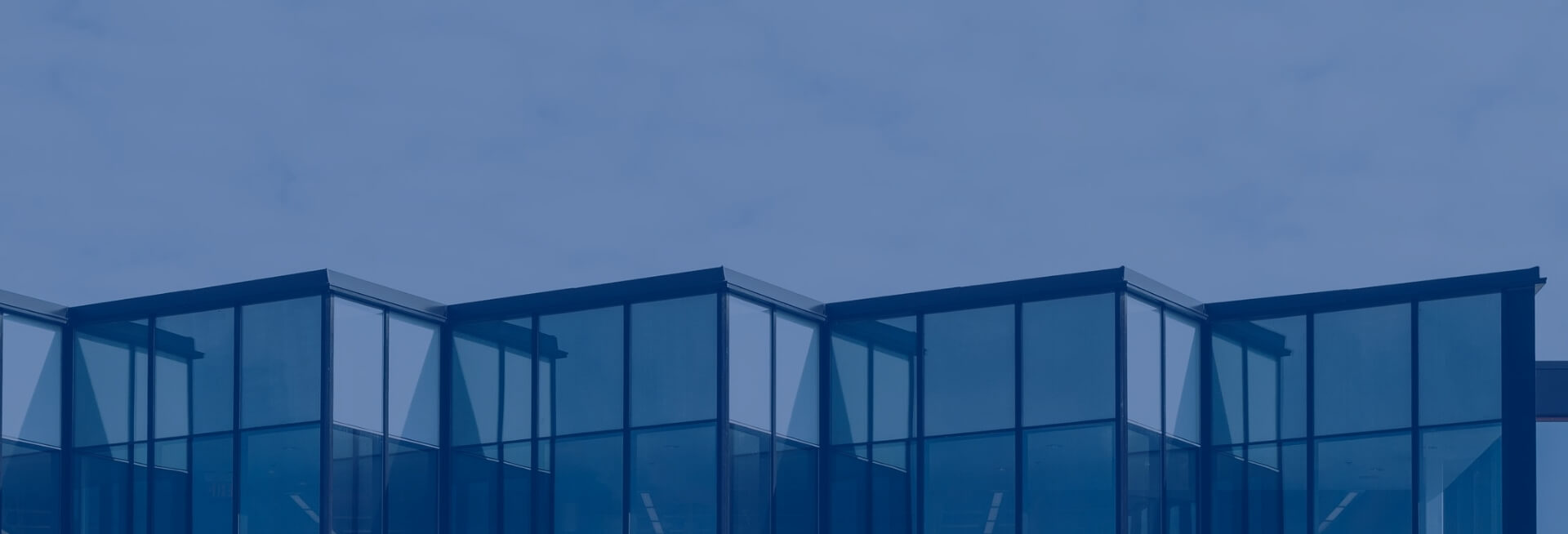
Get Started Now!
It takes less than a minute of your time. Or you may simply call +971 2 555 1 783