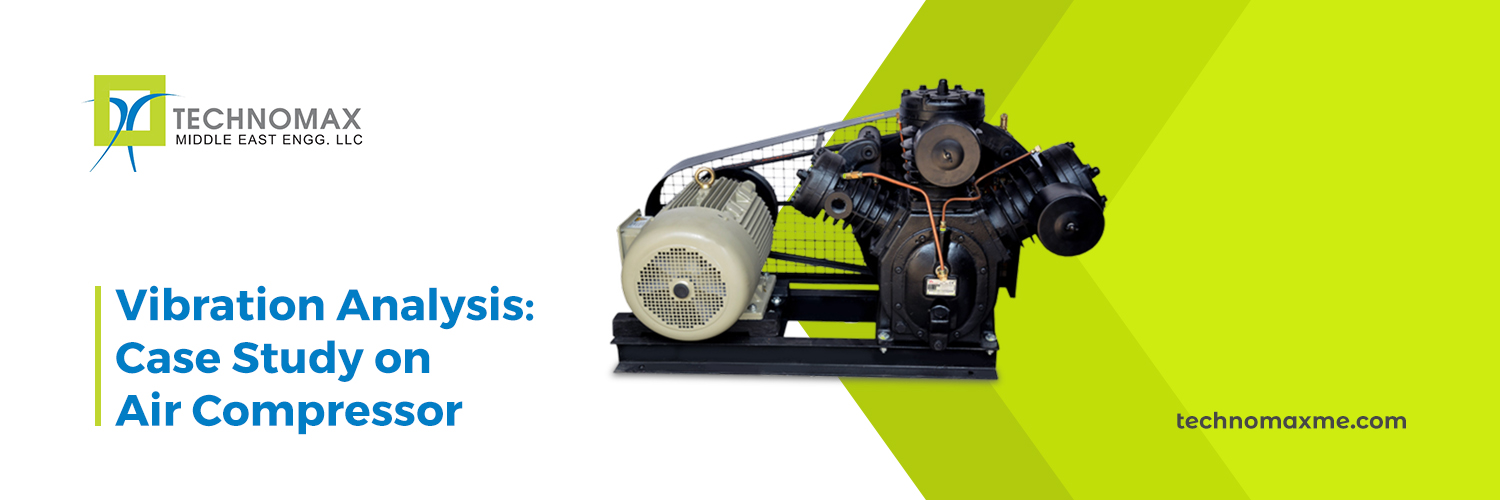
Vibration Analysis: Case Study on Air Compressor
This case study is prepared to provide a brief description about a case study conducted to gauge and fix high vibration issue of an air compressor in oil & gas field.
Analysis and study conducted by: Sharath Vunnam, Level 3 Certified Engineer
Objective:
Many industries are transforming from preventive maintenance to predictive maintenance in recent times. Vibration analysis is one of the most effective tools used to check the health of plant machinery and diagnose the causes. Machinery’s health is checked by routine or continuous vibration monitoring analysis by using sophisticated instruments, which will give early indications of the failure and can take counter-measures to avoid any disastrous impact.
Background:
As part of the routine vibration checks carried out in one of our important customer’s plant, we experienced high vibration issues in one of their air compressor. The team collected all the necessary data (vibration, phase data, structure vibration) for completing a detailed analysis.
Equipment Details:
Motor Speed : | 1470 RPM | ||
Rate Power : | 55 KW | ||
Coupling Type : | Belt Drive | Comp Speed : | 880 RPM |
Instrument & Software:
Instrument: Scout 140 Advanced 4-channel Vibration Analyzer
Make: GE Bently Nevada
Software used: Ascent level-II
Initial Findings:
Our team complied and analyzed all the available data to identify the cause of high vibration in motor and compressor. The below spectrum shows that 1X rotational frequency is dominant on motor bearing:
Fig: High 1X motor rotational frequency as dominant
The team conducted Cross channel analysis on motor, structure and vibro dampers. The MNDE axial and MDE axial were out of phase (180⁰) and MDEH –MDEV was 90⁰, which revealed that there was an issue of shaft runout in motor shaft and Unbalance in motor pulley.
Recommended actions:
We recommended to the customer to complete a check shaft run-out condition and perform motor solo trail without pulley, and provide extra stiffness to motor structure frame.
Maintenance:
The maintenance team changed all the damaged vibro dampers and added extra stiffness with 4 more vibro pads along with existing one
Checked shaft runout condition and found bent shaft which is more than the allowable tolerance
Team decided to replace motor along with new pulley
Post Maintenance:
After completing the suggested maintenance actions, maximum vibration levels had been reduced from 35mm/sec to 7mm/sec during load condition.
Fig: 1X peak reduced after maintenance actions
Conclusion:
Vibration Analysis: Different mechanical faults produce different vibration signature/spectrums. By carrying out careful in-depth analysis and deep study eliminates different possibilities and concludes to single fault.
These types of problems will be identified when there is a regular condition based monitoring activity that helps to reduce the downtime and sudden failure of equipment’s during peak production time. Today, we are able to provide condition based monitoring services to all types of industries across the Middle East with a set of high end technology enabled tools managed by well experienced and certified engineers.
Learn More About Our Services
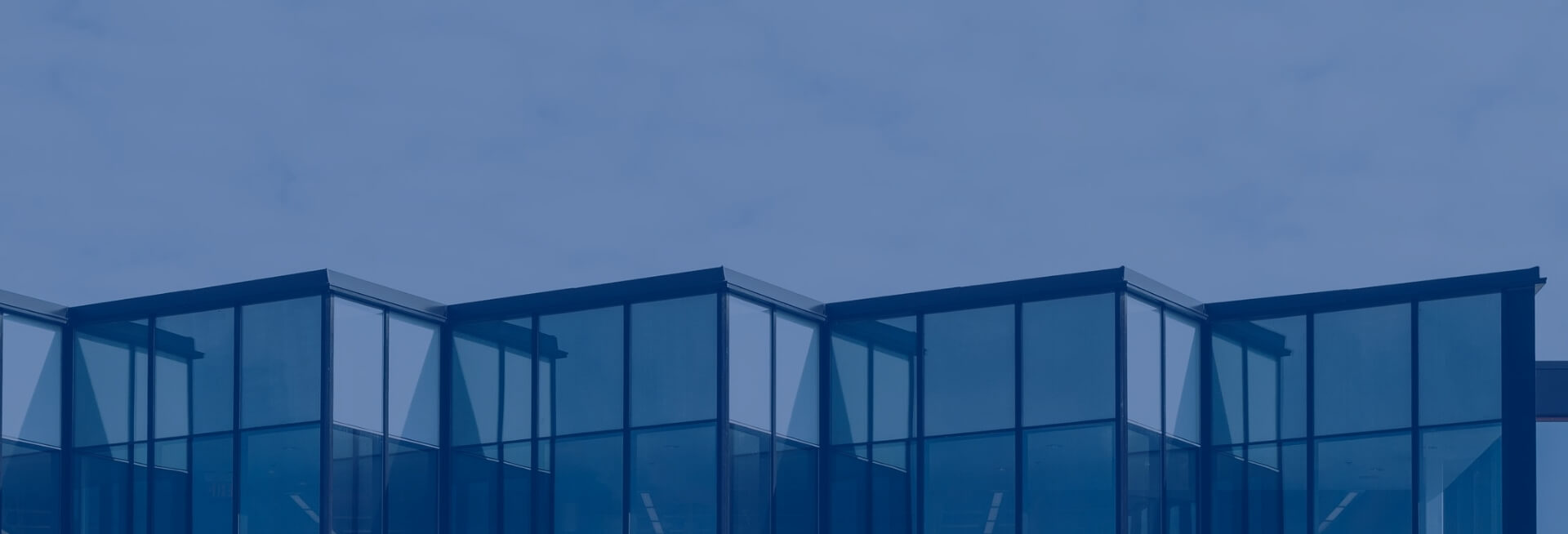
Get Started Now!
It takes less than a minute of your time. Or you may simply call +971 2 555 1 783