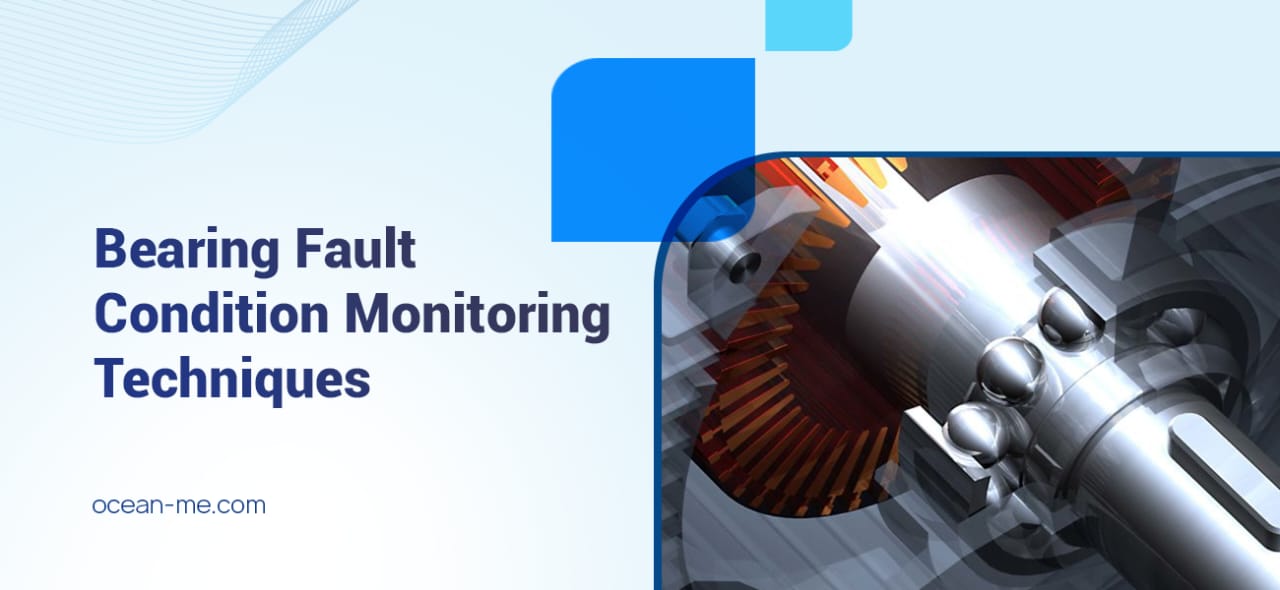
Bearing Fault Condition Monitoring Techniques
Bearing faults account for at least half of the failures that occur in electric machines. The consequences of these failures include machine breakdowns, unplanned downtime, equipment damage, and serious financial losses. To avoid this and make sure you maintain consistent performance, end-to-end bearing maintenance is necessary.
However, when a single machine includes multiple bearings, how could this be managed? In this aspect, of the numerous bearings present in the machines, many of them outlive the system, while some of them fail in service.
But this small fraction can have a significant impact. Having the right condition monitoring strategy can help you overcome this risk. Let’s read more to explore the various bearing fault condition monitoring techniques in detail.
You may also like to read:
- Dynamic Balancing Of Gas Turbine Rotor
- What is Couple Unbalance – Definitive Guide
- Preventive Maintenance Using Vibration Analysis in Electric Induction Motors
Bearing Faults: An Overview
Every year, about 10 billion bearings are produced across the globe. However, only a small fraction undergoes failure. Most of the bearings get replaced before failure strikes, but only with the help of timely bearing monitoring and a prompt preventive maintenance approach.
Bearing failures can cause a loss in productivity and time, or sometimes even result in the shutdown of the entire plant. To make sure bearing monitoring takes place efficiently, you need to adopt the right strategies to monitor and prevent faults with bearings.
While managing the overall health of the machinery, the state of the bearings plays an integral part. A single-bearing failure can result in machine shutdown, which eventually leads to production loss and costly downtime.
Improper lubrication, contamination, misalignment, corrosion, etc. contribute to the damage of bearings. When we consider all the factors that contribute to the failure of bearings, bearings are the core component of motors/generators, particularly when we require smooth rotation and great efficiency.
Traditional Bearing Fault Detection Techniques
Visual Inspection and Manual Fault Detection
Visual inspection and manual fault detection are the conventional methods of performing bearing fault condition monitoring. This involves the inspection of the bearings in and out, the elimination of seals, the inspection of grease, checking for contamination in the bearings, and cleaning the components with solvent or degreaser.
Vibration Analysis
Vibration monitoring is one of the major methods to measure performance and execute predictive maintenance. The equipment emits vibration signals, as does the motion and interaction between the parts within the bearings. The changes in the signals caused by changes in the operational conditions cause issues with the health of the machine.
Faults in moving components like bearings are held responsible for the differences in signals. These changes could be detected with equipment like vibration velocity transducers, accelerometers, etc. Factors like surface roughness, geometric imperfections, contamination, and improper lubrication could be defective signals you can observe.
Once implemented correctly, this method is the ideal way to identify bearing faults, but it would be expensive to set up and requires direct access to the machine for installing sensors. It is also ideal for low-speed machines and instances with high noise, where the defective signals are weaker and more difficult to detect. This finds applications in engines, turbines, and transmissions.
Acoustic Emission Monitoring
In places with high noise levels and low frequencies, the vibrational changes due to the small parts remain undetectable compared to the signals and background noise. But the defects generate waves at high-frequency levels like 100 kHz, which is defined as Acoustic Emission (AE).
The transient elastic waves are produced due to the energy release, which is a result of defects on the components' surfaces. The damaged or faulty bearings lead to this effect, which gets picked up with the help of an AE transducer with little interference from the nearby machinery.
This method is a bit more costly, and dealing with signals needs expert analysis. This method can therefore offer a high signal-to-noise ratio and can be deployed in a multitude of environments to track the condition of bearings.
Temperature Monitoring
At a rated load level, the stabilised bearing temperature should not rise above 45°C. Different factors determine the temperature rise, like lubricant degradation, bearing degradation, temperature in the motor, operational speeds, etc.
Temperature monitoring for unusual ranges can alert the engineers to faults within the bearing. This conventional method allows quantitative measurement of particular parameters; however, it requires the installation of temperature sensors.
Advanced Bearing Fault Condition Monitoring Techniques
Infrared analysis: Infrared analysis detects the heat within the bearing, which is the fault condition at a late stage. Though this is not the best option, it is still being used. Regular oil analysis helps detect the existence of wear metals in the bearing. With regular vibration analysis, you get clear indications about bearing faults. The high-frequency detection methods clearly offer an early warning, which leaves high-frequency vibration analysis, wear particle analysis, and ultrasound analysis.
Ultrasound: Ultrasound is yet another bearing fault condition monitoring technique where you can offer a better indication of the severity and nature of the fault. However, it needs more training and an expensive system to implement analysis and collection.
Machine Learning: Machine Learning is usually performed in stages like data processing, data acquisition, feature extraction, model assessment and training, and the appropriate decision support. In data acquisition, the visual data or signal is gathered with the help of cameras or sensors. Sensing technologies are also used in the condition monitoring of bearing faults, which includes oil analysis, thermography, motor current, dynamic pressures, and speed sensors.
AI-based fault detection: AI-based fault detection helps identify the data that belongs to a particular niche. It also learns from the training set that incorporates the data from that class. Fault detection focuses on detecting whether data monitoring falls into the normal class. Also, fault detection has taken advanced technologies into consideration, such as deep learning, neural networks, etc.
PHM: Prognostics and Health Management Systems involve monitoring the health of bearings and making valuable predictions about the useful life remaining through the assessment of the extent of degradation from the desired state of health.
The condition monitoring techniques take advantage of technologies like IIoT, IoT, edge computing, VR, AR, predictive analytics, Big Data, Wireless sensor networks, remote monitoring, etc.
Importance of Bearing Fault Monitoring
Supports the rotating shaft:
Bearings provide the required support for the shaft, which keeps rotating within the equipment. Since bearings form a significant part of a motor/generator, timely bearing fault monitoring can prevent the shaft from getting damaged.
Ensures smooth rotation:
With inaccurate lubrication, corrosion, misalignment of components, and contamination of the equipment, the bearings can quickly undergo damage. While we gaze at these factors that end up in bearing failure, the fault monitoring system is required to fulfil high-efficiency needs for the machinery and smooth rotation.
Hassle-free operations:
Preventing the failure of bearings makes sure your organisation works at its best and runs at high efficiency. With an effective bearing monitoring technique, you can understand the ideal causes and symptoms that cause bearing failure.
Avoids production time loss: Failure of a single bearing can lead to a complete equipment shutdown, which can cause the loss of production time. With condition monitoring in place, you can analyse the damages in advance and save time.
Prevents the risk of harm: Single bearing damage can result in a cascading chain effect, which leads the shafts to bend. This causes serious risks to the other coupled equipment. Bearing failure can also lead the workforce to experience the risk of harm at the workplace. Hence, a bearing fault condition monitoring technique can avoid these unexpected risks.
Read more about:
- Understanding Busbar Systems: A Comprehensive Guide
- Rotodynamic Analysis Services from Technomax
- Turbo Machinery Analysis and Balancing
Benefits of Advanced Bearing Fault Condition Monitoring Techniques
Fault Detection is crucial to enhancing production efficiency and minimising accident rates in risk-centric mechanical systems. It also helps in monitoring data, which poses significant challenges to the existing fault diagnostic technologies. With fault condition monitoring, you can enable fault detection, determine causes, and offer recommendations to resolve the issues before the damage hits. Advanced condition monitoring has the following benefits:
- High accuracy and early fault detection
- Minimising the downtime and maintenance
- Integration with the already existing condition monitoring systems
- Solving the data requirements and the challenges related to infrastructure
To Sum up
Predicting bearing failure helps minimise the unplanned failure of equipment and the maintenance of the system. Choosing an effective monitoring technique will help your business detect, locate, and interpret faults in advance. Resolving the bearing defects at the incipient stage can also warn the operator before the issue develops into a catastrophic failure. Technomax has a team of expert professionals who offer bearing fault condition monitoring solutions to a multitude of industries based on their requirements while keeping them cost-effective. To learn more about the condition monitoring services we offer, let’s talk today!
Learn More About Our Services
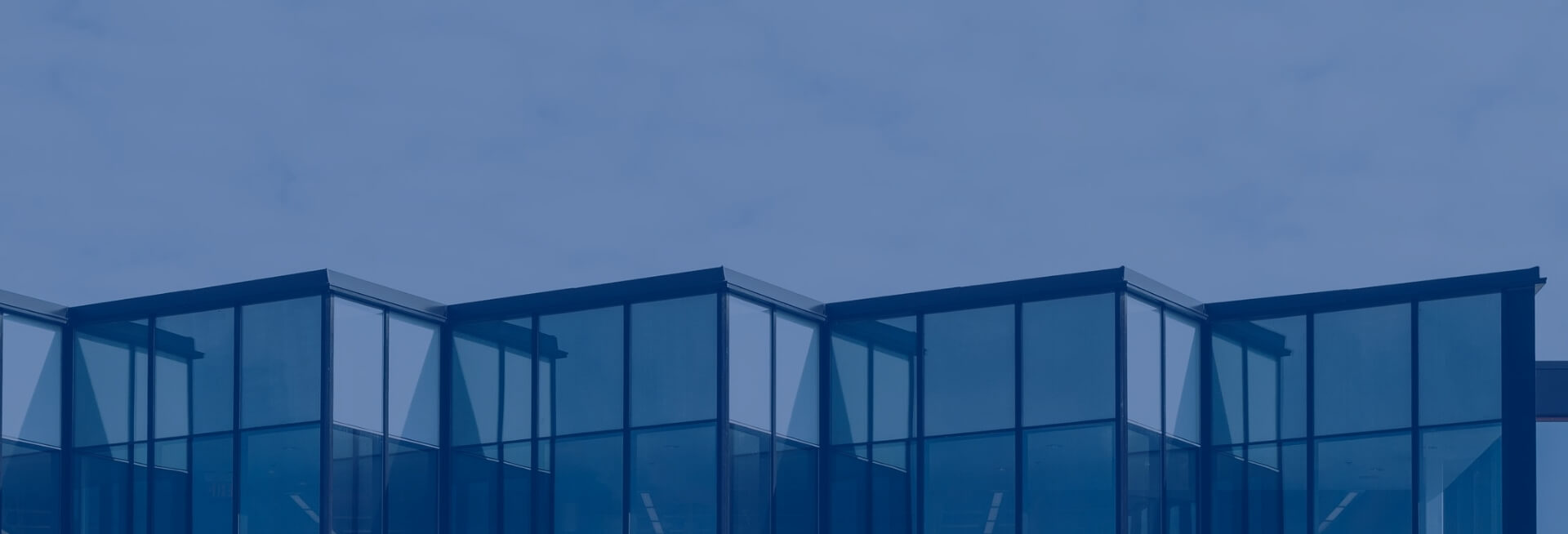
Get Started Now!
It takes less than a minute of your time. Or you may simply call +971 2 555 1 783