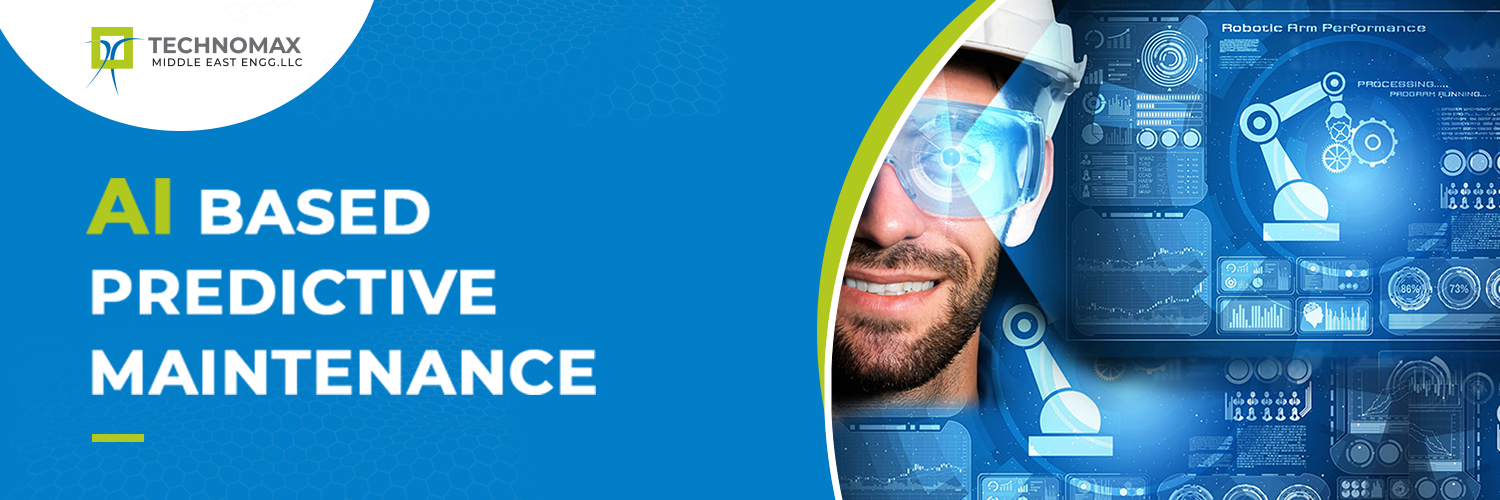
AI-Based Predictive Maintenance System
Every day, we rely on a variety of machines. Still, the truth is that unless properly maintained, every machine will ultimately fail. Since you can't risk expensive machines with vital roles in your plant failing, it’ll be exceedingly expensive to restore severely damaged parts and affect plant productivity.
We have to come up with solutions to prevent this from happening and increase plant safety. Read more about AI Based Predictive Maintenance System.
Plant owners use various maintenance plans to improve operational reliability and cut expenses. Preventive and predictive maintenance are two of the most frequent methods. Preventive maintenance focuses on avoiding machine failure by attempting to schedule maintenance programs before the failure happens.
However, by scheduling maintenance so early, we are losing machine life that is still usable, which increases the cost. However, if you can foresee when a machine will break down, you can schedule maintenance ahead of time.
As a result, the predictive maintenance method outperforms all others. It locates issues in your complex machinery and assists you in determining which pieces require repair before the equipment is in any serious damage. You can cut down on downtime and increase output this way.
Read more about:
- Ultrasonic Testing Devices for Preventive Maintenance
- Vibration Sensors: An Overview- Types Of Vibration Sensors
- Electrical Preventive Maintenance and Scalable Services
How is predictive maintenance implemented through AI?
Predictive maintenance is a sort of condition-based maintenance in which machines are monitored with sensor devices that provide data on the condition of the assets. This information is used to determine when assets will need to be serviced in order to avoid equipment failure.
One of the most difficult aspects of predictive maintenance is filtering through huge amounts of data in order to extract relevant, actionable data. Organisations can find themselves data-rich but information-poor, especially given the rapid rise of industrial technologies.
This is why we introduce you to an AI-based predictive maintenance system.
It’s a method for extracting insights that can be used to spot developing defects before they become severe issues, assess the remaining usable life of even troubled assets, plan repairs during minimally disruptive windows, and undertake a root-cause study to prevent future failures. Read more about AI Based Predictive Maintenance System.
This is a method in which machine learning models collect and analyse data from various streams to identify conditions that are more likely to lead to failure and create more precise predictions about when preventative measures should be taken.
How is AI based predictive maintenance making things better?
- Reduced maintenance cost
The ability to detect and avoid equipment breakdowns can help businesses save money and time. Improved maintenance planning can save a lot of money in asset-intensive industries.
AI based predictive maintenance systems use historical data from a variety of sources, including IoT devices and sensors, to produce accurate forecasts about machine health, usage, and failure risk, allowing you to take action based on this knowledge.
- Increased production time
The system assists in determining the sources of delays, both internal and external, and establishes methods to resolve these issues.
We can also spot any technical problems before they become irreversible and alert us with warning signals, increasing asset uptime, dependability, and efficiency.
- Extended machine life
Real-time monitoring allows you to obtain a deeper understanding of your machines, allowing you to predict machine failure and locate replacement parts.
You can schedule maintenance and repairs and receive real-time notifications, allowing you to respond quickly and extend the life of your assets.
You may also like to read:
- Bearing Fault Condition Monitoring Techniques
- Dynamic Balancing Of Gas Turbine Rotor
- What is Couple Unbalance – Definitive Guide
- Improve working environment
The maintenance team can check the health of field assets at regular intervals with AI based machine monitoring solutions.
Unplanned downtime or machine failure frequently necessitates relocating field service crews from other work locations, employing more personnel, or completely rearranging other scheduled maintenance tasks to handle the problem.
This may be prevented by using AI based predictive maintenance, which increases field service personnel utilisation and reaction times while lowering maintenance length and asset downtime.
- Enhancing the safety and compliance of the plant
Maintenance engineers can anticipate and manage potential safety concerns and identify prospective difficulties with predictive asset maintenance before they affect workers.
By assessing data from many sources, including internal and external sources and data provided by IoT devices and sensors, they can swiftly take necessary action to eliminate safety hazards.
Learn More About Our Services
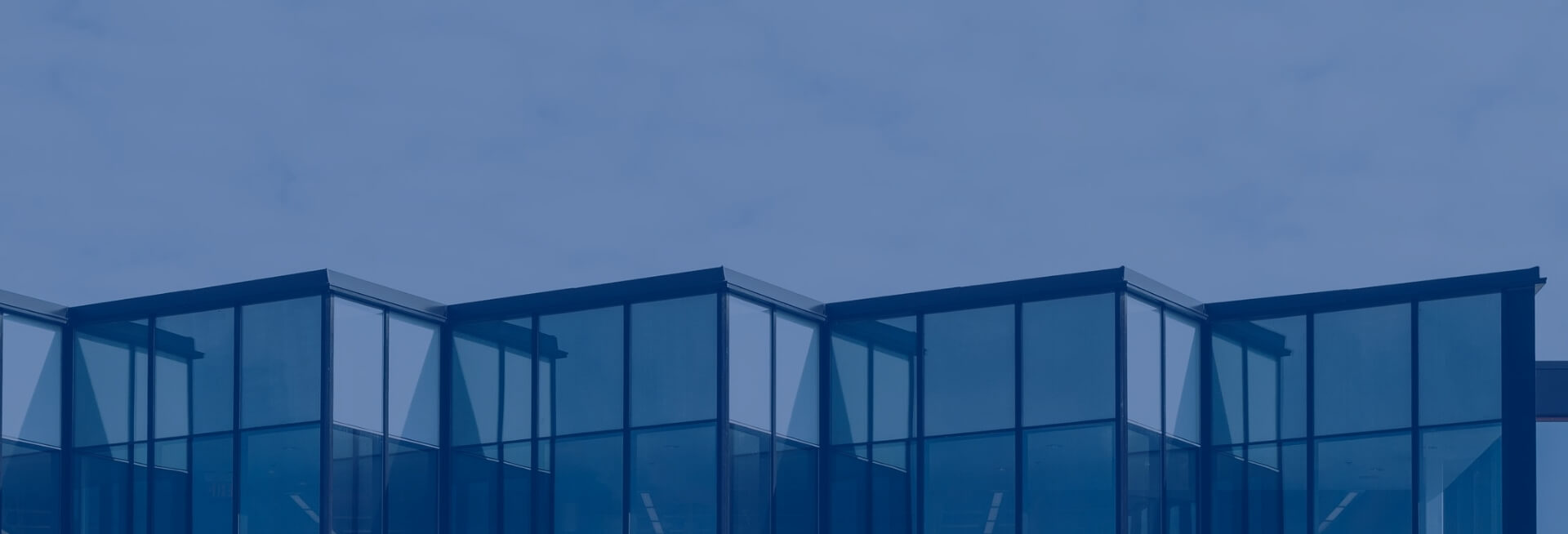
Get Started Now!
It takes less than a minute of your time. Or you may simply call +971 2 555 1 783